CNC Turning of Precision Reducer Output Shaft
A good reducer output shaft can not only provide efficiency, but also effectively reduce the occurrence of accidents, thereby achieving safe and efficient work. The structure of the output shaft of the reducer is relatively complex. It is a slender shaft type part with poor rigidity and requires very detailed processing steps. Below we will introduce the processing technology of the output shaft of the precision planetary reducer!
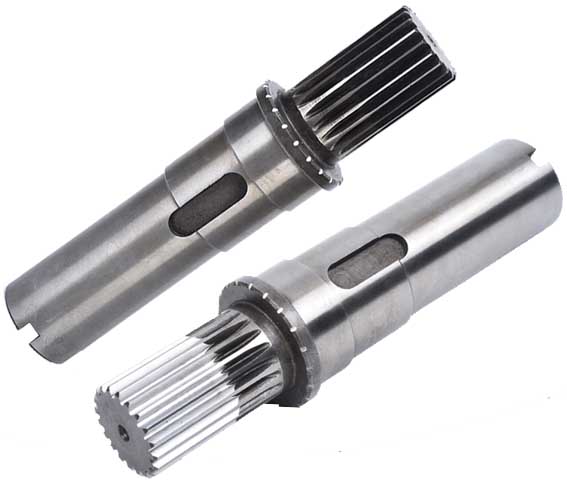
The structural design of the output shaft is an important step in determining the reasonable shape and complete structural size of the shaft. It is related to the type, size and location of the parts mounted on the shaft, the nature, direction, size and distribution of the loads, the type and size of the bearings, the blank of the shaft, and its manufacture. Relevant to the assembly process, installation and transportation. Designers can design according to the specific requirements of the shaft. If necessary, compare several options and choose the best design. The following are general shaft structure design principles:
1. Save materials, reduce weight, and try to use a cross-sectional shape with equal overall size and strength or a large cross-section coefficient;
2. The parts on the shaft are easy to accurately position, fix, assemble, disassemble and adjust;
3. Take various structural measures to reduce stress concentration and improve strength;
4. Facilitate processing technology manufacturing and ensure accuracy.
Processing technology of planetary reducer output shaft:
1. Wire cutting groove: The groove width is processed by precision grinding and wire cutting, and the groove width is tightened to E9 to ensure the accuracy of the drilling position. A special wire cutting tool is designed and manufactured, and the groove width is tightened to 4.25E9. After trial production, the pass rate of wire-cut groove width reached 99.8%, which can meet the requirements of mass production.
2. Drill mold drilling: The drill mold is positioned by fine grinding the outer circle, the key positioning of the plane direction groove and the drill mold, and two sets of drill molds are used to drill according to the slot width. In order to ensure processing accuracy, the structure of the drilling die body has been optimized.
3. Inspection: In order to ensure that customers can use it, we fully inspected the finished product and designed two sets of tooling to analyze and measure the relationship between the positions of the slots and holes.
The above is an introduction to the processing technology of the output shaft of precision planetary reducer.
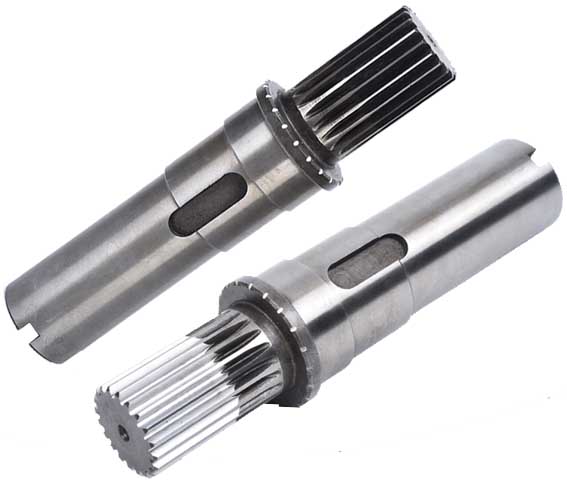
The structural design of the output shaft is an important step in determining the reasonable shape and complete structural size of the shaft. It is related to the type, size and location of the parts mounted on the shaft, the nature, direction, size and distribution of the loads, the type and size of the bearings, the blank of the shaft, and its manufacture. Relevant to the assembly process, installation and transportation. Designers can design according to the specific requirements of the shaft. If necessary, compare several options and choose the best design. The following are general shaft structure design principles:
1. Save materials, reduce weight, and try to use a cross-sectional shape with equal overall size and strength or a large cross-section coefficient;
2. The parts on the shaft are easy to accurately position, fix, assemble, disassemble and adjust;
3. Take various structural measures to reduce stress concentration and improve strength;
4. Facilitate processing technology manufacturing and ensure accuracy.
Processing technology of planetary reducer output shaft:
1. Wire cutting groove: The groove width is processed by precision grinding and wire cutting, and the groove width is tightened to E9 to ensure the accuracy of the drilling position. A special wire cutting tool is designed and manufactured, and the groove width is tightened to 4.25E9. After trial production, the pass rate of wire-cut groove width reached 99.8%, which can meet the requirements of mass production.
2. Drill mold drilling: The drill mold is positioned by fine grinding the outer circle, the key positioning of the plane direction groove and the drill mold, and two sets of drill molds are used to drill according to the slot width. In order to ensure processing accuracy, the structure of the drilling die body has been optimized.
3. Inspection: In order to ensure that customers can use it, we fully inspected the finished product and designed two sets of tooling to analyze and measure the relationship between the positions of the slots and holes.
The above is an introduction to the processing technology of the output shaft of precision planetary reducer.