How to Calculate Machining Parts Cost?
Machining part processing costs, The cost of machining costs is mainly composed of material costs and processing costs. The material cost is determined by the size of the part blank and the type of material, and the processing cost is determined by the equipment cost and labor cost.
The material cost is basically fixed, and the main difference in processing cost is in the processing company's different labor costs, transportation costs, consumption costs, and taxes. This is mainly talking about this one processing costs.
How to cost the machining price?
Detailed calculation method:
1. First of all, you can ask suppliers to provide preliminary process arrangements for key or complex parts, detailed to each process, the time-consuming of each process
2. The processing cost can be calculated according to the hourly cost of the equipment required for each process.
Specific equipment costs you can also ask suppliers to, for example,
Ordinary CNC machining is between ¥60~80 per hour (including tax) Milling machines, general vehicles and other general equipment are generally ¥30. . .
3, in accordance with the proportion of packaging and transportation, management costs, tooling, profit is the price, Of course, the price will have a lot to do with the annual purchase volume and the degree of difficulty of the part. There is a lot of price difference between single item and batch, which is also very easy to understand.
Machining Parts Processing Costs A rough calculation method:
1) Large in volume, Big weight
Difficulty general:
The ratio of processing costs to the raw material cost of the entire part is 1:1, which is inversely proportional to the purchase volume;
Difficult:
The ratio of processing costs to the raw material costs of the entire part is 1.2 to 1.5:1, which is inversely proportional to the purchase volume;
2) For small and medium pieces
Difficulty general:
The ratio of processing costs to the raw material cost of the entire part is approximately 2 to 3:1, which is inversely proportional to the purchase volume;
Difficult:
The ratio of processing costs to the raw material cost of the entire part is approximately 5 to 10:1, which is inversely proportional to the purchase volume;
Since there is a lot of process flexibility in machining, that is, a part can have a variety of process arrangements, the cost is certainly not the same.
But when the supplier sometimes calculates the cost, it will give you a complicated process to increase the price, but actually the production will use other simple processes.
Therefore, the buyer's own understanding of the drawings and the knowledge of the parts processing, determine the accuracy of your estimated cost, so the procurement of mechanical parts requires a more comprehensive knowledge of machining.
If you want to machine a workpiece, the first is the material cost of the other party; Then some travel expenses for the purchase of the workpiece;
The main thing is your workpiece to be machined required processing time, General turning workmanship ¥10-30/hour, fitter probably ¥10-25/hour;
If there are no existing tools (such as tools, molds), the cost of the product also requires you to bear part or all of the tool fee; Finally, add up to the cost of processing you have to pay!
Material fees, machine depreciation, labor costs, management fees, taxes, etc. are basically required. Or the material fees, processing fees and taxes, as well as business costs, transportation costs, and budgeting require a thorough understanding of the market.
Process problems should include material fees, processing fees (which process prices are different), equipment depreciation expenses, workers' wages, management fees, taxes, etc.
It is mainly to determine the process first, namely the processing method, then calculate the working hours according to the craft, and determine the basic processing cost of the individual parts from the working hours, plus other expenses.
Process is a very complicated knowledge, a part using different processes, the price difference, In fact, the working hours of various types of work are not fixed, and will vary according to the difficulty of the workpiece, the size and performance of the equipment. Of course, the key is to see how much your volume, but in general it has a basic price, floating between the basic price.
1. Basic price of turning:¥ 20-40
Specific according to the actual situation, like small pieces, very simple processing, working hours is less than ¥ 20;
Sometimes even only ¥10, such as some large pulleys, the processing allowance is large, the boss only earns the money of cast iron powder is enough;
Sometimes if the workpiece is large, no one on the market generally can process it, and you can raise the price by two or three times. There is no way for others.
2. The basic price of grinding: ¥25-45
3. Milling basic price: ¥25-45
4 drilling basic price:¥ 15-35
5. PlanerBasic price:¥15-35
6. Wire cut base price: ¥30-40/sqm
7. Basic price of electric spark: ¥10-40, single piece generally press 50/piece (less than 1 hour)
8.NC basic price: 2-4 times more expensive than normal
9. Engraving: Generally single piece. ¥50-500/piece,
Of course, still a word. The specific product specific price, The above price is only for reference. If you have any experience, I hope you can speak it out and everyone can communicate together.
Due to different regions, different time, different manufacturers, different requirements, different suppliers, different quantities, there are many different, the price is also very different, there is no certain standard.
However, according to the billing of processing time, one reference is given as follows (where the figures are for reference only, and the difference between regions and time is really great):
This data does not include electricity processing yet. such as wire cutting, generally based on the processing area to billing. "Regarding Charges for General Mechanical Parts"
One. By working hour rate method:
Z25 Drilling Machine, CA6140 Lathe, Planer, Inserting Machine, Sawing Machine With a charge of ¥15/h.
Vertical, horizontal milling, wire cutting, large lathes, gantry milling with ¥20/h.
General fitter maintenance costs ¥15/h.
The chronograph unit starts from the beginning of processing to the end of processing acceptance.
Second, the machining price is based on parts, quantity, accuracy requirements charging methods:
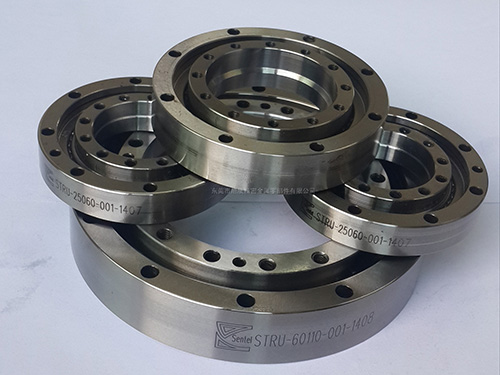
The material cost is basically fixed, and the main difference in processing cost is in the processing company's different labor costs, transportation costs, consumption costs, and taxes. This is mainly talking about this one processing costs.
How to cost the machining price?
Detailed calculation method:
1. First of all, you can ask suppliers to provide preliminary process arrangements for key or complex parts, detailed to each process, the time-consuming of each process
2. The processing cost can be calculated according to the hourly cost of the equipment required for each process.
Specific equipment costs you can also ask suppliers to, for example,
Ordinary CNC machining is between ¥60~80 per hour (including tax) Milling machines, general vehicles and other general equipment are generally ¥30. . .
3, in accordance with the proportion of packaging and transportation, management costs, tooling, profit is the price, Of course, the price will have a lot to do with the annual purchase volume and the degree of difficulty of the part. There is a lot of price difference between single item and batch, which is also very easy to understand.
Machining Parts Processing Costs A rough calculation method:
1) Large in volume, Big weight
Difficulty general:
The ratio of processing costs to the raw material cost of the entire part is 1:1, which is inversely proportional to the purchase volume;
Difficult:
The ratio of processing costs to the raw material costs of the entire part is 1.2 to 1.5:1, which is inversely proportional to the purchase volume;
2) For small and medium pieces
Difficulty general:
The ratio of processing costs to the raw material cost of the entire part is approximately 2 to 3:1, which is inversely proportional to the purchase volume;
Difficult:
The ratio of processing costs to the raw material cost of the entire part is approximately 5 to 10:1, which is inversely proportional to the purchase volume;
Since there is a lot of process flexibility in machining, that is, a part can have a variety of process arrangements, the cost is certainly not the same.
But when the supplier sometimes calculates the cost, it will give you a complicated process to increase the price, but actually the production will use other simple processes.
Therefore, the buyer's own understanding of the drawings and the knowledge of the parts processing, determine the accuracy of your estimated cost, so the procurement of mechanical parts requires a more comprehensive knowledge of machining.
If you want to machine a workpiece, the first is the material cost of the other party; Then some travel expenses for the purchase of the workpiece;
The main thing is your workpiece to be machined required processing time, General turning workmanship ¥10-30/hour, fitter probably ¥10-25/hour;
If there are no existing tools (such as tools, molds), the cost of the product also requires you to bear part or all of the tool fee; Finally, add up to the cost of processing you have to pay!
Material fees, machine depreciation, labor costs, management fees, taxes, etc. are basically required. Or the material fees, processing fees and taxes, as well as business costs, transportation costs, and budgeting require a thorough understanding of the market.
Process problems should include material fees, processing fees (which process prices are different), equipment depreciation expenses, workers' wages, management fees, taxes, etc.
It is mainly to determine the process first, namely the processing method, then calculate the working hours according to the craft, and determine the basic processing cost of the individual parts from the working hours, plus other expenses.
Process is a very complicated knowledge, a part using different processes, the price difference, In fact, the working hours of various types of work are not fixed, and will vary according to the difficulty of the workpiece, the size and performance of the equipment. Of course, the key is to see how much your volume, but in general it has a basic price, floating between the basic price.
1. Basic price of turning:¥ 20-40
Specific according to the actual situation, like small pieces, very simple processing, working hours is less than ¥ 20;
Sometimes even only ¥10, such as some large pulleys, the processing allowance is large, the boss only earns the money of cast iron powder is enough;
Sometimes if the workpiece is large, no one on the market generally can process it, and you can raise the price by two or three times. There is no way for others.
2. The basic price of grinding: ¥25-45
3. Milling basic price: ¥25-45
4 drilling basic price:¥ 15-35
5. PlanerBasic price:¥15-35
6. Wire cut base price: ¥30-40/sqm
7. Basic price of electric spark: ¥10-40, single piece generally press 50/piece (less than 1 hour)
8.NC basic price: 2-4 times more expensive than normal
9. Engraving: Generally single piece. ¥50-500/piece,
Of course, still a word. The specific product specific price, The above price is only for reference. If you have any experience, I hope you can speak it out and everyone can communicate together.
No. | Device name | Model number | Processing range |
Processing costs
(¥/h)
|
1 | lathe | C616 | Φ320×750~1000 | 11 |
2 | lathe | C6140 | Φ400×1000~2000 | 13 |
3 | lathe | J1-MAZAK | Φ460×1000~2000 | 15 |
4 | lathe | C6150 | Φ460×1000~2000 | 15 |
5 | lathe | C630 | Φ630×1000~2000 | 21 |
6 | lathe | C650 | Φ800×1500~5000 | 30 |
7 | Vertical lathe | C5116A | Φ1600 | 28 |
8 | Radial Drilling Machine | Z3050 | Φ50~Φ63 | 16 |
9 | Radial Drilling Machine | Z3080 | Φ80 | 20 |
10 | Vertical drilling machine | Z5140A | Φ32~Φ40 | 12 |
11 | Horizontal boring machine | T68 | 1000×1000 | 26 |
12 | Horizontal boring machine | T611 | 1000×1000 | 30 |
13 | Vertical boring machine | T4163 | 630×1100 | 56 |
14 | Horizontal boring machine | T6111A | 1200×1200 | 36 |
15 | universal circular grinding machine | M1420 | Φ125~220×350~1000 | 15 |
16 | universal circular grinding machine | M1432A | M9025×500~1000 | 19 |
17 | universal circular grinding machine | M1432B | Φ315~320×1500~3000 | 26 |
18 | universal circular grinding machine | M1331A | Φ315~320×1500~3000 | 26 |
19 | universal circular grinding machine | M1450 | Φ500×1500~2000 | 28 |
20 | Precision universal circular grinding machine | MG1432 | Φ320×1000~2000 | 32 |
21 | internal grinding machine | MG1432 | Φ12~Φ100×130 | 13 |
22 | Surface Grinder | M7120 | 200×630~650 | 16 |
23 | Surface Grinder | M7130 | 300×1000 | 21 |
24 | Surface Grinder | M7150 | 500×2000 | 40 |
25 | guideway grinder | M50100 | 1000×6000 | 28 |
26 | Spline grinding machine | M8612A | Φ120×1800 | 28 |
27 | Thread grinding machine | Y7520W | Φ200×500 | 20 |
28 | Gear grinding machine | Y4632A | Φ320×6M | 30 |
29 | Universal Tool Grinding Machine | M5MC | Φ200×500 | 13 |
30 | Universal Tool Grinding Machine | MW6020 | Φ200×500 | 13 |
31 | Universal Tool Grinding Machine | M9025 | Φ200×650 | 16 |
32 | Universal Tool Grinding Machine | M6025H | Φ250×650 | 16 |
33 | Universal Tool Grinding Machine | M6425 | Φ250×650 | 16 |
34 | Broach grinder | M6110D | Φ100×1500~1700 | 16 |
35 | Gear hobbing machine | YM3150E | Φ500×8M | 22 |
36 | Rod rack | YM5150B | Φ500×8M | 18 |
37 | Vertical milling machine | X5030A | Φ300×1120 | 16 |
38 | Vertical milling machine | X52K | Φ320×1250 | 18 |
39 | Vertical milling machine | XA5032 | Φ320×1250 | 18 |
40 | Horizontal milling machine | X63W | Φ400×1600 | 24 |
41 | Sleeper milling machine | XS5646/1 | Φ425×2000 | 28 |
42 | Shaping machine | B665 | 650×800 | 14 |
43 | Shaping machine | B650 | 650×800 | 11 |
44 | Hydraulic planer | BY60100 | 900~1000 | 16 |
45 | Hydraulic planer | B690 | 900~1000 | 16 |
46 | frame planer | B2016A | 900~1000 | 28 |
47 | frame planer | B2020A | 2000~6000 | 50 |
48 | Rod bed | B5032 | 200~320 | 12 |
49 | Broaching machine | L6140 | 40T | 15 |
50 | Line fitter | Φ200×650 | 15 | |
51 | Assembly fitter | Φ200×650 | 30 | |
52 | Mold fitter | Φ200×650 | 30 | |
53 | Machining Center | Φ200×650 | 80 | |
54 | Wire cutting | Φ200×650 | 9 | |
55 | Welding knife | Φ200×650 | 7 |
However, according to the billing of processing time, one reference is given as follows (where the figures are for reference only, and the difference between regions and time is really great):
This data does not include electricity processing yet. such as wire cutting, generally based on the processing area to billing. "Regarding Charges for General Mechanical Parts"
One. By working hour rate method:
Z25 Drilling Machine, CA6140 Lathe, Planer, Inserting Machine, Sawing Machine With a charge of ¥15/h.
Vertical, horizontal milling, wire cutting, large lathes, gantry milling with ¥20/h.
General fitter maintenance costs ¥15/h.
The chronograph unit starts from the beginning of processing to the end of processing acceptance.
Second, the machining price is based on parts, quantity, accuracy requirements charging methods:
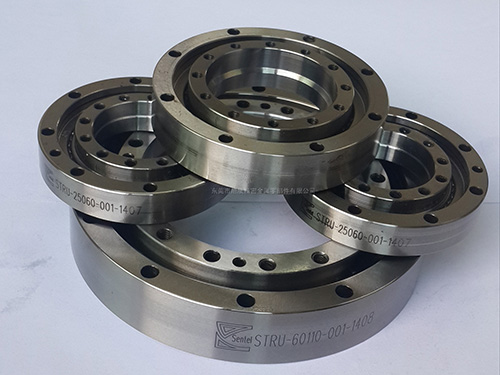