Stainless Steel Features and Applications
Stainless steel anti-corrosion elements 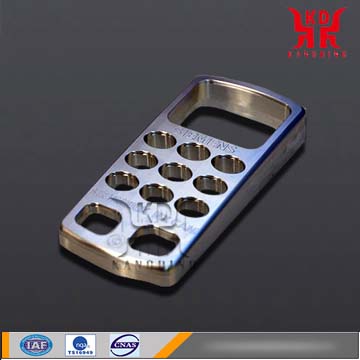
All metals react with oxygen in the atmosphere to form an oxide film on the surface. Unfortunately, the iron oxide formed on ordinary carbon steel continues to oxidize, causing the rust to continuously expand, eventually forming holes. The surface of the carbon steel can be protected by electroplating with paint or oxidation-resistant metals such as zinc, nickel and chromium. However, as people know, this protection is only a thin film. If the protective layer is damaged, the metal begins to rust.
Chromium is an essential element for obtaining corrosion resistance of stainless steel. When the chromium content in the steel reaches approximately 12%, chromium acts on oxygen in the corrosive medium to form a very thin oxide film on the surface of the steel (self-passivation film). It can stop the steel substrate from further corrosion. In addition to chromium, the commonly used alloying elements are nickel, molybdenum, titanium, niobium, copper, nitrogen, etc., to meet the various requirements of stainless steel anti-corrosion structure and performance requirements.
Heat resistance
Heat resistance means that stainless steel can still maintain its excellent physical and mechanical properties at high temperatures. Effect of carbon: Carbon is strongly formed in austenitic stainless steels and stabilizes austenite, and expands the elements of the austenite zone. The ability of carbon to form austenite is about 30 times that of nickel. Carbon is a kind of interstitial element, and the strength of austenitic stainless steel can be significantly improved by solid solution strengthening. Carbon can also improve the stress and corrosion resistance of austenitic stainless steels in high-concentration chlorides (eg, 42% MgCl2 boiling solution).
However, in austenitic stainless steels, carbon is often seen as a harmful element. This is mainly due to the fact that carbon can form high-chromium Cr23C6-type carbon compounds with chromium in steel under certain conditions (such as welding or heating at 450-850°C) in the corrosion resistance of stainless steel. As a result, the partial chrome is depleted and the corrosion resistance of the steel, especially the resistance to intergranular corrosion, is reduced. therefore. Since the 1960s, newly developed chromium-nickel austenitic stainless steels have mostly carbon contents of less than 0.03% or 0.02% of ultra-low carbon types. It can be seen that as the carbon content decreases, the intergranular corrosion susceptibility of the steel decreases. When the carbon content is less than 0.02%, the most obvious effect is obtained. Some experiments also pointed out that carbon also increases the pitting tendency of chromium austenitic stainless steels. Due to the harmful effects of carbon, not only the carbon content as low as possible should be controlled as required during the austenitic stainless steel smelting process. And in the subsequent hot, cold processing and heat treatment process is also preventing the stainless steel surface carbonation, to avoid the precipitation of chromium carbides.
Chemical Composition
Corrosion resistance of stainless steel decreases with increasing carbon content. Therefore, most stainless steels have low carbon content, and some steels have even lower wC than 0.03% (for example, 00Cr12). The main alloying element in stainless steel is Cr. Only when the Cr content reaches a certain value, the steel has corrosion resistance. Therefore, stainless steel generally has more than 13% wCr. Stainless steel also contains elements such as Ni, Ti, Mn, N, and Nb. Stainless steel is usually classified according to the state of organization: martensitic steel, ferritic steel, austenitic steel and so on. In addition, it can be divided into: chromium stainless steel, chromium nickel stainless steel and chromium manganese nitrogen stainless steel.
1, ferritic stainless steel:
chromium containing 12% to 30%. Its corrosion resistance, toughness and weldability increase with the increase of chromium content, and its resistance to chloride stress corrosion is superior to other types of stainless steel. Crl7, Cr17Mo2Ti, Cr25, Cr25Mo3Ti, Cr28 and the like belong to this class. Ferritic stainless steel has high corrosion resistance and oxidation resistance because of its high chromium content, but its mechanical properties and process performance are poor. It is mostly used for acid-resistant structures with less stress and for oxidation resistant steels. This kind of steel can resist the corrosion of the atmosphere and salt water solution, and has the characteristics of high temperature oxidation resistance, small thermal expansion coefficient, etc. Used in food factory equipment, but also in the production of high temperature parts, such as gas turbine parts.
2. Austenitic stainless steel:
Chromium is more than 18%, also contains about 8% nickel and a small amount of molybdenum, titanium, nitrogen and other elements.
Good overall performance, resistant to many media corrosion. The commonly used grades of austenitic stainless steels include 1Cr18Ni9 and 0Cr19Ni9. The wC of the 0Cr19Ni9 steel is less than 0.08% and the steel number is marked as "0". This type of steel contains a large amount of Ni and Cr, making the steel austenitic at room temperature. This type of steel has good plasticity, toughness, weldability and corrosion resistance, and has good corrosion resistance in both oxidizing and reducing media. It is used to make acid-resistant equipment, such as corrosion-resistant containers and equipment parts, and conveying pipes. Austenitic stainless steels are generally treated by solid solution, ie steel is heated to 1050 to 1150°C and then water cooled to obtain single-phase austenite structure.
3. Austenitic-ferritic duplex stainless steel:
It combines the advantages of austenitic and ferritic stainless steels and has superplasticity. Austenite and ferrite are about half of stainless steel. In the case where the C content is low, the Cr content is 18% to 28%, and the Ni content is 3% to 10%. Some steels also contain alloying elements such as Mo, Cu, Si, Nb, Ti, and N. This kind of steel combines the characteristics of austenitic and ferritic stainless steels. Compared with ferrite, it has higher plasticity and toughness, no brittleness at room temperature, and significantly improved intergranular corrosion resistance and welding performance. At the same time, it retains the brittleness and high thermal conductivity of ferritic stainless steel at 475°C, and is characterized by superplasticity. Compared with austenitic stainless steels, they have high strength and resistance to intergranular corrosion and chloride stress corrosion resistance. Duplex stainless steel has excellent pitting corrosion resistance and is also a nickel-stainless steel.
4, martensitic stainless steel:
High strength but poor plasticity and weldability. The commonly used grades of martensitic stainless steel are 1Cr13, 3Cr13, etc., due to higher carbon content. Therefore, it has a higher strength, hardness and wear resistance, but slightly less corrosion resistance. Applied high mechanical performance requirements, the general corrosion resistance requires some parts, Such as springs, turbine blades, hydraulic press valves. This kind of steel is used after quenching and tempering.
5, precipitation hardening stainless steel:
Has good formability and good weldability, Applied to ultra-high strength materials in the nuclear industry, aerospace and aerospace industries, components can be classified into Cr series (SUS400), Cr-Ni series (SUS300), Cr-Mn-Ni (SUS200) and precipitation hardening system (SUS600).
200 Series - Chromium-Nickel-Manganese Austenitic Stainless Steel
300 Series - Chromium-nickel Austenitic Stainless Steel
301 - Good ductility for forming products. It can also be hardened by machine. Good weldability. The wear resistance and fatigue strength are better than 304 stainless steel.
302—Corrosion resistance is the same as 304. The strength is better due to the relatively high carbon content.
303 - Easy to trim by adding a small amount of sulfur and phosphorus.
304 - that is 18/8 stainless steel. The GB grade is 0Cr18Ni9.
309 - better temperature resistance than 304.
316—after 304, the second most widely used steel grade, Mainly used in the food industry and surgical equipment, adding molybdenum element to obtain a special structure that resists corrosion. Because it has better resistance to chloride corrosion than 304, it is also used as "marine steel". SS316 is usually used in nuclear fuel recovery devices. 18/10 grade stainless steel also generally meets this application level.
321 - except that the addition of titanium reduces the risk of weld corrosion of the material, other properties are similar to 304
Series 400 - Ferritic and Martensitic Stainless Steels
408—Good heat resistance, weak corrosion resistance, 11% Cr, 8% Ni.
409 - The cheapest model (British and American), commonly used as automotive exhaust pipe, is a ferritic stainless steel (chrome steel).
410—Martensite (high strength chrome steel), good wear resistance, poor corrosion resistance.
416 - Added sulfur improves the material's processability.
420—"Blade-grade" martensitic steel, similar to Brinell's high chromium steel, the earliest stainless steel. Also used for surgical tools, can do very bright.
430—ferritic stainless steel, decorative, for example for automotive accessories. Good formability, but poor temperature resistance and corrosion resistance.
440—High-strength cutting tool steel with slightly high carbon content. After appropriate heat treatment, it can obtain higher yield strength, and the hardness can reach 58HRC, which is among the hardest stainless steels. The most common application example is the "razor blade." There are three types of commonly used models: 440A, 440B, 440C, and 440F (easy processing type).
Series 500 - Heat-resistant chromium alloy steel.
Series 600 - martensitic precipitation hardened stainless steel.
630—The most commonly used precipitation hardening stainless steel model, also commonly called 17-4; 17% Cr, 4% Ni
Stainless steel is usually divided into matrix structures:
1, ferritic stainless steel.
Chromium 12% to 30%. Its corrosion resistance, toughness and weldability increase with the increase of chromium content, and its resistance to chloride stress corrosion is superior to other types of stainless steel.
2, austenitic stainless steel.
Chromium is more than 18%, and it also contains about 8% nickel and a small amount of molybdenum, titanium, and nitrogen. Good overall performance, resistant to many media corrosion.
3, austenitic - ferritic duplex stainless steel.
It combines the advantages of austenitic and ferritic stainless steels and has superplasticity.
Stainless steel surface processing grade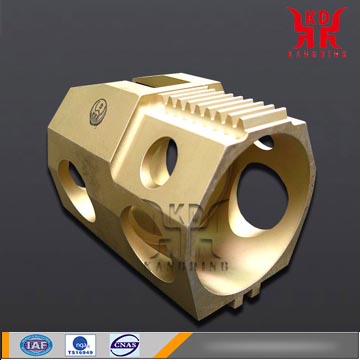
The original side: NO.1
After the hot rolling, annealed and pickled surface. Generally used for cold-rolled materials, industrial tanks, chemical industry equipment, thickness 2.0MM-8.0MM.
Blunt surface: NO.2D
Heat treatment after cold rolling, pickling. Its material is soft, the surface is silvery white luster, used for deep-drawing processing, such as automotive components, water pipes and so on.
Matt surface: NO.2B
After cold rolling, heat treatment, pickling, and finish rolling are used to make the surface a moderate brightness. Because the surface is smooth, easy to re-grind, so that the surface is more bright, widely used, such as tableware, building materials. After surface treatment with improved mechanical properties, almost all applications are satisfied.
Coarse sand NO.3
The product was ground with a 100-120 grinding tape. Better gloss with discontinuous coarse pattern. Used for interior and exterior decoration materials, electrical products and kitchen equipment.
Fine sand: NO.4
The product was ground with a 150-180 grain size tape. With better gloss, with a discontinuous coarse pattern, the stripes are thinner than NO.3. For baths, interior and exterior decorative materials, electrical products, kitchen equipment and food equipment.
#320
Polished product with a No. 320 grinding belt. With better gloss, with a discontinuous coarse pattern, the stripe is thinner than NO.4. For baths, interior and exterior decorative materials, electrical products, kitchen equipment and food equipment.
Wool face HAIRLINE:
HLNO.4 is produced by continuous grinding of abrasive belts of appropriate grain size (Subdivision No. 150-320). Mainly used for building decoration, elevators, doors, panels of buildings, etc.
Shiny: BA
After the cold rolling, bright annealing was performed and the flattened product was obtained. Excellent surface gloss and high reflectivity. Like a mirror surface. For home appliances, mirrors, kitchen equipment, decorative materials and so on.
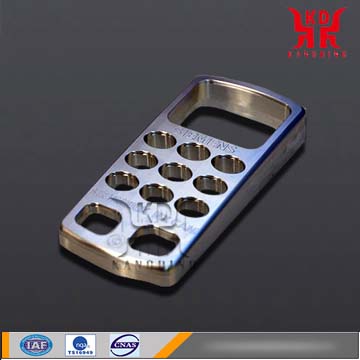
All metals react with oxygen in the atmosphere to form an oxide film on the surface. Unfortunately, the iron oxide formed on ordinary carbon steel continues to oxidize, causing the rust to continuously expand, eventually forming holes. The surface of the carbon steel can be protected by electroplating with paint or oxidation-resistant metals such as zinc, nickel and chromium. However, as people know, this protection is only a thin film. If the protective layer is damaged, the metal begins to rust.
Chromium is an essential element for obtaining corrosion resistance of stainless steel. When the chromium content in the steel reaches approximately 12%, chromium acts on oxygen in the corrosive medium to form a very thin oxide film on the surface of the steel (self-passivation film). It can stop the steel substrate from further corrosion. In addition to chromium, the commonly used alloying elements are nickel, molybdenum, titanium, niobium, copper, nitrogen, etc., to meet the various requirements of stainless steel anti-corrosion structure and performance requirements.
Heat resistance
Heat resistance means that stainless steel can still maintain its excellent physical and mechanical properties at high temperatures. Effect of carbon: Carbon is strongly formed in austenitic stainless steels and stabilizes austenite, and expands the elements of the austenite zone. The ability of carbon to form austenite is about 30 times that of nickel. Carbon is a kind of interstitial element, and the strength of austenitic stainless steel can be significantly improved by solid solution strengthening. Carbon can also improve the stress and corrosion resistance of austenitic stainless steels in high-concentration chlorides (eg, 42% MgCl2 boiling solution).
However, in austenitic stainless steels, carbon is often seen as a harmful element. This is mainly due to the fact that carbon can form high-chromium Cr23C6-type carbon compounds with chromium in steel under certain conditions (such as welding or heating at 450-850°C) in the corrosion resistance of stainless steel. As a result, the partial chrome is depleted and the corrosion resistance of the steel, especially the resistance to intergranular corrosion, is reduced. therefore. Since the 1960s, newly developed chromium-nickel austenitic stainless steels have mostly carbon contents of less than 0.03% or 0.02% of ultra-low carbon types. It can be seen that as the carbon content decreases, the intergranular corrosion susceptibility of the steel decreases. When the carbon content is less than 0.02%, the most obvious effect is obtained. Some experiments also pointed out that carbon also increases the pitting tendency of chromium austenitic stainless steels. Due to the harmful effects of carbon, not only the carbon content as low as possible should be controlled as required during the austenitic stainless steel smelting process. And in the subsequent hot, cold processing and heat treatment process is also preventing the stainless steel surface carbonation, to avoid the precipitation of chromium carbides.
Chemical Composition
Corrosion resistance of stainless steel decreases with increasing carbon content. Therefore, most stainless steels have low carbon content, and some steels have even lower wC than 0.03% (for example, 00Cr12). The main alloying element in stainless steel is Cr. Only when the Cr content reaches a certain value, the steel has corrosion resistance. Therefore, stainless steel generally has more than 13% wCr. Stainless steel also contains elements such as Ni, Ti, Mn, N, and Nb. Stainless steel is usually classified according to the state of organization: martensitic steel, ferritic steel, austenitic steel and so on. In addition, it can be divided into: chromium stainless steel, chromium nickel stainless steel and chromium manganese nitrogen stainless steel.
1, ferritic stainless steel:
chromium containing 12% to 30%. Its corrosion resistance, toughness and weldability increase with the increase of chromium content, and its resistance to chloride stress corrosion is superior to other types of stainless steel. Crl7, Cr17Mo2Ti, Cr25, Cr25Mo3Ti, Cr28 and the like belong to this class. Ferritic stainless steel has high corrosion resistance and oxidation resistance because of its high chromium content, but its mechanical properties and process performance are poor. It is mostly used for acid-resistant structures with less stress and for oxidation resistant steels. This kind of steel can resist the corrosion of the atmosphere and salt water solution, and has the characteristics of high temperature oxidation resistance, small thermal expansion coefficient, etc. Used in food factory equipment, but also in the production of high temperature parts, such as gas turbine parts.
2. Austenitic stainless steel:
Chromium is more than 18%, also contains about 8% nickel and a small amount of molybdenum, titanium, nitrogen and other elements.
Good overall performance, resistant to many media corrosion. The commonly used grades of austenitic stainless steels include 1Cr18Ni9 and 0Cr19Ni9. The wC of the 0Cr19Ni9 steel is less than 0.08% and the steel number is marked as "0". This type of steel contains a large amount of Ni and Cr, making the steel austenitic at room temperature. This type of steel has good plasticity, toughness, weldability and corrosion resistance, and has good corrosion resistance in both oxidizing and reducing media. It is used to make acid-resistant equipment, such as corrosion-resistant containers and equipment parts, and conveying pipes. Austenitic stainless steels are generally treated by solid solution, ie steel is heated to 1050 to 1150°C and then water cooled to obtain single-phase austenite structure.
3. Austenitic-ferritic duplex stainless steel:
It combines the advantages of austenitic and ferritic stainless steels and has superplasticity. Austenite and ferrite are about half of stainless steel. In the case where the C content is low, the Cr content is 18% to 28%, and the Ni content is 3% to 10%. Some steels also contain alloying elements such as Mo, Cu, Si, Nb, Ti, and N. This kind of steel combines the characteristics of austenitic and ferritic stainless steels. Compared with ferrite, it has higher plasticity and toughness, no brittleness at room temperature, and significantly improved intergranular corrosion resistance and welding performance. At the same time, it retains the brittleness and high thermal conductivity of ferritic stainless steel at 475°C, and is characterized by superplasticity. Compared with austenitic stainless steels, they have high strength and resistance to intergranular corrosion and chloride stress corrosion resistance. Duplex stainless steel has excellent pitting corrosion resistance and is also a nickel-stainless steel.
4, martensitic stainless steel:
High strength but poor plasticity and weldability. The commonly used grades of martensitic stainless steel are 1Cr13, 3Cr13, etc., due to higher carbon content. Therefore, it has a higher strength, hardness and wear resistance, but slightly less corrosion resistance. Applied high mechanical performance requirements, the general corrosion resistance requires some parts, Such as springs, turbine blades, hydraulic press valves. This kind of steel is used after quenching and tempering.
5, precipitation hardening stainless steel:
Has good formability and good weldability, Applied to ultra-high strength materials in the nuclear industry, aerospace and aerospace industries, components can be classified into Cr series (SUS400), Cr-Ni series (SUS300), Cr-Mn-Ni (SUS200) and precipitation hardening system (SUS600).
200 Series - Chromium-Nickel-Manganese Austenitic Stainless Steel
300 Series - Chromium-nickel Austenitic Stainless Steel
301 - Good ductility for forming products. It can also be hardened by machine. Good weldability. The wear resistance and fatigue strength are better than 304 stainless steel.
302—Corrosion resistance is the same as 304. The strength is better due to the relatively high carbon content.
303 - Easy to trim by adding a small amount of sulfur and phosphorus.
304 - that is 18/8 stainless steel. The GB grade is 0Cr18Ni9.
309 - better temperature resistance than 304.
316—after 304, the second most widely used steel grade, Mainly used in the food industry and surgical equipment, adding molybdenum element to obtain a special structure that resists corrosion. Because it has better resistance to chloride corrosion than 304, it is also used as "marine steel". SS316 is usually used in nuclear fuel recovery devices. 18/10 grade stainless steel also generally meets this application level.
321 - except that the addition of titanium reduces the risk of weld corrosion of the material, other properties are similar to 304
Series 400 - Ferritic and Martensitic Stainless Steels
408—Good heat resistance, weak corrosion resistance, 11% Cr, 8% Ni.
409 - The cheapest model (British and American), commonly used as automotive exhaust pipe, is a ferritic stainless steel (chrome steel).
410—Martensite (high strength chrome steel), good wear resistance, poor corrosion resistance.
416 - Added sulfur improves the material's processability.
420—"Blade-grade" martensitic steel, similar to Brinell's high chromium steel, the earliest stainless steel. Also used for surgical tools, can do very bright.
430—ferritic stainless steel, decorative, for example for automotive accessories. Good formability, but poor temperature resistance and corrosion resistance.
440—High-strength cutting tool steel with slightly high carbon content. After appropriate heat treatment, it can obtain higher yield strength, and the hardness can reach 58HRC, which is among the hardest stainless steels. The most common application example is the "razor blade." There are three types of commonly used models: 440A, 440B, 440C, and 440F (easy processing type).
Series 500 - Heat-resistant chromium alloy steel.
Series 600 - martensitic precipitation hardened stainless steel.
630—The most commonly used precipitation hardening stainless steel model, also commonly called 17-4; 17% Cr, 4% Ni
Stainless steel is usually divided into matrix structures:
1, ferritic stainless steel.
Chromium 12% to 30%. Its corrosion resistance, toughness and weldability increase with the increase of chromium content, and its resistance to chloride stress corrosion is superior to other types of stainless steel.
2, austenitic stainless steel.
Chromium is more than 18%, and it also contains about 8% nickel and a small amount of molybdenum, titanium, and nitrogen. Good overall performance, resistant to many media corrosion.
3, austenitic - ferritic duplex stainless steel.
It combines the advantages of austenitic and ferritic stainless steels and has superplasticity.
Stainless steel surface processing grade
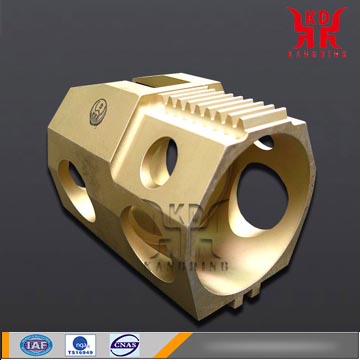
The original side: NO.1
After the hot rolling, annealed and pickled surface. Generally used for cold-rolled materials, industrial tanks, chemical industry equipment, thickness 2.0MM-8.0MM.
Blunt surface: NO.2D
Heat treatment after cold rolling, pickling. Its material is soft, the surface is silvery white luster, used for deep-drawing processing, such as automotive components, water pipes and so on.
Matt surface: NO.2B
After cold rolling, heat treatment, pickling, and finish rolling are used to make the surface a moderate brightness. Because the surface is smooth, easy to re-grind, so that the surface is more bright, widely used, such as tableware, building materials. After surface treatment with improved mechanical properties, almost all applications are satisfied.
Coarse sand NO.3
The product was ground with a 100-120 grinding tape. Better gloss with discontinuous coarse pattern. Used for interior and exterior decoration materials, electrical products and kitchen equipment.
Fine sand: NO.4
The product was ground with a 150-180 grain size tape. With better gloss, with a discontinuous coarse pattern, the stripes are thinner than NO.3. For baths, interior and exterior decorative materials, electrical products, kitchen equipment and food equipment.
#320
Polished product with a No. 320 grinding belt. With better gloss, with a discontinuous coarse pattern, the stripe is thinner than NO.4. For baths, interior and exterior decorative materials, electrical products, kitchen equipment and food equipment.
Wool face HAIRLINE:
HLNO.4 is produced by continuous grinding of abrasive belts of appropriate grain size (Subdivision No. 150-320). Mainly used for building decoration, elevators, doors, panels of buildings, etc.
Shiny: BA
After the cold rolling, bright annealing was performed and the flattened product was obtained. Excellent surface gloss and high reflectivity. Like a mirror surface. For home appliances, mirrors, kitchen equipment, decorative materials and so on.