Welche Bearbeitungsgenauigkeit von Prototypen kann durch Drehen, Fraesen, Hobelschleifen und Bohren erreicht werden?
Die Genauigkeit von Bearbeitungsteilen ist ein Begriff zur Bewertung der geometrischen Parameter von bearbeiteten Oberflächen, der hauptsächlich zur Charakterisierung der Präzision von Produkten verwendet wird. Die Verarbeitungsgenauigkeit wird nach Toleranzklassen gemessen. Je kleiner der Grad-Wert, desto höher ist die Genauigkeit.
Toleranzstufe
Es gibt 20 Toleranzstufen von IT01, IT0, IT1, IT2, IT3 bis IT18. Unter diesen gibt IT01 an, dass das Teil die höchste Bearbeitungsgenauigkeit aufweist. IT18 zeigt an, dass die Verarbeitungsgenauigkeit dieses Teils am niedrigsten ist. Im Allgemeinen gehören die Fabrik- und Bergbaumaschinen zur IT7-Ebene und die landwirtschaftlichen Maschinen zur IT8-Ebene. Entsprechend den unterschiedlichen Funktionen der Produktteile sind die zu erreichenden Bearbeitungspräzisionen unterschiedlich und auch die gewählten Bearbeitungsformen und -techniken unterschiedlich. In diesem Artikel wird die Bearbeitungsgenauigkeit vorgestellt, die mit verschiedenen gängigen Bearbeitungsformen wie Drehen, Fräsen, Hobeln, Schleifen, Bohren und Bohren erzielt werden kann.
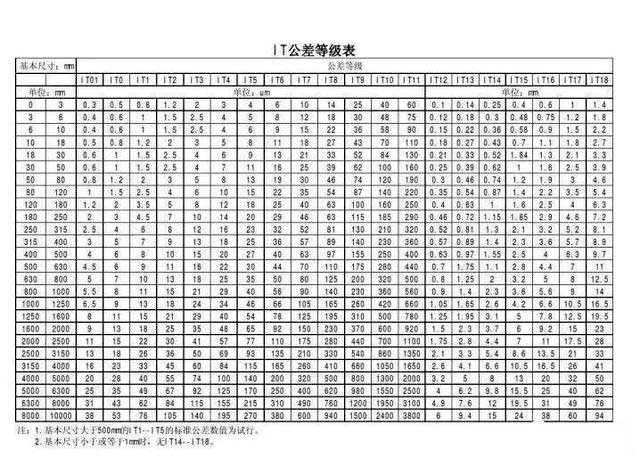
Bearbeitungstoleranz Skala
Drehen
Das Werkstück dreht sich und das Drehwerkzeug führt eine gerade oder gekrümmte Bewegung in der Ebene aus. Das Drehen wird im Allgemeinen auf einer Drehmaschine durchgeführt, um die inneren und äußeren zylindrischen Flächen, Endflächen, konischen Flächen, Formflächen und Gewinde des Werkstücks zu bearbeiten.
Die Drehgenauigkeit beträgt im Allgemeinen IT8-IT7 und die Oberflächenrauheit 1,6-0,8 μm.
1) Schruppen dient zur Verbesserung der Dreheffizienz durch Verwendung einer großen Schnitttiefe und eines großen Vorschubs, ohne die Schnittgeschwindigkeit zu verringern. Die Bearbeitungsgenauigkeit kann jedoch nur IT11 erreichen, und die Oberflächenrauheit beträgt Rα20-10μm.
2) Das Halbfertigdrehen und das Fertigdrehen sollten eine hohe Geschwindigkeit und eine geringe Vorschub- und Schnitttiefe aufweisen, soweit dies möglich ist. Die Bearbeitungsgenauigkeit kann IT10-IT7 erreichen und die Oberflächenrauheit beträgt Rα10-0,16μm.
3) Hochgeschwindigkeits-Präzisionsdrehen von NE-Metallteilen mit feinpolierten Diamantdrehwerkzeugen auf Präzisionsdrehmaschinen. Die Bearbeitungsgenauigkeit kann IT7-IT5 erreichen und die Oberflächenrauheit ist Rα0.04-0.01μm. Diese Drehung wird als „Spiegel Drehen“ bezeichnet.
2. Fräsen
Fräsen bezieht sich auf die Verwendung von rotierenden mehrschneidigen Schneidwerkzeugen zum Schneiden von Werkstücken, was eine hocheffiziente Bearbeitungsmethode darstellt. Geeignet für die Bearbeitung von Ebenen, Nuten, verschiedenen Formflächen (z. B. Keilen, Zahnrädern und Gewinden) und Sonderformen der Form. Entsprechend der gleichen oder entgegengesetzten Richtung der Hauptbewegungsgeschwindigkeit und der Vorschubrichtung des Werkstücks beim Fräsen kann es in Vorwärtsfräsen und Rückwärtsfräsen unterteilt werden. Die Bearbeitungsgenauigkeit beim Fräsen liegt in der Regel bei IT8-IT7 und die Oberflächenrauheit bei 6,3-1,6 μm.
1) Bearbeitungsgenauigkeit beim Schruppfräsen IT11 - IT13, Oberflächenrauheit 5-20μm.
2) Bearbeitungsgenauigkeit beim Halbfertigfräsen IT8 - IT11, Oberflächenrauheit 2,5 - 10 μm.
3) Bearbeitungsgenauigkeit beim Schlichtfräsen IT16-IT8, Oberflächenrauheit 0,63-5 μm.
3. Hobeln
Hobeln ist ein Schneideverfahren, das einen Hobel verwendet, um das Werkstück horizontal sich horizontal hin- und herbewegt. Es wird hauptsächlich zur Formbearbeitung von Teilen eingesetzt.
Die Präzision des Hobelns liegt im Allgemeinen bei IT9-IT7 und die Oberflächenrauheit bei Ra6,3-1,6 μm.
1) Die Präzision der Schruppbearbeitung kann IT12-IT11 erreichen, und die Oberflächenrauheit beträgt 25-12,5 μm.
2) Die Präzision der semipräzisen Bearbeitung kann IT10-IT9 erreichen, und die Oberflächenrauheit beträgt 6,2-3,2 μm.
3) Präzisionshobelbearbeitung kann IT8-IT7 erreichen, und die Oberflächenrauheit ist 3.2-1.6μm.
4. Schleifen
Schleifen bezieht sich auf das Bearbeitungsverfahren zum Entfernen von überschüssigem Material auf dem Werkstück unter Verwendung von Schleifmitteln und Schleifwerkzeugen. Es gehört zur Weiterverarbeitungsindustrie und ist im Maschinenbau weit verbreitet.
Das Schleifen wird normalerweise zum Vorschlichten und Endbearbeiten mit einer Genauigkeit von IT8-IT5 oder höher verwendet, und die Oberflächenrauheit beträgt im Allgemeinen 1,25-0,16 μm.
1) Die Oberflächenrauheit beim Präzisionsschleifen beträgt 0,16-0,04 μm.
2) Die Oberflächenrauheit beim Ultrapräzisionsschleifen beträgt 0,04–0,01 μm.
3) Die Oberflächenrauheit beim Spiegelschleifen kann weniger als 0,01 μm betragen.
5. Bohren
Bohren ist eine grundlegende Methode der Lochbearbeitung. Das Bohren erfolgt häufig auf Bohrmaschinen und Drehmaschinen oder auf einer Bohr- oder Fräsmaschine.
Das Bohren hat eine geringe Bearbeitungsgenauigkeit, erreicht im Allgemeinen nur IT10 und die Oberflächenrauheit beträgt im Allgemeinen 12,5 bis 6,3 μm. Nach dem Bohren werden Reiben und Reiben häufig zum Vorschlichten und Schlichten verwendet.
6. Metallbohren
Das Bohren ist eine Art Innendurchmesser-Schneidtechnologie mit Werkzeug zum Vergrößern von Löchern oder anderen kreisförmigen Konturen. Das Einsatzspektrum reicht in der Regel von der Halb- bis zur Fertigbearbeitung. Das verwendete Werkzeug ist normalerweise ein einschneidiges Bohrwerkzeug (Bohrstange genannt).
1) Die Präzision des Bohrens von Stahlmaterialien beträgt im Allgemeinen bis zu IT9-IT7, und die Oberflächenrauheit beträgt 2,5-0,16 um.
2) Die Präzision des Präzisionsbohrens kann IT7-IT6 erreichen und die Oberflächenrauheit ist 0.63-0.08μm.
Toleranzstufe
Es gibt 20 Toleranzstufen von IT01, IT0, IT1, IT2, IT3 bis IT18. Unter diesen gibt IT01 an, dass das Teil die höchste Bearbeitungsgenauigkeit aufweist. IT18 zeigt an, dass die Verarbeitungsgenauigkeit dieses Teils am niedrigsten ist. Im Allgemeinen gehören die Fabrik- und Bergbaumaschinen zur IT7-Ebene und die landwirtschaftlichen Maschinen zur IT8-Ebene. Entsprechend den unterschiedlichen Funktionen der Produktteile sind die zu erreichenden Bearbeitungspräzisionen unterschiedlich und auch die gewählten Bearbeitungsformen und -techniken unterschiedlich. In diesem Artikel wird die Bearbeitungsgenauigkeit vorgestellt, die mit verschiedenen gängigen Bearbeitungsformen wie Drehen, Fräsen, Hobeln, Schleifen, Bohren und Bohren erzielt werden kann.
Bearbeitungstoleranz Skala
Drehen
Das Werkstück dreht sich und das Drehwerkzeug führt eine gerade oder gekrümmte Bewegung in der Ebene aus. Das Drehen wird im Allgemeinen auf einer Drehmaschine durchgeführt, um die inneren und äußeren zylindrischen Flächen, Endflächen, konischen Flächen, Formflächen und Gewinde des Werkstücks zu bearbeiten.
Die Drehgenauigkeit beträgt im Allgemeinen IT8-IT7 und die Oberflächenrauheit 1,6-0,8 μm.
1) Schruppen dient zur Verbesserung der Dreheffizienz durch Verwendung einer großen Schnitttiefe und eines großen Vorschubs, ohne die Schnittgeschwindigkeit zu verringern. Die Bearbeitungsgenauigkeit kann jedoch nur IT11 erreichen, und die Oberflächenrauheit beträgt Rα20-10μm.
2) Das Halbfertigdrehen und das Fertigdrehen sollten eine hohe Geschwindigkeit und eine geringe Vorschub- und Schnitttiefe aufweisen, soweit dies möglich ist. Die Bearbeitungsgenauigkeit kann IT10-IT7 erreichen und die Oberflächenrauheit beträgt Rα10-0,16μm.
3) Hochgeschwindigkeits-Präzisionsdrehen von NE-Metallteilen mit feinpolierten Diamantdrehwerkzeugen auf Präzisionsdrehmaschinen. Die Bearbeitungsgenauigkeit kann IT7-IT5 erreichen und die Oberflächenrauheit ist Rα0.04-0.01μm. Diese Drehung wird als „Spiegel Drehen“ bezeichnet.
2. Fräsen
Fräsen bezieht sich auf die Verwendung von rotierenden mehrschneidigen Schneidwerkzeugen zum Schneiden von Werkstücken, was eine hocheffiziente Bearbeitungsmethode darstellt. Geeignet für die Bearbeitung von Ebenen, Nuten, verschiedenen Formflächen (z. B. Keilen, Zahnrädern und Gewinden) und Sonderformen der Form. Entsprechend der gleichen oder entgegengesetzten Richtung der Hauptbewegungsgeschwindigkeit und der Vorschubrichtung des Werkstücks beim Fräsen kann es in Vorwärtsfräsen und Rückwärtsfräsen unterteilt werden. Die Bearbeitungsgenauigkeit beim Fräsen liegt in der Regel bei IT8-IT7 und die Oberflächenrauheit bei 6,3-1,6 μm.
1) Bearbeitungsgenauigkeit beim Schruppfräsen IT11 - IT13, Oberflächenrauheit 5-20μm.
2) Bearbeitungsgenauigkeit beim Halbfertigfräsen IT8 - IT11, Oberflächenrauheit 2,5 - 10 μm.
3) Bearbeitungsgenauigkeit beim Schlichtfräsen IT16-IT8, Oberflächenrauheit 0,63-5 μm.
3. Hobeln
Hobeln ist ein Schneideverfahren, das einen Hobel verwendet, um das Werkstück horizontal sich horizontal hin- und herbewegt. Es wird hauptsächlich zur Formbearbeitung von Teilen eingesetzt.
Die Präzision des Hobelns liegt im Allgemeinen bei IT9-IT7 und die Oberflächenrauheit bei Ra6,3-1,6 μm.
1) Die Präzision der Schruppbearbeitung kann IT12-IT11 erreichen, und die Oberflächenrauheit beträgt 25-12,5 μm.
2) Die Präzision der semipräzisen Bearbeitung kann IT10-IT9 erreichen, und die Oberflächenrauheit beträgt 6,2-3,2 μm.
3) Präzisionshobelbearbeitung kann IT8-IT7 erreichen, und die Oberflächenrauheit ist 3.2-1.6μm.
4. Schleifen
Schleifen bezieht sich auf das Bearbeitungsverfahren zum Entfernen von überschüssigem Material auf dem Werkstück unter Verwendung von Schleifmitteln und Schleifwerkzeugen. Es gehört zur Weiterverarbeitungsindustrie und ist im Maschinenbau weit verbreitet.
Das Schleifen wird normalerweise zum Vorschlichten und Endbearbeiten mit einer Genauigkeit von IT8-IT5 oder höher verwendet, und die Oberflächenrauheit beträgt im Allgemeinen 1,25-0,16 μm.
1) Die Oberflächenrauheit beim Präzisionsschleifen beträgt 0,16-0,04 μm.
2) Die Oberflächenrauheit beim Ultrapräzisionsschleifen beträgt 0,04–0,01 μm.
3) Die Oberflächenrauheit beim Spiegelschleifen kann weniger als 0,01 μm betragen.
5. Bohren
Bohren ist eine grundlegende Methode der Lochbearbeitung. Das Bohren erfolgt häufig auf Bohrmaschinen und Drehmaschinen oder auf einer Bohr- oder Fräsmaschine.
Das Bohren hat eine geringe Bearbeitungsgenauigkeit, erreicht im Allgemeinen nur IT10 und die Oberflächenrauheit beträgt im Allgemeinen 12,5 bis 6,3 μm. Nach dem Bohren werden Reiben und Reiben häufig zum Vorschlichten und Schlichten verwendet.
6. Metallbohren
Das Bohren ist eine Art Innendurchmesser-Schneidtechnologie mit Werkzeug zum Vergrößern von Löchern oder anderen kreisförmigen Konturen. Das Einsatzspektrum reicht in der Regel von der Halb- bis zur Fertigbearbeitung. Das verwendete Werkzeug ist normalerweise ein einschneidiges Bohrwerkzeug (Bohrstange genannt).
1) Die Präzision des Bohrens von Stahlmaterialien beträgt im Allgemeinen bis zu IT9-IT7, und die Oberflächenrauheit beträgt 2,5-0,16 um.
2) Die Präzision des Präzisionsbohrens kann IT7-IT6 erreichen und die Oberflächenrauheit ist 0.63-0.08μm.