Long-axis parts - a new process total solution for "Hao" machining
For the work of turning long shafts, the technical content is relatively high and difficult, especially for the turning of the slender shaft. In the clamping method, if a more common method is used, the processing difficulty is increased, and during the processing, the workpiece is easily deformed and sometimes cannot be completed. Long-axis parts are generally required to be high in dimensional accuracy, shape accuracy (cylindricity) or surface roughness. In order to reach these precision requirements, the traditional processing is used, the production capacity is not high, the process is complicated, and the equipment cost is high. There is now a new process called "Hao", Hawker's mirror processing equipment, which replaces the grinding with turning, and it is easy to realize long-axis mirrors in one setup.
After a Hokkonen process, the mirror long-axis workpiece can be machined (surface roughness Ra value <0.2μm); The surface hardness of the workpiece is increased by more than 20%; It solves the problem that it is difficult to ensure the accuracy of long-axis parts processing (using elastic tailstock, tool holder, zero force mechanism, etc.); The wear resistance and corrosion resistance of the workpiece are increased by more than 50%; The surface of the workpiece is strengthened, and its fatigue life can be extended by several times; Extend the service life of the sealing ring with which it is matched; High efficiency, environmental protection, energy saving and high quality.
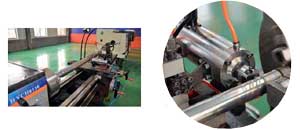
Hokkonen Process Total Solution 1
Rough turning -> fine turning -> Hokkonen processingThe roughing and finishing of the car is completed by a lathe, and the Hokkonen machine is only finished "Hao". This solution can be used for optical axis workpieces with high accuracy requirements but very high roughness requirements (also short stepped workpieces). Customers have upgraded the traditional machining process of lathes.
Hokkonen Process Total Solution 2
Rough turning -> Rough grinding -> Hokkonen processing
After the rough turning process is completed by the lathe, the conversion grinding machine completes the rough grinding, and the Hokkonen machine tool completes the "Hao". This solution can be used for workpieces with very high precision and roughness requirements (or short workpieces with stepped shafts). In the existing lathe, grinding machine traditional processing technology upgrade.
Hokkonen Process Total Solution 3
Rough turning -> Fine turning -> Hokkonen processing
All processing is done in one setup by a composite Hokkonen lathe. This solution is suitable for the machining of optical axis workpieces (which can also be machined with short stepped shaft workpieces) with high precision requirements but very high roughness requirements.
Hokkonen Process Total Solution 4
Rough turning -> fine turning -> rough grinding -> Hokkonen processing
It is machined by a Hokkonen compound car, which is fully loaded in one setup. This solution is suitable for the machining of optical axis workpieces with very high precision and roughness requirements (it can also be used to machine short stepped shaft workpieces).
Hokkonen Process Total Solution 5
Rough turning -> fine turning -> Hokkonen processing
All the shaft machining is completed in one clamping by a composite Hokkonen lathe device. However, this machine has an additional shaft that is dedicated to controlling the Hokkonen tool and completes the machining of the elongated and stepped shaft workpiece in one setup.