Processing and Application of Titanium Alloy Materials in Aerospace Equipment Parts
Key word: Titanium Alloy Engine Materials, Titanium Alloy Aircraft Equipment Parts, Titanium Alloy Parts Processing, High Temperature Titanium Alloy, Ti-6242S, BT36, Ti60
Titanium alloy has the advantages of high specific strength, good corrosion resistance and high temperature resistance. Since the 1950s, titanium alloys have developed rapidly in the aerospace industry. Titanium alloy is one of the main structural materials of modern aircraft and engines, which can reduce the weight of the aircraft and improve the structural efficiency. The proportion of titanium in aircraft materials: The passenger aircraft Boeing 777 is 7%, the transport aircraft C-17 is 10.3%, the fighter F-4 is 8%, the F-15 is 25.8%, and the F-22 is 39%.
The development of high-performance aero engines is driving the development of high-temperature titanium alloys, and the use temperature of titanium alloys is gradually increasing. From the 1950s, it was 350 °C represented by Ti-6Al-4V alloy. After the development of IMI679 and IMI829, it has been upgraded to 600 °C represented by IMI834 alloy. At present, the world's advanced high-temperature titanium alloys include Ti-6242S, Ti-1100 in the United States; IMI834 in the United Kingdom; BT36 in Russia and Ti-60 in China. Table 2 shows the composition and performance characteristics of the main high temperature titanium alloy at 600 °C.
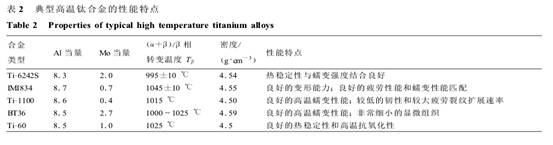
Table 2: Performance characteristics of typical high temperature titanium alloy
Ti-6242S (Ti-6Al-2Sn-4Zr-2Mo-0.1Si) titanium alloy was developed in the United States in the 1960s to meet the needs of improving the high temperature performance of titanium alloys. In particular, a near-alpha titanium alloy developed to meet the requirements of jet engine use. The maximum use temperature of the alloy is 540 ° C, and the room temperature σ b = 930 MPa. It is characterized by a good combination of strength, creep strength, toughness and thermal stability. And has good welding performance, mainly used in gas turbine engine parts, engine structural sheet parts, aircraft body hot end parts.
BT36 (Ti-6.2A1-2Sn-3.6Zr-0.7Mo-0.1Y-5.0W-0.15Si) alloy is a titanium alloy that was successfully developed in Russia at a temperature of 600-650 °C. 5% W and about 0.1% Y were added to the alloy. The addition of W has a significant effect on improving the thermal strength of the alloy. The grain size of the alloy can be refined obviously by adding trace Y, and the plasticity and thermal stability of the alloy can be improved.
Ti60 (Ti-5.8 Al-4.8 Sn-2.OZr-1.0 Mo-0.35Si-0.85Nd) alloy. A 600 °C high temperature titanium alloy was developed by the Metal Research Institute of Chinese Academy of Sciences and Baoji Nonferrous Metal Processing Plant on the basis of Ti55 alloy. One of the characteristics of Ti60 alloy is the addition of 1% Nd (mass fraction) to the alloy. Rare earth phases rich in Nd, Sn and O were formed by internal oxidation to reduce the oxygen content in the matrix. Thereby, it plays a role in purifying the matrix and improving the thermal stability of the alloy. Semi-industrial pilot tests (including die forging of compressor discs) and comprehensive performance measurements have been carried out on Ti60 alloy.
According to the research status at home and abroad, the future development trend of high temperature titanium alloys is:
(1) Develop a new high-temperature titanium alloy above 600 °C. It can adjust the composition of existing high-temperature titanium alloys, improve the processing technology, or develop new high-temperature titanium alloys to improve the use temperature of high-temperature titanium alloys.
(2) The role of rare earth elements in high temperature titanium alloys remains to be further studied. The high temperature titanium alloy containing rare earth elements developed in China has reached a temperature of 600 ° C, and its performance shows good. However, the mechanism of rare earth elements in alloys needs further study, laying a theoretical foundation for the development of high temperature titanium alloys containing rare earth elements.
(3) The alloy develops in the direction of multi-strength strengthening. The optimization of alloy composition is becoming more and more important, and the Ti-Al-Sn-Zr-Mo-Si-(RE) system is dominated by near-α-titanium alloy; Si element is an indispensable element in high temperature titanium alloys.
Titanium alloy has the advantages of high specific strength, good corrosion resistance and high temperature resistance. Since the 1950s, titanium alloys have developed rapidly in the aerospace industry. Titanium alloy is one of the main structural materials of modern aircraft and engines, which can reduce the weight of the aircraft and improve the structural efficiency. The proportion of titanium in aircraft materials: The passenger aircraft Boeing 777 is 7%, the transport aircraft C-17 is 10.3%, the fighter F-4 is 8%, the F-15 is 25.8%, and the F-22 is 39%.
The development of high-performance aero engines is driving the development of high-temperature titanium alloys, and the use temperature of titanium alloys is gradually increasing. From the 1950s, it was 350 °C represented by Ti-6Al-4V alloy. After the development of IMI679 and IMI829, it has been upgraded to 600 °C represented by IMI834 alloy. At present, the world's advanced high-temperature titanium alloys include Ti-6242S, Ti-1100 in the United States; IMI834 in the United Kingdom; BT36 in Russia and Ti-60 in China. Table 2 shows the composition and performance characteristics of the main high temperature titanium alloy at 600 °C.
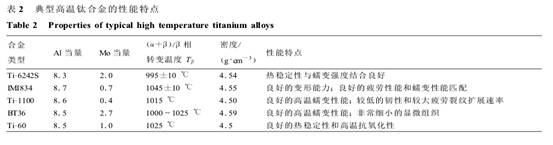
Table 2: Performance characteristics of typical high temperature titanium alloy
Ti-6242S (Ti-6Al-2Sn-4Zr-2Mo-0.1Si) titanium alloy was developed in the United States in the 1960s to meet the needs of improving the high temperature performance of titanium alloys. In particular, a near-alpha titanium alloy developed to meet the requirements of jet engine use. The maximum use temperature of the alloy is 540 ° C, and the room temperature σ b = 930 MPa. It is characterized by a good combination of strength, creep strength, toughness and thermal stability. And has good welding performance, mainly used in gas turbine engine parts, engine structural sheet parts, aircraft body hot end parts.
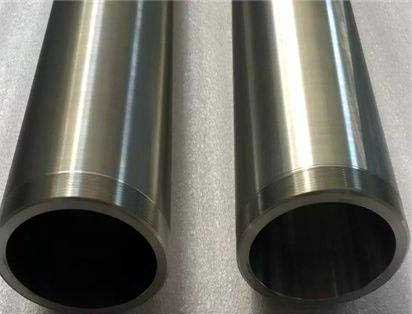
BT36 (Ti-6.2A1-2Sn-3.6Zr-0.7Mo-0.1Y-5.0W-0.15Si) alloy is a titanium alloy that was successfully developed in Russia at a temperature of 600-650 °C. 5% W and about 0.1% Y were added to the alloy. The addition of W has a significant effect on improving the thermal strength of the alloy. The grain size of the alloy can be refined obviously by adding trace Y, and the plasticity and thermal stability of the alloy can be improved.
Ti60 (Ti-5.8 Al-4.8 Sn-2.OZr-1.0 Mo-0.35Si-0.85Nd) alloy. A 600 °C high temperature titanium alloy was developed by the Metal Research Institute of Chinese Academy of Sciences and Baoji Nonferrous Metal Processing Plant on the basis of Ti55 alloy. One of the characteristics of Ti60 alloy is the addition of 1% Nd (mass fraction) to the alloy. Rare earth phases rich in Nd, Sn and O were formed by internal oxidation to reduce the oxygen content in the matrix. Thereby, it plays a role in purifying the matrix and improving the thermal stability of the alloy. Semi-industrial pilot tests (including die forging of compressor discs) and comprehensive performance measurements have been carried out on Ti60 alloy.
According to the research status at home and abroad, the future development trend of high temperature titanium alloys is:
(1) Develop a new high-temperature titanium alloy above 600 °C. It can adjust the composition of existing high-temperature titanium alloys, improve the processing technology, or develop new high-temperature titanium alloys to improve the use temperature of high-temperature titanium alloys.
(2) The role of rare earth elements in high temperature titanium alloys remains to be further studied. The high temperature titanium alloy containing rare earth elements developed in China has reached a temperature of 600 ° C, and its performance shows good. However, the mechanism of rare earth elements in alloys needs further study, laying a theoretical foundation for the development of high temperature titanium alloys containing rare earth elements.
(3) The alloy develops in the direction of multi-strength strengthening. The optimization of alloy composition is becoming more and more important, and the Ti-Al-Sn-Zr-Mo-Si-(RE) system is dominated by near-α-titanium alloy; Si element is an indispensable element in high temperature titanium alloys.