Was sind die Vorsichtsmassnahmen fuer das Bohren von Edelstahl?
Zerspanungstechnik aus Edelstahl und Design von entsprechenden Schneidwerkzeugparameter. Gegenüber der Bearbeitung von gewöhnlichen Stahlwerkstoffen gibt es große Unterschiede. Lassen Sie uns nun über die spezielle Verarbeitungstechnologie sprechen.
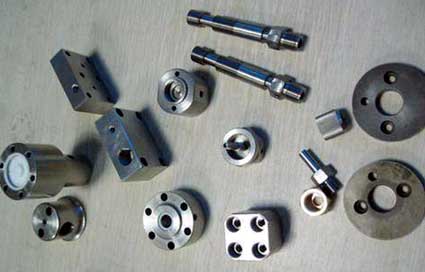
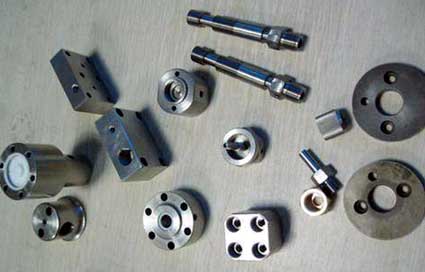
1, bohrbearbeitung
Beim Bohren ist die Lochbearbeitung aufgrund der schlechten Wärmeleitfähigkeit des Edelstahlmaterials und des kleinen Elastizitätsmoduls nicht einfach. Um das Problem der Lochbearbeitung von rostfreiem Stahl zu lösen, ist es am besten, das geeignete Werkzeugmaterial auszuwählen, um die geometrischen Parameter des Werkzeugs und die Schnittmenge des Werkzeugs zu bestimmen. Die Hauptprodukte der Kangding Metal Company sind die Bearbeitung von Kreiseln, Schrauben, Achsen, CNC-Drehbearbeitungen, Werkzeuggriffe, Werkzeugstangen und Spannfutter. Beim Bohren von Edelstahl hat der Bohrer normalerweise einen Bohrer aus W6Mo5Cr4V2Al oder W2Mo9Cr4Co8. Der Nachteil dieses Bohrertyps ist, dass er teuer und nicht sehr gut zu kaufen ist. Bei Verwendung des gängigen Standard-Schnellstahlbohrers W18Cr4V. Da es Mängel wie einen kleinen Scheitelwinkel und zu große Späne gibt, kann das Loch nicht rechtzeitig abgelassen werden und die Schneidflüssigkeit kann den Bohrer nicht rechtzeitig kühlen. Darüber hinaus führt die schlechte Wärmeleitfähigkeit von Edelstahlwerkstoffen zu einer Erhöhung der an der Schneide konzentrierten Schnitttemperatur. Es ist leicht, die zwei Flanken und die Hauptkante zu verbrennen und zu brechen und die Lebensdauer des Meißels zu verkürzen.
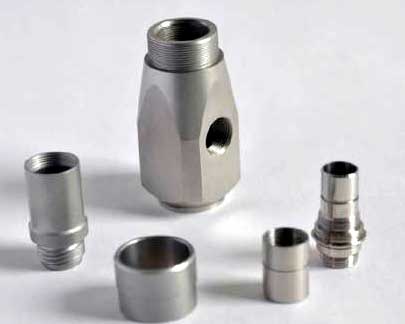
1> Werkzeuggeometrieparameter
Beim Bohren mit dem normalen Schnellstahlbohrer W18Cr4V konzentrieren sich die Schnittkraft und die Schnitttemperatur auf die Bohrerspitze. Um die Haltbarkeit des Schneidteils des Bohrmeißels zu verbessern, kann der Scheitelwinkel in geeigneter Weise vergrößert werden, und der Scheitelwinkel wird im Allgemeinen von 135 ° bis 140 ° gewählt. Eine Vergrößerung des Spitzenwinkels verringert auch den Spanwinkel der Außenkante und verengt die Bohrspäne, um die Spanabfuhr zu erleichtern. Wenn jedoch der obere Winkel vergrößert wird, wird die Meißelkante des Bohrers breiter, was zu einer Erhöhung des Schneidwiderstands führt. Daher muss die Meißelkante geschliffen werden. Nach dem Schleifen beträgt der schräge Winkel der Meißelkante 47 ° bis 55 ° und der Spanwinkel der Meißelkante 3 ° bis 5 °. Beim Schleifen der Meißelkante sollten die Schneide und die zylindrische Ecke abgerundet sein, um die Festigkeit der Meißelkante zu erhöhen.
Da der Elastizitätsmodul von rostfreiem Stahl klein ist, ist die elastische Rückstellung von Metall unter der Chipschicht groß und die Kaltverfestigung ist bei der Verarbeitung ernst. Ein zu kleiner Rückenwinkel beschleunigt den Verschleiß der Bohrerflanke, erhöht die Schnitttemperatur und verkürzt die Lebensdauer des Bohrers. Daher sollte der Freiwinkel angemessen vergrößert werden, der hintere Winkel ist jedoch zu groß, wodurch die Hauptkante des Bohrers dünn wird und die Steifigkeit der Hauptkante verringert wird. Daher sollte der Freiwinkel 12 ° -15 ° betragen. Um die Späne zu verengen und das Entfernen der Späne zu erleichtern, müssen an den beiden Flanken des Meißels versetzt angeordnete Spanrillen geöffnet werden.
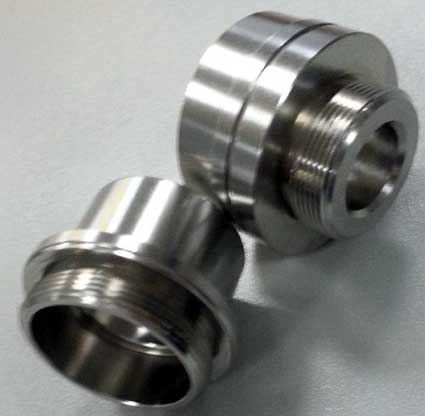
2>, Abtragungsmenge Auswahl
Beim Bohren sollte die Wahl der Schnittmenge auf dem Grundpunkt der Reduzierung der Schnitttemperatur basieren. Da das Hochgeschwindigkeitsschneiden die Schnitttemperatur und die hohen Schnitttemperaturen den Werkzeugverschleiß erhöhen, ist der wichtigste Teil der Schnittmenge die Schnittgeschwindigkeit. Im Allgemeinen beträgt die Schnittgeschwindigkeit vorzugsweise 12 bis 15 m / min. Die Vorschubgeschwindigkeit hat nur einen geringen Einfluss auf die Lebensdauer des Werkzeugs. Die Vorschubauswahl ist jedoch zu gering, um das Werkzeug in die gehärtete Schicht zu schneiden und den Verschleiß zu erhöhen. Wenn die Vorschubmenge zu groß ist, wird die Oberflächenrauheit verschlechtert. In Kombination mit den obigen zwei Faktoren wird die Zufuhrmenge vorzugsweise von 0,32 bis 0,50 mm / r ausgewählt.
3>, Auswahl der Schneidflüssigkeit
Um die Schnitttemperatur beim Bohren zu senken, kann eine Emulsion als Kühlmedium verwendet werden.
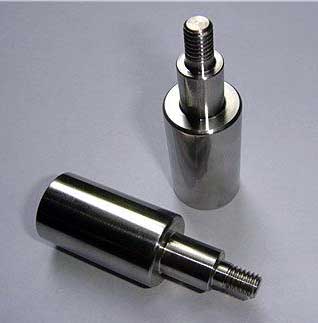
2, Reiben maschinelle Bearbeitung
1> Werkzeuggeometrie-Parameter
Beim Reiben von Edelstahlwerkstoffen wird zum größten Teil eine Hartmetallreibahle verwendet. Die Struktur und die geometrischen Parameter der Reibahle unterscheiden sich von denen einer normalen Reibahle. Um die Festigkeit der Zähne zu verbessern und ein Verstopfen der Späne beim Reiben zu verhindern, ist die Anzahl der Zähne der Reibahle im Allgemeinen gering. Der Spanwinkel der Reibahle beträgt in der Regel 8 bis 12 °, in bestimmten Fällen kann jedoch auch ein Spanwinkel von 0 bis 5 ° verwendet werden, um ein schnelles Reiben zu erreichen. Der Rückenwinkel beträgt im Allgemeinen 8 ° ~ 12 °; Die Wahl des Steigungswinkels variiert je nach Bohrung. Im Allgemeinen beträgt das Durchgangsloch 15 ° bis 30 ° und das Durchgangsloch 45 °;
Beim Reiben kann zum Weiterleiten der Späne auch der Neigungswinkel der Kante entsprechend vergrößert werden. Der Neigungswinkel der Kante beträgt in der Regel 10 ° bis 20 °. Die Breite der Kantenbandbreite beträgt 0,1-0,15 mm. Der umgekehrte Kegel auf der Reibahle sollte größer als die gewöhnliche Reibahle sein, die Reibahle aus Hartlegierung ist im Allgemeinen 0,25 ~ 0,5 mm / 100 mm, die Reibahle aus Schnellarbeitsstahl ist 0,1 ~ 0,25 mm / 100 mm; Die Länge des Räumerkorrekturteils beträgt im Allgemeinen 65% bis 80% des gewöhnlichen Räumers und die Länge des zylindrischen Teils beträgt 40% bis 50% des gewöhnlichen Räumers.
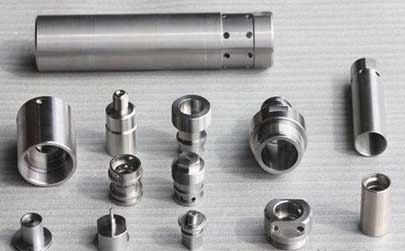
2>, Reib- Volumen Auswahl
Die Zufuhrmenge während Aufreiben 0,08 ~ 0,4 mm / r, und die Räumungsgeschwindigkeit 10 ~ 20 m / min. Die grobe Scharniertoleranz beträgt im Allgemeinen 0,2 bis 0,3 mm und die feine Scharniertoleranz beträgt 0,1 bis 0,2 mm. Hartmetall-Werkzeuge sollten für raue Scharniere und Schnellarbeitsstahl Werkzeuge für die Fein Scharniere verwendet werden.
3>, reiben flüssigkeit auswahl
Wenn das Edelstahlmaterial aufgebohrt wird, kann der vollständige Verlust Systemöl oder Molybdändisulfid als Kühlmedium verwendet werden.
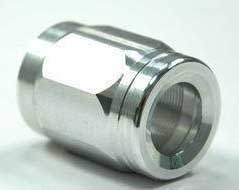
3, langweilige Verarbeitung des Edelstahls
1>, werkzeug material auswahl
Aufgrund der hohen Schnittkraft und der hohen Schnitttemperatur bei der Bearbeitung von Edelstahlteilen sollte das Werkzeugmaterial als hochwertige YC- oder YG-Hartlegierung mit hoher Wärmeleitfähigkeit gewählt werden. Zum Schlichten sind auch Wendeplatten aus Hartmetall YT14 und YT15 erhältlich. Aufgrund der Eigenschaften solcher Materialien ist die Zähigkeit groß und die Kaltverfestigung ist ernst. Späne, die durch Schneiden dieser Materialien in Form von Einheitsspänen erzeugt werden, verursachen Werkzeugvibrationen und leichtes Zusammenfallen der Klinge. Daher ist die erste Überlegung für keramische Schneidwerkzeuge beim Schneiden solcher Materialteile die mikroskopische Zähigkeit.
Derzeit ist Sialon eine bessere Wahl, insbesondere für Alpha / Beta-Sialon-Materialien. Aufgrund seiner hervorragenden Beständigkeit gegen Verformung bei hohen Temperaturen und Diffusionsverschleiß wurde es erfolgreich zum Schneiden von Legierungen auf Nickelbasis eingesetzt, und seine Lebensdauer ist weitaus länger als die von Keramiken auf Al2O3-Basis. Darüber hinaus sind SiC-Whisker-verstärkte Keramiken auch ein sehr wirksames Werkzeugmaterial zum Schneiden von rostfreiem Stahl oder Legierungen auf Nickelbasis.
Für die Bearbeitung von gehärteten Teilen solcher Werkstoffe können CBN-Einsätze (Cubic Boron Nitride) verwendet werden. Die CBN-Härte ist nach Diamant an zweiter Stelle, die Härte kann 7000 bis 8000 HV erreichen, so dass die Verschleißfestigkeit sehr hoch ist. Gegenüber Diamant hat CBN den herausragenden Vorteil, dass die Hitzebeständigkeit mit bis zu 1200 ° C deutlich höher ist als bei Diamant und hohen Schnitttemperaturen standhält. Außerdem ist seine chemische Inertheit sehr groß und spielt beim Eisengruppenmetall bei 1200-1300ºC keine chemische Rolle. Es eignet sich daher sehr gut für die Bearbeitung von Edelstahlwerkstoffen. Seine Werkzeugstandzeit beträgt das Dutzendfache der von Hartmetall- oder Keramikwerkzeugen.
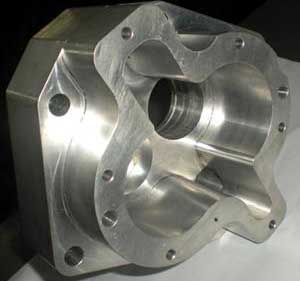
2. Bohrwerkzeug-Geometrieparameter
Die geometrischen Parameter des Bohrwerkzeugs spielen eine wichtige Rolle für die Schneidleistung. Um das Schneiden leicht und glatt zu machen, sollte das Hartmetallwerkzeug einen großen vorderen Winkel einnehmen, um die Werkzeuglebensdauer zu verbessern. Beim Schruppen beträgt der vordere Winkel im Allgemeinen 10 ° bis 20 ° und das Halbfinish 15 ° bis 20 °, während des Finishs 20 ° bis 30 °. Die Wahl des Steigungswinkels basiert auf der Tatsache, dass bei starren Prozesssystemen 30 ° ~ 45 ° erforderlich sind. Wenn das Prozesssystem eine schlechte Steifigkeit aufweist, nehmen Sie 60 bis 75 °. Wenn das Verhältnis der Länge zum Durchmesser des Werkstücks das Zehnfache überschreitet, beträgt es 90 °.
Die geometrischen Parameter des Bohrwerkzeugs spielen eine wichtige Rolle für die Schneidleistung. Um das Schneiden leicht und glatt zu machen, sollte das Hartmetallwerkzeug einen großen vorderen Winkel einnehmen, um die Werkzeuglebensdauer zu verbessern. Beim Schruppen beträgt der vordere Winkel im Allgemeinen 10 ° bis 20 ° und das Halbfinish 15 ° bis 20 °, während des Finishs 20 ° bis 30 °. Die Wahl des Steigungswinkels basiert auf der Tatsache, dass bei starren Prozesssystemen 30 ° ~ 45 ° erforderlich sind. Wenn das Prozesssystem eine schlechte Steifigkeit aufweist, nehmen Sie 60 bis 75 °. Wenn das Verhältnis der Länge zum Durchmesser des Werkstücks das Zehnfache überschreitet, beträgt es 90 °.
Beim Bohren von Edelstahl mit Keramikwerkzeugen werden Keramikwerkzeuge in den meisten Fällen mit einem negativen Spanwinkel geschnitten. Dies trägt dazu bei, die Klinge zu verstärken und die Überlegenheit des Keramikwerkzeugs bei hoher Druckfestigkeit voll auszunutzen. Die Größe des Rückwinkels wirkt sich direkt auf den Werkzeugverschleiß aus und wirkt sich auf die Kantenfestigkeit aus. Sie wird im Allgemeinen zwischen 5 ° und 12 ° gewählt. Die Änderung des Steigungswinkels beeinflusst die Variation der Radial- und Bauteilschneidkräfte sowie die Schnittbreite und die Schnittdicke. Da die Vibration des Prozesssystems für das Keramikwerkzeug äußerst ungünstig ist, ist die Wahl des Steigungswinkels vorteilhaft, um diese Vibration zu verringern, im Allgemeinen 30 ° bis 75 °. Bei Auswahl von CBN als Werkzeugmaterial betragen die Parameter für die Werkzeuggeometrie 0 ° bis 10 ° für den Spanwinkel, 12 ° bis 20 ° für den Rückwinkel und 45 ° bis 90 ° für den Hauptwinkel.
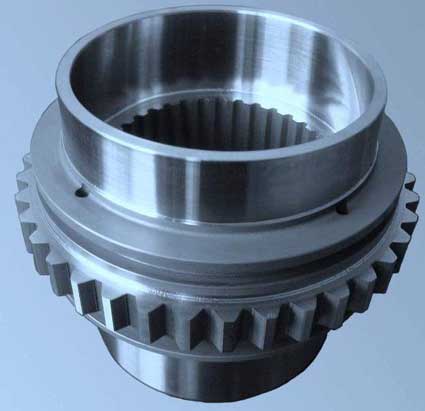
3>. Der Rauheitswert der Spanfläche sollte beim Schärfen klein sein
Um das Phänomen des Anklebens von Spänen zu vermeiden. Die Vorder- und Rückflanke des Werkzeugs sollte sorgfältig geschärft werden, um einen kleinen Rauheitswert zu gewährleisten, wodurch der Spanabflusswiderstand verringert und ein Anhaften der Späne vermieden wird.
4>, halten Sie die scharfe Kante des Werkzeugs
Die Schneide des Werkzeugs sollte scharf sein, um das Aushärten des Werkstücks zu verringern. Die Vorschubmenge und die Menge des Gegenmessers sollten nicht zu gering sein, um das Schneiden des Werkzeugs in die gehärtete Schicht zu verhindern und die Lebensdauer des Werkzeugs zu beeinträchtigen.
5>, Achten Sie auf das Schleifen der Spanbrechnut
Da Späne aus rostfreiem Stahl starke und zähe Eigenschaften aufweisen, sollte das Schleifen der Spanbruchrille auf der Spanfläche des Werkzeugs angemessen sein, damit Spanbruch, Spänehaltung und Spanentfernung beim Schneidvorgang bequem sind.
6>, wählen Sie die Schnittmenge
Aufgrund der Eigenschaften von Edelstahlmaterialien ist es ratsam, zum Schneiden eine niedrige Geschwindigkeit und einen großen Vorschub zu verwenden.
Bei der Verwendung von Keramikwerkzeugen zum Bohren ist die angemessene Auswahl der Schnittmenge einer der Schlüssel, um die Leistung von Keramikwerkzeugen voll auszuschöpfen. Beim Schneiden von Keramikwerkzeugen kann die Schnittmenge entsprechend der Beziehung zwischen Verschleißfestigkeit und Schnittmenge ausgewählt werden; Für unterbrochenes Schneiden sollte die angemessene Schnittmenge gemäß dem Schadensgesetz des Werkzeugs bestimmt werden. Aufgrund der überlegenen Hitzebeständigkeit und Verschleißfestigkeit von Keramikmessern ist der Einfluss der Schnittmenge auf die Lebensdauer des Werkzeugs geringer als bei Hartmetallwerkzeugen.
Bei der Bearbeitung mit Keramikwerkzeugen ist der Vorschub im Allgemeinen am empfindlichsten für die Beschädigung des Werkzeugs. Entsprechend der Art des Werkstückmaterials unter der Voraussetzung von Maschinenleistung, Steifigkeit des Prozesssystems und Klingenfestigkeit. Wählen Sie beim Bohren von Edelstahlteilen eine hohe Schnittgeschwindigkeit, ein großes Gegenmesser und einen relativ kleinen Vorschub.