What are the safe operating procedures for CNC boring machines?
What are the specific safety procedures for CNC boring machines?
What are the things that need to be observed?
It is now introduced to its safe operating procedures in order to have a better understanding of CNC boring machines.
The safe operating procedures for CNC boring machines are:
(1) comply with the general safety procedures milling and boring work. Wear labor protection products as required.
(2) Check whether the connection of the operating handle, switch, knob, clamp mechanism and hydraulic piston is in the correct position, whether the operation is flexible, and whether the safety device is complete and reliable.
(3) Check whether there are obstacles in the machine tool the effective operating range of each axis.
(4) It is strictly forbidden to use the machine tool beyond the performance. According to the workpiece material, the cutting speed and feed rate of the whole process are selected.
(5) When loading and unloading heavy workpieces, reasonable spreaders and lifting methods must be selected according to the weight and shape of the workpiece.
(6) When the spindle rotates, it is strictly forbidden to touch the spindle and the tool attached to the end of the spindle by hand.
(7) When replacing the tool, it must be stopped first, and it can be replaced after confirmation. When cutting, you should pay attention to the damage of the blade.
(8) It is forbidden to step on the rail surface of the equipment and the surface of the paint or place items on it. Do not tap or straighten the workpiece on the workbench.
(9) After inputting the machining program for the new workpiece, you must check the correctness of the program and simulate whether the running program is correct. Automatic cycling is not allowed without testing to prevent machine malfunction.
(10) When cutting with a flat-rotary radial tool holder, the mast should be returned to the zero position first, and then the M43 mode is used to change to the flat-rotary disk mode. If the U-axis is to be moved, make sure that the U-axis manual clamping device has been released.
(11) When you need to rotate the table during work, make sure that it does not touch other parts of the machine while rotating, and cannot touch other objects around the machine.
(12) When the machine is running, it is forbidden to touch the rotating wire shaft, polished rod, main shaft, or flat disk. The operator must not rest on the moving parts of the machine.
(13) The operator is not allowed to leave the job or take care of the person while the machine is running.
(14) If abnormal phenomena and noises occur during the operation of the machine tool, stop it immediately, find out the cause and deal with it in time.
(15) When the headstock of the machine tool is at or near the limit of motion, the operator must not enter the following areas:
a. between the bottom of the headstock and the bed;
b. between the axis and the work;
c. between the bed and the work surface when the shaft is extended;
d. between the worktable and the headstock;
e. When the boring shaft rotates, the rear tail cylinder is between the wall and the fuel tank;
f. between the workbench and the front main column;
g. Other areas that may cause crushing.
(16) When the machine is shut down, the workbench must be retracted to the middle position, the mast is returned, then the operating system is removed, and finally the power is turned off.
What are the things that need to be observed?
It is now introduced to its safe operating procedures in order to have a better understanding of CNC boring machines.
The safe operating procedures for CNC boring machines are:
(1) comply with the general safety procedures milling and boring work. Wear labor protection products as required.
(2) Check whether the connection of the operating handle, switch, knob, clamp mechanism and hydraulic piston is in the correct position, whether the operation is flexible, and whether the safety device is complete and reliable.
(3) Check whether there are obstacles in the machine tool the effective operating range of each axis.
(4) It is strictly forbidden to use the machine tool beyond the performance. According to the workpiece material, the cutting speed and feed rate of the whole process are selected.
(5) When loading and unloading heavy workpieces, reasonable spreaders and lifting methods must be selected according to the weight and shape of the workpiece.
(6) When the spindle rotates, it is strictly forbidden to touch the spindle and the tool attached to the end of the spindle by hand.
(7) When replacing the tool, it must be stopped first, and it can be replaced after confirmation. When cutting, you should pay attention to the damage of the blade.
(8) It is forbidden to step on the rail surface of the equipment and the surface of the paint or place items on it. Do not tap or straighten the workpiece on the workbench.
(9) After inputting the machining program for the new workpiece, you must check the correctness of the program and simulate whether the running program is correct. Automatic cycling is not allowed without testing to prevent machine malfunction.
(10) When cutting with a flat-rotary radial tool holder, the mast should be returned to the zero position first, and then the M43 mode is used to change to the flat-rotary disk mode. If the U-axis is to be moved, make sure that the U-axis manual clamping device has been released.
(11) When you need to rotate the table during work, make sure that it does not touch other parts of the machine while rotating, and cannot touch other objects around the machine.
(12) When the machine is running, it is forbidden to touch the rotating wire shaft, polished rod, main shaft, or flat disk. The operator must not rest on the moving parts of the machine.
(13) The operator is not allowed to leave the job or take care of the person while the machine is running.
(14) If abnormal phenomena and noises occur during the operation of the machine tool, stop it immediately, find out the cause and deal with it in time.
(15) When the headstock of the machine tool is at or near the limit of motion, the operator must not enter the following areas:
a. between the bottom of the headstock and the bed;
b. between the axis and the work;
c. between the bed and the work surface when the shaft is extended;
d. between the worktable and the headstock;
e. When the boring shaft rotates, the rear tail cylinder is between the wall and the fuel tank;
f. between the workbench and the front main column;
g. Other areas that may cause crushing.
(16) When the machine is shut down, the workbench must be retracted to the middle position, the mast is returned, then the operating system is removed, and finally the power is turned off.
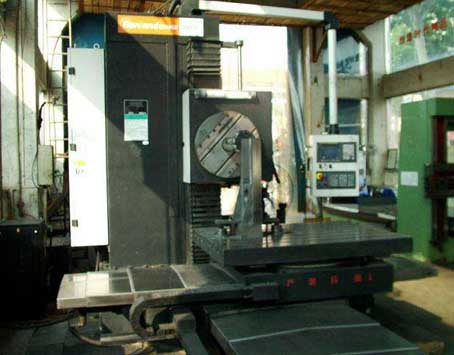