Methods of Descaling and Cleaning Titanium and Titanium Alloy Surfaces
This standard is applicable to the cleaning of titanium and titanium alloys before chemical etching, joining, plating and assembling, as well as the removal of foreign substances affecting corrosion protection, stability and final product quality under any conditions.
Keywords : Cleaning; descaling; pickling; titanium; Titanium alloy surface treatment
1. Scope
This standard specifies the cleaning and descaling methods for titanium and titanium alloy surfaces. It is suitable for the production, use and manufacturer of titanium and titanium alloys to remove general pollution, oxides and dirt produced during heat treatment, as well as foreign substances in the form of surface pollution.
When titanium and titanium alloys are processed, cast or formed, these methods are not mandatory for removing the dirt present, but rather provide a guide. When an oxidized contamination layer or an alpha layer is present on the surface, it must be pickled after cleaning.
2. Cleanup procedure
For greases, oils and lubricants used in the addition, forging and manufacturing operations of titanium and titanium alloys, alkali or emulsion soaking cleaners and alkaline electrolysis systems are recommended. In electrolysis, the workpiece can be either an anode or a cathode. The removal of these soils is preferably carried out prior to heat treatment or acid treatment as specified in 4.2. When using electrolysis, the voltage should be controlled to prevent spark discharge, resulting in dents on the surface of products.
3. Impact cleaning
3.1 Mechanical descaling methods, such as: Sandblasting, shot peening, steam spraying. The conditions and cleaning methods described in Chapter 4 can be used to remove hot worked scales and lubricants from titanium surfaces.
3.2 The sand used for sandblasting should be high quality, cleaned, iron-free silica sand. If carbon steel or low alloy steel products have been sprayed with this equipment, the sand used in these products cannot be used for the cleaning of titanium surfaces, but a separate cleaning sand should be provided.
3.3 If all surfaces are sandblasted, the exposed surface will be roughened by coarse sand or shot sand. To protect surface accuracy, local cleaning should be preferred with a proper pickling procedure.
3.4 When using steel sand or sand containing iron to clean titanium surface by sand blasting, pickling should be used to remove steel particles embedded in titanium surface after sand blasting.
3.5 Any grinding or shot peening cleaning may cause residual compressive stress and local deformation on the surface of materials or titanium structures. Chemical milling or contour machining should be used for processing.
3.6 In most cases, sandblasting does not mean completely eliminating pickling. Grinding does not remove contaminated layers caused by interstitial elements such as carbon, oxygen and nitrogen. When these elements are present in excess, it is more suitable to use the pickling control removal shown in 4.3.
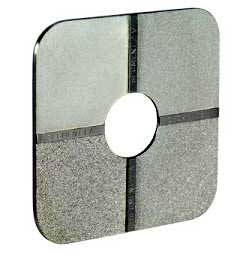
4. Pickling and descaling
4.1 In addition to the recommended rapid sandblasting or grinding of titanium surfaces, in order to ensure complete removal of metallic iron, oxides, scales, and other surface contamination, it should be pickled according to 4.3.2. If the product uses chemical milling to remove the surface oxide contamination layer and the product shape is not conducive to overall sand blasting, salt bath treatment can be used to avoid local corrosion on the surface.
4.2 For scales and lubricant residues formed in rolling, casting, forging, or assembly of titanium products.
It is usually treated by one of the following industrial methods to obtain a completely non-contaminating surface prior to final pickling according to 4.3.2.
4.2.1All corrosion-based solutions are mixed with tap water as recommended by the manufacturer.
4.2.2 The molten base salt bath is carried out at 399 to 454 ° C (750 to 850 ° F) according to the prescribed procedure.
4.2.3 The molten base salt bath is carried out at 204 ° C (400 ° F) according to the specified procedure.
4.2.4 The oxides and the colours produced by heating below 593 (1100) are usually cleaned by acid pickling. The acid liquid ratio (volume) is as follows: 10~20% (150~300g/L) nitric acid (70%)+1~2% (12~24g/L) hydrofluoric acid (60%)+water, 120°F (49°C)
4.2.5 Forged and hot-worked titanium alloys are usually mixed with graphite or glass lubricants to form hot scales, which can be completely dissolved in a base salt bath melted at 454 (850). In the follow-up treatment, some of them should be pickled by 4.3.2.
4.2.6 Heat treatable α+β and β alloys, and the treatment temperature is above 593 ° C (1100 ° F), resulting in a mixture of graphite and molybdenum disulfide lubricant residual hot scale. It is recommended to treat in a base bath of molten base at 204 ° C (400 ° F). The latter part should be pickled by the provisions of 4.3.2.
4.2.7 If the surface structure is a scale which is easy to remove, a suitable grinding method such as a wheel or belt mill, a sheet-like wheel for cutting, and grinding or shot peening can be employed.
4.3 After mechanical grinding or chemical treatment, the material can be further processed as described below to completely clean the surface.
4.3.1 After salt bath treatment and water cleaning, titanium and titanium alloy can be immersed in sulfuric acid solution to remove metamorphosed scales, and the acid used should be kept at 66 ° C (150 ° F). The concentration is: 10 to 40% by volume of sulfuric acid (95% by weight). The final finished surface whitening treatment can be completed by short-time soaking according to the acid solution specified in 4.3.2.
4.3.2 Materials that are mechanically ground according to 3.1 or chemically treated according to 4.2.1, 4.2.2, 4.2.3 may be cleaned and finished by immersion in an acid solution. The ratio of acid to liquid is: 10 to 30% by volume (150 to 450 g/L) of nitric acid (70%) + 1 to 3% by volume (12 to 36 g/L) of hydrofluoric acid (60%) at 49 ° C ( 120 ° F), maintaining a ratio of nitric acid to hydrofluoric acid of 10:1.
5. Operational precautions
5.1 When the titanium in the high temperature oxidized salt is cleaned, the workpiece is in contact with the iron-based material to generate an electric current. Titanium forms a positive or negative electrode with these iron-based materials to form an open circuit voltage of approximately 0.60V. The result of the release from the rack to the workpiece can cause the surface to overheat and may ignite. This effect can be reduced by maintaining a salt bath temperature not higher than 455 ° C (850 ° F) and using titanium fixtures or aluminium insulation between workpieces and fixtures.
5.2 For forgings or hot rolled materials with thicker scales, mechanical grinding can be used to remove excessive surface contamination before salt bath treatment.
5.3 In the process of hot forming or annealing of titanium alloys, silicon-based protective coating can reduce the formation of scales. All coatings should be removed prior to acid treatment.
5.4 Heat treated titanium forms a mixed surface contamination during fabrication or assembly, including graphite with titanium oxide or molybdenum disulfide, which should be cleaned with a molten salt bath. The treatment temperature should be 204 ° C (400 ° F) to avoid thermal deformation.
5.5 When treated in a salt bath or lye, the titanium oxide on the metal surface chemically reacts to form sodium titanate. They are soluble in acids containing sulfur and nitrogen-hydrogen fluoride. Sulfuric acid does not have any corrosive action on titanium or titanium alloy, and corrosion is suppressed by the addition of 0.25 to 1.0% of copper sulfate or ferric sulfate.
5.6 Most of the pickled salt-treated pickling is carried out in an acid solution containing sulfur and nitrogen-hydrogen fluoride. The material is circulated through the dissolved salts, water rinse, and sulfuric acid until all scales are completely removed. The final brightening treatment is done after a short cycle of soaking in the nitric acid and hydrofluoric acid baths.
5.7 In the nitric acid and hydrofluoric acid baths, the ratio of nitric acid to hydrofluoric acid is more important than the concentration of any of the acids. When the ratio is maintained at 10:1, the absorption of hydrogen during the pickling process is minimal.
5.8 In the production of titanium rolled products, the presence of an oxygen-rich layer on the exposed surface under high temperature or oxidizing atmosphere is unavoidable. When acid-washing with strong nitric acid and hydrofluoric acid solutions to remove the oxygen-rich layer and the alpha layer, it is very important that all residual oxides and scales should be completely removed to prevent preferential corrosion of the finished product.
5.9 Excess amounts of hydrogen can be removed by vacuum annealing the cleaned workpiece.
6. Inspection
6.1 Materials cleaned in accordance with this standard shall be visually inspected without significant paint, oil, grease, glass, graphite, lubricants, dirt, abrasives, iron, or other forms of contamination.
6.2 Operating in accordance with the procedures described, the hydrogen absorbed during the cleaning process should be kept to a minimum and within the allowable limits. Regular monitoring of the cleaning system should be carried out using samples of known hydrogen content and chemical analysis to complete the system. When the hydrogen content exceeds 20 ppm of the original product analysis result, the acid solution should be replaced or the acid component should be adjusted to reduce the degree of hydrogen absorption.
6.3 Product cleanliness can also be achieved by using a sample test piece. The test piece is preferably used in an amount of about 0.001 to 0.002 in. (0.025 to 0.05 mm) and is etched from both sides. After chemical corrosion, the surface of the sample should be even and smooth, bright, and free of protrusions and contamination caused by residual scales.
Keywords : Cleaning; descaling; pickling; titanium; Titanium alloy surface treatment
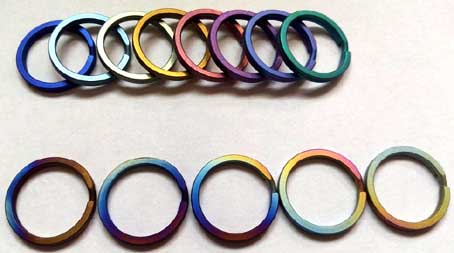
1. Scope
This standard specifies the cleaning and descaling methods for titanium and titanium alloy surfaces. It is suitable for the production, use and manufacturer of titanium and titanium alloys to remove general pollution, oxides and dirt produced during heat treatment, as well as foreign substances in the form of surface pollution.
When titanium and titanium alloys are processed, cast or formed, these methods are not mandatory for removing the dirt present, but rather provide a guide. When an oxidized contamination layer or an alpha layer is present on the surface, it must be pickled after cleaning.
2. Cleanup procedure
For greases, oils and lubricants used in the addition, forging and manufacturing operations of titanium and titanium alloys, alkali or emulsion soaking cleaners and alkaline electrolysis systems are recommended. In electrolysis, the workpiece can be either an anode or a cathode. The removal of these soils is preferably carried out prior to heat treatment or acid treatment as specified in 4.2. When using electrolysis, the voltage should be controlled to prevent spark discharge, resulting in dents on the surface of products.
3. Impact cleaning
3.1 Mechanical descaling methods, such as: Sandblasting, shot peening, steam spraying. The conditions and cleaning methods described in Chapter 4 can be used to remove hot worked scales and lubricants from titanium surfaces.
3.2 The sand used for sandblasting should be high quality, cleaned, iron-free silica sand. If carbon steel or low alloy steel products have been sprayed with this equipment, the sand used in these products cannot be used for the cleaning of titanium surfaces, but a separate cleaning sand should be provided.
3.3 If all surfaces are sandblasted, the exposed surface will be roughened by coarse sand or shot sand. To protect surface accuracy, local cleaning should be preferred with a proper pickling procedure.
3.4 When using steel sand or sand containing iron to clean titanium surface by sand blasting, pickling should be used to remove steel particles embedded in titanium surface after sand blasting.
3.5 Any grinding or shot peening cleaning may cause residual compressive stress and local deformation on the surface of materials or titanium structures. Chemical milling or contour machining should be used for processing.
3.6 In most cases, sandblasting does not mean completely eliminating pickling. Grinding does not remove contaminated layers caused by interstitial elements such as carbon, oxygen and nitrogen. When these elements are present in excess, it is more suitable to use the pickling control removal shown in 4.3.
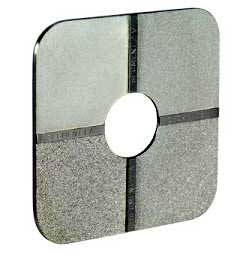
4. Pickling and descaling
4.1 In addition to the recommended rapid sandblasting or grinding of titanium surfaces, in order to ensure complete removal of metallic iron, oxides, scales, and other surface contamination, it should be pickled according to 4.3.2. If the product uses chemical milling to remove the surface oxide contamination layer and the product shape is not conducive to overall sand blasting, salt bath treatment can be used to avoid local corrosion on the surface.
4.2 For scales and lubricant residues formed in rolling, casting, forging, or assembly of titanium products.
It is usually treated by one of the following industrial methods to obtain a completely non-contaminating surface prior to final pickling according to 4.3.2.
4.2.1All corrosion-based solutions are mixed with tap water as recommended by the manufacturer.
4.2.2 The molten base salt bath is carried out at 399 to 454 ° C (750 to 850 ° F) according to the prescribed procedure.
4.2.3 The molten base salt bath is carried out at 204 ° C (400 ° F) according to the specified procedure.
4.2.4 The oxides and the colours produced by heating below 593 (1100) are usually cleaned by acid pickling. The acid liquid ratio (volume) is as follows: 10~20% (150~300g/L) nitric acid (70%)+1~2% (12~24g/L) hydrofluoric acid (60%)+water, 120°F (49°C)
4.2.5 Forged and hot-worked titanium alloys are usually mixed with graphite or glass lubricants to form hot scales, which can be completely dissolved in a base salt bath melted at 454 (850). In the follow-up treatment, some of them should be pickled by 4.3.2.
4.2.6 Heat treatable α+β and β alloys, and the treatment temperature is above 593 ° C (1100 ° F), resulting in a mixture of graphite and molybdenum disulfide lubricant residual hot scale. It is recommended to treat in a base bath of molten base at 204 ° C (400 ° F). The latter part should be pickled by the provisions of 4.3.2.
4.2.7 If the surface structure is a scale which is easy to remove, a suitable grinding method such as a wheel or belt mill, a sheet-like wheel for cutting, and grinding or shot peening can be employed.
4.3 After mechanical grinding or chemical treatment, the material can be further processed as described below to completely clean the surface.
4.3.1 After salt bath treatment and water cleaning, titanium and titanium alloy can be immersed in sulfuric acid solution to remove metamorphosed scales, and the acid used should be kept at 66 ° C (150 ° F). The concentration is: 10 to 40% by volume of sulfuric acid (95% by weight). The final finished surface whitening treatment can be completed by short-time soaking according to the acid solution specified in 4.3.2.
4.3.2 Materials that are mechanically ground according to 3.1 or chemically treated according to 4.2.1, 4.2.2, 4.2.3 may be cleaned and finished by immersion in an acid solution. The ratio of acid to liquid is: 10 to 30% by volume (150 to 450 g/L) of nitric acid (70%) + 1 to 3% by volume (12 to 36 g/L) of hydrofluoric acid (60%) at 49 ° C ( 120 ° F), maintaining a ratio of nitric acid to hydrofluoric acid of 10:1.
5. Operational precautions
5.1 When the titanium in the high temperature oxidized salt is cleaned, the workpiece is in contact with the iron-based material to generate an electric current. Titanium forms a positive or negative electrode with these iron-based materials to form an open circuit voltage of approximately 0.60V. The result of the release from the rack to the workpiece can cause the surface to overheat and may ignite. This effect can be reduced by maintaining a salt bath temperature not higher than 455 ° C (850 ° F) and using titanium fixtures or aluminium insulation between workpieces and fixtures.
5.2 For forgings or hot rolled materials with thicker scales, mechanical grinding can be used to remove excessive surface contamination before salt bath treatment.
5.3 In the process of hot forming or annealing of titanium alloys, silicon-based protective coating can reduce the formation of scales. All coatings should be removed prior to acid treatment.
5.4 Heat treated titanium forms a mixed surface contamination during fabrication or assembly, including graphite with titanium oxide or molybdenum disulfide, which should be cleaned with a molten salt bath. The treatment temperature should be 204 ° C (400 ° F) to avoid thermal deformation.
5.5 When treated in a salt bath or lye, the titanium oxide on the metal surface chemically reacts to form sodium titanate. They are soluble in acids containing sulfur and nitrogen-hydrogen fluoride. Sulfuric acid does not have any corrosive action on titanium or titanium alloy, and corrosion is suppressed by the addition of 0.25 to 1.0% of copper sulfate or ferric sulfate.
5.6 Most of the pickled salt-treated pickling is carried out in an acid solution containing sulfur and nitrogen-hydrogen fluoride. The material is circulated through the dissolved salts, water rinse, and sulfuric acid until all scales are completely removed. The final brightening treatment is done after a short cycle of soaking in the nitric acid and hydrofluoric acid baths.
5.7 In the nitric acid and hydrofluoric acid baths, the ratio of nitric acid to hydrofluoric acid is more important than the concentration of any of the acids. When the ratio is maintained at 10:1, the absorption of hydrogen during the pickling process is minimal.
5.8 In the production of titanium rolled products, the presence of an oxygen-rich layer on the exposed surface under high temperature or oxidizing atmosphere is unavoidable. When acid-washing with strong nitric acid and hydrofluoric acid solutions to remove the oxygen-rich layer and the alpha layer, it is very important that all residual oxides and scales should be completely removed to prevent preferential corrosion of the finished product.
5.9 Excess amounts of hydrogen can be removed by vacuum annealing the cleaned workpiece.
6. Inspection
6.1 Materials cleaned in accordance with this standard shall be visually inspected without significant paint, oil, grease, glass, graphite, lubricants, dirt, abrasives, iron, or other forms of contamination.
6.2 Operating in accordance with the procedures described, the hydrogen absorbed during the cleaning process should be kept to a minimum and within the allowable limits. Regular monitoring of the cleaning system should be carried out using samples of known hydrogen content and chemical analysis to complete the system. When the hydrogen content exceeds 20 ppm of the original product analysis result, the acid solution should be replaced or the acid component should be adjusted to reduce the degree of hydrogen absorption.
6.3 Product cleanliness can also be achieved by using a sample test piece. The test piece is preferably used in an amount of about 0.001 to 0.002 in. (0.025 to 0.05 mm) and is etched from both sides. After chemical corrosion, the surface of the sample should be even and smooth, bright, and free of protrusions and contamination caused by residual scales.