Milling of curved surface of titanium alloy blade by 5-axis machining center
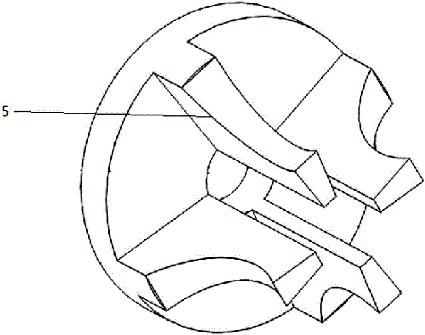
According to the overall technical idea of the curved surface of the blade, the milling of the curved surface of the blade should ensure that the geometrical position accuracy of the profile basically meets the design requirements. And it has a certain surface roughness quality, and the improvement of processing efficiency is also one of the key tasks of arc profile milling. According to the understanding of the processing characteristics of the large-scale titanium alloy fan blade arc profile, it is necessary to comprehensively consider the influence of various factors such as equipment, tool, and machining positioning.
For the milling of the curved surface of large titanium alloy fan blades, it is necessary to select a five-axis linkage machining center. The choice of a mature five-axis linkage blade machining center has both high-efficiency machining considerations and machining accuracy assurance capabilities. For the arc profile machining with large curvature change, the swing angle function of the machine tool spindle can well adapt to the requirement of the same cutting force corresponding to the curvature change of the arc profile. The high-pressure cooling system of the machine tool greatly reduces the cutting temperature and avoids the rapid wear of the tool, so that the arc surface processing can obtain good machining precision and surface processing quality.
One, Blade clamping method
In order to prevent and reduce the torsional deformation generated during long blade clamping and cutting, it is necessary to ensure that the rotary shaft of the front and rear end of the device has a synchronous rotation function. The purpose is to change the positioning and clamping method of one end clamping and one end tightening used in the traditional blade processing technology. It avoids the bending deformation caused by the blade clamping and the one-way rotation of the blade turning process, and the one end follows the torsional deformation of the blade curved surface in the longitudinal direction. In accordance with this requirement of the blade positioning and clamping, the auxiliary positioning portion of the blade tail end has strict positional accuracy requirements with respect to the front end positioning reference of the blade. After the roughing of the arc profile is completed, the positional accuracy error between the front and rear end positioning references of the blade due to stress deformation is to be repaired.
The blade arc surface machining jig is installed on the rotary axes of the front and rear of the machine, and it is determined that there is no concentricity error between the front and rear rotary axes of the machine. The special mandrel is used to detect and adjust the installation accuracy of the front and rear clamps, so as to ensure accurate positional accuracy relationship between the clamps at both ends. In order to avoid the synchronous rotation function of the front and rear rotary axes of the machine tool, additional torsional stress is generated due to the poor clamping accuracy of the clamp.
two, Rough milling of blade arc profile
two, Rough milling of blade arc profile
When milling a blade, the tool centerline is not perpendicular to the tangent of the point or face being milled, but at a certain angle to the normal of the point or face being milled in the direction of the pass. This type of milling uses a cylindrical end mill with a wider elliptical arc. Compared to the milling of the ball-end knives, the resulting tool path spacing is much larger for milling the same arc profile peak height or surface quality. Therefore, this processing has high processing efficiency. In actual machining, a rotary machining method in which the length of the blade moves from one end to the other end, that is, a spiral milling method is employed. From the perspective of efficiency, the spiral milling method also has higher processing efficiency than the longitudinal milling method.
Third, the curved blade surface finish milling
In order to obtain higher geometric and positional accuracy, the roughness level of the curved surface is required to meet certain requirements. In order to reduce the "rebound" effect of titanium alloy material processing and the influence of tool wear on machining accuracy during large-area arc profile machining, the tool must be sharp and avoid long-term machining of a tool. For this reason, if possible, use end mills for longitudinal milling of the curved faces. Longitudinal milling can use several tools to mill the back arc profile, the blade arc profile, the intake edge and the exhaust edge, avoiding the wear caused by a large area of the tool and the arc profile machining of the blade. The level of precision produces inconsistencies, which is conducive to the final finishing of the curved surface.
In the arc face milling of large titanium alloy fan rotor blades, all measures to avoid tool wear are necessary to improve the cutting conditions. In the selection of tool materials and specifications: Select the solid carbide coated cylindrical ball milling cutter to machine the inner side of the blade edge plate, the inner side of the edge plate and the arc-shaped surface transfer arc, the transitional arc profile near the edge plate, and the edge of the intake and exhaust. An end mill with a cylindrical carbide-coated blade is used to machine the large-area curved surface of the blade and the back of the blade. The choice of coating material for processing titanium alloy tools is very important, avoiding the use of coating materials that have affinity with titanium alloys. Currently, PVD coated tools are commonly used in the processing of titanium alloys. The PVD coatings are thin and smooth, and they adhere to the cemented carbide substrate while producing a residual stress. This kind of stress is beneficial to improve the anti-destructive performance of the tool. PVD can be closely attached to the tool, which is beneficial to maintain the sharp cutting edge shape. The PVD tool has good wear resistance, chemical stability and is not easy to produce built-up edge. In the process, use sufficient coolant to cool the tool and improve the friction effect, select reasonable cutting parameters, and improve the influence of cutting force.
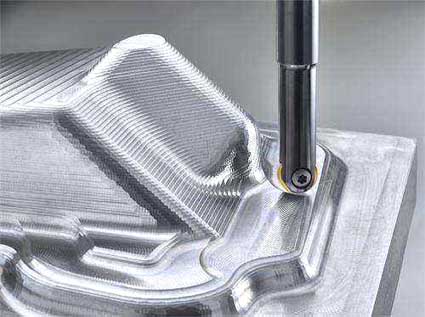