Turning and milling compound
What is Turning Milling Compound ?
Composite machining is currently one of the most popular processing technologies in the field of mechanical processing. It is an advanced manufacturing technology. Composite machining is the realization of several different machining processes on one machine tool. Composite machining
is the most widely used and the most difficult one is turning and milling. The turning and milling complex machining center is equivalent to the compounding of a CNC lathe and a machining center.
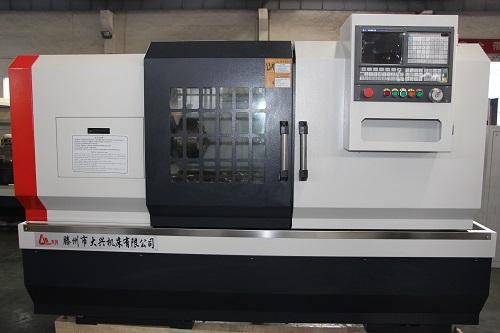
Definition
At present, most of the turning and milling processes are completed at the turning center. In general, turning centers only change the turret turret of CNC lathe to turret with power tools, and the spindle increases the function of C axis. Due to the limitation of the structure and size of the turret, the power of the power head is low, and the speed is not high, and it is not possible to install larger tools. Such a turning center is mainly based on turning, and the milling and drilling functions only perform some auxiliary processing. The high cost of the power tool holder has caused the cost of the turning center to remain high. The domestic price is generally over 100,000, and the imported one is over 200,000. The average user cannot afford it. Most of the economical turning and milling composites are XZC axes, which add a rotating C-axis to the chuck to achieve basic milling functions.
At present, there are many kinds of equipments in the turning and milling complex machining center on the market, such as WFL, DMG, Dalian Machine Tool, Taiwan Taichi Seiki Machine, DOOSAN (Doosan Machine Tool), and such high-end equipment; At present, the well-known software in the market for turning and milling is edgecam, UG NX and so on.
Advantage
Compared with conventional CNC machining processes, the outstanding advantages of composite machining are mainly manifested in the following aspects.
(1) Shorten product manufacturing process chain and increase production efficiency. Turn-milling compound machining can complete all or most of the machining operations at a time, which greatly shortens the product manufacturing process chain. In this way, on the one hand, the production assist time caused by the change of the installation card is reduced, and at the same time, the production equipment fixture manufacturing cycle and waiting time are also reduced, and the production efficiency can be significantly improved.
(2) Reduce the number of clamping and improve the machining precision.
The reduction of the number of clamps avoids the accumulation of errors due to the positioning reference conversion. At the same time, most of the current milling and milling machines have on-line inspection functions, which can realize in-situ detection and precision control of key data in the manufacturing process, thereby improving the machining accuracy of the products.
(3) Reduce the floor space and reduce the production cost.
Although the price of a single unit of turning and milling compound processing equipment is relatively high, the overall fixed assets can be effectively reduced due to the shortening of the manufacturing process chain and the reduction of equipment required for the product, as well as the reduction in the number of fixtures, floor space, and equipment maintenance costs. The costs of investment, production operations and management.
Features
1. Turn-milling machining center uses high-precision internal spindle;
2. Free mobile operation panel to improve work efficiency;
3. The main mass production of various models of small parts and high-speed machining complex parts, diversification and processing;
4. In particular, slim and complex processes can be processed at one time.
Configurable automatic feeding device to increase efficiency;
5. Material details: cutting, copper, iron, aluminum alloy, stainless steel, Teflon and other materials.
Composite machining is currently one of the most popular processing technologies in the field of mechanical processing. It is an advanced manufacturing technology. Composite machining is the realization of several different machining processes on one machine tool. Composite machining
is the most widely used and the most difficult one is turning and milling. The turning and milling complex machining center is equivalent to the compounding of a CNC lathe and a machining center.
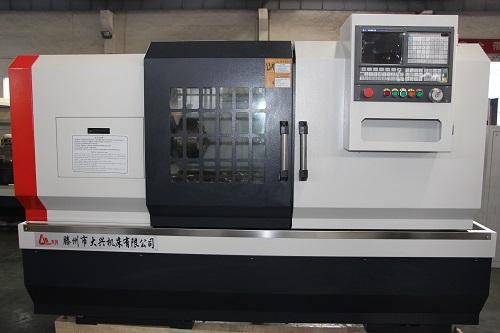
Definition
At present, most of the turning and milling processes are completed at the turning center. In general, turning centers only change the turret turret of CNC lathe to turret with power tools, and the spindle increases the function of C axis. Due to the limitation of the structure and size of the turret, the power of the power head is low, and the speed is not high, and it is not possible to install larger tools. Such a turning center is mainly based on turning, and the milling and drilling functions only perform some auxiliary processing. The high cost of the power tool holder has caused the cost of the turning center to remain high. The domestic price is generally over 100,000, and the imported one is over 200,000. The average user cannot afford it. Most of the economical turning and milling composites are XZC axes, which add a rotating C-axis to the chuck to achieve basic milling functions.
At present, there are many kinds of equipments in the turning and milling complex machining center on the market, such as WFL, DMG, Dalian Machine Tool, Taiwan Taichi Seiki Machine, DOOSAN (Doosan Machine Tool), and such high-end equipment; At present, the well-known software in the market for turning and milling is edgecam, UG NX and so on.
Advantage
Compared with conventional CNC machining processes, the outstanding advantages of composite machining are mainly manifested in the following aspects.
(1) Shorten product manufacturing process chain and increase production efficiency. Turn-milling compound machining can complete all or most of the machining operations at a time, which greatly shortens the product manufacturing process chain. In this way, on the one hand, the production assist time caused by the change of the installation card is reduced, and at the same time, the production equipment fixture manufacturing cycle and waiting time are also reduced, and the production efficiency can be significantly improved.
(2) Reduce the number of clamping and improve the machining precision.
The reduction of the number of clamps avoids the accumulation of errors due to the positioning reference conversion. At the same time, most of the current milling and milling machines have on-line inspection functions, which can realize in-situ detection and precision control of key data in the manufacturing process, thereby improving the machining accuracy of the products.
(3) Reduce the floor space and reduce the production cost.
Although the price of a single unit of turning and milling compound processing equipment is relatively high, the overall fixed assets can be effectively reduced due to the shortening of the manufacturing process chain and the reduction of equipment required for the product, as well as the reduction in the number of fixtures, floor space, and equipment maintenance costs. The costs of investment, production operations and management.
Features
1. Turn-milling machining center uses high-precision internal spindle;
2. Free mobile operation panel to improve work efficiency;
3. The main mass production of various models of small parts and high-speed machining complex parts, diversification and processing;
4. In particular, slim and complex processes can be processed at one time.
Configurable automatic feeding device to increase efficiency;
5. Material details: cutting, copper, iron, aluminum alloy, stainless steel, Teflon and other materials.
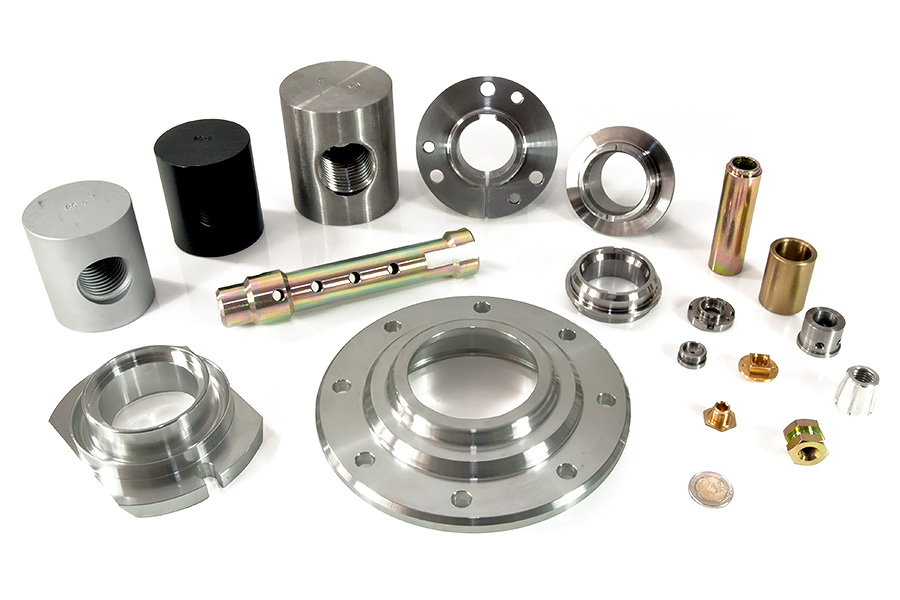