Manual TIG Welding Test of Precision Titanium Alloy Plate and Titanium Tube Parts
Titanium and titanium alloys are mostly welded by tungsten argon arc welding. Vacuum argon filling welding is also widely used. Under the protection and cooling of argon gas flow, the arc heat is concentrated, the current density is high, the heat affected zone is small, and the welding quality is high.
1. When welding titanium and titanium alloys, when the temperature is higher than 500 ° C ~ 700 ° C, it is easy to absorb air, hydrogen and nitrogen in the air, seriously affecting the welding quality. Therefore, when welding titanium and titanium alloys, the weld zone of the molten pool and high temperature (400 ° C ~ 650 ° C or more) must be strictly protected. For this reason, special protective measures must be taken when welding titanium and titanium alloys: That is, a welding torch with a larger spray size is used to enlarge the gas protection zone area. When the nozzle is insufficient to protect the high temperature metal in the weld and near the weld zone, the argon protective tow cover should be attached. The color of the weld and the near seam area is the target of the protective effect. Silver white indicates the best protection and yellow is slightly oxidized and is generally acceptable.
The surface color should meet the requirements of Table (1).
Considering the practicability and high efficiency of the project, we first prepared a simple tow hood. As shown in Figure (a)
Argon enters the distribution tube from the inlet and passes directly through the distribution tube hole into the protection zone. With this towing cover, the welding protection effect is not very good, and the weld bead is dark blue. According to the analysis, the airflow directly enters the protection zone from the distribution pipe. The airflow is not very uniform and stable, which makes the high temperature weld bead not well protected by oxidation. Therefore, we have further improved the structure of the tow hood.
Figure (b)
Argon enters the distribution pipe from the intake hole and returns down through the top of the towing hood. Through the porous plate, the porous plate mainly plays the role of gas sieve and distribution, making the argon flow more stable, the welding protection effect is better, and the weld bead is silver or yellow. The long cover L of the drag cover is 40~100mm and the material is brass.
When argon arc welding of titanium and titanium alloys, attention should also be paid to the north side protection of the weld bead. Considering the welding deformation, we use the method of slotting and fixing the copper pad to protect the argon. In order to fully protect the back of the weld bead, a porous copper pipe was added to the dregs to make argon enter the protection zone uniformly through the copper pipe hole. The protection effect is good, and the back of the weld bead is silver white.
Manual Tungsten Arc Welding Process and Parameter Selection:
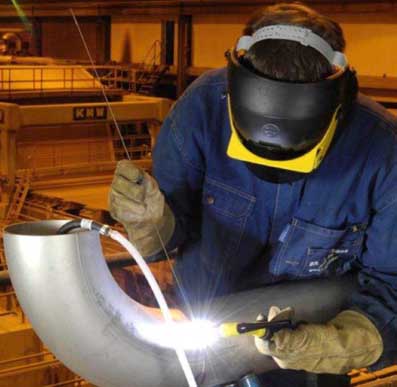
(1) Preparation before welding:
The quality of the weldment and wire surface has a great influence on the mechanical properties of the welded joint and must be strictly cleaned. Iron plate and titanium wire can be cleaned by mechanical cleaning and chemical cleaning.
1) Mechanically cleaned butt welds are not required to have high quality requirements or pickling. It can be wiped with fine sandpaper or stainless steel wire brush, but it is best to scrape the titanium plate with hard alloy yellow to remove the oxide film.
2) Chemical cleaning:
The test piece and the welding wire may be pickled before welding, and the acid washing liquid may be HF5%+HNO335% water melt. Rinse with clean water after pickling and weld immediately after drying. Or use acetone, ethanol, carbon tetrachloride, methanol, etc. to wipe the groove of titanium plate and its sides (within 50 mm each), welding wire surface, fixture and titanium plate contact parts.
(2) Selection of welding equipment:
Titanium and titanium alloy gold tungsten argon arc welding should use DC argon arc welding power source with reduced external characteristics and high frequency arc ignition, and delay the refueling time of not less than 15 seconds to avoid oxidation and pollution.
(3) Selection of welding materials:
The purity of argon should be no less than 99.99%, the dew point should be below -40 °C, and the total mass fraction of impurities & lt; 0.001%. When the pressure in the argon cylinder drops to 0.981 MPa, it should be stopped to prevent the quality of the welded joint from being affected. In principle, a titanium wire having the same basic metal composition should be selected, and sometimes a wire having a slightly lower strength than the base metal may be used in order to grip the weld metal of the weld metal. In principle, titanium wire with the same composition as the basic metal should be selected. Sometimes, in order to grasp the metal plasticity of the high weld, welding wire with slightly lower strength than the basic metal can be selected.
(4) Selection of groove form
The principle is to minimize the number of weld layers and weld metal. As the number of welded layers increases, the cumulative inspiratory amount of the weld increases, which affects the performance of the welded joint. Moreover, since the size of the weld pool is large when the titanium and the titanium alloy are welded, the test piece is opened with a V-shaped 70-80° groove.
(5) Test piece pairing and positioning welding:
In order to reduce the welding deformation, the positioning welding is performed before welding. The general positioning welding pitch is 100~150mm and the length is 10~15 mm. The welding wire, welding process parameters and gas protection conditions for tack welding shall be the same as those for welding joints. The gap is 0~2mm, and the blunt edge is 0~1.0mm.
(6) Welding parameter selection
We have explored the appropriate welding procedure specifications by comparing the performance of welded joints under different processes.
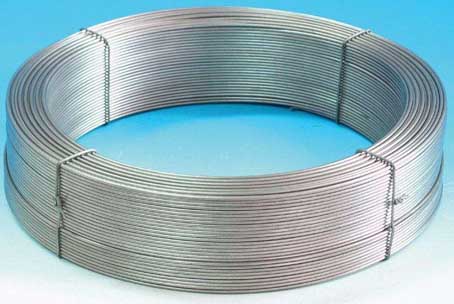
Process (1):
The welding current is 150A, 170A, 180A. According to this parameter, the surface of the welded joint is dark blue and gold-colored, which indicates that the joint oxidation is serious and does not meet the technical requirements. This process is not desirable.
Technology (2):
The welding current is reduced to 120A, 150A and 160A. According to this parameter, the weld surface presents golden purple and deep yellow, X-ray inspection has no defects, but the bending test of mechanical properties is not qualified. The results show that the plasticity of welded joints decreases significantly, which can not meet the technical requirements, and this process is also undesirable.
Technology (3)
Welding current is 95A, 115A and 120A. According to this parameter, the surface of the weld is silver-white and light yellow, and there is no defect in X-ray inspection. However, the bending test of mechanical properties is qualified, the tensile strength also meets the requirements, and the performance of welded joints meets the technical requirements. This process is more suitable.
When titanium and titanium alloys are welded, there is a tendency of coarse grains, which directly affects the mechanical properties of welded joints. Therefore, the selection of welding parameters should not only take into account the oxidation of weld metal and the formation of gas holes, but also consider the factors of grain coarsening, so the smaller welding heat input should be adopted as far as possible. Process (1), (2), due to the larger welding specification, the joint oxidation is more serious than the process (3). And the results of microscopic metallographic experiments show that the degree of grain coarsening of joints is also more serious than that of process (3). Therefore, the mechanical properties of welded joints are poor.
The choice of gas flow rate is based on good protection. Excessive flow rate is not easy to form a stable laminar flow, and the cooling rate of the weld is increased, so that the α phase of the weld surface layer is more likely to cause microcracks. When the argon flow in the towing hood is insufficient, the welds show different oxidation colors. When the flow rate is too large, it will interfere with the air flow of the main nozzle. The flow rate of argon gas on the back of the weld should not be too large, otherwise it will affect the gas protection effect of the first layer weld on the front side.
(7) Manipulation of manual tungsten argon arc welding of titanium and titanium alloy
1) When manual argon arc welding, the minimum angle (10~15°) should be kept between the welding wire and the weldment. The welding wire is smoothly and evenly fed into the molten pool along the front end of the molten pool, and the end of the welding wire must not be removed from the argon protection zone.
2) When welding, the welding torch basically does not swing laterally. When it needs to swing, the frequency should be low, and the swing amplitude should not be too large to prevent the protection of argon gas.
3) When the arc is broken and the weld is finished, the argon gas protection should be continued until the metal in the weld and heat affected zone is cooled to below 350 °C.
(8) Quality inspection 1) Appearance inspection conforms to GB/T13149-91. 2) Radiation deep injury conforms to JB4730-94. 3) Mechanical performance test conforms to GB/T13149-91.
1. When welding titanium and titanium alloys, when the temperature is higher than 500 ° C ~ 700 ° C, it is easy to absorb air, hydrogen and nitrogen in the air, seriously affecting the welding quality. Therefore, when welding titanium and titanium alloys, the weld zone of the molten pool and high temperature (400 ° C ~ 650 ° C or more) must be strictly protected. For this reason, special protective measures must be taken when welding titanium and titanium alloys: That is, a welding torch with a larger spray size is used to enlarge the gas protection zone area. When the nozzle is insufficient to protect the high temperature metal in the weld and near the weld zone, the argon protective tow cover should be attached. The color of the weld and the near seam area is the target of the protective effect. Silver white indicates the best protection and yellow is slightly oxidized and is generally acceptable.
The surface color should meet the requirements of Table (1).
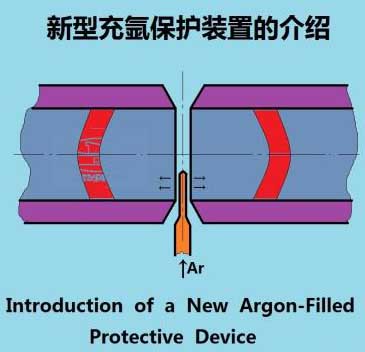
Considering the practicability and high efficiency of the project, we first prepared a simple tow hood. As shown in Figure (a)
Argon enters the distribution tube from the inlet and passes directly through the distribution tube hole into the protection zone. With this towing cover, the welding protection effect is not very good, and the weld bead is dark blue. According to the analysis, the airflow directly enters the protection zone from the distribution pipe. The airflow is not very uniform and stable, which makes the high temperature weld bead not well protected by oxidation. Therefore, we have further improved the structure of the tow hood.
Figure (b)
Argon enters the distribution pipe from the intake hole and returns down through the top of the towing hood. Through the porous plate, the porous plate mainly plays the role of gas sieve and distribution, making the argon flow more stable, the welding protection effect is better, and the weld bead is silver or yellow. The long cover L of the drag cover is 40~100mm and the material is brass.
When argon arc welding of titanium and titanium alloys, attention should also be paid to the north side protection of the weld bead. Considering the welding deformation, we use the method of slotting and fixing the copper pad to protect the argon. In order to fully protect the back of the weld bead, a porous copper pipe was added to the dregs to make argon enter the protection zone uniformly through the copper pipe hole. The protection effect is good, and the back of the weld bead is silver white.
Manual Tungsten Arc Welding Process and Parameter Selection:
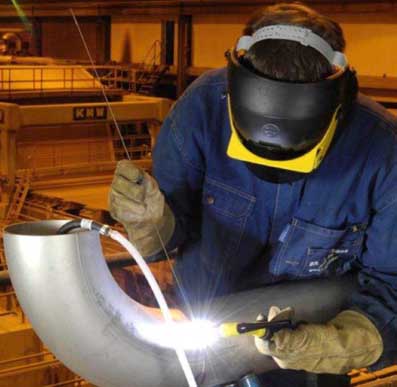
(1) Preparation before welding:
The quality of the weldment and wire surface has a great influence on the mechanical properties of the welded joint and must be strictly cleaned. Iron plate and titanium wire can be cleaned by mechanical cleaning and chemical cleaning.
1) Mechanically cleaned butt welds are not required to have high quality requirements or pickling. It can be wiped with fine sandpaper or stainless steel wire brush, but it is best to scrape the titanium plate with hard alloy yellow to remove the oxide film.
2) Chemical cleaning:
The test piece and the welding wire may be pickled before welding, and the acid washing liquid may be HF5%+HNO335% water melt. Rinse with clean water after pickling and weld immediately after drying. Or use acetone, ethanol, carbon tetrachloride, methanol, etc. to wipe the groove of titanium plate and its sides (within 50 mm each), welding wire surface, fixture and titanium plate contact parts.
(2) Selection of welding equipment:
Titanium and titanium alloy gold tungsten argon arc welding should use DC argon arc welding power source with reduced external characteristics and high frequency arc ignition, and delay the refueling time of not less than 15 seconds to avoid oxidation and pollution.
(3) Selection of welding materials:
The purity of argon should be no less than 99.99%, the dew point should be below -40 °C, and the total mass fraction of impurities & lt; 0.001%. When the pressure in the argon cylinder drops to 0.981 MPa, it should be stopped to prevent the quality of the welded joint from being affected. In principle, a titanium wire having the same basic metal composition should be selected, and sometimes a wire having a slightly lower strength than the base metal may be used in order to grip the weld metal of the weld metal. In principle, titanium wire with the same composition as the basic metal should be selected. Sometimes, in order to grasp the metal plasticity of the high weld, welding wire with slightly lower strength than the basic metal can be selected.
(4) Selection of groove form
The principle is to minimize the number of weld layers and weld metal. As the number of welded layers increases, the cumulative inspiratory amount of the weld increases, which affects the performance of the welded joint. Moreover, since the size of the weld pool is large when the titanium and the titanium alloy are welded, the test piece is opened with a V-shaped 70-80° groove.
(5) Test piece pairing and positioning welding:
In order to reduce the welding deformation, the positioning welding is performed before welding. The general positioning welding pitch is 100~150mm and the length is 10~15 mm. The welding wire, welding process parameters and gas protection conditions for tack welding shall be the same as those for welding joints. The gap is 0~2mm, and the blunt edge is 0~1.0mm.
(6) Welding parameter selection
We have explored the appropriate welding procedure specifications by comparing the performance of welded joints under different processes.
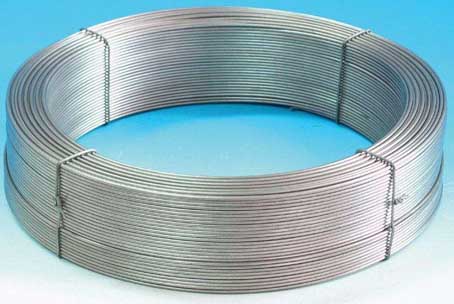
Process (1):
The welding current is 150A, 170A, 180A. According to this parameter, the surface of the welded joint is dark blue and gold-colored, which indicates that the joint oxidation is serious and does not meet the technical requirements. This process is not desirable.
Technology (2):
The welding current is reduced to 120A, 150A and 160A. According to this parameter, the weld surface presents golden purple and deep yellow, X-ray inspection has no defects, but the bending test of mechanical properties is not qualified. The results show that the plasticity of welded joints decreases significantly, which can not meet the technical requirements, and this process is also undesirable.
Technology (3)
Welding current is 95A, 115A and 120A. According to this parameter, the surface of the weld is silver-white and light yellow, and there is no defect in X-ray inspection. However, the bending test of mechanical properties is qualified, the tensile strength also meets the requirements, and the performance of welded joints meets the technical requirements. This process is more suitable.
When titanium and titanium alloys are welded, there is a tendency of coarse grains, which directly affects the mechanical properties of welded joints. Therefore, the selection of welding parameters should not only take into account the oxidation of weld metal and the formation of gas holes, but also consider the factors of grain coarsening, so the smaller welding heat input should be adopted as far as possible. Process (1), (2), due to the larger welding specification, the joint oxidation is more serious than the process (3). And the results of microscopic metallographic experiments show that the degree of grain coarsening of joints is also more serious than that of process (3). Therefore, the mechanical properties of welded joints are poor.
The choice of gas flow rate is based on good protection. Excessive flow rate is not easy to form a stable laminar flow, and the cooling rate of the weld is increased, so that the α phase of the weld surface layer is more likely to cause microcracks. When the argon flow in the towing hood is insufficient, the welds show different oxidation colors. When the flow rate is too large, it will interfere with the air flow of the main nozzle. The flow rate of argon gas on the back of the weld should not be too large, otherwise it will affect the gas protection effect of the first layer weld on the front side.
(7) Manipulation of manual tungsten argon arc welding of titanium and titanium alloy
1) When manual argon arc welding, the minimum angle (10~15°) should be kept between the welding wire and the weldment. The welding wire is smoothly and evenly fed into the molten pool along the front end of the molten pool, and the end of the welding wire must not be removed from the argon protection zone.
2) When welding, the welding torch basically does not swing laterally. When it needs to swing, the frequency should be low, and the swing amplitude should not be too large to prevent the protection of argon gas.
3) When the arc is broken and the weld is finished, the argon gas protection should be continued until the metal in the weld and heat affected zone is cooled to below 350 °C.
(8) Quality inspection 1) Appearance inspection conforms to GB/T13149-91. 2) Radiation deep injury conforms to JB4730-94. 3) Mechanical performance test conforms to GB/T13149-91.