Wire Drawing
Brushed metal surface treatment is a kind of surface treatment means that grinds the product to form a line on the surface of the workpiece and plays a decorative effect. Since the surface drawing process can reflect the texture of the metal material, it has been more and more popular and more and more widely used by users.
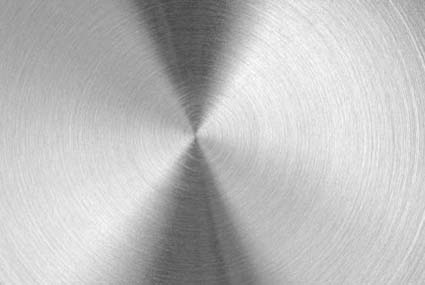
Introduction
Wire drawing is a metal processing process. In metal pressure processing. Under the action of external force to force the metal through the die, the metal cross-sectional area is compressed, and to obtain the required cross-sectional area shape and size of the technical processing method, called the metal wire drawing process. A tool that changes the shape of a metal surface and its dimensions is called a wire drawing die.
Surface treatment
Surface wire drawing is a kind of surface treatment means that grinds the product to form a line pattern on the surface of the workpiece and plays a decorative effect. Since the surface drawing process can reflect the texture of the metal material, it has been more and more popular and more and more widely used by users. This article will discuss the method of surface wire drawing from aspects of wire drawing application, classification, processing methods, wire-grinding products, and related factors of wire drawing.
Application
There are many different forms of metal surface treatment.
For example: sandblasting (forming matt pearl silver surface), polishing (mirror forming), embossing (pressing various textures), electroplating (covering a layer of other metals), Spray (covers other non-metallic coatings), as wire drawing (forms a satin-like effect). Compared to other surface treatments, wire drawing gives the metal surface a non-mirror-like metallic luster, which has a very strong decorative effect like silk satin. It is like giving ordinary metals new life and life, so wire drawing has more and more market recognition and wide application.
In the construction industry there are elevator door panels, escalator decorative panels, Leading, hinge, handle, lock trim, etc. in the architectural hardware industry; Kitchenware such as range hoods, stainless steel cookers, sinks, etc. The rise of various 3C digital products in recent years has pushed the application of wire drawing to a climax, such as the notebook computer panel, keyboard board, mobile phone panel, LCD frame, battery cover, camera protection slider, Digital camera lens slide cover and so on. There are other various electronic products, such as: Mp3, Mp4, DVD players, projectors, and so on. And what we commonly find are locks, furniture, luggage accessories and so on.
Classification
Wire drawing can also be generally called Grit sweeping, sweeping nylon and so on. It is usually divided into straight wire and tangled wire depending on the surface effect. Straight silk, also known as hairline, chaotic silk, is also called snow pattern, and the goodness of the silk pattern is subjective. Each user has different requirements for the surface line pattern and different preferences for the line pattern effect. The line pattern effect is often difficult to describe and define because of the variety of changes. It is determined by the method of drawing the wire, the grinding product used, and the process parameters to determine the effect of the wire drawing. Let's further discuss the processing method of surface wire drawing.
Processing Methods
Surface wire drawing processing methods, according to the requirements of the wire drawing effect, the size and shape of the different workpiece surface to choose different processing methods. Wire drawing methods include manual wire drawing and mechanical wire drawing. The common manual wire drawing is used in 3M's industrial scouring pad, such as 8698, 7447C, etc. The following focuses on the method of mechanical wire drawing.
Common mechanical wire drawing methods are the following:
1.Flat pressure sand belt wire drawing:
Flat pressure wire drawing is a very common wire drawing method. The workpiece is fixed on the mold and the abrasive belt runs at high speed. The back of the belt has a pneumatically controlled pressure block that can be moved up and down. After pressing down, the belt is attached to the machined surface for wire drawing. The commonly used equipment is a flat belt sander. Flat pressure wire drawing Suitable for wire drawing surface with small area, it is widely used in wire drawing of digital camera case, wire drawing of mobile phone case and so on. The line drawn out of this wire drawing surface is usually a straight silk thread. Due to the use of abrasive belts, a wide range of particle size ranges are available, Therefore, it is possible to use coarse-grained abrasive belts to produce rough and distinctly textured lines. Fine-grained belts can also be used to produce finer lines. 3M can not only provide ordinary belts, but also provide pyramidal belts and non-woven nylon belts that are more suitable for wire drawing. The abrasive belts grind wire drawing on the entire surface, generating a lot of heat and causing stress concentration on the wire drawing side of the workpiece, especially for thin-walled parts. So this method is suitable for small area wire drawing processing. Since it is a push-down type operation, it is usually applied to a plane, and the surface cannot have a ledge, such as a raised text logo or the like. However, wire drawing can also be performed on slightly curved workpieces through the ingenious design of a mold such as a briquetting block. The specific method depends on the degree of bending to discuss specifically.

2, non-woven roller brush wire drawing:
The workpiece is conveyed by a conveyor belt through a non-woven roller brush, and the roller brush performs wire drawing on the surface of the workpiece at a high speed. Wire drawing can be used in two ways: roller brush vibration and non vibration. At the same time with different processing speed to produce different length lines. Non-woven roller brush vibration, can produce a very uniform discontinuous thread (short wire); Non-woven roller brushes do not vibrate and can produce continuous filaments (filaments or straight filaments). This kind of wire drawing method is becoming more and more widely used in notebooks' magnesium/aluminum alloy panels, keyboard boards, cell phone LCD boxes, battery covers, camera protection boards, camera slide covers, and so on.
The advantages of the roller brush wire drawing method are:
1> can be suitable for large-area wire drawing, because the wire drawing uses the line contact way, not the flat pressure type face contact, thus avoids the massive heat generation. At the same time, non-woven structure grinding products are used, and there is a good cold grinding effect. (Features of non-woven structure will be specifically introduced in the back wire drawing abrasive products). In addition, the non-woven roller brush can be very wide (3M's non-woven roller brush, roller brush width up to 1219mm), the plate can be processed can be very long.
2> With this wire drawing method, the wire drawing surface can have a certain curvature, or even a small protrusion, such as a text logo, etc. Because the non-woven roller brush has a good adhering property (the characteristics of the non-woven structure will be described in the later wire drawing grinding products).
3> Continuous operation can improve the production efficiency.
4> A roller brush that can produce two types of wire drawing lines with vibration and no vibration.
The line pattern of the non-woven roller brush wire drawing did not have a concavo-convex texture, but the visual appearance of the line pattern was obvious.
3, wide abrasive wire drawing:
This wire drawing method is the most traditional wire drawing method for plane wire drawing, especially suitable for sheet metal processing. As shown in the figure, the belt rotates at a high speed, and the metal plate passes through the belt through the conveyor belt, Polished wire drawing. Usually, stainless steel plates, aluminum alloy plates, etc. are made into wire drawing semi-finished products, so as to further produce products that use plate materials as raw materials. Such as stainless steel wire drawing door panels, stainless steel counters, aluminum chassis and so on. The line drawn in this way is usually very thin and short, and can be called snow pattern. This method requires that the belt has good conformability and the line effect of the plate can be more uniform. This method requires that the belt has good conformability and the line effect of the plate can be more uniform. 3M's non-woven sands have better conformability than conventional coated belts.
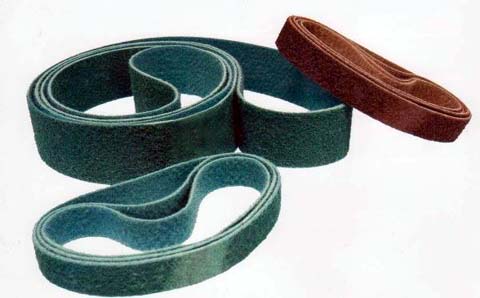
4, no heart grinding wire drawing:
This is carried out by way of centerless grinding wire drawing fashion. The grinding products used are non-woven wire drawing rounds or abrasive bands. Suitable tube-shaped workpiece, for example, the handle grip and the like. The wire drawing of this method is usually a short thread, The length of silking is related to the rotational speed of the workpiece, the rotational speed of the abrasive product, and the abrasive product itself.
5, polishing machine wire drawing:
It only uses the speed of the machine to drive the nylon wheel and polish the product through artificial technology. Suitable for irregular plating products.
Application area
Home Appliance Panels, Various Digital Product Peripherals and Panels, Laptop Panels, For the production of a variety of logos, membrane switches, nameplates and so on.
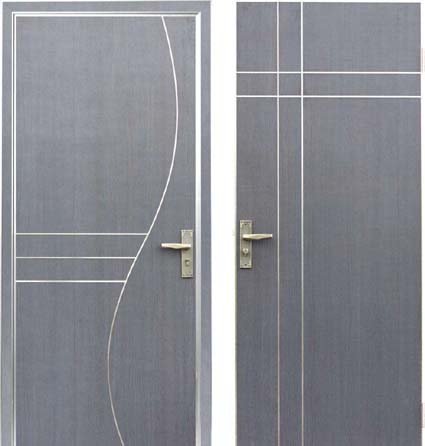
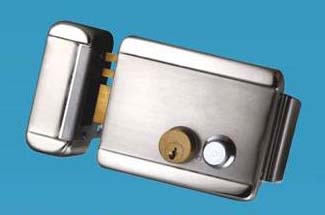
Material properties
Commonly used material thickness 0.125,0.175,0.254,0.38,0.5,0.8,1.0MM
Transparency 90%
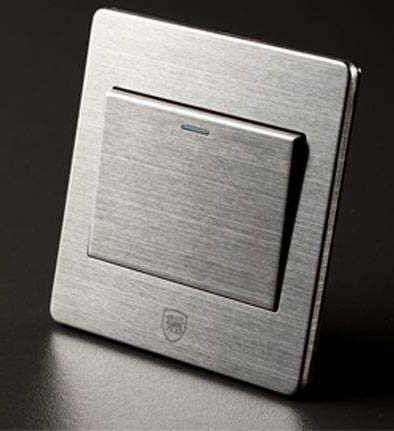