Frequently Asked Questions about CNC Machining and Turning Small Aluminum Parts
Summary:
This paper analyzes the problems of clamping, machining processes, and cutting performance of small aluminum parts in processing. Through this time solving the problems in aluminum processing, we have gained a lot of experience and received good economic benefits.
Keywords: small aluminum parts, tools, fixtures, coolant
I. Introduction
Alumina was reduced to aluminum by electrolysis in the laboratory in 1808 and was used as a building material on the spire of the Washington Monument in the United States in 1884. The density of pure aluminum is small (ρ=2.7g/m3), which is about 1/3 of that of iron and its melting point is low (660°C). Aluminum is a face-centered cubic structure, it has a very high plasticity (δ: 32~40%, ψ: 70~90%), easy to process, and can be made into various profiles and plates. The corrosion resistance is good; however, the strength of pure aluminum is very low, and the annealing state σb value is about 8 kgf/mm2, so it is not suitable as a structural material. Through long-term production practices and scientific experiments, people have gradually strengthened aluminum by adding alloying elements and using heat treatment methods, thus forming a series of aluminum alloys. The alloy formed by adding certain elements can maintain high strength while maintaining the properties of pure aluminum, and the σb values can reach 24 to 60 kgf/mm2, respectively. This makes its "specific strength" (the ratio of strength to specific gravity σb/ρ) outweigh many alloy steels and becomes an ideal structural material. It is widely used in machinery manufacturing, transportation machinery, power machinery and aerospace industries.
Aluminum alloys can be divided into deformed aluminum alloys and cast aluminum alloys by processing methods.Deformed aluminum alloy is divided into non-heat-treatable aluminum alloy and heat-treatable aluminum alloy.
Non-heat-treatable type can not improve the mechanical properties through heat treatment, can only be achieved through cold deformation processing, it mainly includes high-purity aluminum , industrial high-purity aluminum , industrial pure aluminum and rust-proof aluminum.
Heat-treatable aluminum alloys can be improved in mechanical properties by quenching and aging and other heat treatment methods. It can be divided into hard aluminum , wrought aluminum , super hard aluminum and special alumi num alloys .
It can be seen from the above that the aluminum cold processing methods are used more often: casting , cold rolling , cold drawing , cold forging , cold extrusi on , stamping , etc.
In the actual production work, we often also encounter some of the aluminum alloy cutting processing such as: turning , drilling , boring , milling , planing , broaching and saw ing.
Second, the emergence of the problem
In 2008, our factory made Low-Volume's product S3GA-004 for customers. Its material is aluminum alloy and the alloy grade is 1100.
The structure of the parts is shown in the figure below (Figure 1):
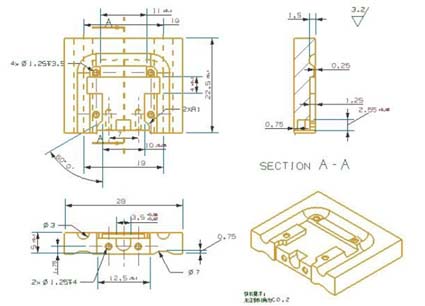
In selecting the factory's conventional processing methods, three problems have emerged in the course of processing:
1, aluminum parts easily deformed during processing;
2. There is no special fixture, only one side can be processed at a time, and the efficiency is low;
3, easy to stick knife phenomenon.
Third, find the cause of the problem and analysis and resolution
Based on the workpiece, the aluminum alloy material has a high degree of ductility. Parts of the machine are often machined to varying degrees of deformation due to internal stresses, cutting heat, and the effects of clamping. The methods that need to be taken to ensure the part's forming quality and control the deformation are:
(1) In the milling process, whether it is rough milling or fine milling, the part should be symmetrically processed and repeatedly turned so that the stresses on both sides are released uniformly.
(2) When the two sides of the part are rough finished, they are left for several hours (usually 48H) for natural aging, so that the residual stress can be fully released and then processed.
(3) When the part is milled on one side, try to take a small margin and multiple passes.
(4) Because of the high strength and toughness of the material, the depth of the knife should be controlled, and sufficient cooling is ensured during cutting to prevent deformation of the part due to the heat of cutting. At the same time, the hardness of the jig must be taken into consideration.
I have taken the following measures in response to the currently processed parts:
If the shape of the part is known, symmetry processing has little effect on its shape, because the middle part of this part (in the main view of Fig. 1) is an open cavity, and it is possible to adopt the general method of isometric ring cutting from the inside to the outside. Therefore, it is not necessary to deliberately program symmetry processing. In natural aging, for example, the precision of the parts is not so high, so if the time is sufficient, natural aging treatment can be used. In single-sided milling, in order to improve the machining efficiency and take into account the accuracy of the parts, Therefore, only when I finish machining, I use small allowance and more knife. After the test cut, the dimensions fully meet the requirements of the drawings.
Due to the fact that the workpiece is too small and the material is soft, I determine the cause of the workpiece deformation based on experience:
1. The vise jaws are much harder than the workpieces and it is easier to pinch the workpiece.
2. Operators do not have a good grasp of the strength of the fixture. Therefore, I decided to use a softer material to clamp the workpiece. Generally, the materials commonly used in my factory include copper, aluminum, steel, iron, and other common metals. According to the factory's existing conditions, I decided to use aluminum because of the relatively low price of aluminum compared with copper.
The principles that should be followed in the installation of parts and fixtures are:
(1) When the parts processing volume is not large, it should try to use combination fixtures, adjustable fixtures and other universal fixtures to shorten production preparation time and save production costs;
(2) Consider the use of special fixtures in batch production and strive for a simple structure;
(3) The loading and unloading of parts should be quick, convenient and reliable to shorten the pause time of the machine tool; Each component on the fixture shall not interfere with the machine tool's machining of each surface of the component, ie, the fixture shall be open for its positioning, and the clamping mechanism components shall not affect the cutting tool in the process (such as collisions, etc.).
In summary, I chose to use two aluminum alloys and mill them into vises and jaws to replace the existing rigid jaws. Coupled with mass production considerations, it is clearly possible to increase work efficiency by clamping multiple workpieces at a time. Therefore, four longer slots are milled on the two aluminum jaws so that multiple workpieces can be clamped at a time. A simple fixture is created as shown below: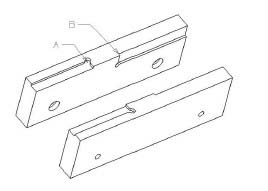
The groove on the right is used to process the main view in Figure 1, and its back, too much clamped in the size is more difficult to control, Therefore, the slot can be clamped three times at a time, and the right slot is dedicated to the side (that is, the top view of Figure 1). In the minute hand, I chose to fix the inner jaw in the clamp: the intersection of slot 2 and the extended surface of the side (that is, the two points A and B in the figure above), which is easy to modify and stable. After the second trial processing, the obtained products can meet the requirements of the drawings, and the clamping effect is shown in the following two diagrams (Figure 2, Figure 3):
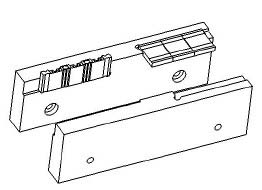
There are several reasons why the Sticky knife phenomenon occurs during processing:
1, the toughness of the material is too great;
2, tool wear is more serious;
3, cooling is not enough;
4, whether the speed and feed fully.
Due to the conditions of the factory, I started to use ordinary HSS tools rather than special tools for aluminum alloys. These tools are relatively poor in terms of aluminum swarf and can easily cause sticky aluminum swarf. I also use general-purpose cutting fluid BD-G101 for coolant.
The above factors are analyzed as follows:
Because of the lower melting point of aluminum, if the cooling is not done enough, it will allow partial confinement during the processing and stick to the cutting tool, resulting in built-up edge, Greatly reduces the quality of the workpiece surface, will change the shape of the cutting edge and ultimately lead to cutting edge chipping, or Sticky knife phenomenon.
Later, I switched to use the Jiejie brand STC-X407 aluminum special cutting fluid, which increased the flow of the cutting fluid and enhanced the cooling effect. The aluminum parts are relatively soft and it seems to be no problem to use cheap HSS cutters. After careful observation and found that it is not true, white knife is very easy to wear, durability is not high, In contrast alloy tool coated cemented carbide cutting tools, cermet cutting tools have much advantages, Take the more commonly used carbide tool, the hardness at room temperature up to 89-94HRA, heat resistance of 800-1000 °C, Carbide cutting tools allow 5 to 10 times higher cutting speed than HSS tools. However, its low bending strength is 1/2 to 1/4 of that of high-speed steel, and its impact toughness is several times lower than high speed.
From the above data, it can be seen that the use of alloy cutting tools in the processing of relatively soft materials such as aluminum has considerable advantages both in terms of processing accuracy and durability. Although the price is more expensive, but in terms of mass production, due to the relatively high tool durability, the average cost per workpiece is lower than the cost of machining with high-speed rigid tools. It can be said that the cost is reduced to a certain extent and the quality of processing is better guaranteed.
Taking into account the quality and cost aspects, in the comments to the leadership, the use of aluminum alloy special carbide cutting tools; Due to the use of higher hardness tools, the processing method should be changed accordingly. I use high speed fast feed processing method. In terms of feed and speed, because it is not a high-speed machine, the general speed is given to the S5000. Since the tool is small in terms of the feed is about F400, according to the actual processing conditions, since the self-adjusting operating crew.
Fourth, the effect of problem solving
Through the improvement of fixtures and the replacement of tools and coolants, the production efficiency and the quality of the products have been significantly improved. The output increased from about the original 40 minutes to 25 minutes, and the scrap rate dropped from the original 20% to 4%. Greatly reduced production costs for the factory and achieved good economic benefits.
Five. Conclusion
Through this processing of aluminum S3GA-004, we have accumulated a lot of valuable experience in aluminum processing. It has contributed a lot to the reduction of costs by enterprises, and with the rapid development of the new national economy, advanced processing technologies have continued to emerge. Under the rapid advancement of science and technology, only by working hard to learn new knowledge, seriously researching new issues, and innovating continuously, can we lay a solid foundation for future work.
This paper analyzes the problems of clamping, machining processes, and cutting performance of small aluminum parts in processing. Through this time solving the problems in aluminum processing, we have gained a lot of experience and received good economic benefits.
Keywords: small aluminum parts, tools, fixtures, coolant
I. Introduction
Alumina was reduced to aluminum by electrolysis in the laboratory in 1808 and was used as a building material on the spire of the Washington Monument in the United States in 1884. The density of pure aluminum is small (ρ=2.7g/m3), which is about 1/3 of that of iron and its melting point is low (660°C). Aluminum is a face-centered cubic structure, it has a very high plasticity (δ: 32~40%, ψ: 70~90%), easy to process, and can be made into various profiles and plates. The corrosion resistance is good; however, the strength of pure aluminum is very low, and the annealing state σb value is about 8 kgf/mm2, so it is not suitable as a structural material. Through long-term production practices and scientific experiments, people have gradually strengthened aluminum by adding alloying elements and using heat treatment methods, thus forming a series of aluminum alloys. The alloy formed by adding certain elements can maintain high strength while maintaining the properties of pure aluminum, and the σb values can reach 24 to 60 kgf/mm2, respectively. This makes its "specific strength" (the ratio of strength to specific gravity σb/ρ) outweigh many alloy steels and becomes an ideal structural material. It is widely used in machinery manufacturing, transportation machinery, power machinery and aerospace industries.
Aluminum alloys can be divided into deformed aluminum alloys and cast aluminum alloys by processing methods.Deformed aluminum alloy is divided into non-heat-treatable aluminum alloy and heat-treatable aluminum alloy.
Non-heat-treatable type can not improve the mechanical properties through heat treatment, can only be achieved through cold deformation processing, it mainly includes high-purity aluminum , industrial high-purity aluminum , industrial pure aluminum and rust-proof aluminum.
Heat-treatable aluminum alloys can be improved in mechanical properties by quenching and aging and other heat treatment methods. It can be divided into hard aluminum , wrought aluminum , super hard aluminum and special alumi num alloys .
It can be seen from the above that the aluminum cold processing methods are used more often: casting , cold rolling , cold drawing , cold forging , cold extrusi on , stamping , etc.
In the actual production work, we often also encounter some of the aluminum alloy cutting processing such as: turning , drilling , boring , milling , planing , broaching and saw ing.
Second, the emergence of the problem
In 2008, our factory made Low-Volume's product S3GA-004 for customers. Its material is aluminum alloy and the alloy grade is 1100.
The structure of the parts is shown in the figure below (Figure 1):
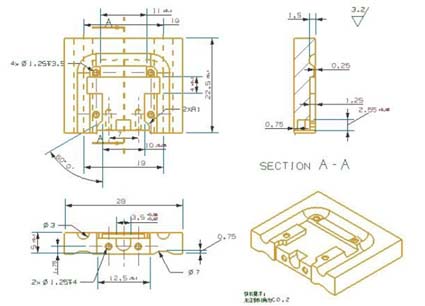
In selecting the factory's conventional processing methods, three problems have emerged in the course of processing:
1, aluminum parts easily deformed during processing;
2. There is no special fixture, only one side can be processed at a time, and the efficiency is low;
3, easy to stick knife phenomenon.
Third, find the cause of the problem and analysis and resolution
Based on the workpiece, the aluminum alloy material has a high degree of ductility. Parts of the machine are often machined to varying degrees of deformation due to internal stresses, cutting heat, and the effects of clamping. The methods that need to be taken to ensure the part's forming quality and control the deformation are:
(1) In the milling process, whether it is rough milling or fine milling, the part should be symmetrically processed and repeatedly turned so that the stresses on both sides are released uniformly.
(2) When the two sides of the part are rough finished, they are left for several hours (usually 48H) for natural aging, so that the residual stress can be fully released and then processed.
(3) When the part is milled on one side, try to take a small margin and multiple passes.
(4) Because of the high strength and toughness of the material, the depth of the knife should be controlled, and sufficient cooling is ensured during cutting to prevent deformation of the part due to the heat of cutting. At the same time, the hardness of the jig must be taken into consideration.
I have taken the following measures in response to the currently processed parts:
If the shape of the part is known, symmetry processing has little effect on its shape, because the middle part of this part (in the main view of Fig. 1) is an open cavity, and it is possible to adopt the general method of isometric ring cutting from the inside to the outside. Therefore, it is not necessary to deliberately program symmetry processing. In natural aging, for example, the precision of the parts is not so high, so if the time is sufficient, natural aging treatment can be used. In single-sided milling, in order to improve the machining efficiency and take into account the accuracy of the parts, Therefore, only when I finish machining, I use small allowance and more knife. After the test cut, the dimensions fully meet the requirements of the drawings.
Due to the fact that the workpiece is too small and the material is soft, I determine the cause of the workpiece deformation based on experience:
1. The vise jaws are much harder than the workpieces and it is easier to pinch the workpiece.
2. Operators do not have a good grasp of the strength of the fixture. Therefore, I decided to use a softer material to clamp the workpiece. Generally, the materials commonly used in my factory include copper, aluminum, steel, iron, and other common metals. According to the factory's existing conditions, I decided to use aluminum because of the relatively low price of aluminum compared with copper.
The principles that should be followed in the installation of parts and fixtures are:
(1) When the parts processing volume is not large, it should try to use combination fixtures, adjustable fixtures and other universal fixtures to shorten production preparation time and save production costs;
(2) Consider the use of special fixtures in batch production and strive for a simple structure;
(3) The loading and unloading of parts should be quick, convenient and reliable to shorten the pause time of the machine tool; Each component on the fixture shall not interfere with the machine tool's machining of each surface of the component, ie, the fixture shall be open for its positioning, and the clamping mechanism components shall not affect the cutting tool in the process (such as collisions, etc.).
In summary, I chose to use two aluminum alloys and mill them into vises and jaws to replace the existing rigid jaws. Coupled with mass production considerations, it is clearly possible to increase work efficiency by clamping multiple workpieces at a time. Therefore, four longer slots are milled on the two aluminum jaws so that multiple workpieces can be clamped at a time. A simple fixture is created as shown below:
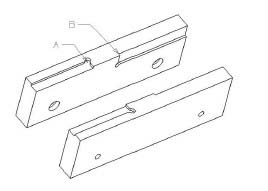
The groove on the right is used to process the main view in Figure 1, and its back, too much clamped in the size is more difficult to control, Therefore, the slot can be clamped three times at a time, and the right slot is dedicated to the side (that is, the top view of Figure 1). In the minute hand, I chose to fix the inner jaw in the clamp: the intersection of slot 2 and the extended surface of the side (that is, the two points A and B in the figure above), which is easy to modify and stable. After the second trial processing, the obtained products can meet the requirements of the drawings, and the clamping effect is shown in the following two diagrams (Figure 2, Figure 3):
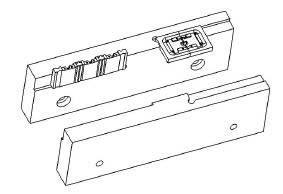
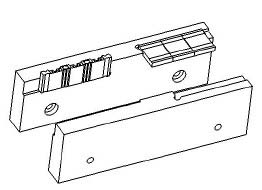
There are several reasons why the Sticky knife phenomenon occurs during processing:
1, the toughness of the material is too great;
2, tool wear is more serious;
3, cooling is not enough;
4, whether the speed and feed fully.
Due to the conditions of the factory, I started to use ordinary HSS tools rather than special tools for aluminum alloys. These tools are relatively poor in terms of aluminum swarf and can easily cause sticky aluminum swarf. I also use general-purpose cutting fluid BD-G101 for coolant.
The above factors are analyzed as follows:
Because of the lower melting point of aluminum, if the cooling is not done enough, it will allow partial confinement during the processing and stick to the cutting tool, resulting in built-up edge, Greatly reduces the quality of the workpiece surface, will change the shape of the cutting edge and ultimately lead to cutting edge chipping, or Sticky knife phenomenon.
Later, I switched to use the Jiejie brand STC-X407 aluminum special cutting fluid, which increased the flow of the cutting fluid and enhanced the cooling effect. The aluminum parts are relatively soft and it seems to be no problem to use cheap HSS cutters. After careful observation and found that it is not true, white knife is very easy to wear, durability is not high, In contrast alloy tool coated cemented carbide cutting tools, cermet cutting tools have much advantages, Take the more commonly used carbide tool, the hardness at room temperature up to 89-94HRA, heat resistance of 800-1000 °C, Carbide cutting tools allow 5 to 10 times higher cutting speed than HSS tools. However, its low bending strength is 1/2 to 1/4 of that of high-speed steel, and its impact toughness is several times lower than high speed.
From the above data, it can be seen that the use of alloy cutting tools in the processing of relatively soft materials such as aluminum has considerable advantages both in terms of processing accuracy and durability. Although the price is more expensive, but in terms of mass production, due to the relatively high tool durability, the average cost per workpiece is lower than the cost of machining with high-speed rigid tools. It can be said that the cost is reduced to a certain extent and the quality of processing is better guaranteed.
Taking into account the quality and cost aspects, in the comments to the leadership, the use of aluminum alloy special carbide cutting tools; Due to the use of higher hardness tools, the processing method should be changed accordingly. I use high speed fast feed processing method. In terms of feed and speed, because it is not a high-speed machine, the general speed is given to the S5000. Since the tool is small in terms of the feed is about F400, according to the actual processing conditions, since the self-adjusting operating crew.
Fourth, the effect of problem solving
Through the improvement of fixtures and the replacement of tools and coolants, the production efficiency and the quality of the products have been significantly improved. The output increased from about the original 40 minutes to 25 minutes, and the scrap rate dropped from the original 20% to 4%. Greatly reduced production costs for the factory and achieved good economic benefits.
Five. Conclusion
Through this processing of aluminum S3GA-004, we have accumulated a lot of valuable experience in aluminum processing. It has contributed a lot to the reduction of costs by enterprises, and with the rapid development of the new national economy, advanced processing technologies have continued to emerge. Under the rapid advancement of science and technology, only by working hard to learn new knowledge, seriously researching new issues, and innovating continuously, can we lay a solid foundation for future work.