project
Stamping parts (also known as pressing) is the process of placing flat sheet metal((stainless steel, iron, aluminum, copper and other anisotropic materials) in either blank or coil form into a stamping press where a tool and die surface forms the metal into a parts shape.
Stamping parts includes a variety of sheet-metal forming manufacturing processes, such as punching using a machine press or stamping press, blanking, embossing, bending, flanging, and coining.
This could be a single stage operation where every stroke of the press produces the desired form on the sheet metal part, or could occur through a series of stages. The process is usually carried out on sheet metal, but can also be used on other materials, such as polystyrene.
Mold design
The metal mold is a special tool installed on the press, and the metal material is made into a part or product of a desired shape through pressure. Such a special tool is collectively referred to as a metal mold.
(1). Analysis of materials (product materials, mold materials).
(2). Bump mold gap size. (For parts with high dimensional precision and high perpendicularity, small clearance values should be used. For parts with low requirements for vertical section and dimensional accuracy, the blanking force should be reduced and the life of the stamping die should be increased. Larger gap values: The following empirical formulas and practical gap gauges are used:
Soft material: t<1 mm, c=[3% to 4%] tt=1 to 3mm, c=(5% to 8%)tt=3 ~ 5mm ,c =(8% ~10%)t
Hard materials: t <1mm, c = (4% ~ 5%) tt = 1 ~ 3mm, c = (6% ~ 8%) t = 3 ~ 8mm, c = (8% ~ 13%). )
(3). The pilot pins adequate quantity and position.
(4). Consider whether the waste rebounds and whether the mold is discharged smoothly.
(5). Whether the monitor is designed, the waste rebound sensor.
(6). Positioning plate and floating jack selection appropriate.
(7). The number of bolts (including discharge bolts), size, and position are selected properly.
(8). Consider punching power and choose a punch press.
Technology
The stamping process is a process of separating or forming a sheet to obtain a workpiece. Stamping is a kind of metal processing method. It is based on the plastic deformation of metal. It uses a die and a punching device to exert pressure on the sheet material to make the sheet material plastically deform or separate to obtain a part with a certain shape, size and performance. (Stamping).
With the unprecedented consensus on the importance of the development of advanced manufacturing technology, stamping forming technology has achieved unprecedented progress both in depth and breadth. Its characteristics are combined with high technology, and great changes have taken place in methods and systems. The penetration and cross-fusion of computer technology, information technology, modern measurement and control technologies and other stamping fields have promoted the formation and development of advanced stamping forming technologies.
Features
1, stamping is a high production efficiency, low consumption of processing methods. The stamping process is suitable for the production of large-volume parts, facilitates mechanization and automation, and has high production efficiency. At the same time, stamping production can not only strive to achieve less scrap, and even if there are scraps in some cases, it can be fully utilized.
2, the operation process is convenient, does not require the operator to have a higher level of skills.
3, stamped parts generally do not need to be machined again, with high dimensional accuracy.
4, stamping parts have better interchangeability. Stamping processing stability is better, the same batch of stamping parts. Can be used interchangeably without affecting assembly and product performance.
5. Because the stamped parts are made of plate material, its surface quality is better, which provides convenient conditions for subsequent surface treatment processes (such as electroplating and painting).
6, stamping processing can obtain high strength, high stiffness and light weight parts.
7. Stamping parts produced in batch with molds are inexpensive.
8. Stamping can create complex parts that are difficult to machine with other metal processing methods.
equipment
Drive Structure: Manual Punching Machine, Mechanical Press, Hydraulic Press, Pneumatic Press, High Speed Mechanical Press, CNC Punch (AIDA High Speed Punch, Micron High Speed Punch, KYORI High Speed Punch)
According to processing precision: ordinary punch, precision punch
According to use range: ordinary punch, special punch
Grouped equipment: Automatic Feeder, High Speed Roller Feeder, NC Servo Roll Feeder, Material Discharge Rack/Receiver, Material Straightener/Leveler, Triple Feeder Bridge Feeder, Second Machine One Thick Plate Feeder leveler, decoiling, leveling and shearing line
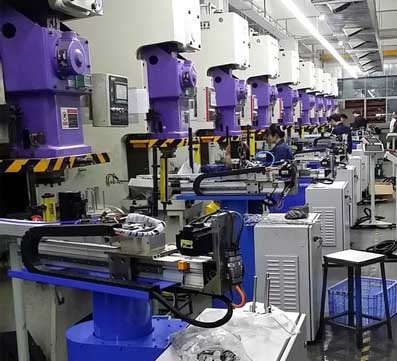
application
Metal stamping parts application areas: the automotive industry's overall stamping parts, auto parts stamping parts, electrical parts stamping parts, daily-use stamping parts, stamping parts for household electrical appliance parts, aviation special stamping parts,
1. There are stamping and processing in aerospace, aviation, military, machinery, agricultural machinery, electronics, information, railways, post and telecommunications, transportation, chemicals, medical equipment, household appliances and light industry.
2. There are many large, medium and small stamping parts on airplanes, trains, automobiles and tractors.
3. 80% of bicycles, sewing machines, and watches are stamping parts; 90% of televisions, tape recorders, and cameras are stamping parts;
4, food metal shell, steel boiler, enamel bowl and stainless steel tableware, all stamping products using the mold;
5, computer hardware stamping parts.
Detection method
Hardness testing of metal stampings uses Rockwell hardness tester. Small, complex shaped stampings cannot be tested on an ordinary bench Rockwell hardness tester. Stamping processing includes punching, bending, deep drawing, forming, finishing and other processes. The stamped parts are mainly made of hot-rolled or cold-rolled (based on cold-rolled) sheet metal materials such as carbon steel sheets, alloy steel sheets, spring steel sheets, galvanized sheets, tinplates, stainless steel sheets, copper and copper alloys. Plates, aluminum and aluminum alloy plates.
1, touch
Clean the surface of the outer cover with a clean gauze. The inspector needs to wear a touch glove to touch the surface of the stamping part along the longitudinal direction of the stamping part. This inspection method depends on the inspector's experience. If necessary, whetstones can be used to polish the suspect area and verify it, but this method is an effective method of rapid inspection.
2, Whetstone Grinding
1> First clean the surface of the outer cover with a clean gauze, then grind it with whetstone, where it has arcs and hard-to-reach areas, grind it with relatively small whetstone.
2> the choice of oilstone particle size depends on the surface conditions. It is recommended to use fine-grained whey stone. The direction of grinding of the whetstone is basically in the longitudinal direction, and it fits well on the surface of the stamping part. Part of the special place can also supplement the horizontal grinding.
3, soft gauze grinding
Clean the surface of the outer cover with a clean gauze. The surface of the stamping part is tightly attached to the surface of the stamped part by means of a flexible sand net, and it is ground to the entire surface in the longitudinal direction. Any pitting and indentation can be easily found.
4,Oiled test
Clean the surface of the outer cover with a clean gauze. Then use a clean brush to evenly apply oil to the entire outer surface of the stamping in the same direction. The stamped parts coated with oil should be tested under strong light. It is recommended to place the stamped parts upright on the body. With this method, it is easy to find tiny pits and ripples on stampings.
Surface treatment
1: galvanized, nickel-plated, chrome-plated, gold-plated, silver-plated, blackened, oxidized, electropolished, pickled, phosphatized, electrophoretically.
2: spray paint, spray, spray porcelain.
3: Polishing, brushing, grinding, shot peening, shot blasting, vibration grinding.
4: Plastic covered.
(1) Stamping Part Plating: A part to be plated is immersed in an aqueous solution containing a metal compound to be deposited, and an electric current is passed through the plating solution so that the plating metal is precipitated and deposited on the part. General hardware standard parts are plated with galvanized, copper, nickel, chromium, copper-nickel alloys, etc., sometimes boiled (blue), phosphatized, etc. are also included.
(2) Hot-dip galvanizing of stamping parts: This is accomplished by immersing the hardware parts of the carbon steel parts into a bath of zinc-dissolved zinc at a temperature of about 510°C. As a result, the iron-zinc alloy on the surface of the steel gradually becomes passivated zinc on the outer surface of the product. Hot dip aluminum plating is a similar process.
(3), stamping parts mechanical plating: It is through the coating metal particles to impact the surface of the product, and the coating is cold welded to the surface of the hardware standard product.
The cost of electroplating is generally 0.6-0.8 yuan per kilogram, hot-dip zinc is generally 1.5-2 yuan / kg, the cost is higher. Bright surface treatment methods: Galvanizing, copper plating, nickel plating, chrome plating, copper-nickel alloy plating, etc.
PREVIOUS:NONE
NEXT:Metal Terminal
NEXT:Metal Terminal