Reaming of aluminum alloy engine cylinder head tappet
Due to the complicated structure of the engine and the high technical content, the manufacture of its components has always been the focus of attention.
When the tappet hole of cylinder head is reamed, the short service life of the cutter has been bothering the technicians in the production line. The structure of tappet hole of cylinder head is shown in Figure 2. After close cooperation with a domestic automobile company, UNIMERCO has successfully developed a new type of fine reamer for processing the light alloy engine cylinder head tappet hole (as shown in Figure 3). Effectively solved the above problems.
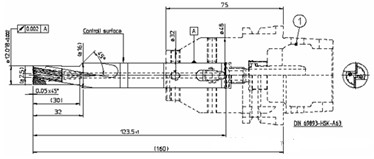
Figure 3 Schematic diagram of the new fine reaming knife
UNIMERCO's reamer has a spiral structure with 2 cutting edges and 6 guide strips.
Practice has proved that this product not only solves the problem of burr, but also its common cutting parameters are greatly improved compared with other PCD tools:
The roughing allowance is 0.35mm on one side;
Finishing speed n=10000r/min;
Feed rate Fn=3200mm/min;
The retraction feed rate is 6000 mm/min. The life before grinding can reach 150,000 holes, almost achieving burr-free and mirror effect.
Compared with the cutting parameters of the original tool used by the automobile company, Fn=1800mm/min, Fz=0.045, and the life is about 70,000 holes, and the efficiency has been significantly improved.
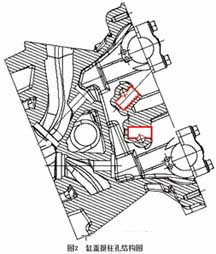
When the tappet hole of cylinder head is reamed, the short service life of the cutter has been bothering the technicians in the production line. The structure of tappet hole of cylinder head is shown in Figure 2. After close cooperation with a domestic automobile company, UNIMERCO has successfully developed a new type of fine reamer for processing the light alloy engine cylinder head tappet hole (as shown in Figure 3). Effectively solved the above problems.
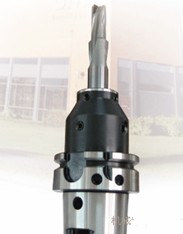
Figure 1 Spiral groove PCD reamer
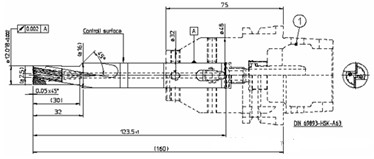
Figure 3 Schematic diagram of the new fine reaming knife
UNIMERCO's reamer has a spiral structure with 2 cutting edges and 6 guide strips.
Practice has proved that this product not only solves the problem of burr, but also its common cutting parameters are greatly improved compared with other PCD tools:
The roughing allowance is 0.35mm on one side;
Finishing speed n=10000r/min;
Feed rate Fn=3200mm/min;
The retraction feed rate is 6000 mm/min. The life before grinding can reach 150,000 holes, almost achieving burr-free and mirror effect.
Compared with the cutting parameters of the original tool used by the automobile company, Fn=1800mm/min, Fz=0.045, and the life is about 70,000 holes, and the efficiency has been significantly improved.