University Student Manufacturing China's First 3D Printed Metal Racing
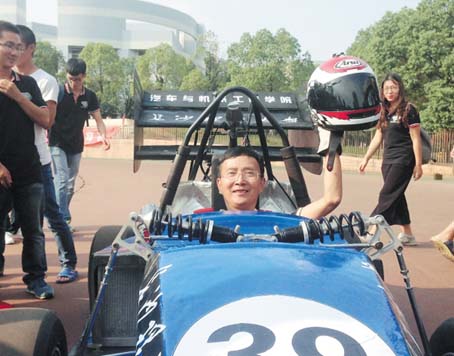
The team leader Peng Fei prepared the vehicle test and test drive for the FNX-16.
Changsha University of Science and Technology has such a group of “scientific and technical men” who developed and funded themselves and worked overtime to design and manufacture a “metal 3D printing car”—FNX-16. According to public information, such a metal 3D printing car is still the first in the country. Yesterday, Changsha University of Technology held a new car conference to launch this new car. And announced that the car is about to set off for the 2016 China University Formula Auto Race.
China's first metal 3D printing concept racing
"Boom -" At 4 o'clock yesterday afternoon, at the Jinpenling Campus of Changsha University of Science and Technology, a FNX-16 car weighing about 200 kilograms circumnavigated all around the track. After testing, it has a speed of 130 kilometers per hour, stable driving posture, and quick control. I saw the car drifting from time to time, accelerating, attracting a large number of students watching, everyone shouted in unison. This is the first "metal 3D printing race car" in China - the launch ceremony of FNX-16 at Changsha University of Science and Technology. It is about to set up a 2016 China University Formula Auto Race.
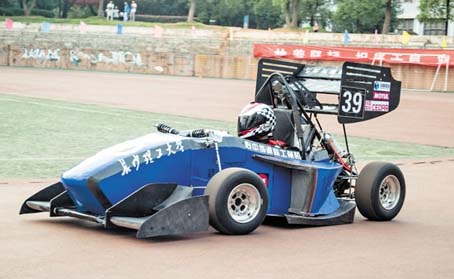
"About 3 years ago, the Chinese racing industry introduced the concept of 3D printing of polymer materials. Today, we made the nation’s first metal 3D printing as a concept car. These metal 3D printed parts are stronger, more stable, and more expensive. For us, it is more difficult to make. Zhao Shucheng, the captain of the Changsha University of Science and Technology's racing team, said about the creation of the car. Five years before and after the Changsha University of Science and Technology, more than 300 university students relayed for 5 years to create the "FNX Series" Formula Student Racing Car. It was already the fifth "FNX-16" car yesterday. The car began to develop from last year and it was not until the end of the summer vacation this year. During the research phase, many of my classmates worked until late at 8 am. In terms of funding, due to insufficient funding, Zhao Shusheng and some team members successively raised tens of thousands of RMB, and at the same time contacted an industry-leading 3D printing company as a sponsor and sponsored more than 200,000 rmbs of the team.
Research and development process
Racing design is done by college students
The cost of metal 3D printing is very high, and a metal 3D printed part costs 10,000 yuan. The sponsors only manage production, and the engineering design must be done by the college students themselves. For example, a suspension column was reworked five times. Under the guidance of teacher Yuan Xiang, manufacturers engineers working Tang et al guidance, the team redesigned several times, change plans, do match, took a summer vacation, Finally, the column, rocker, etc. of the suspension system were manufactured in 3D printing of metal. Due to the use of the most advanced SLS selective laser sintering technology, all parts are tightly meshed and work well.
Students doing, learning, exploration side, from design to manufacturing and then to adapt, bought thousands of parts. Sleeping garage, Insufficient funds, they will make up their own money to buy parts, stay in school during the summer and winter vacations and work overtime... "Once, in order to debug the engine, We found a sponsored field and took a two-hour bus to the factory in the hot summer. The crack of dawn to go out, and came back a starry sky. ” Zhao Shucheng said that from the quest for sponsorship, parts processing, vehicle assembly, car landing, and finally ready to participate in the competition, all by the team to complete. "Team members have different ages and specialties, but we all have a common racing dream."
"This time, the process of making a car has developed its own thinking and has exercised its own innovative ability. "Team member Tao Yiwei said that the FNX-16 is only about 200 kilograms in weight, and its driving posture is much more stable than the previous version.
Cao Yu, secretary of the Party Committee of the School of Automobile and Mechanical Engineering at Changsha University of Science and Technology, said with emotion that these students have made arduous pioneering efforts and made outstanding achievements. From them, they can see the bright future of “Made in China 2025”.
3D printing can produce various metal parts for racing cars
"Included intake manifolds, hubs, steering wheels, aerodynamic kits and many other components are manufactured using 3D printing technology. “Wang Hui, a member of the team, said, “If mechanical methods are used, many parts need to be manufactured in many small parts, with different molds and machine tools. After using 3D printing technology, it only needs to be modeled on the software and imported into the printer. Disposable can print out the entire automotive systems. ”
In the entire production process, metal 3D printing is somewhat different from plastic 3D printing, requiring the use of special additives. This means that it needs to be divided into multiple levels and printed in layers to create the desired shape. At the same time, metals can be broken down into very fine metal powders by lasers. The diameter of this powder is less than half the diameter of human hair, which means that metal 3D printers can produce very small and complex components. The main metal parts that make up the chassis of the car, including aluminum and steel, can be completed by 3D printing.
Future prospects
The automotive industry will make extensive use of 3D printing technology
According to the rules of the China University Formula Auto Race, vehicles must use four-stroke gasoline engines with a displacement of no more than 610cc. Therefore, the FNX-16 uses a 600cc motorcycle engine. In order to make this car race better, the entire team was divided into multiple groups such as power, suspension, and body to make this car as light as possible, more robust and more maneuverable. The 40 members of the team have a professional division of labor, from the frame body manufacturing, engine manufacturing, to financial management, propaganda outreach, all have dedicated personnel.
It is understood that BMW Germany is one of the first automotive companies to start using 3D printing technology. Back in 1990, shortly after the official birth of 3D printing, they introduced the technology into their own fast technology center.
China has a huge industrial market and hundreds of thousands of industrial enterprises above the scale. Industrial companies will become the most important customers of metal 3D printing in the future. With 3D technology, large-scale industries will no longer need oversized factory buildings, and the future manufacturing base will be smaller, faster, smarter, and the production capacity will be several times higher than at present. "The future automobile industry will inevitably use 3D printing technology more widely," said Wang Hui.