Milling of the free surface of the forming electrode
Strategies for high-speed roughing and finishing of graphite electrodes are different. Generally rough machining should leave less allowance for finishing, so when using small diameter tools, high feeds (cutting and feed) should be used. On the premise of minimizing tool wear, a high unit cutting volume and a single cutting edge effective cutting amount are obtained, and the residual cutting amount must meet the requirements of finishing: The goal of finishing is to obtain the highest machining quality with the shortest machining time. The ratio of the best surface quality to the minimum tool wear should be optimized.When processing, the processing speed should be increased and the processing time should be shortened to minimize the instability of the processing process caused by the change in the cutting amount and maximize the tool life.
The high-speed machining strategy of free-surface forming electrodes is mainly to optimize the cutting machining path considering the local machining allowance.
I. Milling roughing
Graphite electrodes are usually performed on a single piece of material. The machining allowance is easy to describe. The goal is to remove the largest amount of material in the shortest time. Roughing can be profiled or contoured (Figure 11). Copy milling uses ball-end milling cutters. Both cutting depth and cutting width are changing. Small cutting depth, fast tool wear and long processing time: Contour milling adopts a flat-bottom milling cutter, with short processing time and low tool wear. In contour milling, milling can be performed along the envelope trajectory. That is, the machining surface is fed in a zigzag and then processed, the cutting width is fixed, there is not much reciprocation, and a large feed can be achieved by rapid acceleration. The processing along the contour trajectory uses traditional processing methods to sequentially process local contour surfaces. The quality of the roughing process depends on the NC programming according to the contour function of the tool surface, which enables fast and easy milling along the contour of the envelope.
Work material: EK85
Stone size: 13mm:
Tool: Ball-end milling cutter, D = 10mm, Z = 2
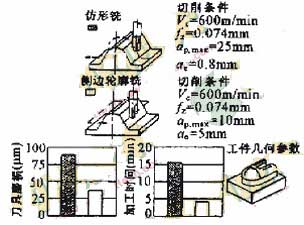
Figure 11 Comparison of (Copy milling) and contour milling
II. Milling finishing
Finishing should make the process stable, with small shape errors and good surface quality, and at the same time, the amount of tool wear is small. Tool wear and machining costs are major considerations. In the finishing, the influence of the milling direction on the machining accuracy and surface quality should be considered for the processing of the bending angle, which is related to the tool load and machine vibration. When milling along a curved surface, broaching (upward cutting) or drilling (downward cutting) will occur. Deformation of the tool will cause deviation of the workpiece contour (Figure 12). The contour deviation of drilling and milling is smaller than that of broaching, and the contour deviation of counterclockwise milling is better than clockwise milling. Therefore, considering the critical conditions of tool quality and the stability and reliability of the machining process, the best strategy for milling along a plane contour is to use a combination of counterclockwise milling and plane contour milling. In addition, in clockwise milling, the cutting tool life of envelope contour milling is longer than that of drilling and milling, and they are similar in counterclockwise milling.
Work material: EK85
Grain size: 13mm
Graphite particle size: D = 6mm, Ik = 50mm
Tool material: Carbide K10
Cutting conditions: Vc = 600m / min, fz = 0.044mm, Rth = 10? M
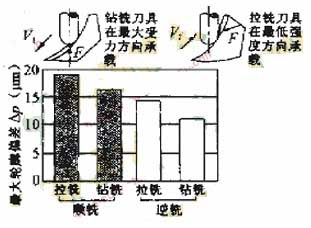
figure 2 Broaching and drilling-milling finishing strategies
The high-speed machining strategy of free-surface forming electrodes is mainly to optimize the cutting machining path considering the local machining allowance.
I. Milling roughing
Graphite electrodes are usually performed on a single piece of material. The machining allowance is easy to describe. The goal is to remove the largest amount of material in the shortest time. Roughing can be profiled or contoured (Figure 11). Copy milling uses ball-end milling cutters. Both cutting depth and cutting width are changing. Small cutting depth, fast tool wear and long processing time: Contour milling adopts a flat-bottom milling cutter, with short processing time and low tool wear. In contour milling, milling can be performed along the envelope trajectory. That is, the machining surface is fed in a zigzag and then processed, the cutting width is fixed, there is not much reciprocation, and a large feed can be achieved by rapid acceleration. The processing along the contour trajectory uses traditional processing methods to sequentially process local contour surfaces. The quality of the roughing process depends on the NC programming according to the contour function of the tool surface, which enables fast and easy milling along the contour of the envelope.
Work material: EK85
Stone size: 13mm:
Tool: Ball-end milling cutter, D = 10mm, Z = 2
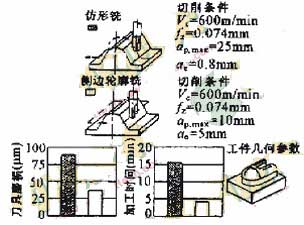
Figure 11 Comparison of (Copy milling) and contour milling
II. Milling finishing
Finishing should make the process stable, with small shape errors and good surface quality, and at the same time, the amount of tool wear is small. Tool wear and machining costs are major considerations. In the finishing, the influence of the milling direction on the machining accuracy and surface quality should be considered for the processing of the bending angle, which is related to the tool load and machine vibration. When milling along a curved surface, broaching (upward cutting) or drilling (downward cutting) will occur. Deformation of the tool will cause deviation of the workpiece contour (Figure 12). The contour deviation of drilling and milling is smaller than that of broaching, and the contour deviation of counterclockwise milling is better than clockwise milling. Therefore, considering the critical conditions of tool quality and the stability and reliability of the machining process, the best strategy for milling along a plane contour is to use a combination of counterclockwise milling and plane contour milling. In addition, in clockwise milling, the cutting tool life of envelope contour milling is longer than that of drilling and milling, and they are similar in counterclockwise milling.
Work material: EK85
Grain size: 13mm
Graphite particle size: D = 6mm, Ik = 50mm
Tool material: Carbide K10
Cutting conditions: Vc = 600m / min, fz = 0.044mm, Rth = 10? M
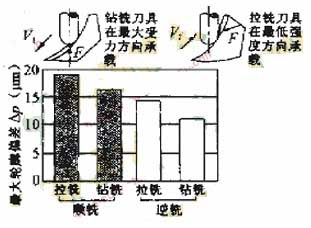
figure 2 Broaching and drilling-milling finishing strategies