How to Accuracy Requirement of Titanium Alloy Parts Processed by Lathe to Achieve the Processing Standard of Grinding Machine
Through careful study of the drawings of high-precision titanium alloy parts, the processing plan and process parameters were determined. Using the existing ordinary lathe equipment, the processing of the parts was completed smoothly and completed on the lathe processing, realizing the accuracy requirements that only the grinding machine can achieve.
1. Processing difficulties analysis
There are a number of TC4 titanium alloy precision parts coming to the military industry. This task is a new challenge in terms of processing materials and processing precision. The processing of convex lens rotating axis (see Fig. 1) has the following problems:
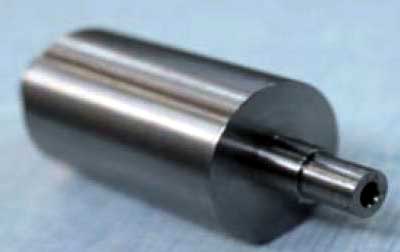
Fig 1. Rotating axis of TC4 titanium alloy precision convex lens
(1) The convex lens rotating shaft is made of a titanium alloy material. Due to its high strength and high hardness, it is easy to produce a surface hardened layer during processing, and the material has a small thermal conductivity and a small elastic modulus. The amount of springback of the machined surface during cutting is large, causing severe friction, adhesion and bond wear on the flank of the tool.
(2) While ensuring the accuracy of the shape processing, the coaxiality of the two ends of the part requires 0.006mm, which is almost impossible to achieve for existing machine tools. Because the existing machine tool has a spindle jump of >0.01mm after starting, it is easy to know the difficulty of completing the machining task on such a machine.
(3) The dimensional accuracy of the part shape and the hole are very high, 0.005 mm and 0.01 mm, respectively, and the surface roughness value Ra = 0.8 μm is required. Under normal circumstances, it needs to be processed on the grinding machine to achieve the pattern requirements. Because there is no grinding machine in the factory for precision processing, the task must be completed by lathe. Before processing, the drawings are carefully studied and various processing schemes are analyzed. Finally, the following methods are adopted to process the drawings.
2. Selection of process parameters
According to the characteristics of titanium alloy materials, the cutting tool materials with high strength, good wear resistance and YW series are selected for processing.
(1) Tool parameters:
Use a positive and negative outer-circular knives with a 90° lead angle and a horizontal groove cutter. While ensuring the cutting strength of the tool, in order to reduce the cutting resistance and prevent the material from overheating during the cutting process, the tool rake angle is selected to be 20° to 25°. In order to avoid sharp friction and adhesion of the flank of the tool to the surface of the part during the cutting process, the tool back angle is selected from 5° to 8°.
(2) Cutting parameters: Due to the low thermal conductivity and small modulus of elasticity of titanium alloy materials, bonding is easy during processing. Therefore, the cutting parameter value is not easy to set too large during machining, and the spindle speed is selected to be 350-500r/min, which should not be too high. The choice of cutting depth and feed is larger when turning roughly and choose a smaller finish turning.
3. Processing method
(1) Rough turning: First, use the horizontal groove cutter to rough the outer ends of the parts (see Figure 2), leaving a margin of 0.5mm on one side. Because of the small resistance and easy chip breaking in the cutting process of the transverse groove turning tool, it is better to use the transverse groove turning tool for rough turning of Figure 1 at both ends. However, since the titanium alloy material is extremely susceptible to thermal deformation during processing, it is necessary to use a cutting fluid for sufficient cooling during the cutting process.
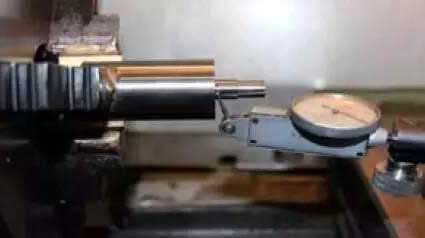
Figure 2. The coaxiality of the two ends of the titanium alloy parts is 0.006mm
(2) Half finished turning: After the parts have been completely cooled, use the 90° outer circular knife to drive out the reference outer circle of the part. After the parts are completely cooled, the benchmark cylindrical turning of the parts is carried out with a 90° cylindrical deflector. The shape of the part is clamped by the soft claw, and the shape of the part is corrected by the micrometer lever meter (see figure 3). Make the circle run to within 0.005mm and machine the part at one end. Can not be processed in one position, leaving a margin of 0.1 to 0.2mm on one side.

figure 3. High-precision titanium alloy parts China supplier
3) Finish turning:
① After excision of spare parts, drilling and boring are carried out to ensure the size and accuracy requirements.
Correct the shape of the part again to ensure that the dimensional accuracy is within 0.005mm, and the finished shape of the finished car is 0.05mm. Since the double top is positioned with the inner holes at both ends, and the shape margin of the parts before finishing is small (0.05 mm). Therefore, the drilling and boring and finishing of the car are completed in one clamping and correcting, and the hole chamfering is completed to prepare for the next double top process.
② When turning on a lathe, the parts are passed through the double-top method. The surface roughness Ra=0.8um is achieved by using the positive and negative deflection cutter to finish turning and polishing the shape of the parts.
4. Conclusion
With this processing method, the machining of the parts was completed smoothly. Through inspection, the dimensional accuracy and shape tolerance of the parts meet the requirements of the design drawings.
1. Processing difficulties analysis
There are a number of TC4 titanium alloy precision parts coming to the military industry. This task is a new challenge in terms of processing materials and processing precision. The processing of convex lens rotating axis (see Fig. 1) has the following problems:
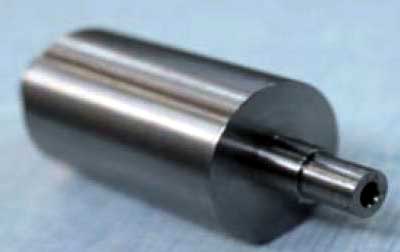
Fig 1. Rotating axis of TC4 titanium alloy precision convex lens
(1) The convex lens rotating shaft is made of a titanium alloy material. Due to its high strength and high hardness, it is easy to produce a surface hardened layer during processing, and the material has a small thermal conductivity and a small elastic modulus. The amount of springback of the machined surface during cutting is large, causing severe friction, adhesion and bond wear on the flank of the tool.
(2) While ensuring the accuracy of the shape processing, the coaxiality of the two ends of the part requires 0.006mm, which is almost impossible to achieve for existing machine tools. Because the existing machine tool has a spindle jump of >0.01mm after starting, it is easy to know the difficulty of completing the machining task on such a machine.
(3) The dimensional accuracy of the part shape and the hole are very high, 0.005 mm and 0.01 mm, respectively, and the surface roughness value Ra = 0.8 μm is required. Under normal circumstances, it needs to be processed on the grinding machine to achieve the pattern requirements. Because there is no grinding machine in the factory for precision processing, the task must be completed by lathe. Before processing, the drawings are carefully studied and various processing schemes are analyzed. Finally, the following methods are adopted to process the drawings.
2. Selection of process parameters
According to the characteristics of titanium alloy materials, the cutting tool materials with high strength, good wear resistance and YW series are selected for processing.
(1) Tool parameters:
Use a positive and negative outer-circular knives with a 90° lead angle and a horizontal groove cutter. While ensuring the cutting strength of the tool, in order to reduce the cutting resistance and prevent the material from overheating during the cutting process, the tool rake angle is selected to be 20° to 25°. In order to avoid sharp friction and adhesion of the flank of the tool to the surface of the part during the cutting process, the tool back angle is selected from 5° to 8°.
(2) Cutting parameters: Due to the low thermal conductivity and small modulus of elasticity of titanium alloy materials, bonding is easy during processing. Therefore, the cutting parameter value is not easy to set too large during machining, and the spindle speed is selected to be 350-500r/min, which should not be too high. The choice of cutting depth and feed is larger when turning roughly and choose a smaller finish turning.
3. Processing method
(1) Rough turning: First, use the horizontal groove cutter to rough the outer ends of the parts (see Figure 2), leaving a margin of 0.5mm on one side. Because of the small resistance and easy chip breaking in the cutting process of the transverse groove turning tool, it is better to use the transverse groove turning tool for rough turning of Figure 1 at both ends. However, since the titanium alloy material is extremely susceptible to thermal deformation during processing, it is necessary to use a cutting fluid for sufficient cooling during the cutting process.
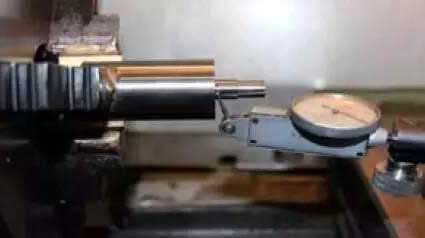
Figure 2. The coaxiality of the two ends of the titanium alloy parts is 0.006mm
(2) Half finished turning: After the parts have been completely cooled, use the 90° outer circular knife to drive out the reference outer circle of the part. After the parts are completely cooled, the benchmark cylindrical turning of the parts is carried out with a 90° cylindrical deflector. The shape of the part is clamped by the soft claw, and the shape of the part is corrected by the micrometer lever meter (see figure 3). Make the circle run to within 0.005mm and machine the part at one end. Can not be processed in one position, leaving a margin of 0.1 to 0.2mm on one side.

figure 3. High-precision titanium alloy parts China supplier
3) Finish turning:
① After excision of spare parts, drilling and boring are carried out to ensure the size and accuracy requirements.
Correct the shape of the part again to ensure that the dimensional accuracy is within 0.005mm, and the finished shape of the finished car is 0.05mm. Since the double top is positioned with the inner holes at both ends, and the shape margin of the parts before finishing is small (0.05 mm). Therefore, the drilling and boring and finishing of the car are completed in one clamping and correcting, and the hole chamfering is completed to prepare for the next double top process.
② When turning on a lathe, the parts are passed through the double-top method. The surface roughness Ra=0.8um is achieved by using the positive and negative deflection cutter to finish turning and polishing the shape of the parts.
4. Conclusion
With this processing method, the machining of the parts was completed smoothly. Through inspection, the dimensional accuracy and shape tolerance of the parts meet the requirements of the design drawings.