Cold extrusion processing of profiled workpieces
Definition of cold extrusion: extrusion at a temperature below the recovery temperature. For most non-ferrous metals such as aluminum, copper, titanium, and steel materials, it generally refers to extrusion at room temperature.
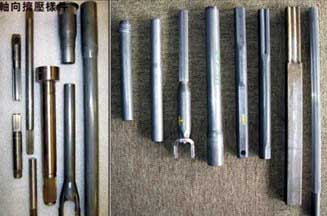
Cold extrusion is to place the metal blank in a cold extrusion cavity, and at room temperature, apply pressure to the blank through a fixed punch on the press to plastically deform the metal blank to produce a part processing method.
At present, China has been able to cold-extrude metals such as lead, tin, aluminum, copper, zinc and their alloys, low carbon steel, medium carbon steel, tool steel, low alloy steel and stainless steel. Even for bearing steel, high carbon high aluminum alloy tool steel, high speed steel, etc., it can also be cold extruded with a certain amount of deformation. In terms of extrusion equipment, China has the ability to design and manufacture tonnage extrusion presses at all levels. In addition to the use of general mechanical presses, hydraulic presses, and cold extrusion presses, it has also successfully used cold presses with friction presses and high-speed high-energy equipment.
KangDing provides the American RP series radial cold extrusion molding machine for cold extrusion of involute or rectangular spline and profiled parts. It is the preferred cold forming equipment for automotive parts.
1, the principle of the process
Kine-Flow warp cold extrusion forming process:
The plurality of molds radially arranged are pressed against a workpiece located at the center by a set of power actuators to be deformed. The mold is fed in the radial direction, and this action is performed by the axial hydraulic cylinder pushing the ring having the wedge face. Thereby the axial displacement and force are converted into radial displacement and force.
2, processing capacity
The amount of extrusion force depends on the number of teeth of the workpiece, the depth of the teeth, the shape of the flank and the length of the forming, in addition to the elongation of the material. As long as the tooth side after the forming of the workpiece does not hinder the extraction of the mold teeth, most of the tooth shapes can be extruded. The sides of the formed teeth may be straight, involute or other complicated spherical convex shape, and the formed flank and the root may not have sharp corners, and all the tooth surfaces are opposite.
3, the characteristics of the molding
Pitch and tooth tolerance are the main parameters after forming. If the blank is well controlled, it will produce extremely high precision stability. Unlike axial compression, which controls the outer diameter, the radially extruded tip has a flange. That is because the axial flow of the material during forming is unconstrained.
4, material requirements
In general, the hardness of the material is greater than HRC25, and the elongation is at least 15% to improve the mold life. In addition, the smaller the pressure angle, the larger the mold load, which will affect the mold life and the cumulative error of the pitch.
5, equipment construction
The device has both horizontal and vertical knots. The mold disassembly and replacement is modular, simple and fast. It can be loaded and unloaded manually or fully automated. The hydraulic system can be placed inside the fuselage or separately outside the fuselage.
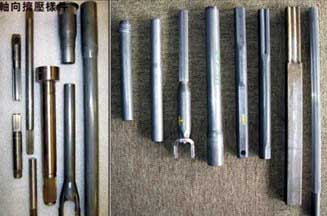
Cold extrusion is to place the metal blank in a cold extrusion cavity, and at room temperature, apply pressure to the blank through a fixed punch on the press to plastically deform the metal blank to produce a part processing method.
At present, China has been able to cold-extrude metals such as lead, tin, aluminum, copper, zinc and their alloys, low carbon steel, medium carbon steel, tool steel, low alloy steel and stainless steel. Even for bearing steel, high carbon high aluminum alloy tool steel, high speed steel, etc., it can also be cold extruded with a certain amount of deformation. In terms of extrusion equipment, China has the ability to design and manufacture tonnage extrusion presses at all levels. In addition to the use of general mechanical presses, hydraulic presses, and cold extrusion presses, it has also successfully used cold presses with friction presses and high-speed high-energy equipment.
KangDing provides the American RP series radial cold extrusion molding machine for cold extrusion of involute or rectangular spline and profiled parts. It is the preferred cold forming equipment for automotive parts.
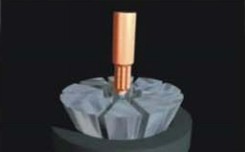
1, the principle of the process
Kine-Flow warp cold extrusion forming process:
The plurality of molds radially arranged are pressed against a workpiece located at the center by a set of power actuators to be deformed. The mold is fed in the radial direction, and this action is performed by the axial hydraulic cylinder pushing the ring having the wedge face. Thereby the axial displacement and force are converted into radial displacement and force.
2, processing capacity
The amount of extrusion force depends on the number of teeth of the workpiece, the depth of the teeth, the shape of the flank and the length of the forming, in addition to the elongation of the material. As long as the tooth side after the forming of the workpiece does not hinder the extraction of the mold teeth, most of the tooth shapes can be extruded. The sides of the formed teeth may be straight, involute or other complicated spherical convex shape, and the formed flank and the root may not have sharp corners, and all the tooth surfaces are opposite.
3, the characteristics of the molding
Pitch and tooth tolerance are the main parameters after forming. If the blank is well controlled, it will produce extremely high precision stability. Unlike axial compression, which controls the outer diameter, the radially extruded tip has a flange. That is because the axial flow of the material during forming is unconstrained.
4, material requirements
In general, the hardness of the material is greater than HRC25, and the elongation is at least 15% to improve the mold life. In addition, the smaller the pressure angle, the larger the mold load, which will affect the mold life and the cumulative error of the pitch.
5, equipment construction
The device has both horizontal and vertical knots. The mold disassembly and replacement is modular, simple and fast. It can be loaded and unloaded manually or fully automated. The hydraulic system can be placed inside the fuselage or separately outside the fuselage.