The perfect Combination Of In-Die Tapping Technology In Automatic Stamping Production
The stamping industry needs to process stampings for forming threads. Many manufacturers still stay in single punch or after stamping products, and then carry out secondary operations such as manual tapping, active tapping, etc. This is a waste of traditional processing technology. The in-mold tapping skills can be combined with the automatic production of punching equipment to achieve the integration of punching and tapping. Whether it is to improve automation, increase efficiency or improve quality, the benefits of in-mold tapping technology to stamping production companies are enormous.
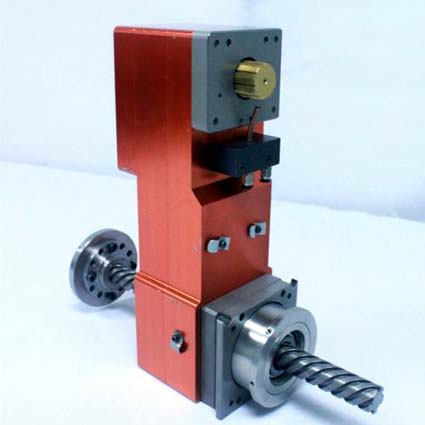
Comparison between traditional tapping and in-mold tapping:
1, Traditional tapping production methods
The traditional tapping production methods are generally processed by single punch or automatic press forming process, transfer process, manual tapping, or active tapping process, resulting in high production cost, low efficiency, and lack of guarantee of product consistency.
The total cost includes: stamping process costs, transfer costs, and tapping costs.
2. In-die tapping method
The mode of production of in-mold tapping is completed by the automatic integration of stamping “forming + tapping”. The production speed is fast, the efficiency is high, and the thread quality is stable.
The total cost includes: stamping processing costs + tapping machine investment in the mold, while the mold tapping machine is a capital investment.
Materials: In-Die Tapping Technology is available for low carbon steel, stainless steel, aluminum and aluminum alloys, brass plates, and copper plates.
The screw tap category used by In-Die Tapping Technology is a chipless kneading screw tap. Kneading the screw tap is a new type of thread cutting tool that uses the metal plastic deformation principle to process the internal thread, without cutting edge and chip flutes. However, there are one or more smooth oil grooves, and the shape of the screw tap is multi-diamond, which is a chipless processing technology. The threads extruded by the kneading screw tap have a high surface finish, the metal fibers of the threads do not crack, and form a layer of chilled layer on the outer surface, which can improve the strength and wear resistance of the threads. It fundamentally solves the difficult problem of tapping the tapping, because no chip discharge, more conducive to the assembly of the thread. Instead of cutting metal during tapping, threads are formed by metal plasticity. Therefore, the diameter is larger than the diameter of the thread, and the kink formed thread shape is u-shaped.
In-Die Tapping features:
(1) screw tap replacement is quick and can be completed in just 1 min.
(2) The screw tap device is divided into three methods: fixed, floating and suspended. The device can be accurately positioned according to customer requirements.
Fixed type
(1) The left-handed or right-handed thread can be formed according to the product requirements.
(2) Six-point concentric colleting technology ensures the high precision of thread forming.
(3) selection of mold tapping device double protection insurance, tapping the punching safe and fast.
Floating
(1) screw tap and atomization cooling and smoothing system WD-10 for equipment and punch synchronization signals, with good fuel economy and cooling effect.
(2) Fast tapping speed, up to 120 holes/minute, high efficiency.
(3) After replacing lead assemblies of different standards, different thread dimensions can be formed on the same body.
Suspension type
(1) The model is exquisite, does not occupy the mould space, does not affect the model cost, the elastic device planning.
(2) Closed and smooth circulation, convenient operation and maintenance.
(3) There are single-hole type, porous type, horizontal type, combined type, and servo-driven series models that can satisfy various conditions of use.
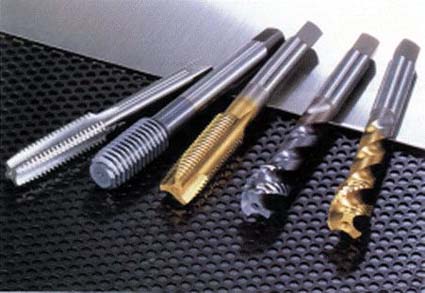
Influencing factors
If you do not consider the factors such as product technology, the main factors affecting the In-Die Tapping role are: tapping speed, screw tap life, mold planning and equipment, tapping oil selection.
(1) Tapping speed.
The following factors affect the in-mold tapping speed: thread bottom hole, tapping depth, feed point of view, product raw material, screw tap quality, cooling effect.
(2) screw tap life.
The main factors affecting the life of the screw tap are the following nine:
Thread bottom hole, thread depth, tapping speed, product raw material, feeding accuracy, screw tap quality, cooling effect, correct device, national standard.
(3) mold planning and installations.
The prerequisite for the introduction of In-Die Tapping skills is that it is necessary to have the device space. This requires all manufacturers who import this skill to change the production process, but also to innovate existing molds. Newly developed successive metal molds, the mold core is divided into two parts during planning, leaving the device space, the original mold has the planning and repair space for the preparation of the process positions, modified or multi-process mold with planned reserve positions, can be introduced into the device In-Die Tapping skills.
(4) Selection of tapping oil.
Appropriate tapping oils should be selected according to the materials in production. In addition, when processing deep holes, we can add the number of smooth oil grooves on the kneading tap to facilitate smoothness.
The use of In-Die Tapping skills in planer blade production
The production process of domestic planer blade companies has only stayed in the artificially combined semi-automatic processing conditions. Its traditional processing methods and numerous processes consume a lot of resources and profitable space. Slow production progress and unstable quality. In response to this situation, many companies have begun the pace of technological innovation and achieved excellent results. Original planing blade products, product thickness 3.8MM, raw material Q235. Its processing procedures are numerous and the process is messy.
The use of the In-Die Tapping technology to automate the stamping integration system requires only two stamping production processes to complete the processing of the product. After the In-Die Tapping dental auto stamping system selects the coiling material to carry out blank blanking and blanking, the robot welding machine is used to perform rough embryo welding of blades into the product. Automated production lines (punching + in-mold tapping) complete the production of finished products.
After the new process is selected, the change in length dimension of the product after stamping is less than 0.2mm, the meandering amount of the side bend (inset steel edge) is less than 0.1mm (change amount before and after punching), and the plane zigzag is less than 0.2mm. The punching section of each hole, the minimum 1/3 smooth surface to ensure the data thickness, 2/3 section, no appearance defects such as tearing, sticking, etc. The height of the stamped corner is less than 0.3mm, and the threads are full after threading. No teeth, fangs and other conditions. Its normal mass production reaches 6000 pieces / 8 hours or more, far higher than the 1500 pieces / 8 hours of the old craft. Production power has increased significantly, production costs and resource depletion have been well controlled, and the company’s product competitiveness has been further enhanced.
After the actual comparison of the old and new technologies and the production return visit, no matter how the product appearance, scale accuracy, production power, stability, and workshop production environment are still equipment protection operations have reached a new level of skills.
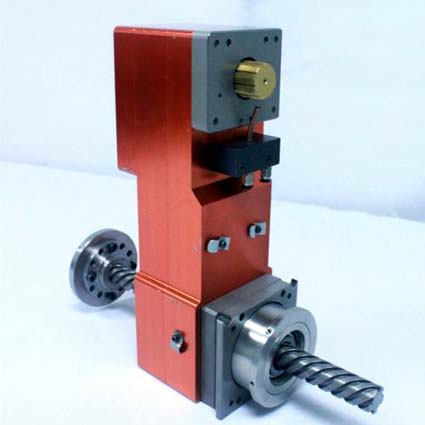
Comparison between traditional tapping and in-mold tapping:
1, Traditional tapping production methods
The traditional tapping production methods are generally processed by single punch or automatic press forming process, transfer process, manual tapping, or active tapping process, resulting in high production cost, low efficiency, and lack of guarantee of product consistency.
The total cost includes: stamping process costs, transfer costs, and tapping costs.
2. In-die tapping method
The mode of production of in-mold tapping is completed by the automatic integration of stamping “forming + tapping”. The production speed is fast, the efficiency is high, and the thread quality is stable.
The total cost includes: stamping processing costs + tapping machine investment in the mold, while the mold tapping machine is a capital investment.
Materials: In-Die Tapping Technology is available for low carbon steel, stainless steel, aluminum and aluminum alloys, brass plates, and copper plates.
The screw tap category used by In-Die Tapping Technology is a chipless kneading screw tap. Kneading the screw tap is a new type of thread cutting tool that uses the metal plastic deformation principle to process the internal thread, without cutting edge and chip flutes. However, there are one or more smooth oil grooves, and the shape of the screw tap is multi-diamond, which is a chipless processing technology. The threads extruded by the kneading screw tap have a high surface finish, the metal fibers of the threads do not crack, and form a layer of chilled layer on the outer surface, which can improve the strength and wear resistance of the threads. It fundamentally solves the difficult problem of tapping the tapping, because no chip discharge, more conducive to the assembly of the thread. Instead of cutting metal during tapping, threads are formed by metal plasticity. Therefore, the diameter is larger than the diameter of the thread, and the kink formed thread shape is u-shaped.
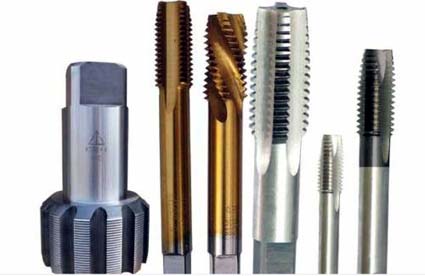
(1) screw tap replacement is quick and can be completed in just 1 min.
(2) The screw tap device is divided into three methods: fixed, floating and suspended. The device can be accurately positioned according to customer requirements.
Fixed type
(1) The left-handed or right-handed thread can be formed according to the product requirements.
(2) Six-point concentric colleting technology ensures the high precision of thread forming.
(3) selection of mold tapping device double protection insurance, tapping the punching safe and fast.
Floating
(1) screw tap and atomization cooling and smoothing system WD-10 for equipment and punch synchronization signals, with good fuel economy and cooling effect.
(2) Fast tapping speed, up to 120 holes/minute, high efficiency.
(3) After replacing lead assemblies of different standards, different thread dimensions can be formed on the same body.
Suspension type
(1) The model is exquisite, does not occupy the mould space, does not affect the model cost, the elastic device planning.
(2) Closed and smooth circulation, convenient operation and maintenance.
(3) There are single-hole type, porous type, horizontal type, combined type, and servo-driven series models that can satisfy various conditions of use.
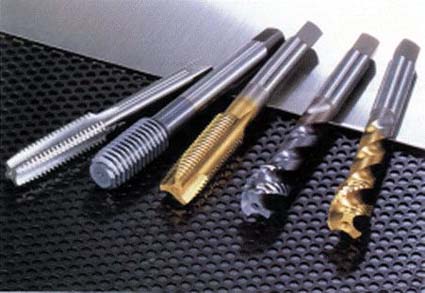
Influencing factors
If you do not consider the factors such as product technology, the main factors affecting the In-Die Tapping role are: tapping speed, screw tap life, mold planning and equipment, tapping oil selection.
(1) Tapping speed.
The following factors affect the in-mold tapping speed: thread bottom hole, tapping depth, feed point of view, product raw material, screw tap quality, cooling effect.
(2) screw tap life.
The main factors affecting the life of the screw tap are the following nine:
Thread bottom hole, thread depth, tapping speed, product raw material, feeding accuracy, screw tap quality, cooling effect, correct device, national standard.
(3) mold planning and installations.
The prerequisite for the introduction of In-Die Tapping skills is that it is necessary to have the device space. This requires all manufacturers who import this skill to change the production process, but also to innovate existing molds. Newly developed successive metal molds, the mold core is divided into two parts during planning, leaving the device space, the original mold has the planning and repair space for the preparation of the process positions, modified or multi-process mold with planned reserve positions, can be introduced into the device In-Die Tapping skills.
(4) Selection of tapping oil.
Appropriate tapping oils should be selected according to the materials in production. In addition, when processing deep holes, we can add the number of smooth oil grooves on the kneading tap to facilitate smoothness.
The use of In-Die Tapping skills in planer blade production
The production process of domestic planer blade companies has only stayed in the artificially combined semi-automatic processing conditions. Its traditional processing methods and numerous processes consume a lot of resources and profitable space. Slow production progress and unstable quality. In response to this situation, many companies have begun the pace of technological innovation and achieved excellent results. Original planing blade products, product thickness 3.8MM, raw material Q235. Its processing procedures are numerous and the process is messy.
The use of the In-Die Tapping technology to automate the stamping integration system requires only two stamping production processes to complete the processing of the product. After the In-Die Tapping dental auto stamping system selects the coiling material to carry out blank blanking and blanking, the robot welding machine is used to perform rough embryo welding of blades into the product. Automated production lines (punching + in-mold tapping) complete the production of finished products.
After the new process is selected, the change in length dimension of the product after stamping is less than 0.2mm, the meandering amount of the side bend (inset steel edge) is less than 0.1mm (change amount before and after punching), and the plane zigzag is less than 0.2mm. The punching section of each hole, the minimum 1/3 smooth surface to ensure the data thickness, 2/3 section, no appearance defects such as tearing, sticking, etc. The height of the stamped corner is less than 0.3mm, and the threads are full after threading. No teeth, fangs and other conditions. Its normal mass production reaches 6000 pieces / 8 hours or more, far higher than the 1500 pieces / 8 hours of the old craft. Production power has increased significantly, production costs and resource depletion have been well controlled, and the company’s product competitiveness has been further enhanced.
After the actual comparison of the old and new technologies and the production return visit, no matter how the product appearance, scale accuracy, production power, stability, and workshop production environment are still equipment protection operations have reached a new level of skills.
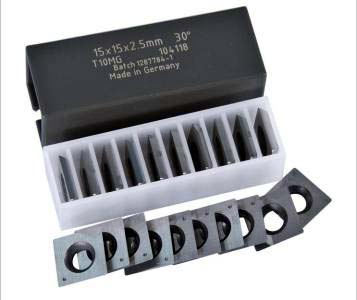