Aluminum Alloy Shell Silver Plating Process
Summary: The bright silver plating process pretreated by the combination of secondary zincation and cyanidation zinc plating was studied. The process flow and related parameters were introduced. The effects of zincizing solution preparation, temperature, and time on the coating performance were discussed. The coating obtained by this process is fine, with good lightness and strong binding force.
Keywords: aluminum alloy; Secondary zinc leaching; Cyanide galvanized; Bright silver plating
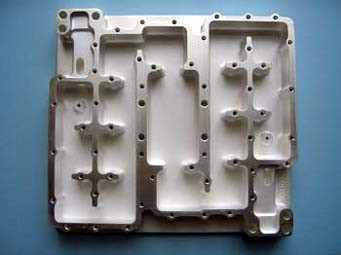
1. Introduction
Aluminum alloy silver plating is widely used in electronics, communications, electrical appliances and other industries. However, since aluminum is a very active metal, it has a strong affinity for oxygen and forms an oxide film on the surface. At the same time, the coefficient of thermal expansion of aluminum and its alloys is very different from that of silver, which makes it difficult to plate silver on aluminum parts.
[1]. The larger the part size and the more complex the shape, the more difficult the plating. Many parts of a military filter are aluminum alloy (brand 7R04-Hll2) silver plated parts, in which the main component U, V-type cavity silver plating is the most difficult. The size of the cavity is 316mm × 190mm × 93mm, the surface area is 40.6dm2, and the inner cavity size is l80mm × 56mm × 90mm (deep). The shape of the cavity is shown in Fig. l. Silver plating is required (23±2) μm and electrolytic passivation.
The part has a large volume and a deep cavity. To obtain a silver plated layer with good adhesion, pretreatment before plating is the key. Many researches on the pretreatment of aluminum and its alloys have been carried out at home and abroad. The author conducted a large number of experiments on the basis of summarizing these methods.
Turn Out:
The pretreatment process combined with secondary zinc leaching and potassium chloride galvanization was replated with silver, and most of the cavities had peeling, blistering and shedding.
In the pretreatment process combining secondary zinc leaching and cyanidation galvanizing, cyanide plating of copper and silver results in fine crystals, good lightness, and strong bonding power, which can better meet the quality requirements of military products.
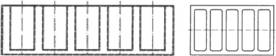
Figure1 Shell structure
2 process specifications
2.1 Process flow
Organic degreasing- chemical degreasing- Alkali corrosion- Acid etching- Zinc leaching- pickle acid- heavy zincate- Cyanide galvanizing- Copper plating- Pre- plated silver- bright silver plated- An electrolytic passivation is blow dried and dried.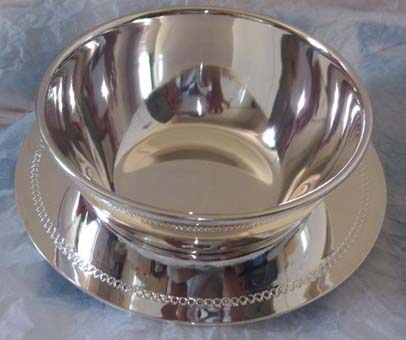
2.2 Solution Formulas and Process Conditions for Each Major Process
2.2.1 Organic Degreasing
At room temperature, using l80 # aviation gasoline.
2.2.2 Chemical Degreasing
2.2.3 Alkali corrosion
The purpose of the alkali etching is to remove the oxide film on the surface of the aluminum part, to obtain an ideal micro-roughness, and to further remove the oil, so as to increase the binding force of the coating. The response is faster and time should be strictly controlled.
2.2.4 Etching
After alkali etching, copper, silicon, manganese, etc. in aluminum and its alloys do not dissolve in alkaline substances, and remain on the surface of the workpiece and the corrosion residue forms a "hanging ash" adsorption film.
The purpose of the etching is to dissolve these attachments, leaving the workpiece exposed to a bright surface and in a good state of activation.
(1) Suitable for general aluminum alloy parts
(2) Suitable for silicon aluminum alloy pieces
2.2.5 First time Zinc leaching
2.2.6 Second zincation
The secondary zincation process has obvious effects on improving the quality of the zinc-impregnated layer and improving the bonding force. This is due to the fact that for the first time of zinc immersion, Al203 must be dissolved before replacing Al. The resulting zinc layer has a rough and loose crystal, uneven distribution of crystal grains, large size difference, and poor adhesion of the zinc-impregnated layer. The secondary zinc immersion method can improve the adhesion, uniformity and corrosion resistance of subsequent coatings. When the zinc crystal grains with poor bonding between the surface of aluminum and its alloys are dissolved in nitric acid, the large grain size of the zinc grains becomes smaller and a uniform and detailed surface is formed. The exposed grains become the nucleation centers for the secondary zinc immersion, so the resulting zinc layer is fine and the bond with the substrate is enhanced.
The process conditions are:
2.2.7 Cyanide galvanizing
For the complex shape of the Shell part, although the secondary zinc-immersing, the zinc layer deposited in the crucible and the deep depression is relatively thin, and the subsequent copper plating is prone to dissolution due to the strong alkalinity and the higher temperature. In this way, the protective effect of the zinc layer on the aluminum surface layer is lost, and the adhesion of the plating layer is severely reduced. Therefore, it is necessary to galvanize before copper plating to increase the thickness of the zinc layer.
Keywords: aluminum alloy; Secondary zinc leaching; Cyanide galvanized; Bright silver plating
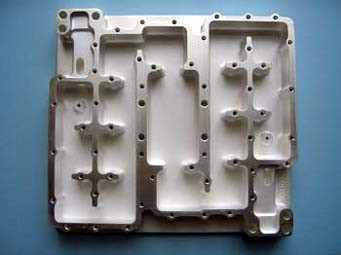
1. Introduction
Aluminum alloy silver plating is widely used in electronics, communications, electrical appliances and other industries. However, since aluminum is a very active metal, it has a strong affinity for oxygen and forms an oxide film on the surface. At the same time, the coefficient of thermal expansion of aluminum and its alloys is very different from that of silver, which makes it difficult to plate silver on aluminum parts.
[1]. The larger the part size and the more complex the shape, the more difficult the plating. Many parts of a military filter are aluminum alloy (brand 7R04-Hll2) silver plated parts, in which the main component U, V-type cavity silver plating is the most difficult. The size of the cavity is 316mm × 190mm × 93mm, the surface area is 40.6dm2, and the inner cavity size is l80mm × 56mm × 90mm (deep). The shape of the cavity is shown in Fig. l. Silver plating is required (23±2) μm and electrolytic passivation.
The part has a large volume and a deep cavity. To obtain a silver plated layer with good adhesion, pretreatment before plating is the key. Many researches on the pretreatment of aluminum and its alloys have been carried out at home and abroad. The author conducted a large number of experiments on the basis of summarizing these methods.
Turn Out:
The pretreatment process combined with secondary zinc leaching and potassium chloride galvanization was replated with silver, and most of the cavities had peeling, blistering and shedding.
In the pretreatment process combining secondary zinc leaching and cyanidation galvanizing, cyanide plating of copper and silver results in fine crystals, good lightness, and strong bonding power, which can better meet the quality requirements of military products.
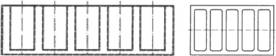
Figure1 Shell structure
2.1 Process flow
Organic degreasing- chemical degreasing- Alkali corrosion- Acid etching- Zinc leaching- pickle acid- heavy zincate- Cyanide galvanizing- Copper plating- Pre- plated silver- bright silver plated- An electrolytic passivation is blow dried and dried.
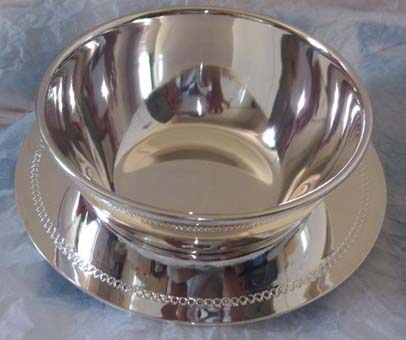
2.2 Solution Formulas and Process Conditions for Each Major Process
2.2.1 Organic Degreasing
At room temperature, using l80 # aviation gasoline.
2.2.2 Chemical Degreasing
Type B 898 degreasing Ling | 50g/L |
θ | <50℃ |
t | 2~10min |
2.2.3 Alkali corrosion
The purpose of the alkali etching is to remove the oxide film on the surface of the aluminum part, to obtain an ideal micro-roughness, and to further remove the oil, so as to increase the binding force of the coating. The response is faster and time should be strictly controlled.
NaOH | 80—100g/L |
θ | 60~700 |
Ct | 0.5~1 min |
After alkali etching, copper, silicon, manganese, etc. in aluminum and its alloys do not dissolve in alkaline substances, and remain on the surface of the workpiece and the corrosion residue forms a "hanging ash" adsorption film.
The purpose of the etching is to dissolve these attachments, leaving the workpiece exposed to a bright surface and in a good state of activation.
(1) Suitable for general aluminum alloy parts
HN03(p=1.639/mL) | 500 mL/L |
t | Room temperature |
f | 5~10S |
(2) Suitable for silicon aluminum alloy pieces
HN03(p=1.63g/mL) | 500 mL/L |
HF(W≈40%) | 60 mL/L |
θ | Room temperature |
t | 5~10S |
Zn0 | 100g/L |
NaOH | 500g/L |
NaKC4H406·2H20 |
10g/L |
FeCl3·6H20 | 1g/L |
HF(w≈40%) | 3 mL/L |
θ | 25~30℃ |
t |
45—60S |
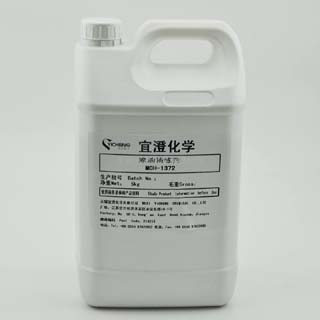
The secondary zincation process has obvious effects on improving the quality of the zinc-impregnated layer and improving the bonding force. This is due to the fact that for the first time of zinc immersion, Al203 must be dissolved before replacing Al. The resulting zinc layer has a rough and loose crystal, uneven distribution of crystal grains, large size difference, and poor adhesion of the zinc-impregnated layer. The secondary zinc immersion method can improve the adhesion, uniformity and corrosion resistance of subsequent coatings. When the zinc crystal grains with poor bonding between the surface of aluminum and its alloys are dissolved in nitric acid, the large grain size of the zinc grains becomes smaller and a uniform and detailed surface is formed. The exposed grains become the nucleation centers for the secondary zinc immersion, so the resulting zinc layer is fine and the bond with the substrate is enhanced.
The process conditions are:
Zn(NO)2 | 30g/L |
NaOH | 200g/L |
C6H807 | 40g/L |
FeCl3·6H20 | 1g/L |
θ | 15~30℃ |
Ct | 30~60S |
2.2.7 Cyanide galvanizing
For the complex shape of the Shell part, although the secondary zinc-immersing, the zinc layer deposited in the crucible and the deep depression is relatively thin, and the subsequent copper plating is prone to dissolution due to the strong alkalinity and the higher temperature. In this way, the protective effect of the zinc layer on the aluminum surface layer is lost, and the adhesion of the plating layer is severely reduced. Therefore, it is necessary to galvanize before copper plating to increase the thickness of the zinc layer.
Zn0 | 35~459/L |
NaCN | 70~90g/L |
NaOH | 60~70g/L |
95 cyanide galvanizing and opening agent | 5 mL/L |
95 cyanide zinc plating brightener | 3~5 mL/L |
θ | 5~30℃, |
J | O.5~3 A/dm2 |
t | 2~5 min |
2.2.8 Copper plating
2.2.9 Pre-plated Silver
CuCN | 55~85g/L |
NaCN(free) | 10~15g/L |
991Brightener | l0~12mL/L |
θ | 55~65℃, |
J | 1~3 A/dm2 |
t | 10~15 min |
Stirring method | Cathode move |
Ag(以KAg(CN)2加入) | 1~2g/L |
KCN | l00g/L |
anode | Stainless steel plate |
J | 1~2 A/dm2 |
θ | 10~30℃ |
Ct | 5~10S |
2.2.10 Silver Plating
The current density of cyanide copper plating has an important influence on the quality of the coating. With different cathode current densities, the binding force of the coating varies greatly. Experiments show that the current density should be limited to the allowable value within a short period of time after the start of energization and then be reduced to near the lower limit for electroplating. In this way, all parts of the workpiece can be deposited with copper so as to improve the adhesion of the subsequent silver plating layer; Otherwise, the workpiece will not be deposited on the crucible or in the deep recess, and the silver plating layer will have poor adhesion. In addition, when cyanide copper plating, parts should be charged under the groove in order to prevent replacement of the copper layer.
4.7 Auxiliary Cathodes for Bright Silver Plating
It was found in the experiment that if a protective cathode is used during electroplating of silver, the coating on Shell's surface is crystallized with fineness and uniformity; Otherwise, the coating on the external corner of the shell is scorched. When the auxiliary anode is used for electroplating silver, the thickness of the shell plating inside the shell is uniform, otherwise the shell plating inside the shell is thinner at the sharp corners, which affects the quality of the plating. Therefore, in the bright silver plating, on the one hand, a protective cathode is used, and on the other hand, an auxiliary anode is suspended inside the shell. Auxiliary anodes are made of silver strips and there should be enough anodes in each cavity. The silver anode is partially glued with insulating tape to avoid shorting the silver anode to the shell.
5 Conclusion
A zinc-galvanizing and zinc-plating combined pretreatment process is used to obtain bright silver plating on the surface of aluminum and its alloys, which is characterized by fine crystals, good brightness, and strong bonding force.
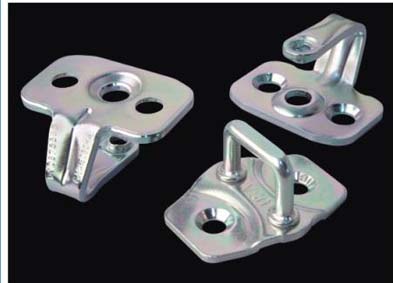
Ag(以KAg(CN)2 Join) | 20~40g/L |
KCN(free) | 90~150g/L |
KOH | 5~10g/L |
Silver Brightener A | 30mL/L |
Silver Brightener B | 15 mL/L |
θ | 10~30℃ |
J | 0.5~1.5 |
Stirring method | Cathode move |
2.2.11 Electrolysis passivation
3. Plating performance test
3.1 Appearance test
The visual observation method observes the smoothness of the coating, the evenness of the color, and whether there are blemishes such as peeling, blistering, peeling off, pitting, spots, and burns.
3.2 binding force test
3.2.1 Cross-cut method
On the sample, use a steel knife to draw several squares with a side of 1 mm × 1 mm. Observe whether the coating in this area is blistering or falling off.
3.2.2 hot and cold cycle method
Place the sample in an electric oven at 200°C and incubate for 1 h. Immediately after removal, it is placed in a water of 18° C. to 25° C. to cool, and it is checked whether the coating is blistering or falling off.
4. Factors affecting the plating performance
4.1 Alkali and Acid Etching
The experiment found that the temperature of alkali etching is too high and the time is too long, and the shell surface is easily over-etched; When the temperature is too low and the time is too short, the uneven oxide film on the shell surface is not completely removed, resulting in a decrease in the plating adhesion. In addition, in order to remove the mixture of tri-alumina, silicon alloy elements and their oxides formed after the alkali etching of the Shell surface, the workpiece is in a good activated state, Different aluminum alloy components usually use different acid etching solutions, which have a greater impact on the binding force of the coating.
4.2 Pretreatment
Table 1 shows the effect of different pretreatment process combinations on coating quality. It can be seen from the table that only the pretreatment process of the combination of secondary zinc immersion and galvanizing provides a crystal with fine grain, strong bonding force, good lightness, and good coating quality. Shell has a very small part of blistering due to poor water during operation caused.
Table 1 Effect of Pretreatment Process on Coating Quality
4.3 The temperature of the zinc dipping solution
The temperature of the zinc dipping solution has a great influence on the quality of the coating. In the zinc deposition process, for the same aluminum substrate, if the temperature is different, the deposition rate is also different, and the temperature of the zinc crystallizes faster when the temperature is increased. If the temperature is too high, the reaction is too fast, the zinc layer is thick, the crystals are rough, the solution life is short, the bonding strength of the coating is poor, and the batch pass rate is low; If the temperature is too low, the reaction is slow, the zinc layer is thin, easy to break down during pre-plating, and the bonding strength is poor. It is known from the experiment that the zinc immersion should be carried out at 25-30° C. The resulting coating is uniform, dense, with good bonding force and a high batch pass rate.
4.4 Preparation of Zinc Dipping Solution
Lashmore proposed that the addition of trivalent iron ions has a great influence on the zinc leaching reaction. Therefore, in order to crystallize the zinc immersion layer, FeCl3 needs to be added to the solution. The experimental results show that the addition order of ferric ions also seriously affects the performance of the coating. Addition of FeCl3 and NaKC4H406 has a significant effect on the reaction. If ferric chloride is added directly to the sodium hydroxide solution, the resulting coating foams and falls off. This is because under alkaline conditions, iron ions tend to form precipitates, which reduces the effective concentration of iron in the solution. Ferric chloride should be first dissolved in potassium sodium tartrate solution, zinc oxide dissolved in sodium hydroxide solution, and then mixed, resulting in good binding of the coating, the batch pass rate is high.
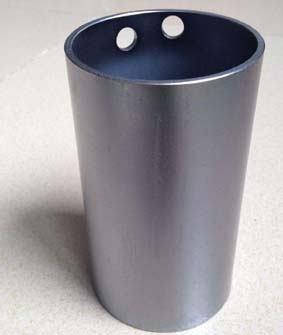
4.5 Zinc dipping time
When the time of zinc immersion is more than 60s, the zinc layer is thick, the crystal is rough, the bonding power is poor, and the batch pass rate is low. When the first zinc immersion time is less than 45 seconds and the second zinc immersion time is less than 30 seconds, the resulting zinc layer is thin, easy to break down during pre-plating, and the coating adhesion is poor. Therefore, the first zinc immersion should be controlled at 45-60S, and the second zinc immersion time should be 30-60 s. The obtained coating is uniform, dense, with high bonding force and high batch passing
4.6 Cathode Current Density in Cyanide Copper PlatingKECr204 | 8~10g/L |
K2C03 | 6~8g/L |
pH | 9~10 |
θ | 10~35℃ |
J | 0.5~1 A/dm2 |
t | 2~5 min |
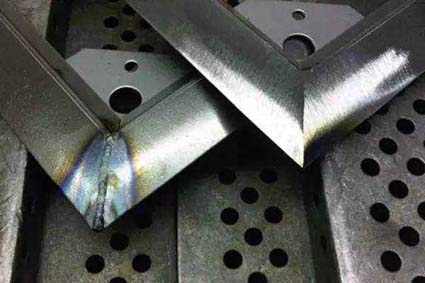
3.1 Appearance test
The visual observation method observes the smoothness of the coating, the evenness of the color, and whether there are blemishes such as peeling, blistering, peeling off, pitting, spots, and burns.
3.2 binding force test
3.2.1 Cross-cut method
On the sample, use a steel knife to draw several squares with a side of 1 mm × 1 mm. Observe whether the coating in this area is blistering or falling off.
3.2.2 hot and cold cycle method
Place the sample in an electric oven at 200°C and incubate for 1 h. Immediately after removal, it is placed in a water of 18° C. to 25° C. to cool, and it is checked whether the coating is blistering or falling off.
4. Factors affecting the plating performance
4.1 Alkali and Acid Etching
The experiment found that the temperature of alkali etching is too high and the time is too long, and the shell surface is easily over-etched; When the temperature is too low and the time is too short, the uneven oxide film on the shell surface is not completely removed, resulting in a decrease in the plating adhesion. In addition, in order to remove the mixture of tri-alumina, silicon alloy elements and their oxides formed after the alkali etching of the Shell surface, the workpiece is in a good activated state, Different aluminum alloy components usually use different acid etching solutions, which have a greater impact on the binding force of the coating.
4.2 Pretreatment
Table 1 shows the effect of different pretreatment process combinations on coating quality. It can be seen from the table that only the pretreatment process of the combination of secondary zinc immersion and galvanizing provides a crystal with fine grain, strong bonding force, good lightness, and good coating quality. Shell has a very small part of blistering due to poor water during operation caused.
Table 1 Effect of Pretreatment Process on Coating Quality
Pretreatment process | Plating quality |
once Zinc leaching | Coarse crystals, poor light, most of Shell from the skin, blistering, loss |
Twice Zinc leaching | The outer surface is crystal-clear with good lightness, and the inner surface of the shell has peeling and blistering. |
Combined secondary zinc immersion and zinc plating | Crystallized, good light, very few shells have blisters |
Dip zinc-nickel alloy | The outer surface of the surface is scorched, and the inner surface of the shell is peeled, blisters, and peeled off. |
Pre-galvanized | Poor brightness, shell surface peeling, blistering, shedding |
4.3 The temperature of the zinc dipping solution
The temperature of the zinc dipping solution has a great influence on the quality of the coating. In the zinc deposition process, for the same aluminum substrate, if the temperature is different, the deposition rate is also different, and the temperature of the zinc crystallizes faster when the temperature is increased. If the temperature is too high, the reaction is too fast, the zinc layer is thick, the crystals are rough, the solution life is short, the bonding strength of the coating is poor, and the batch pass rate is low; If the temperature is too low, the reaction is slow, the zinc layer is thin, easy to break down during pre-plating, and the bonding strength is poor. It is known from the experiment that the zinc immersion should be carried out at 25-30° C. The resulting coating is uniform, dense, with good bonding force and a high batch pass rate.
4.4 Preparation of Zinc Dipping Solution
Lashmore proposed that the addition of trivalent iron ions has a great influence on the zinc leaching reaction. Therefore, in order to crystallize the zinc immersion layer, FeCl3 needs to be added to the solution. The experimental results show that the addition order of ferric ions also seriously affects the performance of the coating. Addition of FeCl3 and NaKC4H406 has a significant effect on the reaction. If ferric chloride is added directly to the sodium hydroxide solution, the resulting coating foams and falls off. This is because under alkaline conditions, iron ions tend to form precipitates, which reduces the effective concentration of iron in the solution. Ferric chloride should be first dissolved in potassium sodium tartrate solution, zinc oxide dissolved in sodium hydroxide solution, and then mixed, resulting in good binding of the coating, the batch pass rate is high.
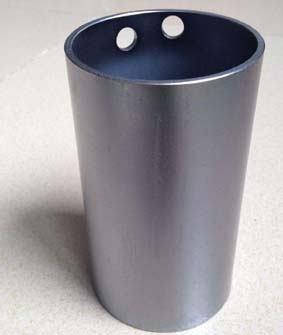
4.5 Zinc dipping time
When the time of zinc immersion is more than 60s, the zinc layer is thick, the crystal is rough, the bonding power is poor, and the batch pass rate is low. When the first zinc immersion time is less than 45 seconds and the second zinc immersion time is less than 30 seconds, the resulting zinc layer is thin, easy to break down during pre-plating, and the coating adhesion is poor. Therefore, the first zinc immersion should be controlled at 45-60S, and the second zinc immersion time should be 30-60 s. The obtained coating is uniform, dense, with high bonding force and high batch passing
The current density of cyanide copper plating has an important influence on the quality of the coating. With different cathode current densities, the binding force of the coating varies greatly. Experiments show that the current density should be limited to the allowable value within a short period of time after the start of energization and then be reduced to near the lower limit for electroplating. In this way, all parts of the workpiece can be deposited with copper so as to improve the adhesion of the subsequent silver plating layer; Otherwise, the workpiece will not be deposited on the crucible or in the deep recess, and the silver plating layer will have poor adhesion. In addition, when cyanide copper plating, parts should be charged under the groove in order to prevent replacement of the copper layer.
4.7 Auxiliary Cathodes for Bright Silver Plating
It was found in the experiment that if a protective cathode is used during electroplating of silver, the coating on Shell's surface is crystallized with fineness and uniformity; Otherwise, the coating on the external corner of the shell is scorched. When the auxiliary anode is used for electroplating silver, the thickness of the shell plating inside the shell is uniform, otherwise the shell plating inside the shell is thinner at the sharp corners, which affects the quality of the plating. Therefore, in the bright silver plating, on the one hand, a protective cathode is used, and on the other hand, an auxiliary anode is suspended inside the shell. Auxiliary anodes are made of silver strips and there should be enough anodes in each cavity. The silver anode is partially glued with insulating tape to avoid shorting the silver anode to the shell.
5 Conclusion
A zinc-galvanizing and zinc-plating combined pretreatment process is used to obtain bright silver plating on the surface of aluminum and its alloys, which is characterized by fine crystals, good brightness, and strong bonding force.