Grinding of large diameter thin-walled parts
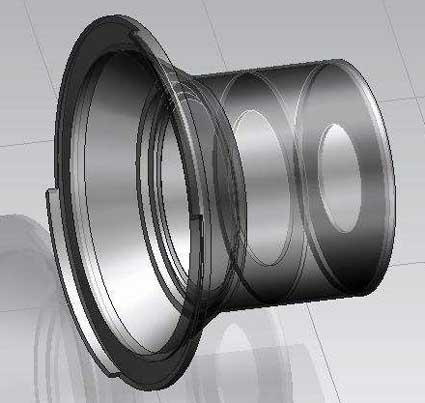
In the towed concrete pump truck, there is a typical large diameter thin walled part - the intermediate sleeve. The inner hole has a diameter of 202 mm, an outer diameter of 212 mm, and a wall thickness of only 5 mm. Moreover, the positional accuracy between the dimensions of the part is required to be high, the outer surface roughness Ra is required to be 0.4 μm, and the outer circularness error is required to be less than 0.010 mm. Due to the thin wall thickness of the part, when the outer circle is ground, if the measures are not taken, the workpiece will often be deformed greatly due to the clamping force, the grinding force, the grinding heat, the internal stress and the like. The quality of the part cannot be guaranteed. In order to reduce the deformation of the parts, we have developed a reasonable processing flow according to the structural characteristics of the parts. Special grinding fixtures have been designed and special clamping methods have been adopted to effectively guarantee the processing quality of such parts.
I. Deformation analysis of parts when grinding outer circle
According to the shape characteristics of the part, when the taper mandrel is used for clamping, the workpiece will be deformed by the radial component force generated by the action of the cone under the action of the clamping force. In addition, since the grinding heat of the inner wall of the workpiece is not easily lost during grinding, the grinding heat is also an important cause of deformation of the thin-walled part. Due to the deformation of the workpiece, the workpiece will form a saddle shape after grinding, and it is difficult to ensure the roundness and coaxiality error of the workpiece. The quality of the part must be ensured by designing special fixtures and using a reasonable process plan.
II. Fixture structure and principle of use
The clamp is a mandrel and a riser adjustable structure: It consists of a mandrel 1, a fixing pin 2, a left positioning plate 3, a tie rod 4, a support plate 5, a right positioning plate 6, a spring sleeve 7, a pressure plate 8, a shoulder nut 9 and a top bolt 10. The cooperation between the left and right positioning plates and the workpiece is H6/h5, and the cooperation between the right positioning plate 6 and the elastic sleeve 7 is E8/h7. The inner taper of the spring sleeve 7 is 20°. When the jig is used, the left positioning plate 3 is first fixed to the mandrel 1 by the fixing pin 2, and then the upper support plate 5 is attached to the other end of the mandrel. The fixture is loaded into the fixture with the inner hole of the part as the positioning reference, and the right positioning plate 6 is mounted on the mandrel and matched with the inner hole of the part. Insert two tie rods 4 (uniform position) on the clamp and lock them with nuts so that the clamp is fastened to the workpiece: Then, the spring sleeve 7 is inserted into the gap between the mandrel 1 and the right positioning plate 6, the pressure plate is installed, the shoulder nut 9 on the mandrel is tightened, the spring sleeve is pressed in, and the spring sleeve can be automatically centered. . With the axis of the mandrel aligned with the axis of the workpiece, the fixture is installed. After the parts are processed, loosen the shoulder nut 9 and screw the three top wire bolts 10 (the three top wire bolts 10 are evenly distributed and are offset from the two tie rods 4). The right positioning plate can drive the spring sleeve 7 to exit the workpiece in the opposite direction, and the clamp can be easily disassembled.
III. Grinding wheel selection
When selecting a grinding wheel, the characteristics of the grinding wheel such as abrasive, particle size, hardness, binder, graphite packing and grinding wheel structure have an effect on the grinding quality. If not properly selected, it is difficult to achieve the desired surface roughness of the workpiece. In addition, the cutting performance of the grinding wheel should be improved as much as possible, and the micro-blade and its contour of the grinding surface of the working surface of the grinding wheel should be controlled and kept in a sharp state. In view of the fact that the material of the part is 45 steel, in order to reduce the surface roughness of the part, the abrasive grain of the selected grinding wheel should have a moderate particle size and a slightly smaller hardness. This is because the abrasive wheel is too hard to pass off after it has been completely passivated, and the grinding is continued to increase the roughness. In practical applications, the grinding wheel is selected from microcrystalline corundum or single crystal corundum, the hardness is intermediate (K), and the particle size is 46 to 60. In addition, the grinding wheel must be trimmed before use, so that the surface of the grinding wheel has good grain cutting edge and micro-blade threshing and contouring, so as to ensure the surface roughness of the workpiece grinding.
IV. Grinding machine equipment selection
In order to reduce the shape and position errors of the part processing, the choice of equipment is very important. It is required that the machine tool spindle should have a high rotation precision, the radial runout is not more than 0.001 mm, the spindle stiffness is good, and there should be no vibration phenomenon in all parts of the machine tool. The Japanese Sun Machine CNC vertical grinding machine provided by KangDing has the advantages of high grinding precision, high processing efficiency, small floor space and high automation. In particular, there is an advantage that a horizontal grinding machine does not have a large workpiece. It is the best choice for grinding large diameter thin wall parts.