CNC Machining of Helical Gear Bracket for Reducer
A steering drive axle helical gear planetary reduction structure. Among them, it includes: thrust bearing (18), spring (17), bell hub (1), planet carrier (27), thrust washer (28), helical gear ring carrier (26), needle roller (4 ), spacer (2), fixed traveler spring (6), adjusting pad (11), retaining ring (13), helical sun gear (21), helical planetary gear (3), helical internal tooth ring gear (5 ) and helical gear ring bracket (26).
The invention optimizes the spur gear planetary reducer mechanism, and can also be used to increase the steering function to the helical gear planetary reducer mechanism, effectively overcoming the axial force. At the same time, the axial force is effectively converted into rolling friction, which reduces power loss and increases the steering function of the helical gear planetary reduction mechanism of the drive axle.
By using the spiral bevel gear CNC gear milling machine, not only can bevel gears and hypoid gears be processed, but also cylindrical gears can be processed by eliminating the hob. This method is realized through the principle that the cutterhead rotates on one side and translates on the other side to form a shaped rack (media rack). To this end, the fixed rack coordinate system and the cutterhead fixed coordinate system are introduced. When the cutterhead rotates around the x-axis of the fixed coordinate system, a conical surface is formed; the helical cylindrical gear is the enveloping surface of the cone-shaped rack for translation and the cylindrical gear for rotation. At the same time, the cone surface equation of the cone, the helical gear meshing equation and the tooth surface equation of this method are derived.
The invention optimizes the spur gear planetary reducer mechanism, and can also be used to increase the steering function to the helical gear planetary reducer mechanism, effectively overcoming the axial force. At the same time, the axial force is effectively converted into rolling friction, which reduces power loss and increases the steering function of the helical gear planetary reduction mechanism of the drive axle.
By using the spiral bevel gear CNC gear milling machine, not only can bevel gears and hypoid gears be processed, but also cylindrical gears can be processed by eliminating the hob. This method is realized through the principle that the cutterhead rotates on one side and translates on the other side to form a shaped rack (media rack). To this end, the fixed rack coordinate system and the cutterhead fixed coordinate system are introduced. When the cutterhead rotates around the x-axis of the fixed coordinate system, a conical surface is formed; the helical cylindrical gear is the enveloping surface of the cone-shaped rack for translation and the cylindrical gear for rotation. At the same time, the cone surface equation of the cone, the helical gear meshing equation and the tooth surface equation of this method are derived.
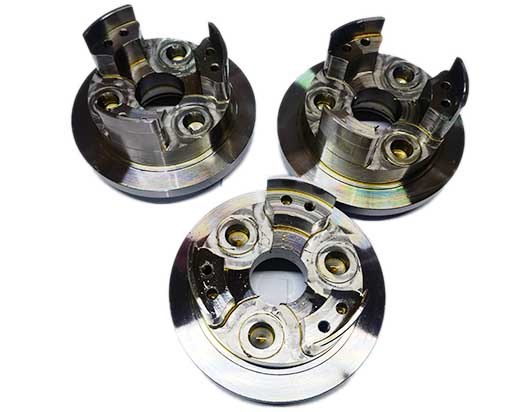