Discussion on Ultrasonic Testing Technology of Titanium Alloy Parts in Modern Titanium Industry
1.1 The basis and significance of ultrasonic testing for titanium alloy parts
Titanium and titanium alloys are widely used in aviation, aerospace, military, chemical, petroleum, metallurgical and other industries and play an irreplaceable role in various industries. This topic mainly discusses the ultrasonic testing of titanium and titanium alloys. Therefore, the importance of titanium alloy workpieces in modern industry, the necessity of ultrasonic testing of titanium alloy workpieces, and the importance of ultrasonic testing of titanium alloy workpieces for non-destructive testing skills training are studied.
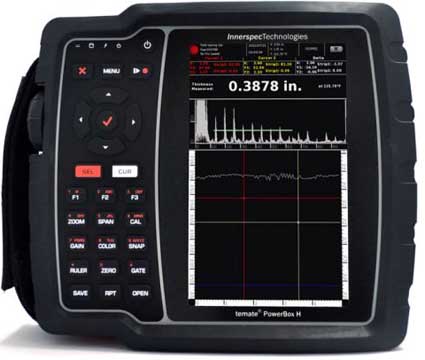
1.1.1 The importance of titanium alloy workpieces in modern industry
Titanium is an important metal material in modern industry. Titanium alloy has the advantages of high strength, corrosion resistance and heat resistance. Therefore, titanium alloy has been widely used in the industrial field of modern society.
In the aerospace industry, titanium and titanium alloy workpieces are used in the largest amount. Mainly used for aircraft, landing gear, main structures, rockets and missiles of aviation aircraft; Titanium alloys are also widely used in petroleum, metallurgy, chemical, electric power, nuclear industry and other fields. For example, steam turbine generators and blades used in power generation, etc. Oil pipelines and drilling platforms in the petroleum industry; engine valves, bearing blocks, connecting rods, etc. in the automotive industry; Nuclear waste storage tanks in the nuclear industry; In addition, titanium is also used in shipbuilding, offshore platforms, diving devices and so on.
It can be seen that titanium and titanium alloys have an irreplaceable important role in all fields of modern industry. Today, with the rapid development of science and technology, it is believed that the important role of titanium and its alloys will become more obvious. Therefore, studying the related properties of titanium and alloys is of great significance to the development of modern industry.
1.1.2 Necessity of Ultrasonic Testing of Titanium Alloy Workpieces
Alloys are widely used in various fields because of their various advantages, and in some special fields, the role of titanium alloys is irreplaceable. However, due to its own nature, it is very difficult to process titanium alloy workpieces, and the work is also quite difficult.
Titanium alloys may cause sticking or cutting difficulties due to their own hardness during cutting. In addition, titanium alloys also have cutting characteristics such as small deformation coefficient, high cutting temperature, large cutting force per unit area, severe chill phenomenon and severe tool wear: In addition, because the thermal conductivity of titanium alloy is very low, the tool life will be greatly shortened in milling.
It is precisely because of the poor processability of the machining and milling of titanium alloys. Therefore, it is particularly important to ensure the quality of the titanium alloy billet and reduce the scrap rate during the cutting process.
In addition, with the increasing use of titanium alloys, the increasingly harsh conditions of use of titanium alloy components and the increasing complexity of their structures, damage and failure of titanium alloys and their components are inevitable; There have been many catastrophic accidents caused by failures and breaks in titanium alloy parts.
Ultrasonic testing is an important means of quality control for nondestructive testing. Metallurgical defects (such as inclusions), process defects (such as overheating, insufficient deformation, cracks, etc.) and tissue defects that may exist in titanium alloy materials. Both the production plant and the aerospace plant use ultrasonic flaw detection for quality control. Through ultrasonic testing, unqualified raw blanks can be eliminated in time to prevent unqualified blanks from entering the processing process and reducing the workload in the production process. At the same time, ultrasonic testing can also detect in-service titanium alloy workpieces, and timely monitor the state of titanium alloy workpieces, thereby reducing the occurrence of catastrophic accidents caused by failure and fracture of titanium alloy workpieces.
1.2 Research status at home and abroad
Non-destructive testing technology has been developed for nearly a hundred years, and the quality of non-destructive testing technology is the specific performance of the country's industrial technology level. The economic benefits of non-destructive testing technology are obvious. German scientists believe that non-destructive testing technology is one of the four pillars of the machinery industry. Former US President Ronald Reagan once said: "Without advanced non-destructive testing technology, the United States cannot enjoy its leading position in many fields." It can be seen that modern industry is indeed based on non-destructive testing. All countries in the world have attached great importance to ultrasonic nondestructive testing.
With the development of non-destructive testing technology, non-destructive testing methods for titanium alloys have gradually increased. For example, TOFD (Time Of Flight Diffraction) ultrasonic diffraction time difference method, phased array ultrasound imaging detection method. All of them can accurately detect defects in titanium alloy workpieces, and even have the functions of automatic detection and imaging inspection. However, in China's current non-destructive testing level, taking into account the cost, timeliness, acceptance level and other aspects of non-destructive testing. At present, the most widely used non-destructive testing of titanium alloy workpieces is conventional pulse reflection ultrasonic testing. Therefore, the research on conventional ultrasonic testing of titanium alloys is still of great significance.
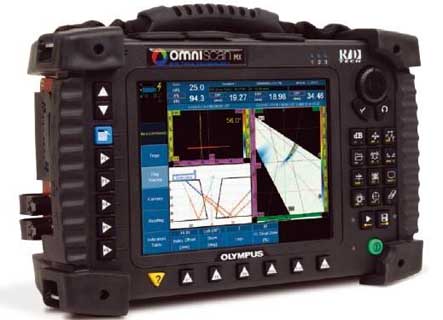
1.3 Brief Introduction of Standards for Titanium Alloy Ultrasound Testing
With the rapid development of the titanium industry and the increasing emphasis on the safety of modern industry in the country, the non-destructive testing technology for titanium and its alloy workpieces has also developed rapidly. Among them, ultrasonic testing is an efficient, fast, stable, reliable and non-polluting non-destructive testing technology, which is increasingly valued by various industrial testing departments. At the same time, various industries have established a number of standards and specifications for ultrasonic testing of titanium alloys. The following is a brief introduction to the domestic titanium alloy ultrasonic testing standards.
GB/T5193-2007 "Method for ultrasonic flaw detection of titanium and titanium alloy processed products": It is a national standard issued by the General Administration of Quality Supervision, Inspection and Quarantine of the People's Republic of China and the National Standardization Reform Commission for ultrasonic testing methods for general titanium and titanium alloy processed products.
GB/T12969.1-2007 "Method for ultrasonic flaw detection of titanium and titanium alloy pipes": The national standard for ultrasonic testing of titanium and titanium alloy pipes with external diameter of 6-80 mm and wall thickness of 0.5-4.5 mm was jointly issued by the General Administration of Quality Supervision, Inspection and Quarantine and the National Standardization Reform Commission.
HB/Z36-1982 "Instructions for Ultrasound Inspection of Wrought Titanium Alloy Bars": It was drafted by the Beijing Aeronautical Materials Research Institute (621), issued by the Ministry of Aviation Industry, and implemented on May 1, 1983, and is still used in the aviation industry standard for ultrasonic testing of deformed titanium alloy bars. Suitable for ultrasonic testing of diameter 16-60mm titanium alloy bars for the manufacture of aerospace engine compressor blades.
HB/Z37-1982 "Deformation of Titanium Alloy Park and Ultrasonic Inspection Instructions for Disc Parts": The guiding technical documents of the Ministry of Aviation Industry of the People's Republic of China are applicable to the ultrasonic testing of titanium alloy round cakes and discs for the manufacture of aerospace engine compressor discs.
HB5265-1983 "Instructions for Ultrasound Inspection of Combined (Ring) Blanks and Forgings for Aeroengine TC11 Titanium Alloy Compressor Disks": It is proposed by the Beijing Aeronautical Materials Research Institute (621), drafted by the TC11 titanium alloy disk and cake (ring) blank flaw detection standard drafting group, and issued by the Ministry of Aviation Industry. This standard is used together with HB/Z59-81 "Aeronautical Metal Materials and Parts Ultrasonic Longitudinal Wave Detection Instructions". It is also used in conjunction with HB5265-1983 "Acceptance Standard for Ultrasound Inspection of Titanium Alloy Compressor Disks and Forgings for Aeroengine TC11". This standard is mainly used to guide the ultrasonic testing of aero-engine turbojet 13 compressor TC11 titanium alloy disc and cake (ring) billet, and is also applicable to similar specifications of other models.
YB 950-80 "Special TC4 Titanium Alloy Forged Ultrasonic Flaw Detection Method": It is a metallurgical industry standard issued by the former Ministry of Metallurgy. The specific content involves confidential laws and regulations, so no specific standard content has been obtained.
GJB1580-2004 "Method for Ultrasonic Testing of Deformed Metals": It was proposed by China Aviation Industry First Group Corporation. China Aviation Integrated Technology Research Institute, Beijing Aeronautical Materials Research Institute, China Aviation Industry First Group Corporation Beijing Aeronautical Materials Research Institute, Aerospace 703, Aviation 430 Factory jointly drafted the national military standards. It is suitable for guiding ultrasonic inspection of forgings, forgings, rolled parts, plates, extruded or rolled bars, profiles, and parts machined from them.
JB/T4730-2005 "Non-destructive Testing of Pressure Equipment": It is an industry recommendation standard issued by the National Development and Reform Commission. It is used to guide the non-destructive testing and acceptance methods of pressure equipment. The standard is divided into 6 parts. The third part of the ultrasonic testing stipulates the ultrasonic testing method and quality grading requirements for the pressure-receiving equipment using the A-type pulse reflection ultrasonic testing equipment to detect the workpiece defects. This part is suitable for ultrasonic testing of raw materials, parts and joints for pressure-bearing equipment made of metal materials, as well as for ultrasonic testing of pressure-bearing equipment made of metal materials. Among them, the ultrasonic testing and quality grading of titanium and titanium alloy sheets are introduced in Section 4.3, which is used to guide the ultrasonic testing of titanium and titanium alloy pressure parts.
Titanium and titanium alloys are widely used in aviation, aerospace, military, chemical, petroleum, metallurgical and other industries and play an irreplaceable role in various industries. This topic mainly discusses the ultrasonic testing of titanium and titanium alloys. Therefore, the importance of titanium alloy workpieces in modern industry, the necessity of ultrasonic testing of titanium alloy workpieces, and the importance of ultrasonic testing of titanium alloy workpieces for non-destructive testing skills training are studied.
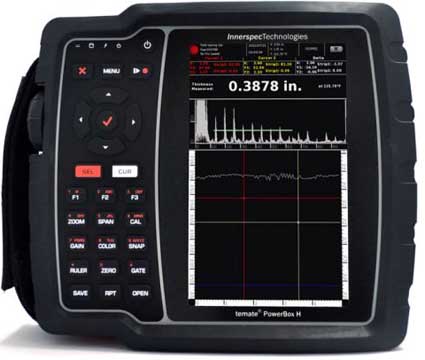
1.1.1 The importance of titanium alloy workpieces in modern industry
Titanium is an important metal material in modern industry. Titanium alloy has the advantages of high strength, corrosion resistance and heat resistance. Therefore, titanium alloy has been widely used in the industrial field of modern society.
In the aerospace industry, titanium and titanium alloy workpieces are used in the largest amount. Mainly used for aircraft, landing gear, main structures, rockets and missiles of aviation aircraft; Titanium alloys are also widely used in petroleum, metallurgy, chemical, electric power, nuclear industry and other fields. For example, steam turbine generators and blades used in power generation, etc. Oil pipelines and drilling platforms in the petroleum industry; engine valves, bearing blocks, connecting rods, etc. in the automotive industry; Nuclear waste storage tanks in the nuclear industry; In addition, titanium is also used in shipbuilding, offshore platforms, diving devices and so on.
It can be seen that titanium and titanium alloys have an irreplaceable important role in all fields of modern industry. Today, with the rapid development of science and technology, it is believed that the important role of titanium and its alloys will become more obvious. Therefore, studying the related properties of titanium and alloys is of great significance to the development of modern industry.
1.1.2 Necessity of Ultrasonic Testing of Titanium Alloy Workpieces
Alloys are widely used in various fields because of their various advantages, and in some special fields, the role of titanium alloys is irreplaceable. However, due to its own nature, it is very difficult to process titanium alloy workpieces, and the work is also quite difficult.
Titanium alloys may cause sticking or cutting difficulties due to their own hardness during cutting. In addition, titanium alloys also have cutting characteristics such as small deformation coefficient, high cutting temperature, large cutting force per unit area, severe chill phenomenon and severe tool wear: In addition, because the thermal conductivity of titanium alloy is very low, the tool life will be greatly shortened in milling.
It is precisely because of the poor processability of the machining and milling of titanium alloys. Therefore, it is particularly important to ensure the quality of the titanium alloy billet and reduce the scrap rate during the cutting process.
In addition, with the increasing use of titanium alloys, the increasingly harsh conditions of use of titanium alloy components and the increasing complexity of their structures, damage and failure of titanium alloys and their components are inevitable; There have been many catastrophic accidents caused by failures and breaks in titanium alloy parts.
Ultrasonic testing is an important means of quality control for nondestructive testing. Metallurgical defects (such as inclusions), process defects (such as overheating, insufficient deformation, cracks, etc.) and tissue defects that may exist in titanium alloy materials. Both the production plant and the aerospace plant use ultrasonic flaw detection for quality control. Through ultrasonic testing, unqualified raw blanks can be eliminated in time to prevent unqualified blanks from entering the processing process and reducing the workload in the production process. At the same time, ultrasonic testing can also detect in-service titanium alloy workpieces, and timely monitor the state of titanium alloy workpieces, thereby reducing the occurrence of catastrophic accidents caused by failure and fracture of titanium alloy workpieces.
1.2 Research status at home and abroad
Non-destructive testing technology has been developed for nearly a hundred years, and the quality of non-destructive testing technology is the specific performance of the country's industrial technology level. The economic benefits of non-destructive testing technology are obvious. German scientists believe that non-destructive testing technology is one of the four pillars of the machinery industry. Former US President Ronald Reagan once said: "Without advanced non-destructive testing technology, the United States cannot enjoy its leading position in many fields." It can be seen that modern industry is indeed based on non-destructive testing. All countries in the world have attached great importance to ultrasonic nondestructive testing.
With the development of non-destructive testing technology, non-destructive testing methods for titanium alloys have gradually increased. For example, TOFD (Time Of Flight Diffraction) ultrasonic diffraction time difference method, phased array ultrasound imaging detection method. All of them can accurately detect defects in titanium alloy workpieces, and even have the functions of automatic detection and imaging inspection. However, in China's current non-destructive testing level, taking into account the cost, timeliness, acceptance level and other aspects of non-destructive testing. At present, the most widely used non-destructive testing of titanium alloy workpieces is conventional pulse reflection ultrasonic testing. Therefore, the research on conventional ultrasonic testing of titanium alloys is still of great significance.
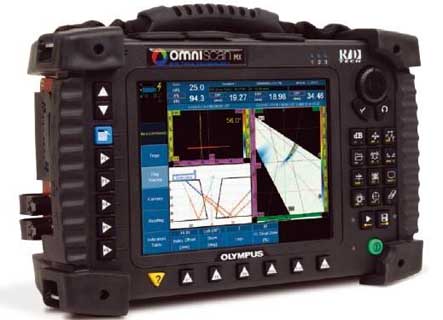
1.3 Brief Introduction of Standards for Titanium Alloy Ultrasound Testing
With the rapid development of the titanium industry and the increasing emphasis on the safety of modern industry in the country, the non-destructive testing technology for titanium and its alloy workpieces has also developed rapidly. Among them, ultrasonic testing is an efficient, fast, stable, reliable and non-polluting non-destructive testing technology, which is increasingly valued by various industrial testing departments. At the same time, various industries have established a number of standards and specifications for ultrasonic testing of titanium alloys. The following is a brief introduction to the domestic titanium alloy ultrasonic testing standards.
GB/T5193-2007 "Method for ultrasonic flaw detection of titanium and titanium alloy processed products": It is a national standard issued by the General Administration of Quality Supervision, Inspection and Quarantine of the People's Republic of China and the National Standardization Reform Commission for ultrasonic testing methods for general titanium and titanium alloy processed products.
GB/T12969.1-2007 "Method for ultrasonic flaw detection of titanium and titanium alloy pipes": The national standard for ultrasonic testing of titanium and titanium alloy pipes with external diameter of 6-80 mm and wall thickness of 0.5-4.5 mm was jointly issued by the General Administration of Quality Supervision, Inspection and Quarantine and the National Standardization Reform Commission.
HB/Z36-1982 "Instructions for Ultrasound Inspection of Wrought Titanium Alloy Bars": It was drafted by the Beijing Aeronautical Materials Research Institute (621), issued by the Ministry of Aviation Industry, and implemented on May 1, 1983, and is still used in the aviation industry standard for ultrasonic testing of deformed titanium alloy bars. Suitable for ultrasonic testing of diameter 16-60mm titanium alloy bars for the manufacture of aerospace engine compressor blades.
HB/Z37-1982 "Deformation of Titanium Alloy Park and Ultrasonic Inspection Instructions for Disc Parts": The guiding technical documents of the Ministry of Aviation Industry of the People's Republic of China are applicable to the ultrasonic testing of titanium alloy round cakes and discs for the manufacture of aerospace engine compressor discs.
HB5265-1983 "Instructions for Ultrasound Inspection of Combined (Ring) Blanks and Forgings for Aeroengine TC11 Titanium Alloy Compressor Disks": It is proposed by the Beijing Aeronautical Materials Research Institute (621), drafted by the TC11 titanium alloy disk and cake (ring) blank flaw detection standard drafting group, and issued by the Ministry of Aviation Industry. This standard is used together with HB/Z59-81 "Aeronautical Metal Materials and Parts Ultrasonic Longitudinal Wave Detection Instructions". It is also used in conjunction with HB5265-1983 "Acceptance Standard for Ultrasound Inspection of Titanium Alloy Compressor Disks and Forgings for Aeroengine TC11". This standard is mainly used to guide the ultrasonic testing of aero-engine turbojet 13 compressor TC11 titanium alloy disc and cake (ring) billet, and is also applicable to similar specifications of other models.
YB 950-80 "Special TC4 Titanium Alloy Forged Ultrasonic Flaw Detection Method": It is a metallurgical industry standard issued by the former Ministry of Metallurgy. The specific content involves confidential laws and regulations, so no specific standard content has been obtained.
GJB1580-2004 "Method for Ultrasonic Testing of Deformed Metals": It was proposed by China Aviation Industry First Group Corporation. China Aviation Integrated Technology Research Institute, Beijing Aeronautical Materials Research Institute, China Aviation Industry First Group Corporation Beijing Aeronautical Materials Research Institute, Aerospace 703, Aviation 430 Factory jointly drafted the national military standards. It is suitable for guiding ultrasonic inspection of forgings, forgings, rolled parts, plates, extruded or rolled bars, profiles, and parts machined from them.
JB/T4730-2005 "Non-destructive Testing of Pressure Equipment": It is an industry recommendation standard issued by the National Development and Reform Commission. It is used to guide the non-destructive testing and acceptance methods of pressure equipment. The standard is divided into 6 parts. The third part of the ultrasonic testing stipulates the ultrasonic testing method and quality grading requirements for the pressure-receiving equipment using the A-type pulse reflection ultrasonic testing equipment to detect the workpiece defects. This part is suitable for ultrasonic testing of raw materials, parts and joints for pressure-bearing equipment made of metal materials, as well as for ultrasonic testing of pressure-bearing equipment made of metal materials. Among them, the ultrasonic testing and quality grading of titanium and titanium alloy sheets are introduced in Section 4.3, which is used to guide the ultrasonic testing of titanium and titanium alloy pressure parts.