Sheet Metal Processing Process
With the development of today's society, sheet metal industry also will be developed rapidly, Now sheet metal involves all walks of life. For any sheet metal part, it has a certain processing process. The so-called process flow, to understand the sheet metal processing process, we must first know the choice of sheet metal materials.
Selection of materials
The commonly used materials for sheet metal are cold-rolled sheet (SPCC), hot-rolled sheet (SHCC), galvanized sheet (SECC, SGCC), copper (CU) brass, beryllium copper, aluminum sheet (6061, 6063, Hard aluminum, etc.), aluminum profiles, stainless steel (mirror, brushed surface, matt surface), depending on the role of the product, the choice of materials is different, generally need to consider the use of the product and the cost.
1. Cold-rolled plate SPCC: mainly used for electroplating and baking paint parts, low cost, easy molding, material thickness ≤ 3.2mm.
2. Hot-rolled plate SHCC: material T ≥ 3.0mm, also used for electroplating, paint parts, low cost, but difficult to shape, mainly used flat pieces.
3. Galvanized sheet SECC, SGCC: SECC Electrolytic plate divided N material, P material, N material is not mainly for surface treatment, high cost, P material for spraying parts.
4. Copper: The main use of conductive materials, the surface treatment is nickel, chrome, or no treatment, high cost.
5. Aluminum plate: generally used for surface chromate (J11-A), oxidation (conductive oxidation, chemical oxidation), high cost, silver plating, nickel plating.
6. Aluminium profile: The material with complex cross-section structure is widely used in a variety of subracks. Surface treatment with aluminum plate.
7. Stainless steel: Mainly used without any surface treatment, high cost.
Drawing review
To write the part's technological process, we must first know the various technical requirements of the parts drawing; The drawing review is the most important part of the process flow of the parts.
1. Check whether the drawings are complete.
2. The view relationship of the drawings, whether the labels are clear and complete, and the dimension units are marked.
3. Assembly relationship, assembly requirements focus size.
4. The difference between new and old drawings.
5. Translation of foreign languages.
6. Chart code conversion.
7. Drawing problems and feedback.
8. material
9. Quality requirements and process requirements
10. The official release drawings, shall be stamped with quality control chapter.
Expand Notes
Expanded drawing is a plan (2D) that expands in accordance with the parts drawing (3D)
1. Expand the convenient way to save material and workability
2. Reasonably select gaps and margins, T=2.0 or less gap 0.2, T=2-3 gap 0.5, edge wrapping using short edge (doorboard)
3. Reasonably consider the tolerance dimensions: Negative difference to go in the end, positive difference to go half; Hole size: positive difference goes to the end, negative difference takes half.
4. Burr direction
5. Extrude, pressure riveting, punching points (bags), and other position directions, draw a sectional view
6. Check material, plate thickness, thickness tolerance
7. Special angle, inner radius of bending angle (usually R=0.5)
8. Where error-prone (similar asymmetry) should focus on the prompt
9. Place to add more size enlarged view
10. Need to spray protection place to be logo
Sheet metal processing process
According to the difference in the structure of the sheet metal parts, the process flow may be different, but the total does not exceed the following points.
1, blanking:blanking way there are various, mainly in the following ways
1> Shears: Shears are used to cut strips of simple materials. It is mainly used for blank blank forming and processing. The cost is low and the precision is less than 0.2. However, only blanks or blocks with no holes or corners can be processed.
2> Punch: It is the use of punch to divide the flat parts of the parts after being unfolded on the plate to form all kinds of shapes. The advantages are short working hours, high efficiency, high precision, low cost, and suitable for mass production. Need to design the mold.
3> NC blanking, NC blanking first to write the NC program, using programming software, The drawing developed is written as a recognizable program by the NC number drawing machine. According to these programs, it can be used to punch flat components of various shapes on the flat plate one by one, but its structure is affected by the structure of the cutter. The cost is low and the precision is 0.15.
4. Laser blanking: It uses a laser cutting method to cut the shape of its flat plate on a large flat plate. You need to write a laser program like NCblanking. It can be a variety of complex shapes of flat parts, high cost, accuracy of 0.1.
5> Saw: Mainly used under the aluminum, square tube, tube, round bar and the like, low cost, low precision.
2. Fitter: Counterbore, Tapping, Reaming, Drilling
The Sinking angle is generally 120°C for riveting, 90°C for countersunk screws, and tapping for inch bottom holes.
3. Flanging: Also called drawing hole, hole flanging, is to draw a larger hole in a smaller base hole, and then tapping. Mainly use sheet metal with relatively thin plate thickness to increase its strength and number of thread turns to avoid slipping. Generally used for relatively thin plate thickness, its normal shallow hole flanging, the thickness does not change, Thickness of 30-40% is allowed to obtain height 40-60% higher than normal flange height. With a 50% squeeze, the maximum flange height can be obtained. When the plate thickness is large, such as 2.0, 2.5, etc., the plate thickness can be directly tapped.
4. punch: Is the use of mold forming process, the general punch processing punching, cutting angle, blanking, punch bumps (bumps), punch tear, draw holes, forming and other processing methods. The processing needs to have a corresponding mold to complete the operation, such as punching blanking die, convex bag die, tearing die, suction hole die, forming die, etc. The operation mainly pays attention to position and direction.
5. Pressure riveting: There are pressure riveting nuts, screws, loose, etc., through the hydraulic pressure riveting machine or punch to complete the operation, riveting it to the sheet metal parts, pay attention to directionality.
6. Bend: Bending is folding a 2D panel into a 3D part.Its processing requires a folding bed and a corresponding bending die, and it also has a certain bending sequence. The principle is the first fold that does not interfere with the next knife.
The number of bends is calculated by calculating the groove width at 6 times the thickness of T = 3.0mm or less. Such as: T = 1.0, V = 6 .0 F = 1.8, T = 1.2, V = 8, F = 2.2, T = 1.5, V = 10, F = 2.7, T = 2.0, V = 12, F = 4.0
Folding bed mold classification, straight knife, machete (80°C, 30°C)
When the aluminum plate is bent, there is a crack, which can increase the width of the lower mold groove to increase the upper mold R (annealing can avoid cracks)
Note when bending: I plan surface, require plate thickness, quantity; II bending direction
Bend angle; IV bending size; VI appearance, electroplated chrome parts must not be creased.
The relationship between bending and riveting process: Under normal circumstances riveting first, then bending, However, if the material is pressed after riveting, it must be folded and then pressed. In some cases, bending, riveting and re-bending are required.
6. Welding: Also referred to as splicing, is a manufacturing process and technique for joining metals or other thermoplastic materials, such as plastics, by heating, high temperature, or high pressure.
1>Classification: a fusion welding: argon arc welding, CO2 welding, gas welding, manual welding
b. Pressure welding: spot welding, butt welding, bump welding
c. Brazing: electrochromic welding, copper wire
2> welding methods: a CO2 gas shielded welding
b. Argon arc welding
c. Spot welding
d. Robot welding
The choice of welding method is based on actual requirements and materials, in general, CO2 gas shielded welding is used for iron plate welding boring; Argon arc welding for stainless steel, aluminum welding. Robot welding saves man hours, improves work efficiency and welding quality, and reduces work intensity.
3> Welding symbols: Δ fillet weld, Д, I weld, V weld, unilateral V weld (V) with blunt V weld (V), spot weld (O), plug weld or slot weld (∏) , Crimping (χ), Single-sided V-type welding with blunt edges (V), U-shaped welding with blunt, J-shaped welding with blunt, back-end welding, Fracturing
4> Arrow Lines and Connectors
5> Missing welds and their prevention
Spot welding: Insufficient strength can hit bumps, impose welding area
CO2 welding: high productivity, low energy consumption, low cost, strong rust resistance
Argon arc welding: shallow depth of dissolution, slow welding speed, low efficiency, high production cost, tungsten clip defects, but with good welding quality, can be welded non-ferrous metals, such as aluminum, copper, magnesium and so on.
6> welding deformation causes: insufficient preparation before welding, need to increase the fixture
Welding fixture bad improvement process
Bad welding sequence
7> Welding Deformation Effect Positive Method: Flame Effect Method
Vibration method
Hammering
Artificial aging
Selection of materials
The commonly used materials for sheet metal are cold-rolled sheet (SPCC), hot-rolled sheet (SHCC), galvanized sheet (SECC, SGCC), copper (CU) brass, beryllium copper, aluminum sheet (6061, 6063, Hard aluminum, etc.), aluminum profiles, stainless steel (mirror, brushed surface, matt surface), depending on the role of the product, the choice of materials is different, generally need to consider the use of the product and the cost.
1. Cold-rolled plate SPCC: mainly used for electroplating and baking paint parts, low cost, easy molding, material thickness ≤ 3.2mm.
2. Hot-rolled plate SHCC: material T ≥ 3.0mm, also used for electroplating, paint parts, low cost, but difficult to shape, mainly used flat pieces.
3. Galvanized sheet SECC, SGCC: SECC Electrolytic plate divided N material, P material, N material is not mainly for surface treatment, high cost, P material for spraying parts.
4. Copper: The main use of conductive materials, the surface treatment is nickel, chrome, or no treatment, high cost.
5. Aluminum plate: generally used for surface chromate (J11-A), oxidation (conductive oxidation, chemical oxidation), high cost, silver plating, nickel plating.
6. Aluminium profile: The material with complex cross-section structure is widely used in a variety of subracks. Surface treatment with aluminum plate.
7. Stainless steel: Mainly used without any surface treatment, high cost.
Drawing review
To write the part's technological process, we must first know the various technical requirements of the parts drawing; The drawing review is the most important part of the process flow of the parts.
1. Check whether the drawings are complete.
2. The view relationship of the drawings, whether the labels are clear and complete, and the dimension units are marked.
3. Assembly relationship, assembly requirements focus size.
4. The difference between new and old drawings.
5. Translation of foreign languages.
6. Chart code conversion.
7. Drawing problems and feedback.
8. material
9. Quality requirements and process requirements
10. The official release drawings, shall be stamped with quality control chapter.
Expand Notes
Expanded drawing is a plan (2D) that expands in accordance with the parts drawing (3D)
1. Expand the convenient way to save material and workability
2. Reasonably select gaps and margins, T=2.0 or less gap 0.2, T=2-3 gap 0.5, edge wrapping using short edge (doorboard)
3. Reasonably consider the tolerance dimensions: Negative difference to go in the end, positive difference to go half; Hole size: positive difference goes to the end, negative difference takes half.
4. Burr direction
5. Extrude, pressure riveting, punching points (bags), and other position directions, draw a sectional view
6. Check material, plate thickness, thickness tolerance
7. Special angle, inner radius of bending angle (usually R=0.5)
8. Where error-prone (similar asymmetry) should focus on the prompt
9. Place to add more size enlarged view
10. Need to spray protection place to be logo
Sheet metal processing process
According to the difference in the structure of the sheet metal parts, the process flow may be different, but the total does not exceed the following points.
1, blanking:blanking way there are various, mainly in the following ways
1> Shears: Shears are used to cut strips of simple materials. It is mainly used for blank blank forming and processing. The cost is low and the precision is less than 0.2. However, only blanks or blocks with no holes or corners can be processed.
2> Punch: It is the use of punch to divide the flat parts of the parts after being unfolded on the plate to form all kinds of shapes. The advantages are short working hours, high efficiency, high precision, low cost, and suitable for mass production. Need to design the mold.
3> NC blanking, NC blanking first to write the NC program, using programming software, The drawing developed is written as a recognizable program by the NC number drawing machine. According to these programs, it can be used to punch flat components of various shapes on the flat plate one by one, but its structure is affected by the structure of the cutter. The cost is low and the precision is 0.15.
4. Laser blanking: It uses a laser cutting method to cut the shape of its flat plate on a large flat plate. You need to write a laser program like NCblanking. It can be a variety of complex shapes of flat parts, high cost, accuracy of 0.1.
5> Saw: Mainly used under the aluminum, square tube, tube, round bar and the like, low cost, low precision.
2. Fitter: Counterbore, Tapping, Reaming, Drilling
The Sinking angle is generally 120°C for riveting, 90°C for countersunk screws, and tapping for inch bottom holes.
3. Flanging: Also called drawing hole, hole flanging, is to draw a larger hole in a smaller base hole, and then tapping. Mainly use sheet metal with relatively thin plate thickness to increase its strength and number of thread turns to avoid slipping. Generally used for relatively thin plate thickness, its normal shallow hole flanging, the thickness does not change, Thickness of 30-40% is allowed to obtain height 40-60% higher than normal flange height. With a 50% squeeze, the maximum flange height can be obtained. When the plate thickness is large, such as 2.0, 2.5, etc., the plate thickness can be directly tapped.
4. punch: Is the use of mold forming process, the general punch processing punching, cutting angle, blanking, punch bumps (bumps), punch tear, draw holes, forming and other processing methods. The processing needs to have a corresponding mold to complete the operation, such as punching blanking die, convex bag die, tearing die, suction hole die, forming die, etc. The operation mainly pays attention to position and direction.
5. Pressure riveting: There are pressure riveting nuts, screws, loose, etc., through the hydraulic pressure riveting machine or punch to complete the operation, riveting it to the sheet metal parts, pay attention to directionality.
6. Bend: Bending is folding a 2D panel into a 3D part.Its processing requires a folding bed and a corresponding bending die, and it also has a certain bending sequence. The principle is the first fold that does not interfere with the next knife.
The number of bends is calculated by calculating the groove width at 6 times the thickness of T = 3.0mm or less. Such as: T = 1.0, V = 6 .0 F = 1.8, T = 1.2, V = 8, F = 2.2, T = 1.5, V = 10, F = 2.7, T = 2.0, V = 12, F = 4.0
Folding bed mold classification, straight knife, machete (80°C, 30°C)
When the aluminum plate is bent, there is a crack, which can increase the width of the lower mold groove to increase the upper mold R (annealing can avoid cracks)
Note when bending: I plan surface, require plate thickness, quantity; II bending direction
Bend angle; IV bending size; VI appearance, electroplated chrome parts must not be creased.
The relationship between bending and riveting process: Under normal circumstances riveting first, then bending, However, if the material is pressed after riveting, it must be folded and then pressed. In some cases, bending, riveting and re-bending are required.
6. Welding: Also referred to as splicing, is a manufacturing process and technique for joining metals or other thermoplastic materials, such as plastics, by heating, high temperature, or high pressure.
1>Classification: a fusion welding: argon arc welding, CO2 welding, gas welding, manual welding
b. Pressure welding: spot welding, butt welding, bump welding
c. Brazing: electrochromic welding, copper wire
2> welding methods: a CO2 gas shielded welding
b. Argon arc welding
c. Spot welding
d. Robot welding
The choice of welding method is based on actual requirements and materials, in general, CO2 gas shielded welding is used for iron plate welding boring; Argon arc welding for stainless steel, aluminum welding. Robot welding saves man hours, improves work efficiency and welding quality, and reduces work intensity.
3> Welding symbols: Δ fillet weld, Д, I weld, V weld, unilateral V weld (V) with blunt V weld (V), spot weld (O), plug weld or slot weld (∏) , Crimping (χ), Single-sided V-type welding with blunt edges (V), U-shaped welding with blunt, J-shaped welding with blunt, back-end welding, Fracturing
4> Arrow Lines and Connectors
5> Missing welds and their prevention
Spot welding: Insufficient strength can hit bumps, impose welding area
CO2 welding: high productivity, low energy consumption, low cost, strong rust resistance
Argon arc welding: shallow depth of dissolution, slow welding speed, low efficiency, high production cost, tungsten clip defects, but with good welding quality, can be welded non-ferrous metals, such as aluminum, copper, magnesium and so on.
6> welding deformation causes: insufficient preparation before welding, need to increase the fixture
Welding fixture bad improvement process
Bad welding sequence
7> Welding Deformation Effect Positive Method: Flame Effect Method
Vibration method
Hammering
Artificial aging
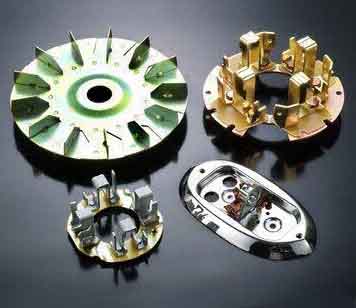