China Gear Parts Machining supplier
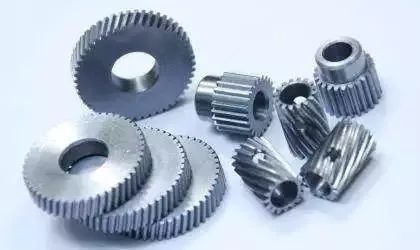
Gears are mechanical parts that can match each other and have teeth. Gear transmission can complete functions such as deceleration, speed increase and direction change. It is extremely versatile in mechanical transmission and in the entire mechanical field. This paper summarizes the processing technology of gear parts.
1. The function and structure of the gear
Gears, although designed in different shapes and sizes due to their different functions in the machine, can always be divided into two parts: the ring gear and the wheel body. Common cylindrical gears have the following categories (below): Disc gears, sleeve gears, internal gears, shaft gears, sector gears, racks. Among them, disc gears are the most widely used.
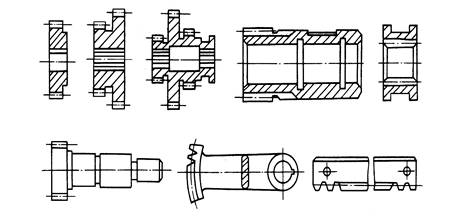
A spur gear can have one or more ring gears. Ordinary single ring gear has good manufacturability. The small ring gear of the double or triple gear is often affected by the shoulder, which limits the use of certain processing methods. Generally, only the insert teeth can be used. If the gear accuracy is high and it is necessary to shave or grind the gear, the multi-ring gear is usually made into a combination of single-ring gears.
2. Precision requirements for cylindrical gears
The manufacturing precision of the gear itself has a great influence on the working performance, load bearing capacity and service life of the whole machine. According to the conditions of use of the gear, the following requirements are imposed on the gear transmission:
1. motion accuracy
The gear is required to accurately transmit motion and the transmission ratio is constant. That is, the gear is required to be in one revolution, and the corner error does not exceed a certain range.
2, work stability
This requires that the change of the instantaneous speed ratio when the gear rotates should be small, that is to say, the angle error in a short period should be limited. This requirement limits the instantaneous change in the speed ratio is smaller gear is rotated, that is, to limit the angular error in a short period.
3. Contact accuracy
When the gear transmits power, the contact stress is too large in order to avoid uneven distribution of the load, causing premature wear of the tooth surface. This requires that the tooth surface contact should be uniform when the gear is working, and that a certain contact area and a desired contact position are ensured.4. Tooth side clearance
When gear transmission is required, a certain gap is left between the non-working tooth surfaces to store the lubricating oil, to compensate for dimensional changes caused by temperature and elastic deformation, and some errors in processing and assembly.
3. Gear material
The gears should be of the appropriate material according to the working conditions used. The choice of gear material has a direct impact on the machining performance and service life of the gear.
Generally, the gears are made of medium carbon steel (such as 45 steel) and low and medium carbon alloy steels, such as 20Cr, 40Cr, 20CrMnTi. Important requirements higher gear can be selected 38CrMoAlA nitrided steel. Non-force transmission gears can also be made of cast iron, bakelite or nylon cloth and other materials.
Heat treatment of gears
In the gear processing, two heat treatment processes are arranged according to different purposes:
1. Blank heat treatment
Pre-heat treatment or tempering is arranged before and after the tooth blank processing. The main purpose is to eliminate the residual stress caused by forging and roughing, improve the machinability of the material and improve the comprehensive mechanical properties.
2. Tooth surface heat treatment
After the tooth profile processing, in order to improve the hardness and wear resistance of the tooth surface, heat treatment processes such as carburizing and quenching, high frequency induction heating quenching, carbonitriding and nitriding are often performed.
Gear blank
The blank form of the gears mainly consists of bars, forgings and castings.
Bars are used for gears that are small in size, simple in construction, and low in strength. When the gear is required to have high strength, wear resistance and impact resistance, the forgings are often used, and the gears having a diameter larger than 400-600 mm are commonly used for casting blanks.
In order to reduce the amount of machining, for large-size, low-precision gears, the gear teeth can be directly cast; For small size and complex gears, precision casting, pressure casting, precision forging, powder metallurgy, hot rolling and cold extrusion are available. The new process produces tooth blanks with gear teeth to increase labor productivity and save raw materials.