Surface Treatment of Titanium Screw, Fasteners of Different Colors
Introduction: Characteristics of titanium and titanium alloys, preparation before surface treatment. Surface treatment techniques such as chemical oxidation, anodization, micro-arc oxidation, electroless plating, electrodeposition, conversion film treatment, electrochemical processing, electrophoretic coating and nano-treatment. Surface film properties and application profiles, etc., combined with the application examples of titanium and titanium alloys are described in detail.
Surface treatment is the process of forming a coating on the surface of a workpiece by a certain method. The purpose is to give the titanium product a beautiful surface and anti-corrosion effect. The surface treatment methods are all based on the following methods:
1, Electroplating: The electroplated component is immersed in an aqueous solution containing the deposited metal compound, and an electric current is passed through the plating solution to deposit and deposit the electroplated metal on the component. Generally, electroplating includes: galvanizing, copper, nickel, chromium, copper-nickel alloy, etc., and sometimes black boiled (blue), phosphating, and the like are also included.
2, Hot dip galvanizing: This was accomplished by immersing the titanium member in a plating bath of molten zinc at a temperature of about 810 °C. As a result, the iron-zinc alloy on the surface of the titanium member gradually becomes passivated zinc on the outer surface of the product.
Hot dip aluminizing is a similar process.
3, Mechanical plating: The surface of the product is impacted by the particles of the plated metal and the coating is cold welded to the surface of the product.
4. Sandblasting: In general, white corundum is preferable for sand blasting treatment of titanium castings, and the pressure of sand blasting is smaller than that of non-precious metals, which is generally controlled below 0.45 Mpa. Because, when the injection pressure is too high, the sand particles impact the titanium surface to produce intense sparks, and the temperature rise can react with the titanium surface, resulting in secondary pollution and affecting the surface quality. The time is 15 to 30 seconds. Only the adhering sand, sintered layer and partial oxide layer on the surface of the castings can be removed. The remaining surface reaction layer structure should be quickly removed by chemical pickling.
5. Pickling: Acid pickling can quickly and completely remove the surface reaction layer, and the surface will not produce pollution of other elements. Both HF-HCl and HF-HNO3 acid pickling solutions can be used for pickling of titanium. However, HF-HCl acid pickling liquid has a large amount of hydrogen absorption, while HF-HNO3 acid pickling liquid has a small amount of hydrogen absorption. It can control the concentration of HNO3 to reduce hydrogen absorption and brighten the surface. Generally, the concentration of HF is about 3% to 5%, and the concentration of HNO3 is about 15% to 30%.
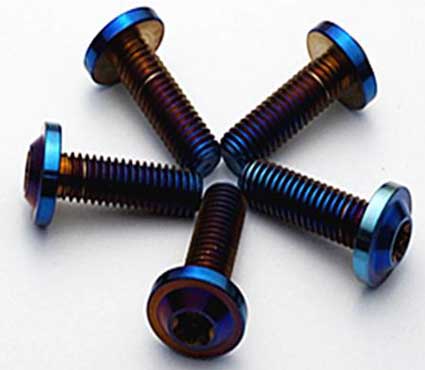
Second, titanium surface treatment quality control:
The quality of electroplating is mainly measured by its corrosion resistance, followed by appearance. Corrosion resistance is to imitate the working environment of the product, set as the test condition, and conduct corrosion test. The quality of electroplated products is controlled in the following ways:
1. Appearance:
The surface of titanium products is not allowed to have no local coating, burning, rough, gray, peeling, crust condition and obvious stripes. No pinhole pitting, black slag plating, loose passivation film, cracking, peeling off and serious passivation marks are allowed.
2, Plating Thickness: The working life of a fastener in a corrosive atmosphere is proportional to its coating thickness. Generally recommended economic plating thickness is 0.00015 in ~ 0.0005 in (4 ~ 12um).
Hot dip galvanizing: The standard average thickness is 54 um (the nominal diameter ≤ 3/8 is 43 um) and the minimum thickness is 43 um (the nominal diameter ≤ 3/8 is 37 um).
3. Plating distribution: With different deposition methods, the agglomeration mode of the coating on the fastener surface is also different. The plating metal is not uniformly deposited on the peripheral edge during plating, and a thicker coating is obtained at the corner. In the threaded portion of the fastener, the thickest coating is located on the crest of the thread, gradually thinning along the side of the thread, and depositing the thinnest at the base of the tooth. Hot dip galvanizing is just the opposite. Thicker coatings are deposited on the inner corners and the bottom of the threads. Mechanically plated plating metals tend to be deposited as hot dip coatings, but are smoother and much more uniform throughout the surface.
4, hydrogen embrittlement: During processing and handling of the fasteners, particularly during pickling and caustic washing prior to plating and subsequent plating, the surface absorbs hydrogen atoms and the deposited metal coating then captures hydrogen. When the fastener is tightened, hydrogen is transferred to the most concentrated portion of the stress, causing the pressure to increase beyond the strength of the base metal and causing minor surface cracking. Hydrogen is particularly active and quickly penetrates into newly formed fissures. This pressure-fracture-infiltration cycle continues until the fastener breaks. It usually occurs within hours of the first stress application.
In order to eliminate the threat of hydrogen embrittlement, the fasteners are heated and baked as quickly as possible after plating to allow hydrogen to ooze out of the coating. Baking is usually carried out at 375-4000 F (176-190 ° C) for 3-24 hours.
Since mechanical galvanizing is non-electrolytic, this virtually eliminates the threat of hydrogen embrittlement. In addition, due to engineering standards, fasteners with hardness higher than HRC35 (Inch Gr8, metric 10.9 or higher) are prohibited from hot dip galvanizing. Therefore, hot dip-plated fasteners rarely suffer from hydrogen embrittlement.
Surface treatment is the process of forming a coating on the surface of a workpiece by a certain method. The purpose is to give the titanium product a beautiful surface and anti-corrosion effect. The surface treatment methods are all based on the following methods:
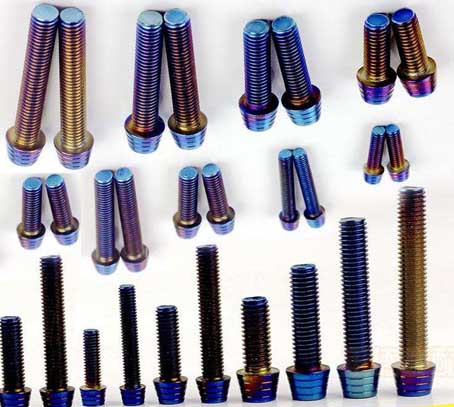
2, Hot dip galvanizing: This was accomplished by immersing the titanium member in a plating bath of molten zinc at a temperature of about 810 °C. As a result, the iron-zinc alloy on the surface of the titanium member gradually becomes passivated zinc on the outer surface of the product.
Hot dip aluminizing is a similar process.
3, Mechanical plating: The surface of the product is impacted by the particles of the plated metal and the coating is cold welded to the surface of the product.
4. Sandblasting: In general, white corundum is preferable for sand blasting treatment of titanium castings, and the pressure of sand blasting is smaller than that of non-precious metals, which is generally controlled below 0.45 Mpa. Because, when the injection pressure is too high, the sand particles impact the titanium surface to produce intense sparks, and the temperature rise can react with the titanium surface, resulting in secondary pollution and affecting the surface quality. The time is 15 to 30 seconds. Only the adhering sand, sintered layer and partial oxide layer on the surface of the castings can be removed. The remaining surface reaction layer structure should be quickly removed by chemical pickling.
5. Pickling: Acid pickling can quickly and completely remove the surface reaction layer, and the surface will not produce pollution of other elements. Both HF-HCl and HF-HNO3 acid pickling solutions can be used for pickling of titanium. However, HF-HCl acid pickling liquid has a large amount of hydrogen absorption, while HF-HNO3 acid pickling liquid has a small amount of hydrogen absorption. It can control the concentration of HNO3 to reduce hydrogen absorption and brighten the surface. Generally, the concentration of HF is about 3% to 5%, and the concentration of HNO3 is about 15% to 30%.
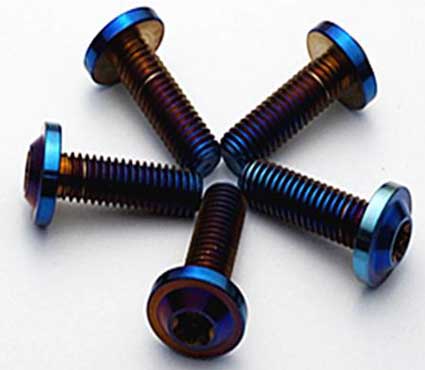
Second, titanium surface treatment quality control:
The quality of electroplating is mainly measured by its corrosion resistance, followed by appearance. Corrosion resistance is to imitate the working environment of the product, set as the test condition, and conduct corrosion test. The quality of electroplated products is controlled in the following ways:
1. Appearance:
The surface of titanium products is not allowed to have no local coating, burning, rough, gray, peeling, crust condition and obvious stripes. No pinhole pitting, black slag plating, loose passivation film, cracking, peeling off and serious passivation marks are allowed.
2, Plating Thickness: The working life of a fastener in a corrosive atmosphere is proportional to its coating thickness. Generally recommended economic plating thickness is 0.00015 in ~ 0.0005 in (4 ~ 12um).
Hot dip galvanizing: The standard average thickness is 54 um (the nominal diameter ≤ 3/8 is 43 um) and the minimum thickness is 43 um (the nominal diameter ≤ 3/8 is 37 um).
3. Plating distribution: With different deposition methods, the agglomeration mode of the coating on the fastener surface is also different. The plating metal is not uniformly deposited on the peripheral edge during plating, and a thicker coating is obtained at the corner. In the threaded portion of the fastener, the thickest coating is located on the crest of the thread, gradually thinning along the side of the thread, and depositing the thinnest at the base of the tooth. Hot dip galvanizing is just the opposite. Thicker coatings are deposited on the inner corners and the bottom of the threads. Mechanically plated plating metals tend to be deposited as hot dip coatings, but are smoother and much more uniform throughout the surface.
4, hydrogen embrittlement: During processing and handling of the fasteners, particularly during pickling and caustic washing prior to plating and subsequent plating, the surface absorbs hydrogen atoms and the deposited metal coating then captures hydrogen. When the fastener is tightened, hydrogen is transferred to the most concentrated portion of the stress, causing the pressure to increase beyond the strength of the base metal and causing minor surface cracking. Hydrogen is particularly active and quickly penetrates into newly formed fissures. This pressure-fracture-infiltration cycle continues until the fastener breaks. It usually occurs within hours of the first stress application.
In order to eliminate the threat of hydrogen embrittlement, the fasteners are heated and baked as quickly as possible after plating to allow hydrogen to ooze out of the coating. Baking is usually carried out at 375-4000 F (176-190 ° C) for 3-24 hours.
Since mechanical galvanizing is non-electrolytic, this virtually eliminates the threat of hydrogen embrittlement. In addition, due to engineering standards, fasteners with hardness higher than HRC35 (Inch Gr8, metric 10.9 or higher) are prohibited from hot dip galvanizing. Therefore, hot dip-plated fasteners rarely suffer from hydrogen embrittlement.