The Characteristics And Application Of CNC Machine Tools
1. The characteristics of CNC machine tools
CNC machine tools are a type of processing equipment that uses digital signals to control the movement of a machine tool and its machining process. The modern CNC machine tool is a typical processing equipment integrating light, machine, electricity and magnetic technology. CNC machining equipment is mainly divided into three major categories of cutting (grinding), pressure processing and special processing (such as EDM and wire cutting). The machining process of cutting-type CNC machine tools can be automatically performed according to a predetermined program, which eliminates man-made operation errors and achieves control accuracy that is difficult to achieve by manual operation. The machining accuracy can also be corrected and compensated by software. Therefore, it is possible to obtain higher machining accuracy and repeatability than the accuracy of the machine tool itself; After the workpieces are clamped one after another, they can be roughed and finished in succession. After the automatic tool changer is configured, the auxiliary machining time can be shortened and the productivity can be increased. Because the machine tool's trajectory is controlled by a programmable digital signal, single parts and small batches of parts with complex shapes can be processed, and the production preparation cycle is greatly shortened. In summary, CNC machine tools are characterized by high precision, high efficiency, high degree of automation, and good flexibility. From the current production status and development trend of CNC machine tools in recent years, due to the wide application of computer technology in the machine tool industry, compared with ordinary machine tools, not only great changes have taken place in the electrical control, but also in the mechanical structure performance Unique style and features. Specifically, it can be summarized as the following aspects:
(a) high precision machining.
(b) The quality of work is stable and reliable.
(c) high production efficiency.
(d) conducive to the modernization of production management.
(e) Low labor intensity and good working conditions.
(f) Good adaptability and flexibility.
(g) High technical requirements for use and maintenance.
(h) High degree of automation.
2. Processing range
According to the characteristics of numerical control processing, and a large number of application practices at home and abroad, CNC machine tools are usually most suitable for machining parts with the following characteristics.
(a) Multi-variety, low-volume production parts or rapid prototype samples. With the gradual decline in the cost of manufacturing CNC machine tools, now whether domestic or foreign, the processing of large quantities of parts has also emerged. When machining very small batches and single pieces of production, the debugging of the program and the preparation time of the tooling can be shortened.
(B) The shape is complex, the machining accuracy is high, and the size compensation can be conveniently performed. Parts that can not be machined by the general machine can be made.
(c) Parts with small surface roughness.
The surface roughness depends on the cutting speed and the feed rate in the case of a certain workpiece and tool material, finishing allowance and tool angle. Ordinary machine tool is a constant speed, different diameters of different cutting speeds, such as CNC lathes with constant line speed cutting function, turning the end surface, different diameters and outer circles can use the same linear speed, to ensure that the surface roughness value is both small and consistent. When processing surfaces with different surface roughness, small feedrates are used for surfaces with small roughness, large feedrates are used for surfaces with large roughness, and variability is very good, which is difficult to achieve on ordinary machine tools.
(d) Parts with complex contours. Any plane curve can be approximated by a straight line or an arc. CNC machine tools have circular interpolation functions and can process various complicated contour parts.
(e) It can process difficult-to-measure, difficult-to-control feed, difficult-to-control-size cavity housings, or box-type parts.
(f) Milling, boring, boring, reaming or tapping must be completed in one setup.
(g) The expensive parts are not allowed to be scrapped during processing.
(h) Urgently needed parts that require the shortest production cycle.
(i) When general-purpose machine tools are processed, they are vulnerable to human factors (such as emotional fluctuations, physical strength, and technical level), and the parts are of high value. Once the quality is out of control, it will cause major economic losses.
CNC machine tools are a type of processing equipment that uses digital signals to control the movement of a machine tool and its machining process. The modern CNC machine tool is a typical processing equipment integrating light, machine, electricity and magnetic technology. CNC machining equipment is mainly divided into three major categories of cutting (grinding), pressure processing and special processing (such as EDM and wire cutting). The machining process of cutting-type CNC machine tools can be automatically performed according to a predetermined program, which eliminates man-made operation errors and achieves control accuracy that is difficult to achieve by manual operation. The machining accuracy can also be corrected and compensated by software. Therefore, it is possible to obtain higher machining accuracy and repeatability than the accuracy of the machine tool itself; After the workpieces are clamped one after another, they can be roughed and finished in succession. After the automatic tool changer is configured, the auxiliary machining time can be shortened and the productivity can be increased. Because the machine tool's trajectory is controlled by a programmable digital signal, single parts and small batches of parts with complex shapes can be processed, and the production preparation cycle is greatly shortened. In summary, CNC machine tools are characterized by high precision, high efficiency, high degree of automation, and good flexibility. From the current production status and development trend of CNC machine tools in recent years, due to the wide application of computer technology in the machine tool industry, compared with ordinary machine tools, not only great changes have taken place in the electrical control, but also in the mechanical structure performance Unique style and features. Specifically, it can be summarized as the following aspects:
(a) high precision machining.
(b) The quality of work is stable and reliable.
(c) high production efficiency.
(d) conducive to the modernization of production management.
(e) Low labor intensity and good working conditions.
(f) Good adaptability and flexibility.
(g) High technical requirements for use and maintenance.
(h) High degree of automation.
2. Processing range
According to the characteristics of numerical control processing, and a large number of application practices at home and abroad, CNC machine tools are usually most suitable for machining parts with the following characteristics.
(a) Multi-variety, low-volume production parts or rapid prototype samples. With the gradual decline in the cost of manufacturing CNC machine tools, now whether domestic or foreign, the processing of large quantities of parts has also emerged. When machining very small batches and single pieces of production, the debugging of the program and the preparation time of the tooling can be shortened.
(B) The shape is complex, the machining accuracy is high, and the size compensation can be conveniently performed. Parts that can not be machined by the general machine can be made.
(c) Parts with small surface roughness.
The surface roughness depends on the cutting speed and the feed rate in the case of a certain workpiece and tool material, finishing allowance and tool angle. Ordinary machine tool is a constant speed, different diameters of different cutting speeds, such as CNC lathes with constant line speed cutting function, turning the end surface, different diameters and outer circles can use the same linear speed, to ensure that the surface roughness value is both small and consistent. When processing surfaces with different surface roughness, small feedrates are used for surfaces with small roughness, large feedrates are used for surfaces with large roughness, and variability is very good, which is difficult to achieve on ordinary machine tools.
(d) Parts with complex contours. Any plane curve can be approximated by a straight line or an arc. CNC machine tools have circular interpolation functions and can process various complicated contour parts.
(e) It can process difficult-to-measure, difficult-to-control feed, difficult-to-control-size cavity housings, or box-type parts.
(f) Milling, boring, boring, reaming or tapping must be completed in one setup.
(g) The expensive parts are not allowed to be scrapped during processing.
(h) Urgently needed parts that require the shortest production cycle.
(i) When general-purpose machine tools are processed, they are vulnerable to human factors (such as emotional fluctuations, physical strength, and technical level), and the parts are of high value. Once the quality is out of control, it will cause major economic losses.
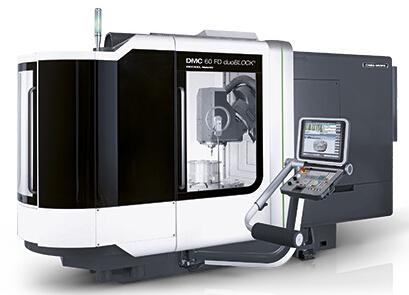