How To Choose The CNC Lathe Processing Tool Route?
CNC standards are a trend in the development of manufacturing informatization. In the 50 years after the CNC lathe machining CNC technology was born, information exchange was based on the ISO 6983 standard. That is, using the G and M codes to describe how to process, the essential feature is the processing-oriented process. Obviously, he has been unable to meet the needs of the rapid development of modern digital control technology.
For this purpose, a new CNC system standard ISO14649 (STEP-NC) is being researched and developed internationally. Its purpose is to provide a neutral mechanism that does not depend on specific systems. Ability to describe a unified data model throughout the product's lifecycle, In order to achieve the entire manufacturing process, and even the standardization of product information in various industrial fields.
How to choose the CNC lathe processing tool route?
The cutting path is the trajectory and direction of the tool relative to the workpiece during the index control machining process. The rational choice of processing routes is very important. Because it is closely related to the machining accuracy and surface quality of parts. The following points are mainly considered in determining the route of the knife:
1, to ensure the accuracy of parts processing requirements.
2, easy numerical calculation, reduce the programming workload.
3, seek the shortest processing route, reduce the empty knife time to improve processing efficiency.
4. Minimize Number of program segments.
5, to ensure the workpiece contour surface roughness requirements after processing, the final contour should be arranged for the last pass of continuous processing.
6, CNC lathe cutting tool advance and retreat knife (cut in and cut out) route should also be carefully considered to minimize the stop at the contour (abrupt changes in cutting force caused by elastic deformation) leaving a knife mark, It is also necessary to avoid vertical cutting on the contour surface and scratch the workpiece.
For this purpose, a new CNC system standard ISO14649 (STEP-NC) is being researched and developed internationally. Its purpose is to provide a neutral mechanism that does not depend on specific systems. Ability to describe a unified data model throughout the product's lifecycle, In order to achieve the entire manufacturing process, and even the standardization of product information in various industrial fields.
How to choose the CNC lathe processing tool route?
The cutting path is the trajectory and direction of the tool relative to the workpiece during the index control machining process. The rational choice of processing routes is very important. Because it is closely related to the machining accuracy and surface quality of parts. The following points are mainly considered in determining the route of the knife:
1, to ensure the accuracy of parts processing requirements.
2, easy numerical calculation, reduce the programming workload.
3, seek the shortest processing route, reduce the empty knife time to improve processing efficiency.
4. Minimize Number of program segments.
5, to ensure the workpiece contour surface roughness requirements after processing, the final contour should be arranged for the last pass of continuous processing.
6, CNC lathe cutting tool advance and retreat knife (cut in and cut out) route should also be carefully considered to minimize the stop at the contour (abrupt changes in cutting force caused by elastic deformation) leaving a knife mark, It is also necessary to avoid vertical cutting on the contour surface and scratch the workpiece.
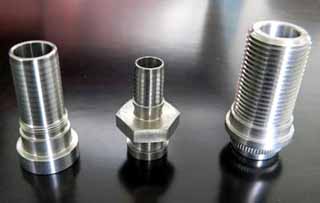