Titanium Alloy Deep Hole Drilling Boring Processing
Titanium alloy tube material Tc6, tube bore diameter Φ40, length 575, The deep-hole processing technology of this titanium alloy material is the first deep-hole processing technology we have come into contact with. The deep hole is similar to the hollow structure of a typical long axis type part, especially the deep hole whose part has a hole diameter size of Φ40; With the company's deep hole processing equipment (T2120 deep hole drilling boring machine) can not be matched; Because the outer diameter of the supporting shank on the original machine tool is Φ38, the total length of the part during machining must be 750-1500mm. Under the existing conditions, it is impossible to realize the deep hole processing requirements for the diameter of the pipe. The deep hole machining technology of titanium alloy tubes has become a key technology to be solved in the development of parts.
As shown in Figure 1,
2.2 special tooling design
2.2.1 Special deep hole cutter design.
Due to the determination of the deep-hole processing equipment (deep hole drilling boring machine T2120), the design of the arbor must be matched with the machine cutting and sealing system. Since the inner diameter of the deep hole of the titanium alloy tube is Ф40, the design structure of the inside diameter and outside diameter of the arbor is limited. On the one hand, the outer diameter of the cutter bar cannot be too large, resulting in a decrease in the inflow of high-pressure oil during deep-hole machining. Insufficient pressure is generated, which affects the swarf removal function of deep hole machining. Arbor easy to produce chip clogging phenomenon. On the other hand, when designing the arbor, the maximum inner diameter of the arbor should also be taken into consideration. The inner and outer diameters of the cutter bar must be matched to ensure the firmness and reliability of the rectangular thread at the connection of the cutter bar head, and the cutter bar has enough rigidity. At the same time, it is necessary to meet and realize the chip removal function of the deep hole processing equipment (T2120 deep hole drilling boring machine), Ensure that under the action of high-pressure oil, the chips are smoothly discharged into the scrap box along the internal hole of the cutter rod.
2.2.2 Tool design.
Separately designed special deep-hole drill bits, Deep hole reaming drill, Adaptor, Deep hole reamer and matching reamer seat.
2.3 Design the positioning seal structure connected with the machine tool and the part, that is, the selected design seal transition adapter sleeve structure, realize the sealing function of the contact surface between the part and the machine tool, solve the smooth transition of the joint, and make the part and the tool form a closed space. In the deep hole cutting process, a closed high-pressure circulation system is formed to prevent the leakage of high-pressure oil and realize the functions of cooling, chip removal, and lubrication during deep hole machining.
3, Titanium tubes deep hole machining process embodiment
In deep hole processing of titanium alloy pipes, the conventional deep hole machining method is still used in the machining process. Our production site through the use of equipment after the transformation, the installation of a dedicated deep hole Arbor and supporting tools, deep hole machining, The specific processing steps are divided into three steps: Drilling - reaming - hinged hole, processing trials,
as shown in picture 2
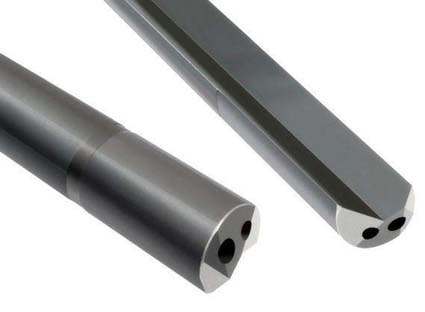
Figure 2 Deep hole drilling, reaming and deep hole reaming
As shown in Figure 1,
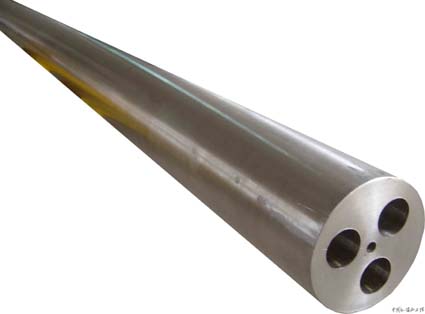
Figure 1 Parts Structure
1, analysis of processing technology difficulties
The outer diameter and technical conditions of the parts are strictly required, and their technical difficulties appear as deep-hole machining of thin-walled parts. And it is difficult to process the titanium alloy material: Tc6, in order to meet the equipment conditions, the length of the deep hole to be processed in the process is specified as 1170mm (the length of two parts), the aspect ratio is 1170:38, and the surface roughness is Ra0.5 ; Because of the special material of the parts, the deep hole diameter size does not match the machine system. The structural design, material selection and manufacturing of the arbor on special deep hole drilling machines are very difficult, resulting in extremely difficult deep hole machining of parts. At the same time, the existing equipment needs to be improved to meet the matching requirements of the newly designed cutter bar. For this purpose, we carry out special work on deep-hole machining of thin-walled titanium alloy shaft parts.
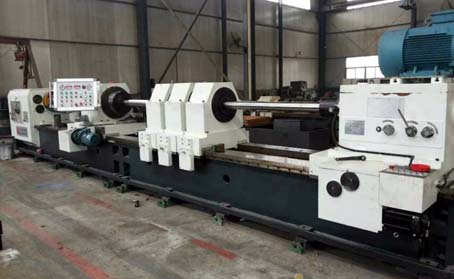
2. Formulate specific measures
2.1 Determine the processing plan
We titanium alloy deep-processing as the research topic, the development of new tooling, positioning sealing structure design, restructuring deep hole drilling equipment and other technical problems, Determined to use the company's existing deep-hole equipment to improve this machining program, That is, in the T2120 deep hole drilling machine, deep hole drilling and development of titanium alloy tubes is carried out.
Specific improvements have been formulated as follows:
Reorganize the positioning system structure of the machine tool shank;
Design and component matching positioning seal structure;
Research deep hole processing, tool material;
To meet the design requirements of the tool shank, the tool structure dimensions are formulated. At the same time, the basic research work such as the chip removal function of the inner hole of the arbor is also required when designing the arbor.
To this end, we have designed and manufactured (9 types) special deep hole tools, boring heads, tool holders and other equipment and equipment supporting parts.
A large number of processing tests were carried out to ensure the smooth development of deep hole drilling and processing of titanium alloy tubes. After the test, it meets the needs of production and development and solves the key problem of deep hole processing technology for titanium alloy tubes.
First of all, we combine the deep hole structure of the titanium alloy pipe and the existing equipment in the company to formulate a specific process route and formulate the process specification.
Titanium alloy pipe processing route is as follows:
Rough turn benchmark - Drilling deep hole - Extended hole - Reaming - finishing cylindrical - test.
The outer diameter and technical conditions of the parts are strictly required, and their technical difficulties appear as deep-hole machining of thin-walled parts. And it is difficult to process the titanium alloy material: Tc6, in order to meet the equipment conditions, the length of the deep hole to be processed in the process is specified as 1170mm (the length of two parts), the aspect ratio is 1170:38, and the surface roughness is Ra0.5 ; Because of the special material of the parts, the deep hole diameter size does not match the machine system. The structural design, material selection and manufacturing of the arbor on special deep hole drilling machines are very difficult, resulting in extremely difficult deep hole machining of parts. At the same time, the existing equipment needs to be improved to meet the matching requirements of the newly designed cutter bar. For this purpose, we carry out special work on deep-hole machining of thin-walled titanium alloy shaft parts.
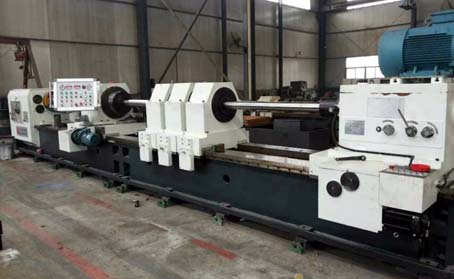
2. Formulate specific measures
2.1 Determine the processing plan
We titanium alloy deep-processing as the research topic, the development of new tooling, positioning sealing structure design, restructuring deep hole drilling equipment and other technical problems, Determined to use the company's existing deep-hole equipment to improve this machining program, That is, in the T2120 deep hole drilling machine, deep hole drilling and development of titanium alloy tubes is carried out.
Specific improvements have been formulated as follows:
Reorganize the positioning system structure of the machine tool shank;
Design and component matching positioning seal structure;
Research deep hole processing, tool material;
To meet the design requirements of the tool shank, the tool structure dimensions are formulated. At the same time, the basic research work such as the chip removal function of the inner hole of the arbor is also required when designing the arbor.
To this end, we have designed and manufactured (9 types) special deep hole tools, boring heads, tool holders and other equipment and equipment supporting parts.
A large number of processing tests were carried out to ensure the smooth development of deep hole drilling and processing of titanium alloy tubes. After the test, it meets the needs of production and development and solves the key problem of deep hole processing technology for titanium alloy tubes.
First of all, we combine the deep hole structure of the titanium alloy pipe and the existing equipment in the company to formulate a specific process route and formulate the process specification.
Titanium alloy pipe processing route is as follows:
Rough turn benchmark - Drilling deep hole - Extended hole - Reaming - finishing cylindrical - test.
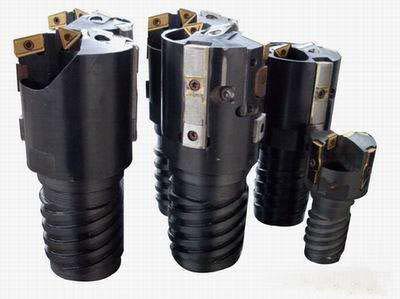
2.2 special tooling design
2.2.1 Special deep hole cutter design.
Due to the determination of the deep-hole processing equipment (deep hole drilling boring machine T2120), the design of the arbor must be matched with the machine cutting and sealing system. Since the inner diameter of the deep hole of the titanium alloy tube is Ф40, the design structure of the inside diameter and outside diameter of the arbor is limited. On the one hand, the outer diameter of the cutter bar cannot be too large, resulting in a decrease in the inflow of high-pressure oil during deep-hole machining. Insufficient pressure is generated, which affects the swarf removal function of deep hole machining. Arbor easy to produce chip clogging phenomenon. On the other hand, when designing the arbor, the maximum inner diameter of the arbor should also be taken into consideration. The inner and outer diameters of the cutter bar must be matched to ensure the firmness and reliability of the rectangular thread at the connection of the cutter bar head, and the cutter bar has enough rigidity. At the same time, it is necessary to meet and realize the chip removal function of the deep hole processing equipment (T2120 deep hole drilling boring machine), Ensure that under the action of high-pressure oil, the chips are smoothly discharged into the scrap box along the internal hole of the cutter rod.
2.2.2 Tool design.
Separately designed special deep-hole drill bits, Deep hole reaming drill, Adaptor, Deep hole reamer and matching reamer seat.
2.3 Design the positioning seal structure connected with the machine tool and the part, that is, the selected design seal transition adapter sleeve structure, realize the sealing function of the contact surface between the part and the machine tool, solve the smooth transition of the joint, and make the part and the tool form a closed space. In the deep hole cutting process, a closed high-pressure circulation system is formed to prevent the leakage of high-pressure oil and realize the functions of cooling, chip removal, and lubrication during deep hole machining.
3, Titanium tubes deep hole machining process embodiment
In deep hole processing of titanium alloy pipes, the conventional deep hole machining method is still used in the machining process. Our production site through the use of equipment after the transformation, the installation of a dedicated deep hole Arbor and supporting tools, deep hole machining, The specific processing steps are divided into three steps: Drilling - reaming - hinged hole, processing trials,
as shown in picture 2
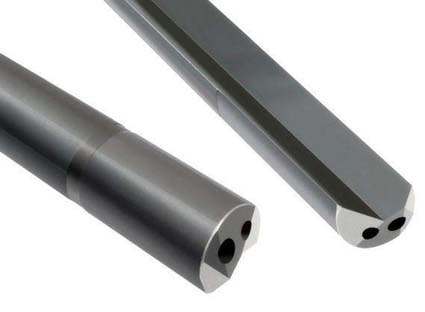
Figure 2 Deep hole drilling, reaming and deep hole reaming
After the machining test, the following problems occurred in the deep hole surface of the first titanium alloy pipe:The diameter of the inner hole is locally poor, the surface roughness is not good, and the surface of the inner hole has a groove mark.
After analysis, we found that the size of the transition joint of the floating reamer is the upper limit, the cutting force at the leading end of the reamer is uneven, and the production of the floating blade shifts, causing the inner hole diameter size to exceed the drawing requirements. In addition, the occurrence of groove marks in the inner hole is due to the thinner wall, deeper hole, and the phenomenon of easy occurrence of vibrating knife and squeezing knife when machining the reaming hole. In addition, the reamer may cause the above problems after worn.
In response to the causes of these problems, gradually improve and improve the tool structure, develop improved methods. Increase the actual size of the reamer before machining and the centering effect of the guide end of the floating reamer, so as to ensure the reaming of the reamer after automatic centering. At the same time check the wear of the tool and replace the new one in time. This ensures deep hole machining dimensions in subsequent machining. Completed the first deep hole processing and development of titanium alloy tubes. And in the subsequent processing, 48 pieces of titanium alloy pipe deep hole processing tasks were successively completed. Satisfy the company's development and production needs, to solve the key to deep hole processing technology of titanium alloy pipe.
4, processing summary
The verification of the test results proves that it was feasible to formulate this kind of deep-hole machining plan. The deep-hole processing method and processing technology of this titanium alloy material have been incorporated into relevant technical documents and applied to a dedicated production line.
After analysis, we found that the size of the transition joint of the floating reamer is the upper limit, the cutting force at the leading end of the reamer is uneven, and the production of the floating blade shifts, causing the inner hole diameter size to exceed the drawing requirements. In addition, the occurrence of groove marks in the inner hole is due to the thinner wall, deeper hole, and the phenomenon of easy occurrence of vibrating knife and squeezing knife when machining the reaming hole. In addition, the reamer may cause the above problems after worn.
In response to the causes of these problems, gradually improve and improve the tool structure, develop improved methods. Increase the actual size of the reamer before machining and the centering effect of the guide end of the floating reamer, so as to ensure the reaming of the reamer after automatic centering. At the same time check the wear of the tool and replace the new one in time. This ensures deep hole machining dimensions in subsequent machining. Completed the first deep hole processing and development of titanium alloy tubes. And in the subsequent processing, 48 pieces of titanium alloy pipe deep hole processing tasks were successively completed. Satisfy the company's development and production needs, to solve the key to deep hole processing technology of titanium alloy pipe.
4, processing summary
The verification of the test results proves that it was feasible to formulate this kind of deep-hole machining plan. The deep-hole processing method and processing technology of this titanium alloy material have been incorporated into relevant technical documents and applied to a dedicated production line.
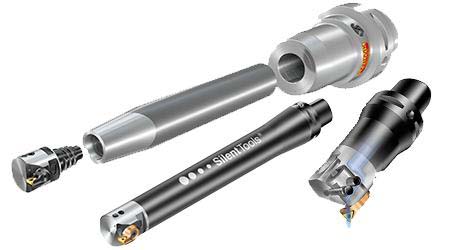