Effiziente Verarbeitung von Aluminium-Motor Zylinderbohrung Aufbohren, Fertig Bohren
Da die gusseiserne Zylinderlaufbuchse im Rohling vorgegossen ist. Die Grob-, Fein- und Teillochbearbeitung der Zylinderbohrung konzentriert sich im selben Prozess und ist somit ein Verarbeitungsengpass für die Vollaluminium-Motorblockfertigung. Zu diesem Zweck senkt der Einsatz der neuen Schneidetheorie zur rationellen Optimierung des Werkzeugs nicht nur die Produktionskosten, sondern erzielt auch eine effiziente Bearbeitung bei geringem Stromverbrauch.
Der Motor (siehe Abbildung 1) besteht aus Vollaluminium, das die Vorteile des geringen Gewichts, der guten Wärmeableitung und des niedrigen Energieverbrauchs aufweist. Bei der Verarbeitung, dem Gießen des Hauptölkanals, dem Brechen der Verbindung usw. werden eine Reihe neuer Verfahren angewendet; Die Produktionslinie folgt einem hochflexiblen Designkonzept, und die Bearbeitungsausrüstung basiert hauptsächlich auf dem Bearbeitungszentrum.
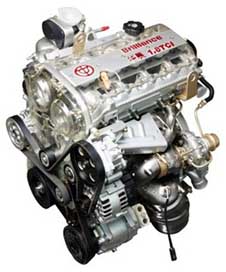
Abbildung 1 Turbomotor der Brilliance 1.8T-Serie
Die 1.8T-Zylinderproduktionslinie ist eine vollflexible Produktionslinie, und alle Verarbeitungsgeräte mit Ausnahme der Honmaschine sind Bearbeitungszentren (siehe Abbildung 2). Der Motorblock (siehe Abbildung 3) besteht aus Aluminium, und die Zylinderlaufbuchse aus Gusseisen ist im Rohling vorgegossen. Die Rohloch- und Teillochbearbeitung werden in demselben Prozess konzentriert. Da Aluminiumlegierung ein leicht zu verarbeitendes Material ist, ist es leicht, eine hocheffiziente Verarbeitung zu erreichen, und Gusseisen ist ein allgemeines Material mit allgemeinen Verarbeitungseigenschaften, und die Bearbeitbarkeit der beiden Materialien variiert stark. Daher wird die Grobbearbeitung der Zylinderbohrung zum Verarbeitungsengpass der Zylinderfertigungsstraße, was die Produktionskapazität der Zylinderfertigungsstraße einschränkt.
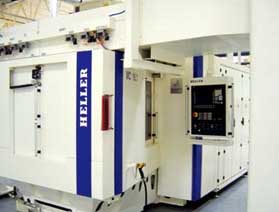
Abbildung 2 Bearbeitungszentrum auf der Zylinderfertigungsstraße
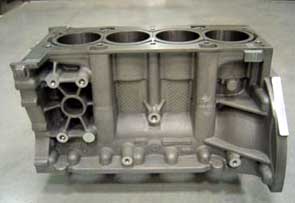
Abbildung 3 Der Motorblock besteht aus Aluminium
Eingehende Analyse der spezifischen Bedingungen der Schruppbearbeitung der Zylinderbohrung, um einen besseren Bearbeitungsplan zu erhalten und die Schruppeffizienz der Zylinderbohrung zu verbessern.
Die tatsächliche Bearbeitungssituation der rauen Zylinderbohrung ist: Die Bearbeitung erfolgt mit einer Feile mit drei Klingen (siehe Abbildung 4), einem Anstellwinkel von 75 ° und einem vorderen Winkel von 0 °. Die Klinge besteht aus CBN-Material.
Spezifische Schnittparameter: Schnittgeschwindigkeit = 400 m / min, Vorschub pro Zahn = 0,18 mm, Schnitttiefe = 2,5 mm, Bearbeitungszeit 42,5 s.
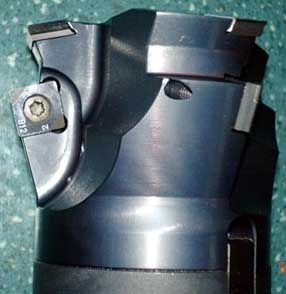
Abbildung 4 Das traditionelle Werkzeug für das raue Loch der Zylinderbohrung - Dreiblattfeile
Für das Probeschneiden wurden verschiedene Verarbeitungsschemata entwickelt. Nach der Analyse der Testergebnisse wird angenommen, dass es zwei Hauptgründe für die Einschränkung der Effizienz der Zylinderbohrungsbearbeitung gibt:
1, langweilige Vibration
Die bei rauer Zylinderbohrung erzeugte Schneidschwingung nimmt mit zunehmender Schnittgeschwindigkeit zu, wodurch die Erhöhung der Schnittgeschwindigkeit begrenzt wird. Darüber hinaus führt die Schneidevibration dazu, dass die Klinge leicht beschädigt wird und der Werkzeugwechsel häufig erfolgt, was zu einer Verringerung der Startrate der Vorrichtung führt.
2, die Spindellast ist zu hoch
Der 1.8T-Motor ist ein Vollaluminiummotor, und die Bearbeitung erfolgt hauptsächlich in Aluminium. Um Energie zu sparen und die Anlagenkapazität zu reduzieren, wird in der Produktionslinie kein Hochleistungsbearbeitungszentrum eingesetzt. Daher wird die Maschine bei der Bearbeitung der Gusszylinderbohrung mit Volllast betrieben. Aufgrund von Leistungsbeschränkungen der Maschine können die Materialabtragsraten nicht durch Erhöhen der Vorschubrate oder Erhöhen der Anzahl der Schneideinsätze erhöht werden.
Um die Schnittkraft zu verringern, müssen die Schneidvibrationen beseitigt und die Bearbeitungseffizienz verbessert werden. Wir haben mit einem Werkzeughersteller zusammengearbeitet, um ein neues Werkzeug zum Schruppen von Zylinderlöchern zu entwickeln (siehe Abbildung 5). Gegenüber herkömmlichen Bohrwerkzeugen bietet das neue Bohrwerkzeug folgende Vorteile:
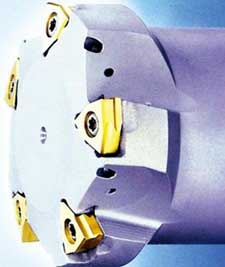
Abbildung 5 Neues Schruppbohrwerkzeug zur Bearbeitung der Zylinderbohrung
I. den Schnittwinkel
1, positiver Rechenschnitt
Es wird allgemein angenommen, dass Werkzeuge, die spröde Materialien wie Gusseisen verarbeiten, einen negativen Spanwinkel verwenden sollten, um die Werkzeugfestigkeit zu erhöhen und eine Beschädigung des Werkzeugs durch Abplatzen zu verhindern. Unter den verschiedenen geometrischen Parametern des Werkzeugs hat der Spanwinkel jedoch den größten Einfluss auf die Schnittkraft. Je gleich die Bedingungen sind, desto größer ist der Spanwinkel des Werkzeugs und desto geringer ist die Schnittkraft.
Mit der Verbesserung der Werkzeugmaschinenstabilität und dem Aufkommen verschiedener neuer Werkzeugmaterialien ist es möglich geworden, spröde Materialien mit Werkzeugen mit großem Spanwinkel zu bearbeiten, so dass die neue Feile einen positiven Spanwinkel von 10 ° verwendet. Im Vergleich zu herkömmlichen Bohrwerkzeugen mit einem Spanwinkel von 0 ° oder einem negativen Spanwinkel erzeugt der Spanwinkel des positiven Spanwinkels weniger Schnittkraft. Die Schneidkraft kann wirksam reduziert werden, ohne die Schneidparameter zu verringern, was nicht nur das Schneiden leichter macht, sondern auch das Auftreten von Schneidvibrationen wirksam verringert.
2, 90 ° Steigungswinkel
Die radiale Schneidkomponente ist die Hauptursache für Schneidvibrationen. Je größer die radiale Komponente ist, desto wahrscheinlicher ist es, dass sie Vibrationen verursacht. Das neue Bohrwerkzeug verwendet einen 90 ° -Schneidwinkel und erzeugt keine radiale Schneidkomponente an der Hauptschneide. Im Vergleich zu Werkzeugen mit kleinen Anstellwinkeln wird die radiale Schneidkomponente stark reduziert, was den Schneidprozess stabiler macht.
II. Methode zum Festklemmen der Klinge
Bei Verwendung einer supergehärteten Klinge wie CBN oder Cermet in der normalen Spannmethode ist es unmöglich, einen positiven Spanwinkel auf die Klinge anzuwenden, und ein positiver Spanwinkel auf das Werkzeug erhöht die Schwierigkeit beim Einsetzen und Einstellen der Klinge.
Im Vergleich zu herkömmlichen Spannklingen können vertikale Klingen leicht Klingen mit großen Spanwinkeln erzeugen, und die Klingen können größeren Schnittkräften standhalten und die Werkzeugzuverlässigkeit verbessern.
Die Spanfläche des Vertikaleinsatzes kommt nicht mit anderen Teilen oder Teilen des Werkzeugs in Berührung. Die Konstruktion der Spannut ist begrenzt und die Optimierung ist einfacher.
Verglichen mit dem gewöhnlichen Spanntyp der Klinge hat die vertikale Klinge in den meisten Fällen eine bessere Spanbrechwirkung, einen angemesseneren Spanraum, eine glattere Spanentfernung und eine einfachere Erzielung eines stabilen Verarbeitungsprozesses. Somit wird durch vertikalen klemmend befestigt die neue Bohrwerkzeugs Klinge.
III. Klingenmaterial und -struktur
Keramikwerkzeuge sind ein neuartiges Werkstoffwerkzeug in der modernen Zerspanung. Es zeichnet sich durch hohe Härte, hohe Festigkeit, hohe Rothärte, hohe Verschleißfestigkeit, hervorragende chemische Stabilität und geringen Reibungskoeffizienten aus. In den letzten Jahren wurden durch die Verwendung verschiedener Additive und die Aufbringung feiner Partikel die Bruchzähigkeit und Schlagzähigkeit von Keramikeinsätzen stark verbessert. Es sind Keramiktypen entstanden, die zum Schruppen unter Schlagbeanspruchung eingesetzt werden können. Der Bohrprozess ist ein kontinuierlicher Schneidprozess, und während des Schneidprozesses werden keine Stöße erzeugt, sodass eine Keramikklinge auch für die Schruppbearbeitung verwendet werden kann. Keramikwerkzeuge haben im Vergleich zu CBN-Werkzeugen einen geringeren Reibungskoeffizienten und erzeugen unter gleichen Bedingungen weniger Schnittkräfte. Daher wird beim neuen Bohrwerkzeug kein CBN-Einsatz verwendet, und es wird ein Keramikeinsatz ausgewählt, der für ein stabiles Schneiden günstiger ist.
Damit die Keramikklinge eine ausreichende Festigkeit aufweist. Nach mehreren Vergleichstests wurde festgestellt, dass die Klinge eine W-förmige Klinge mit einem Klingenwinkel von 80 ° einnimmt, der Werkzeugnasenradius 0,8 mm beträgt und die Schneide und die Werkzeugspitze passiviert sind. Die passivierte Klinge eliminiert mikroskopische Defekte in der Schneide, was nicht nur die Standzeit des Werkzeugs verlängert, sondern auch die Festigkeit der Schneide erhöht und die Stabilität des Schneidprozesses verbessert.
Entsprechend den Eigenschaften des neuen Bohrwerkzeugs wurden unterschiedliche Verarbeitungsparameter zur Durchführung des Vergleichsversuchs herangezogen und schließlich die Verarbeitungsparameter wie folgt bestimmt:
Schnittgeschwindigkeit = 500 m / min, Vorschub pro Zahn = 0,12 mm; Die Schnitttiefe ist unkontrollierbar und nicht eingestellt. Wenn das neue Bohrwerkzeug die Anzahl der Schneiden und die Schnittgeschwindigkeit erhöht, verringert sich die Bearbeitungszeit auf 30,5 s und die Bearbeitungseffizienz erhöht sich um 39%. Aufgrund der Antivibrationsmaßnahmen, die das neue Werkzeug in verschiedenen Aspekten anwendet, wird die Stabilität des Bearbeitungsprozesses verbessert und die anormale Beschädigung der Klinge wird im Wesentlichen beseitigt, wodurch die Anzahl der Werkzeugwechsel verringert und die Startrate der Vorrichtung erhöht wird. Basierend auf den obigen beiden Faktoren wird die Produktionseffizienz des OP20-Prozesses, bei dem die Zylinderbohrung rau ist, um ungefähr 6% erhöht.
Durch die Analyse des Gebrauchseffekts des neuen Bohrwerkzeugs wird die gute Leistung des neuen Werkzeugmaterials voll ausgenutzt. Die richtige Optimierung des Werkzeugs mit der neuen Schneidetheorie senkt nicht nur die Produktionskosten, sondern ermöglicht auch eine effiziente Bearbeitung bei geringem Stromverbrauch.
Der Motor (siehe Abbildung 1) besteht aus Vollaluminium, das die Vorteile des geringen Gewichts, der guten Wärmeableitung und des niedrigen Energieverbrauchs aufweist. Bei der Verarbeitung, dem Gießen des Hauptölkanals, dem Brechen der Verbindung usw. werden eine Reihe neuer Verfahren angewendet; Die Produktionslinie folgt einem hochflexiblen Designkonzept, und die Bearbeitungsausrüstung basiert hauptsächlich auf dem Bearbeitungszentrum.
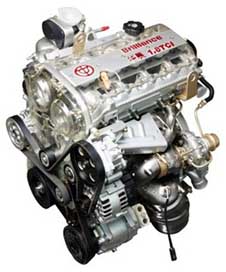
Abbildung 1 Turbomotor der Brilliance 1.8T-Serie
Die 1.8T-Zylinderproduktionslinie ist eine vollflexible Produktionslinie, und alle Verarbeitungsgeräte mit Ausnahme der Honmaschine sind Bearbeitungszentren (siehe Abbildung 2). Der Motorblock (siehe Abbildung 3) besteht aus Aluminium, und die Zylinderlaufbuchse aus Gusseisen ist im Rohling vorgegossen. Die Rohloch- und Teillochbearbeitung werden in demselben Prozess konzentriert. Da Aluminiumlegierung ein leicht zu verarbeitendes Material ist, ist es leicht, eine hocheffiziente Verarbeitung zu erreichen, und Gusseisen ist ein allgemeines Material mit allgemeinen Verarbeitungseigenschaften, und die Bearbeitbarkeit der beiden Materialien variiert stark. Daher wird die Grobbearbeitung der Zylinderbohrung zum Verarbeitungsengpass der Zylinderfertigungsstraße, was die Produktionskapazität der Zylinderfertigungsstraße einschränkt.
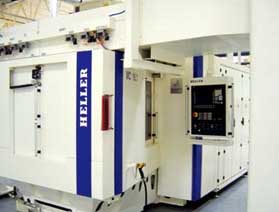
Abbildung 2 Bearbeitungszentrum auf der Zylinderfertigungsstraße
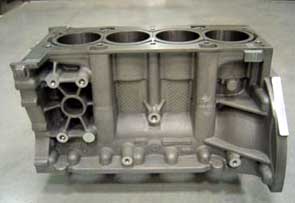
Abbildung 3 Der Motorblock besteht aus Aluminium
Die tatsächliche Bearbeitungssituation der rauen Zylinderbohrung ist: Die Bearbeitung erfolgt mit einer Feile mit drei Klingen (siehe Abbildung 4), einem Anstellwinkel von 75 ° und einem vorderen Winkel von 0 °. Die Klinge besteht aus CBN-Material.
Spezifische Schnittparameter: Schnittgeschwindigkeit = 400 m / min, Vorschub pro Zahn = 0,18 mm, Schnitttiefe = 2,5 mm, Bearbeitungszeit 42,5 s.
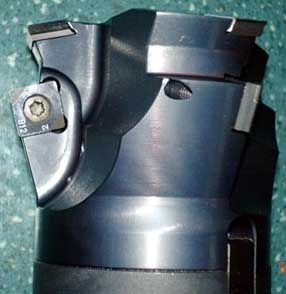
Abbildung 4 Das traditionelle Werkzeug für das raue Loch der Zylinderbohrung - Dreiblattfeile
Für das Probeschneiden wurden verschiedene Verarbeitungsschemata entwickelt. Nach der Analyse der Testergebnisse wird angenommen, dass es zwei Hauptgründe für die Einschränkung der Effizienz der Zylinderbohrungsbearbeitung gibt:
1, langweilige Vibration
Die bei rauer Zylinderbohrung erzeugte Schneidschwingung nimmt mit zunehmender Schnittgeschwindigkeit zu, wodurch die Erhöhung der Schnittgeschwindigkeit begrenzt wird. Darüber hinaus führt die Schneidevibration dazu, dass die Klinge leicht beschädigt wird und der Werkzeugwechsel häufig erfolgt, was zu einer Verringerung der Startrate der Vorrichtung führt.
2, die Spindellast ist zu hoch
Der 1.8T-Motor ist ein Vollaluminiummotor, und die Bearbeitung erfolgt hauptsächlich in Aluminium. Um Energie zu sparen und die Anlagenkapazität zu reduzieren, wird in der Produktionslinie kein Hochleistungsbearbeitungszentrum eingesetzt. Daher wird die Maschine bei der Bearbeitung der Gusszylinderbohrung mit Volllast betrieben. Aufgrund von Leistungsbeschränkungen der Maschine können die Materialabtragsraten nicht durch Erhöhen der Vorschubrate oder Erhöhen der Anzahl der Schneideinsätze erhöht werden.
Um die Schnittkraft zu verringern, müssen die Schneidvibrationen beseitigt und die Bearbeitungseffizienz verbessert werden. Wir haben mit einem Werkzeughersteller zusammengearbeitet, um ein neues Werkzeug zum Schruppen von Zylinderlöchern zu entwickeln (siehe Abbildung 5). Gegenüber herkömmlichen Bohrwerkzeugen bietet das neue Bohrwerkzeug folgende Vorteile:
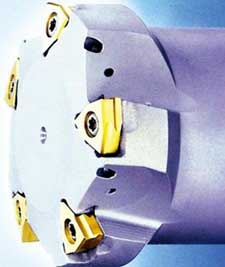
Abbildung 5 Neues Schruppbohrwerkzeug zur Bearbeitung der Zylinderbohrung
I. den Schnittwinkel
1, positiver Rechenschnitt
Es wird allgemein angenommen, dass Werkzeuge, die spröde Materialien wie Gusseisen verarbeiten, einen negativen Spanwinkel verwenden sollten, um die Werkzeugfestigkeit zu erhöhen und eine Beschädigung des Werkzeugs durch Abplatzen zu verhindern. Unter den verschiedenen geometrischen Parametern des Werkzeugs hat der Spanwinkel jedoch den größten Einfluss auf die Schnittkraft. Je gleich die Bedingungen sind, desto größer ist der Spanwinkel des Werkzeugs und desto geringer ist die Schnittkraft.
Mit der Verbesserung der Werkzeugmaschinenstabilität und dem Aufkommen verschiedener neuer Werkzeugmaterialien ist es möglich geworden, spröde Materialien mit Werkzeugen mit großem Spanwinkel zu bearbeiten, so dass die neue Feile einen positiven Spanwinkel von 10 ° verwendet. Im Vergleich zu herkömmlichen Bohrwerkzeugen mit einem Spanwinkel von 0 ° oder einem negativen Spanwinkel erzeugt der Spanwinkel des positiven Spanwinkels weniger Schnittkraft. Die Schneidkraft kann wirksam reduziert werden, ohne die Schneidparameter zu verringern, was nicht nur das Schneiden leichter macht, sondern auch das Auftreten von Schneidvibrationen wirksam verringert.
2, 90 ° Steigungswinkel
Die radiale Schneidkomponente ist die Hauptursache für Schneidvibrationen. Je größer die radiale Komponente ist, desto wahrscheinlicher ist es, dass sie Vibrationen verursacht. Das neue Bohrwerkzeug verwendet einen 90 ° -Schneidwinkel und erzeugt keine radiale Schneidkomponente an der Hauptschneide. Im Vergleich zu Werkzeugen mit kleinen Anstellwinkeln wird die radiale Schneidkomponente stark reduziert, was den Schneidprozess stabiler macht.
II. Methode zum Festklemmen der Klinge
Bei Verwendung einer supergehärteten Klinge wie CBN oder Cermet in der normalen Spannmethode ist es unmöglich, einen positiven Spanwinkel auf die Klinge anzuwenden, und ein positiver Spanwinkel auf das Werkzeug erhöht die Schwierigkeit beim Einsetzen und Einstellen der Klinge.
Im Vergleich zu herkömmlichen Spannklingen können vertikale Klingen leicht Klingen mit großen Spanwinkeln erzeugen, und die Klingen können größeren Schnittkräften standhalten und die Werkzeugzuverlässigkeit verbessern.
Die Spanfläche des Vertikaleinsatzes kommt nicht mit anderen Teilen oder Teilen des Werkzeugs in Berührung. Die Konstruktion der Spannut ist begrenzt und die Optimierung ist einfacher.
Verglichen mit dem gewöhnlichen Spanntyp der Klinge hat die vertikale Klinge in den meisten Fällen eine bessere Spanbrechwirkung, einen angemesseneren Spanraum, eine glattere Spanentfernung und eine einfachere Erzielung eines stabilen Verarbeitungsprozesses. Somit wird durch vertikalen klemmend befestigt die neue Bohrwerkzeugs Klinge.
III. Klingenmaterial und -struktur
Keramikwerkzeuge sind ein neuartiges Werkstoffwerkzeug in der modernen Zerspanung. Es zeichnet sich durch hohe Härte, hohe Festigkeit, hohe Rothärte, hohe Verschleißfestigkeit, hervorragende chemische Stabilität und geringen Reibungskoeffizienten aus. In den letzten Jahren wurden durch die Verwendung verschiedener Additive und die Aufbringung feiner Partikel die Bruchzähigkeit und Schlagzähigkeit von Keramikeinsätzen stark verbessert. Es sind Keramiktypen entstanden, die zum Schruppen unter Schlagbeanspruchung eingesetzt werden können. Der Bohrprozess ist ein kontinuierlicher Schneidprozess, und während des Schneidprozesses werden keine Stöße erzeugt, sodass eine Keramikklinge auch für die Schruppbearbeitung verwendet werden kann. Keramikwerkzeuge haben im Vergleich zu CBN-Werkzeugen einen geringeren Reibungskoeffizienten und erzeugen unter gleichen Bedingungen weniger Schnittkräfte. Daher wird beim neuen Bohrwerkzeug kein CBN-Einsatz verwendet, und es wird ein Keramikeinsatz ausgewählt, der für ein stabiles Schneiden günstiger ist.
Damit die Keramikklinge eine ausreichende Festigkeit aufweist. Nach mehreren Vergleichstests wurde festgestellt, dass die Klinge eine W-förmige Klinge mit einem Klingenwinkel von 80 ° einnimmt, der Werkzeugnasenradius 0,8 mm beträgt und die Schneide und die Werkzeugspitze passiviert sind. Die passivierte Klinge eliminiert mikroskopische Defekte in der Schneide, was nicht nur die Standzeit des Werkzeugs verlängert, sondern auch die Festigkeit der Schneide erhöht und die Stabilität des Schneidprozesses verbessert.
Entsprechend den Eigenschaften des neuen Bohrwerkzeugs wurden unterschiedliche Verarbeitungsparameter zur Durchführung des Vergleichsversuchs herangezogen und schließlich die Verarbeitungsparameter wie folgt bestimmt:
Schnittgeschwindigkeit = 500 m / min, Vorschub pro Zahn = 0,12 mm; Die Schnitttiefe ist unkontrollierbar und nicht eingestellt. Wenn das neue Bohrwerkzeug die Anzahl der Schneiden und die Schnittgeschwindigkeit erhöht, verringert sich die Bearbeitungszeit auf 30,5 s und die Bearbeitungseffizienz erhöht sich um 39%. Aufgrund der Antivibrationsmaßnahmen, die das neue Werkzeug in verschiedenen Aspekten anwendet, wird die Stabilität des Bearbeitungsprozesses verbessert und die anormale Beschädigung der Klinge wird im Wesentlichen beseitigt, wodurch die Anzahl der Werkzeugwechsel verringert und die Startrate der Vorrichtung erhöht wird. Basierend auf den obigen beiden Faktoren wird die Produktionseffizienz des OP20-Prozesses, bei dem die Zylinderbohrung rau ist, um ungefähr 6% erhöht.
Durch die Analyse des Gebrauchseffekts des neuen Bohrwerkzeugs wird die gute Leistung des neuen Werkzeugmaterials voll ausgenutzt. Die richtige Optimierung des Werkzeugs mit der neuen Schneidetheorie senkt nicht nur die Produktionskosten, sondern ermöglicht auch eine effiziente Bearbeitung bei geringem Stromverbrauch.