Research on Mechanical Finishing Technology of TC4 Titanium Alloy Parts in China
TC4 has the following special physicochemical properties:
1. The thermal conductivity of TC4 is low, which makes the workpiece and tool temperature higher during the machining process;
2. TC4 has a low modulus of elasticity, which results in a large rebound after deformation under load. It causes the increase of workpiece processing error, the increase of cutting tool torque, the rapid wear of cutting edge and the decrease of durability.
3, TC4 has low hardness and high chemical activity, which results in dissolution and diffusion between TC4 and cutting tools at high temperature, resulting in sticking knife, burning knife, breaking knife and other phenomena.
Based on the above analysis, the processing technology of TC4 should include the following principles:
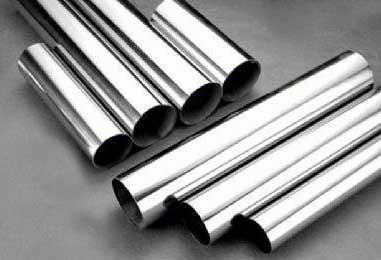
1. Due to the low thermal conductivity of TC4, low plasticity and high work hardening tendency. The cutting force is large during machining, and the cutting temperature is high, which causes the tool to be easily worn and the life is reduced. Therefore, the tool should be selected from materials with good wear resistance, high heat hardness and sufficient toughness. YG8, YG8W and YG10H are selected for roughing, and YG8W or YP15 (YGRM) is used for finishing.
2. Optimize the cutting conditions, including the machine tool-clamp-tool system rigidity.
3. Choose a reasonable amount of cutting. Under normal circumstances, the cutting speed should be low, the cutting depth should be large, and the cutting can not be stopped during the cutting process.
4. Improve chip control and ensure reliable chip breaking measures.
Test design
Considering the above factors, this process studies the single-factor test and multi-factor orthogonal test to study the cutting process of TC4, and analyze the surface integrity of the processed samples. The evaluation indicators mainly include: Surface roughness, processing hardness, residual stress and microstructure.
1. Single factor test: Referring to the actual production cutting range, the range of the various factors of the test is set to:
(1) The milling speed level changes to: 40, 80, 100, 120, 140 m/min. The feed speed is 50 mm/min, the axial milling depth is 1.5 mm, and the radial milling depth is 28 mm.
(2) The positive level change of each tooth feed is 0.05, 0.07, 0.09, 0.11, 0.13mm, Keep the milling speed 40mm/min, The axial milling depth is 0.9mm. The radial milling depth is unchanged at 8 mm;
(3) The axial milling depth level changes to 0.4, 0.6, O.8, 1.0, 1.2, 1.5 mm. Keep the milling speed 40mm/min, Feed rate 40.7mm/min, The radial milling depth is unchanged at 8mm.
(4) The radial milling depth level changes to 4, 6, 8, 10, 12 5, 14, 16 mm. Keep the milling speed k=40mm/min, Feed rate 40.7mm/min, The axial milling depth is constant at 1 mm.
2. Multi-factor orthogonal test.
This process research uses the orthogonal design L16 to study the milling process of TC4. The specific parameters are as follows:
The milling parameters and horizontal coding are:
Milling depth (mm) | Milling speed (m/min) | Feed per tooth (mm) | Milling width (mm) | |
Upper Level (3) | 1.4 | 120 | 0.14 | 14 |
Subordinate level (1) | 1 | 100 | 0.1 | 11 |
Next level (-1) | 0.6 | 80 | 0.06 | 18 |
Lower level (3) | 0.2 | 60 | 0.02 | 5 |
Orthogonal test table:
Milling depth (mm)
|
Milling speed (m/min) | Feed per tooth (mm) | Milling width (mm) | |
1 | 1.4 | 100 | 0.06 | 11 |
2 | 1.4 | 80 | 0.14 | 5 |
3 | 1.4 | 120 | 0.02 | 8 |
4 | 1.4 | 60 | 0.1 | 14 |
5 | 1 | 60 | 0.06 | 8 |
6 | 1 | 120 | 0.14 | 14 |
7 | 1 | 80 | 0.02 | 11 |
8 | 1 | 100 | 0.1 | 5 |
9 | 0.6 | 60 | 0.14 | 11 |
10 | 0.6 | 120 | 0.06 | 5 |
11 | 0.6 | 80 | 0.1 | 8 |
12 | 0.6 | 100 | 0.02 | 14 |
13 | 0.2 | 100 | 0.14 | 8 |
14 | 0.2 | 80 | 0.06 | 14 |
15 | 0.2 | 120 | 0.1 | 11 |
16 | 0.2 | 60 | 0.02 | 5 |
Through the above orthogonal test, the degree of influence of each processing parameter on the surface integrity of the machine can be understood, and the best processing technology can be obtained.
Third, analysis and evaluation:
The surface roughness is measured by white light interferometer. Each of the tests was carried out by taking 5 places in the milling direction.
Moreover, hardening is the result of the combined effect of the thermo-mechanical coupling non-uniform stress field on the machined surface of the workpiece, which is related to the cutting conditions and the mechanical properties of the workpiece material. In this work, the influence of milling factors on work hardening and hardening law were studied by measuring the hardness of the surface layer after TC4 milling. The hardness of the machined surface was measured by a Vickers microhardness tester, and the degree of work hardening was obtained by comparing the surface hardness with the hardness of the unmachined surface. Each sample was taken at 5 locations in the milling direction for measurement.
The TC4 material is very sensitive to stress conditions, especially the residual stress of the machined surface and its distribution state is very important for the rational use of the component. The residual stress of the machined surface has the difference between residual tensile stress and residual compressive stress. Residual tensile stress reduces the fatigue strength and service life of the part, while residual compressive stress sometimes increases the fatigue strength and service life of the part. The uneven distribution of residual stress on each part of the machined surface will also cause deformation of the workpiece, affecting the shape and dimensional accuracy of the workpiece. Therefore, the research work uses X-ray method to study the surface residual stress and its distribution of TC4TC4 material at high speed milling.
The microstructures of several small samples were cut by WEDM, and the cross section of the vertical feeding direction was taken as the observation plane. After polishing, the appropriate etching solution was selected for surface corrosion and observed by SEM.