Schneidbearbeitung und Werkzeugdesign von Titanteilen
Einführung: Titan-Legierung hat einen kleinen Elastizitätsmodul. Zum Beispiel ist der Elastizitätsmodul von TC4 E = 110 GPa, was ungefähr der Hälfte desjenigen von Stahl entspricht. Daher verringert die große elastische Verformung des Werkstücks, die durch die Schneidkraft verursacht wird, die Genauigkeit des Werkstücks, so dass die Steifigkeit des Bearbeitungssystems verbessert werden sollte. Das Werkstück muss sehr fest eingespannt sein und das Werkzeugmoment zum Werkstückaufnahmepunkt wird minimiert. Das Werkzeug muss scharf sein, da sonst Vibrationen und Reibungen auftreten, die die Lebensdauer des Werkzeugs verkürzen und die Genauigkeit des Werkstücks verringern.
Beim Schneiden von Titanlegierungen können sich nur im Bereich der Schnittgeschwindigkeit von 1-5 mm / min Späne bilden. Unter allgemeinen Produktionsbedingungen treten daher beim Schneiden von Titanlegierungen keine Späne auf. Der Reibungskoeffizient zwischen dem Werkstück und dem Werkzeug ist nicht sehr groß und es ist leicht, eine gute Oberflächenqualität zu erzielen. Die Verwendung eines Kühlschmiermittels hat keinen Einfluss auf die Verbesserung der Mikrogeometrie der Oberfläche der Titanlegierung. Die Rauheit der unteren Oberfläche der bearbeiteten Titanlegierung ist auf das Fehlen von Aufbauschneiden am Werkzeug zurückzuführen. Die Verwendung von Kühlschmierstoffen hat keinen Einfluss auf die Verbesserung der Mikrogeometrie von Titanlegierungsoberflächen. Die geringe Rauheit der bearbeiteten Oberfläche beim Schneiden von Titanlegierungen ist auf die Abwesenheit von Spantumoren am Werkzeug zurückzuführen.
Um jedoch die Schnittbedingungen zu verbessern, die Schnitttemperaturen zu senken, die Lebensdauer des Werkzeugs zu erhöhen und die Brandgefahr zu beseitigen, ist es erforderlich, während der Verarbeitung eine große Menge löslichen Kühlmittels zu verwenden.
Normalerweise tritt bei der Bearbeitung von Teilen aus Titanlegierungen kein Zünd- und Verbrennungsphänomen auf, während es beim Mikroschneidvorgang zu einem Zünd- und Verbrennungsphänomen kommt. Um diese Gefahr zu vermeiden, sollte das Kühlmittel in großen Mengen verwendet werden. Entfernen Sie die Späne rechtzeitig von den Werkzeugmaschinen. Feuerlöscheinrichtungen sind vorhanden; Ersetzen Sie stumpfe Messer rechtzeitig. Wenn die Oberfläche des Werkstücks verschmutzt ist, können leicht Funken entstehen. Zu diesem Zeitpunkt muss die Schnittgeschwindigkeit reduziert werden. Im Vergleich zu dünnen Spänen ist es bei dicken Spänen nicht einfach, Funken zu erzeugen. Daher muss das Schnittvolumen erhöht werden, wodurch die Temperatur nicht so schnell ansteigt, wie die Schnittgeschwindigkeit zunimmt.
Auswahlkriterien für die Bearbeitung von Titanlegierungen: Unter dem Gesichtspunkt der Absenkung der Schnitttemperatur sollten eine niedrigere Schnittgeschwindigkeit und eine größere Schnittmenge angewendet werden. Aufgrund der hohen Schnitttemperatur nimmt die Titanlegierung Sauerstoff und Wasserstoff aus der Atmosphäre auf, wodurch die Oberfläche des Werkstücks hart und spröde wird und das Werkzeug stark abgenutzt wird. Daher muss während der Bearbeitung die Temperatur der Werkzeugspitze auf einer geeigneten Temperatur gehalten werden, um eine Übertemperatur zu vermeiden.
Beim Drehen von harthäutigen Titanlegierungswerkstücken mit dem YG8-Drehwerkzeug unter intermittierenden Schnittbedingungen werden folgende Schnittparameter empfohlen: v = 15 ~ 28 m / min, f = 0,25 ~ 0,35 mm / r, ap = 1 ~ 3 mm.
Bei Verwendung eines YG3-Drehwerkzeugs zum Bearbeiten eines Titanlegierungs-Werkstücks unter kontinuierlichen Schneidebedingungen beträgt die empfohlene Schneidemenge: v = 50 ~ 70 m / min, f = 0,1 ~ 0,2 mm / r, ap = 0,3 ~ 1 mm. Tabelle 2 zeigt den verfügbaren Schneidumfang zum Drehen von Titanlegierungen.
Schnittmenge beim Drehen von Titanlegierungen:
Verfahrenseigenschaften - Titanlegierungsmaterial - Härte - Schneidzugabe (mm) - Schneidgeschwindigkeit (mm / min) - Werkzeuggehen
Oxid haut dicke
Grobdrehen: TA1 ~ 7, TC1 ~ 2-Soft->
Grobdrehen: TA8, TC3 ~ 8-Medium->
Grobdrehen : TC9 ~ 10, TB1 ~ 2 - Schwer ->
Fertig drehen : TA1 ~ 7, TC1 ~ 2-Soft
Fertig drehen: TA8, TC3-8-in
Fertig drehen: TC9-10, TB1-2-Hard
Der TC4 (Härte HB320 ~ 360) wird mit dem YG6X-Drehwerkzeug gedreht, und die optimale Schnittgeschwindigkeit beträgt 60 mm / min, wenn ap = 1 mm und f = 0,1 mm / r. Auf dieser Basis ist in Tabelle 3 die Schnittgeschwindigkeit bei unterschiedlicher Schnittmenge und Schnitttiefe angegeben.
Schnittgeschwindigkeit beim Drehen der Titanlegierung TC4
Ein typisches Drehwerkzeug zur Bearbeitung von Titanlegierungen weist folgende Eigenschaften auf:
Das Klingenmaterial ist YG6X, YG10HT; Der Spanwinkel ist klein, im Allgemeinen & ggr; 0 = 4 ° ~ 6 °, was die Festigkeit des Messerkopfs erhöht; Es gibt negative Fasen von f = 0,05 bis 0,1 mm, um die Stärke der Klinge zu verbessern. Der hintere Winkel ist groß, im Allgemeinen α0 = 14 ° bis 16 °, um die Reibung dahinter zu verringern und die Haltbarkeit des Werkzeugs zu verbessern; Im Allgemeinen ist es nicht erlaubt, scharfe Ecken oder Übergangskanten zu schleifen, und die abgerundeten Ecken der Schleifkante sind r = 0,5 mm, und das Grobdrehen kann r = 1 ~ 2 mm erreichen, um die Festigkeit der Schneidkante zu verbessern; Beim Fertigdrehen oder Drehen dünnwandiger Teile ist der Hauptabweichungswinkel des Werkzeugs groß, im Allgemeinen 75 ° ~ 90 °.
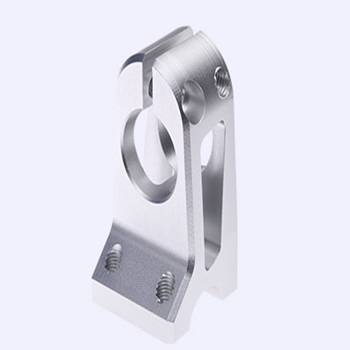
Schnittmenge:
Grobe Drehung: v = 40 ~ 50 m / min, f = 0,2 ~ 0,3 mm / r, ap = 3 ~ 5 mm.
Halbfertigdrehen: v = 40 ~ 45 m / min, f = 0,2 ~ 0,3 mm / r, ap = 1 ~ 2 mm.
Feines Drehen: v = 50 ~ 55 m / min, f = 0,1 ~ 0,15 mm / r, ap = 0,2 ~ 0,5 mm.
Das Kühlen mit Emulsionen kann die Werkzeughaltbarkeit effektiv verbessern.
Das Bohren von Titanlegierungen ist schwierig. Beim Bohren kommt es häufig zu Verbrennungen und Bohrerbrüchen. Der Hauptgrund ist das schlechte Schleifen des Bohrers, die vorzeitige Spanabfuhr, die schlechte Kühlung und die schlechte Steifigkeit des Prozesssystems.
(1) Bohren Auswahl: Für Bohrer mit einem Durchmesser von mehr als 5 mm verwenden Sie am besten Hartmetall YG8 als Werkzeugmaterial. Bei der Bearbeitung von Löchern mit einem Durchmesser von weniger als 5 mm können Schnellstahlbohrer (wie M42 oder B201) mit einer Härte von mehr als 63 HRC verwendet werden. Wenn die Lochtiefe weniger als das Doppelte des Durchmessers beträgt, wird ein Bit (kurzer Typ) verwendet. Wenn die Lochtiefe mehr als das Doppelte des Durchmessers beträgt, wird ein Spiralbohrer verwendet. Geometrische Parameter des Bohrers: λ = 0 ° ~ 3 °, αc = 13 ° ~ 15 °, 2φ = 120 ° ~ 130 °.
des Bohrers, um die Bildung von Spänen zu erleichtern.
Die Breite des Führungskantenbandes kann je nach Durchmesser des Bohrers auf 0,1 - 0,3 mm reduziert werden, die Querkante kann auf 0,1D geschliffen werden. und der Spitzenwinkel des Doppelkantenschleifens kann 2φ = 130 ° ~ 140 °, 2φ = 70 ° ~ 80 ° betragen.
Tabelle 4 sind die geometrischen Parameter des Doppelpunkt-Bohrmeißel.
Geometrische Parameter des Doppelflankenbits
Meißeldurchmesser (mm) - Spitzenwinkel 2_ - zweiter Spitzenwinkel 2_0 - Rückwinkel der zweiten Kante a
> 3 ~ 6-130 ° ~ 140 ° ~ 80 ° ~ 140 ° ~ 12 ° ~ 18 ° -
> 6 ~ 10-130 ° ~ 140 ° ~ 80 ° ~ 140 ° ~ 12 ° ~ 18 ° -
> 10 ~ 18-125 ° ~ 140 ° ~ 80 ° ~ 140 ° ~ 12 ° ~ 18 ° -
> 18 ~ 30-125 ° ~ 140 ° ~ 80 ° ~ 140 ° ~ 12 ° ~ 18 ° -
(2) Schnittmenge
Hartmetallbohrer: v = 9 ~ 15 m / min, f = 0,05 ~ 0,2 mm / r; Schnellstahlbohrer v = 4 ~ 5 m / min, f = 0,05 ~ 0,3 mm / r.
(3) Beim Bohren von tiefen Löchern oder Löchern mit kleinem Durchmesser kann ein manueller Vorschub durchgeführt werden.
Der Bohrer muss während des Bohrens regelmäßig aus dem Loch gezogen werden, um die Späne zu entfernen. Um die starke Abnutzung des Bohrers zu vermeiden, sollte der Bohrer nicht im Loch bleiben und die Bohrerkante reibt die Oberfläche, wodurch das Werkstück verhärtet und der Bohrer stumpf wird. Der Kühlschmierstoff muss beim Bohren ausreichend zugeführt werden. Im Allgemeinen verwenden Sie Sojaöl, falls erforderlich, kann Französisch OLTIP Bohren und Gewindebohren Spezialöl hinzufügen. Um die Steifigkeit des Prozesssystems zu verbessern, befestigen Sie die Bohrmatrize auf der Werkbank. Die Bohrmatrize sollte sich so nah wie möglich an der Bearbeitungsoberfläche befinden, um den Bohrer zu kürzen.
Die Verschleißrate an der hinteren Ecke des Meißels beträgt 0,4 bis 0,5 mm, was als Kriterium für die Stumpfheit des Bohrers herangezogen wird.
(4) Bohrbeispiele:
Ein Bohrer aus Molybdän-Schnellarbeitsstahl wird zum Bohren von α + β TC4-Titanlegierungswerkstücken verwendet. Der Durchmesser des Bohrers beträgt D = 6,35 mm und die Tiefe des Lochs beträgt H = 12,7 mm.
Die Schnittparameter v = 11,6 m / min und f = 0,127 mm / r wurden ausgewählt und mit einer Emulsion gekühlt.
Die Werkzeughaltbarkeit T basiert auf der Verschleißbreite h = 0,38 mm, und jeder Bohrer kann 260 Löcher bohren, um hervorragende Ergebnisse zu erzielen.
Beim Schneiden von Titanlegierungen können sich nur im Bereich der Schnittgeschwindigkeit von 1-5 mm / min Späne bilden. Unter allgemeinen Produktionsbedingungen treten daher beim Schneiden von Titanlegierungen keine Späne auf. Der Reibungskoeffizient zwischen dem Werkstück und dem Werkzeug ist nicht sehr groß und es ist leicht, eine gute Oberflächenqualität zu erzielen. Die Verwendung eines Kühlschmiermittels hat keinen Einfluss auf die Verbesserung der Mikrogeometrie der Oberfläche der Titanlegierung. Die Rauheit der unteren Oberfläche der bearbeiteten Titanlegierung ist auf das Fehlen von Aufbauschneiden am Werkzeug zurückzuführen. Die Verwendung von Kühlschmierstoffen hat keinen Einfluss auf die Verbesserung der Mikrogeometrie von Titanlegierungsoberflächen. Die geringe Rauheit der bearbeiteten Oberfläche beim Schneiden von Titanlegierungen ist auf die Abwesenheit von Spantumoren am Werkzeug zurückzuführen.
Um jedoch die Schnittbedingungen zu verbessern, die Schnitttemperaturen zu senken, die Lebensdauer des Werkzeugs zu erhöhen und die Brandgefahr zu beseitigen, ist es erforderlich, während der Verarbeitung eine große Menge löslichen Kühlmittels zu verwenden.
Normalerweise tritt bei der Bearbeitung von Teilen aus Titanlegierungen kein Zünd- und Verbrennungsphänomen auf, während es beim Mikroschneidvorgang zu einem Zünd- und Verbrennungsphänomen kommt. Um diese Gefahr zu vermeiden, sollte das Kühlmittel in großen Mengen verwendet werden. Entfernen Sie die Späne rechtzeitig von den Werkzeugmaschinen. Feuerlöscheinrichtungen sind vorhanden; Ersetzen Sie stumpfe Messer rechtzeitig. Wenn die Oberfläche des Werkstücks verschmutzt ist, können leicht Funken entstehen. Zu diesem Zeitpunkt muss die Schnittgeschwindigkeit reduziert werden. Im Vergleich zu dünnen Spänen ist es bei dicken Spänen nicht einfach, Funken zu erzeugen. Daher muss das Schnittvolumen erhöht werden, wodurch die Temperatur nicht so schnell ansteigt, wie die Schnittgeschwindigkeit zunimmt.
Auswahlkriterien für die Bearbeitung von Titanlegierungen: Unter dem Gesichtspunkt der Absenkung der Schnitttemperatur sollten eine niedrigere Schnittgeschwindigkeit und eine größere Schnittmenge angewendet werden. Aufgrund der hohen Schnitttemperatur nimmt die Titanlegierung Sauerstoff und Wasserstoff aus der Atmosphäre auf, wodurch die Oberfläche des Werkstücks hart und spröde wird und das Werkzeug stark abgenutzt wird. Daher muss während der Bearbeitung die Temperatur der Werkzeugspitze auf einer geeigneten Temperatur gehalten werden, um eine Übertemperatur zu vermeiden.
Beim Drehen von harthäutigen Titanlegierungswerkstücken mit dem YG8-Drehwerkzeug unter intermittierenden Schnittbedingungen werden folgende Schnittparameter empfohlen: v = 15 ~ 28 m / min, f = 0,25 ~ 0,35 mm / r, ap = 1 ~ 3 mm.
Bei Verwendung eines YG3-Drehwerkzeugs zum Bearbeiten eines Titanlegierungs-Werkstücks unter kontinuierlichen Schneidebedingungen beträgt die empfohlene Schneidemenge: v = 50 ~ 70 m / min, f = 0,1 ~ 0,2 mm / r, ap = 0,3 ~ 1 mm. Tabelle 2 zeigt den verfügbaren Schneidumfang zum Drehen von Titanlegierungen.
Schnittmenge beim Drehen von Titanlegierungen:
Verfahrenseigenschaften - Titanlegierungsmaterial - Härte - Schneidzugabe (mm) - Schneidgeschwindigkeit (mm / min) - Werkzeuggehen
Oxid haut dicke
Grobdrehen: TA1 ~ 7, TC1 ~ 2-Soft->
Grobdrehen: TA8, TC3 ~ 8-Medium->
Grobdrehen : TC9 ~ 10, TB1 ~ 2 - Schwer ->
Fertig drehen : TA1 ~ 7, TC1 ~ 2-Soft
Fertig drehen: TA8, TC3-8-in
Fertig drehen: TC9-10, TB1-2-Hard
Der TC4 (Härte HB320 ~ 360) wird mit dem YG6X-Drehwerkzeug gedreht, und die optimale Schnittgeschwindigkeit beträgt 60 mm / min, wenn ap = 1 mm und f = 0,1 mm / r. Auf dieser Basis ist in Tabelle 3 die Schnittgeschwindigkeit bei unterschiedlicher Schnittmenge und Schnitttiefe angegeben.
Schnittgeschwindigkeit beim Drehen der Titanlegierung TC4
Ein typisches Drehwerkzeug zur Bearbeitung von Titanlegierungen weist folgende Eigenschaften auf:
Das Klingenmaterial ist YG6X, YG10HT; Der Spanwinkel ist klein, im Allgemeinen & ggr; 0 = 4 ° ~ 6 °, was die Festigkeit des Messerkopfs erhöht; Es gibt negative Fasen von f = 0,05 bis 0,1 mm, um die Stärke der Klinge zu verbessern. Der hintere Winkel ist groß, im Allgemeinen α0 = 14 ° bis 16 °, um die Reibung dahinter zu verringern und die Haltbarkeit des Werkzeugs zu verbessern; Im Allgemeinen ist es nicht erlaubt, scharfe Ecken oder Übergangskanten zu schleifen, und die abgerundeten Ecken der Schleifkante sind r = 0,5 mm, und das Grobdrehen kann r = 1 ~ 2 mm erreichen, um die Festigkeit der Schneidkante zu verbessern; Beim Fertigdrehen oder Drehen dünnwandiger Teile ist der Hauptabweichungswinkel des Werkzeugs groß, im Allgemeinen 75 ° ~ 90 °.
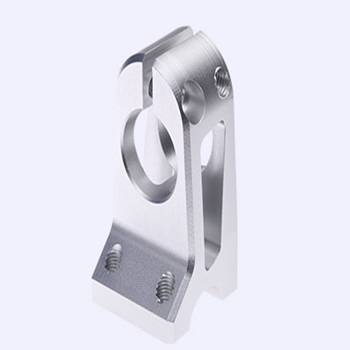
Schnittmenge:
Grobe Drehung: v = 40 ~ 50 m / min, f = 0,2 ~ 0,3 mm / r, ap = 3 ~ 5 mm.
Halbfertigdrehen: v = 40 ~ 45 m / min, f = 0,2 ~ 0,3 mm / r, ap = 1 ~ 2 mm.
Feines Drehen: v = 50 ~ 55 m / min, f = 0,1 ~ 0,15 mm / r, ap = 0,2 ~ 0,5 mm.
Das Kühlen mit Emulsionen kann die Werkzeughaltbarkeit effektiv verbessern.
Die hohe Verschleißfestigkeit und Härte des Messerkopfes unter der Voraussetzung, dass die Festigkeit des Messerkopfes gewährleistet ist, ist der Schlüssel für die rationelle Verarbeitung von Titanlegierungen. Daher sollte die ausgewählte YG6X-Klinge nach dem Schärfen (Zurückfasen) mit Diamant oder SiC-Schleifstein poliert werden, um das Schärfen der Schnittfuge zu vermeiden und die Festigkeit der Klinge zu verbessern.
Beim Grobdrehen von unregelmäßigen schwarzen Lederwerkstücken wird die Klinge im Allgemeinen um 3 ° bis + 5 ° geneigt geschliffen. Beim Feindrehen tritt im Allgemeinen keine Messerneigung auf, und der Werkzeugverschleiß ist zu diesem Zeitpunkt hauptsächlich die Haftung (Verklebung) der Spanfläche.
Ein solches typisches Drehwerkzeug kann das Problem vernünftigerweise lösen, dass die Materialaktivität mit zunehmender Temperatur zunimmt und die Wärmeleitfähigkeit schlecht ist, wenn die Titanlegierung verarbeitet wird, und somit die Werkzeughaltbarkeit stark verbessert wird.
3.2 Bohren
Beim Grobdrehen von unregelmäßigen schwarzen Lederwerkstücken wird die Klinge im Allgemeinen um 3 ° bis + 5 ° geneigt geschliffen. Beim Feindrehen tritt im Allgemeinen keine Messerneigung auf, und der Werkzeugverschleiß ist zu diesem Zeitpunkt hauptsächlich die Haftung (Verklebung) der Spanfläche.
Ein solches typisches Drehwerkzeug kann das Problem vernünftigerweise lösen, dass die Materialaktivität mit zunehmender Temperatur zunimmt und die Wärmeleitfähigkeit schlecht ist, wenn die Titanlegierung verarbeitet wird, und somit die Werkzeughaltbarkeit stark verbessert wird.
3.2 Bohren
(1) Bohren Auswahl: Für Bohrer mit einem Durchmesser von mehr als 5 mm verwenden Sie am besten Hartmetall YG8 als Werkzeugmaterial. Bei der Bearbeitung von Löchern mit einem Durchmesser von weniger als 5 mm können Schnellstahlbohrer (wie M42 oder B201) mit einer Härte von mehr als 63 HRC verwendet werden. Wenn die Lochtiefe weniger als das Doppelte des Durchmessers beträgt, wird ein Bit (kurzer Typ) verwendet. Wenn die Lochtiefe mehr als das Doppelte des Durchmessers beträgt, wird ein Spiralbohrer verwendet. Geometrische Parameter des Bohrers: λ = 0 ° ~ 3 °, αc = 13 ° ~ 15 °, 2φ = 120 ° ~ 130 °.
des Bohrers, um die Bildung von Spänen zu erleichtern.
Die Breite des Führungskantenbandes kann je nach Durchmesser des Bohrers auf 0,1 - 0,3 mm reduziert werden, die Querkante kann auf 0,1D geschliffen werden. und der Spitzenwinkel des Doppelkantenschleifens kann 2φ = 130 ° ~ 140 °, 2φ = 70 ° ~ 80 ° betragen.
Tabelle 4 sind die geometrischen Parameter des Doppelpunkt-Bohrmeißel.
Geometrische Parameter des Doppelflankenbits
Meißeldurchmesser (mm) - Spitzenwinkel 2_ - zweiter Spitzenwinkel 2_0 - Rückwinkel der zweiten Kante a
> 3 ~ 6-130 ° ~ 140 ° ~ 80 ° ~ 140 ° ~ 12 ° ~ 18 ° -
> 6 ~ 10-130 ° ~ 140 ° ~ 80 ° ~ 140 ° ~ 12 ° ~ 18 ° -
> 10 ~ 18-125 ° ~ 140 ° ~ 80 ° ~ 140 ° ~ 12 ° ~ 18 ° -
> 18 ~ 30-125 ° ~ 140 ° ~ 80 ° ~ 140 ° ~ 12 ° ~ 18 ° -
(2) Schnittmenge
Hartmetallbohrer: v = 9 ~ 15 m / min, f = 0,05 ~ 0,2 mm / r; Schnellstahlbohrer v = 4 ~ 5 m / min, f = 0,05 ~ 0,3 mm / r.
(3) Beim Bohren von tiefen Löchern oder Löchern mit kleinem Durchmesser kann ein manueller Vorschub durchgeführt werden.
Der Bohrer muss während des Bohrens regelmäßig aus dem Loch gezogen werden, um die Späne zu entfernen. Um die starke Abnutzung des Bohrers zu vermeiden, sollte der Bohrer nicht im Loch bleiben und die Bohrerkante reibt die Oberfläche, wodurch das Werkstück verhärtet und der Bohrer stumpf wird. Der Kühlschmierstoff muss beim Bohren ausreichend zugeführt werden. Im Allgemeinen verwenden Sie Sojaöl, falls erforderlich, kann Französisch OLTIP Bohren und Gewindebohren Spezialöl hinzufügen. Um die Steifigkeit des Prozesssystems zu verbessern, befestigen Sie die Bohrmatrize auf der Werkbank. Die Bohrmatrize sollte sich so nah wie möglich an der Bearbeitungsoberfläche befinden, um den Bohrer zu kürzen.
Die Verschleißrate an der hinteren Ecke des Meißels beträgt 0,4 bis 0,5 mm, was als Kriterium für die Stumpfheit des Bohrers herangezogen wird.
(4) Bohrbeispiele:
Ein Bohrer aus Molybdän-Schnellarbeitsstahl wird zum Bohren von α + β TC4-Titanlegierungswerkstücken verwendet. Der Durchmesser des Bohrers beträgt D = 6,35 mm und die Tiefe des Lochs beträgt H = 12,7 mm.
Die Schnittparameter v = 11,6 m / min und f = 0,127 mm / r wurden ausgewählt und mit einer Emulsion gekühlt.
Die Werkzeughaltbarkeit T basiert auf der Verschleißbreite h = 0,38 mm, und jeder Bohrer kann 260 Löcher bohren, um hervorragende Ergebnisse zu erzielen.
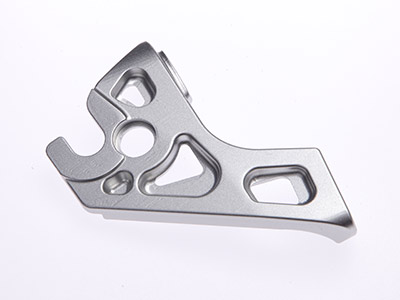