Edelstahl Oberflaechenbehandlung
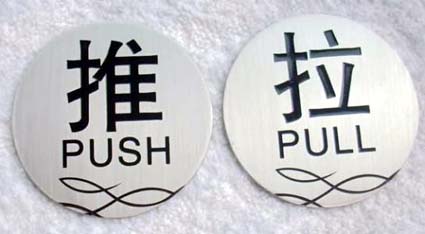
Produkteinführung
1.1.1 Hauptbestandteile von Edelstahl: Enthält in der Regel hochwertige metallische Elemente wie Chrom (Cr), Nickel (Ni), Molybdän (Mo) und Titan (Ti).
1.1.2 Allgemeiner rostfreier Stahl: Chromstahl, der mehr als 12% Cr enthält; Nickel-Chrom-Edelstahl, mit Cr ≥ 18%, mit Ni ≥ 12%.
1.1.3 Klassifizierung von nichtrostendem Hüttenmaterial: Austenitischer nichtrostender Stahl, zum Beispiel: 1Cr18Ni9Ti, 1Cr18Ni11Nb, Cr18Mn8Ni5. Martensitischer rostfreier Stahl, wie zum Beispiel: Cr17, Cr28 und so weiter. Im Allgemeinen als nicht magnetischer Edelstahl und magnetischer Edelstahl bezeichnet.
Ursache der Korrosion
Chemische Korrosion
2.1.1 Oberflächenkontamination: An der Oberfläche des Werkstücks anhaftende Öle, Stäube, Säuren, Laugen und Salze werden unter bestimmten Bedingungen in korrosives Medium umgewandelt, es kommt zu chemischen Reaktionen mit bestimmten Komponenten in den Edelstahlteilen und zu chemischer Korrosion und Rostbildung .
2.1.2 Kratzer auf der Oberfläche: Alle Arten von Kratzern beschädigen den Passivierungsfilm, so dass die Schutzwirkung des rostfreien Stahls reduziert wird und leicht mit chemischen Medien reagiert, was zu chemischer Korrosion und Rost führt.
2.1.3 Reinigung: Nach dem Beizen und Passivieren ist die Reinigung nicht sauber und es verbleibt die Restflüssigkeit, die Edelstahlteile direkt angreift (chemische Korrosion).
Elektrochemische Korrosion
2.2.1 Kohlenstoffstahlverschmutzung:
Das durch den Kontakt mit dem Kohlenstoffstahlelement verursachte zerkratzte und korrosive Medium bildet eine Primärbatterie und erzeugt eine elektrochemische Korrosion.
2.2.2 Schneiden:
Schneiden von Schlacke, Spritzeradhäsion an den Rost und andere korrosive Medien bilden primäre elektrochemische Zellen und Korrosion.
2.2.3 Bratschule
Die Komponenten der Flammenheizzone und der metallurgischen Struktur verändern sich ungleichmäßig, wobei galvanische Zellen mit dem korrosiven Medium gebildet werden und eine elektrochemische Korrosion verursachen.
2.2.4 Schweißen:
Physikalische Defekte im Schweißbereich (Hinterschneidungen, Poren, Risse, nicht schweißend, unvollständige Penetration usw.) und chemische Defekte (größere Korn-, Chrom-abgereicherte Korngrenzen, Segregation usw.) und das korrosive Medium bilden Primärzellen. Erzeugen Sie elektrochemische Korrosion.
2.2.5 Material: Rostfreie chemische Defekte (inhomogene Zusammensetzung, S, P Verunreinigungen usw.) und physikalische Defekte an der Oberfläche (lose, Trachom, Risse usw.) sind förderlich für die Bildung von Primärbatterien mit Korrosionsmedium und elektrochemischer Korrosion.
2.2.6 Passivierung: Die schlechte Beizpassivierung führt zu einem ungleichmäßigen oder dünnen Passivierungsfilm auf der Oberfläche von rostfreiem Stahl, der leicht elektrochemische Korrosion bildet.
2.2.7 Reinigung: Restsäurebeiz- und Passivierungsrückstände sowie chemische Korrosionsprodukte aus rostfreiem Stahl und Edelstahlteile bilden elektrochemische Korrosion.
Spannungskorrosion
Wegen seiner speziellen metallographischen Struktur und seiner Oberflächenpassivierungsschicht macht rostfreier Stahl es schwierig, unter normalen Umständen mit einer chemischen Reaktion mit dem Medium zu korrodieren, kann jedoch unter keinen Bedingungen korrodieren.
In Gegenwart von korrosiven Medien und Ursachen (wie Kratzer, Schlacken usw.) kann rostfreier Stahl auch mit langsamen chemischen und elektrochemischen Reaktionen mit korrosiven Medien korrodieren, weiterhin ist die Korrosionsgeschwindigkeit unter bestimmten Bedingungen ziemlich schnell und verursacht Korrosion, insbesondere Lochfraß und Spaltkorrosion Der Korrosionsmechanismus von Edelstahlteilen ist hauptsächlich elektrochemische Korrosion.
Vorsichtsmaßnahmen
Lagerung und Heben
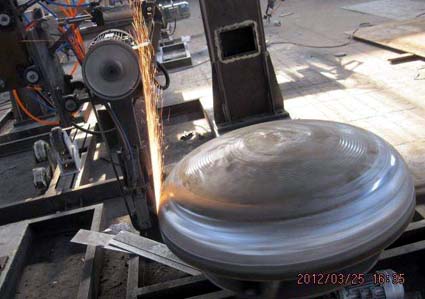
4.1.1 Lagerung von Teilen aus rostfreiem Stahl: Es sollte ein spezielles Lagerregal vorhanden sein, das eine Halterung oder ein Pad aus Kohlenstoffstahl mit einer Holz- oder lackierten Oberfläche sein sollte, um es von anderen Metallmaterialien wie Kohlenstoffstahl zu isolieren. Bei der Lagerung sollte der Lagerort leicht von anderen Lagerbereichen isoliert werden und es sollten Schutzmaßnahmen getroffen werden, um eine Verunreinigung des Edelstahls durch Staub, Öl und Rost zu vermeiden.4.1.2 Heben von Edelstahlteilen: Beim Heben Es sind spezielle Spreizer, wie Hebegurte, Spezialfutter etc. zu verwenden. Es ist verboten, Drahtseile zu verwenden, um ein Verkratzen der Oberfläche zu vermeiden. Beim Anheben und Aufstellen sollten Kollisionen vermieden werden, um Kratzer zu verursachen.
4.1.3 Transport von Edelstahlteilen: Verwenden Sie beim Transport Transportmittel (wie Wagen, Autobatterien usw.), und reinigen Sie diese sowie Isolierungs- und Schutzmaßnahmen, um zu verhindern, dass Staub, Öl und Rost den Edelstahl verunreinigen. Ziehen Sie nicht, vermeiden Sie Beulen, Kratzer.
wird bearbeitet
4.2.1 Bearbeitungsbereich: Der Bearbeitungsbereich von Edelstahlteilen sollte relativ fest sein. Die Plattform des Edelstahlbearbeitungsbereichs sollte Isolationsmaßnahmen ergreifen, z. B. die Verlegung von Gummipuffern. Das Setting-Management und die zivilisierte Produktion von Edelstahlverarbeitungsbereichen sollten verstärkt werden, um Schäden und Verunreinigungen von Edelstahlteilen zu vermeiden.
4.2.2 Stanzen: Das Stanzen von Edelstahlteilen erfolgt durch Scheren oder Plasmaschneiden, Sägen usw.
(1) Schnitt: Beim Schneiden sollte es von der Zufuhrklammer isoliert werden, und der fallende Trichter sollte mit einer Gummiauflage bedeckt sein, um ein Verkratzen zu vermeiden.
(2) Plasmaschneiden: Nach dem Plasmaschneiden sollte das Bohrklein gereinigt werden. Beim Chargenschneiden sollte das Feld rechtzeitig für die fertigen Teile geräumt werden, um die Schlackenschlacke am Werkstück zu vermeiden.
(3) Sägen Ausschneiden: Beim Sägen des Materials sollte die Klemme durch Gummi geschützt werden. Nach dem Sägen sollten das Öl und die Rückstände auf dem Werkstück gereinigt werden.
4.2.3 Mechanische Bearbeitung: Auch beim Drehen, Fräsen und anderen Bearbeitungen sollten Edelstahlteile geschützt werden. Nach dem Vorgang reinigen Sie die Oberfläche des Werkstücks wie Öl, Eisen und andere Verunreinigungen.
4.2.4 Verarbeitung von Formteilen: Während des Walzens und Biegens von Platten sollten wirksame Maßnahmen ergriffen werden, um Kratzer und Falten auf der Oberfläche der Edelstahlteile zu vermeiden.
4.2.5 Nietschweißen: Bei der Montage von Edelstahlteilen sollte eine Zwangskonfektionierung vermieden werden, insbesondere sollte Flammbrand und Montage vermieden werden. Wenn während des Paarungs- oder Produktionsprozesses zeitweiliges Plasmaschneiden stattfindet, müssen Isolationsmaßnahmen ergriffen werden, um eine Verunreinigung anderer Teile aus rostfreiem Stahl durch Schlackenschneiden zu vermeiden. Nach dem Schneiden sollte die Schlacke auf dem Werkstück gereinigt werden.
4.2.6 Schweißen: Edelstahlteile müssen vor dem Schweißen sorgfältig von Öl, Rost, Staub und anderen Verunreinigungen gereinigt werden. Versuchen Sie beim Schweißen das Argon-Lichtbogenschweißen. Verwenden Sie beim manuellen Lichtbogenschweißen ein kleines Strom und schnelles Schweißen, um ein Schwingen zu vermeiden. Es ist verboten, den Lichtbogen im nicht schweißbaren Bereich zu starten. Die Erdungsposition ist angemessen und die Verbindung ist fest, um Lichtbogenkratzer zu vermeiden. Beim Schweißen sollten Spritzschutzmaßnahmen getroffen werden (z. B. weiße Asche und andere Methoden). Nach dem Schweißen werden flache Spaten aus rostfreiem Stahl (kein Kohlenstoffstahl) verwendet, um die Schlacke und den Spritzer gründlich zu reinigen.
4.2.7 Mehrlagenschweißen: Beim Mehrlagenschweißen muss die Zwischenschlacke entfernt werden. Beim mehrschichtigen Schweißen sollte die Temperatur zwischen den Schichten kontrolliert werden und sollte im Allgemeinen 60 ° C nicht übersteigen.
4.2.8 Schweißnähte: Schweißverbindungen müssen geschliffen sein. Die Oberfläche der Schweißnaht darf keine Defekte wie Schlacke, Luftlöcher, Hinterschneidungen, Spritzer, Risse, unvollständige Verschmelzung, unvollständige Durchdringung usw. aufweisen. Die Schweißnähte und das Grundmetall müssen glattgängig sein und dürfen nicht niedriger als das Grundmetall sein.
4.2.9 Orthopädie: In der Orthopädie von Edelstahlteilen sollten Flammenheizverfahren vermieden werden, insbesondere ist ein wiederholtes Erhitzen desselben Bereichs nicht erlaubt. Korrigieren Sie mechanische Geräte so weit wie möglich, oder hämmern Sie sie mit Holzhämmern (Gummihämmern) oder Pad-Gummi-Pads, und hämmern Sie sie nicht mit Hämmern, um Schäden an den Edelstahlteilen zu vermeiden.
Oberflächenbehandlung
4.3.1 Reinigen und Polieren: Wenn der Schaden poliert werden sollte, Kratzer und Spritzer, die insbesondere durch den Kontakt mit Kohlenstoffstahlteilen verursacht werden, müssen Schäden durch Schneidschlacke gründlich gereinigt und poliert werden.
4.3.2 Mechanisches Polieren: Die Verwendung eines geeigneten Polierwerkzeugs zum Polieren erfordert eine einheitliche Handhabung und vermeidet eine übermäßige Entsorgung und Wiederverkratzen.
4.3.3 Entfettung und Entstaubung: Bevor die Edelstahlteile gebeizt und passiviert werden, müssen Verunreinigungen wie Öl, Oxidzunder und Staub prozessbedingt entfernt werden.
4.3.4 Sprühwasser Behandlung: Nach verschiedenen Verarbeitungsanforderungen, wählt unterschiedliche Mikroglasperlen, verschiedene Prozessparameter und Übersprühen vermeiden.
4.3.5 Beizpassivierung: Die Beizpassivierung von Edelstahlteilen muss streng nach den Prozessanforderungen passiviert werden.
4.3.6 Reinigung und Trocknung: Nach dem Beizen und der Passivierung sollte das Produkt sorgfältig verarbeitet und neutralisiert, gespült und getrocknet werden, um die restliche Säure vollständig zu entfernen.
4.3.7 Schutz: Nach Abschluss der Oberflächenbehandlung von Edelstahlteilen ist Schutz zu gewährleisten, um eine sekundäre Verschmutzung von sich berührendem Personal, Öl, Staub und anderen Verunreinigungen zu verhindern.
4.3.8 Wiederaufbereitung vermeiden: Nach der Oberflächenbehandlung von Edelstahlteilen sollte eine Nachbearbeitung der Teile oder Produkte vermieden werden.
Einschließlich: Oberflächenbehandlung von Edelstahl / kohlenstoffarmen Stahlprodukten wie chemischen Behältern, Lagertanks und Rohrheizkesseln, wie Schleifen / Polieren, Beizen / Passivieren, Inspektion / Überwachung und technische Beratung.
Die Hauptziele sind Schiffe, Petrochemie und Nahrungsmittel.
Vorhandene Probleme
5.1 Schweißfehler: Schweißfehler sind von Hand schwerer, um eine mechanische Polierbehandlung durchzuführen. Die resultierenden Schleifspuren verursachen unebene Oberflächen und beeinträchtigen das Aussehen.
5.2 Inkonsistente Oberfläche: Nur Beizen und Passivieren der Schweißnähte können auch zu Oberflächenunregelmäßigkeiten führen und das Aussehen beeinträchtigen.
5.3 schwer zu entfernende Kratzer: Die gesamte Beizpassivierung kann nicht alle während der Bearbeitung entstandenen Kratzer entfernen. Darüber hinaus ist es nicht möglich, Kohlenstoffstahl, Spritzer und andere Verunreinigungen zu entfernen, die aufgrund von Kratzern und Schweißspritzern auf der Oberfläche von rostfreiem Stahl haften. In Gegenwart von korrosivem Medium treten chemische Korrosion und Rost oder galvanische Korrosion auf.
5.4 Polierpassivierung ungleichmäßig: Nach dem Handpolieren wird eine Beiz- und Passivierungsbehandlung durchgeführt. Bei einem Werkstück mit einer großen Fläche ist es schwierig, einen gleichmßigen und gleichmßigen Behandlungseffekt zu erzielen, und eine ideale einheitliche Oberfläche kann nicht erhalten werden. Und Arbeitsstunden, Zubehörkosten sind auch hoch.
5.5 Beizkapazität ist begrenzt: Beizpaste ist kein Allheilmittel. Es ist schwieriger für Plasmaschneiden und Brennschneiden zu entfernen.
5.6 Der durch menschliche Faktoren verursachte Kratzer ist ernster: Beim Heben, Transportieren und strukturellen Bearbeiten verursachen Kratzer, Schleifen, Hämmern und andere menschliche Faktoren ernsthafte Kratzer, was die Oberflächenbehandlung schwieriger macht, und sie ist auch die Hauptursache der Korrosion nach der Verarbeitung.
5.7 Ausstattungsfaktoren: Beim Biegen, Biegen und Biegen von Profilen sind auch Platten, Kratzer und Knicke die Hauptursachen für Korrosion nach der Verarbeitung.
5.8 Weitere Faktoren: Bei der Beschaffung und Lagerung von Edelstahlrohstoffen sind auch Stöße und Kratzer durch Anheben und Transport von Bedeutung und eine der Ursachen für Korrosion.
Grundlegende Verarbeitung
Die gebräuchlichste Edelstahl-Oberflächenbehandlungstechnologie weist die folgenden Behandlungsmethoden auf:
1. Oberflächenaufhellungsbehandlung;
2. Oberflächenspiegelleuchte Behandlung;
3. Oberflächenfärbung.
1.2.1 Oberflächenaufhellungsbehandlung:
Bei der Verarbeitung von Edelstahl entstehen nach dem Wickeln, Binden, Verschweißen oder künstlichem Oberflächenhärten und Erhitzen Wärmewallungen. Diese harte grau-schwarze Skala besteht hauptsächlich aus NiCr2O4 und NiF EO4. Flusssäure und Salpetersäure werden normalerweise verwendet, um starke Korrosion zu entfernen. Diese Methode ist jedoch kostspielig, verschmutzt die Umwelt, ist schädlich für den menschlichen Körper und hochgradig korrosiv und wird allmählich beseitigt.
Es gibt zwei Hauptmethoden zur Behandlung von Oxidschuppen:
(1) Sandstrahlen (Pill) -Verfahren: Das Verfahren zum Sprühen von Mikroglasperlen wird hauptsächlich verwendet, um die Schwarzoxid-Zunder auf der Oberfläche zu entfernen.
(2) Chemisches Verfahren: Eine nicht verunreinigende Beiz- und Passivierungspaste und eine Reinigungslösung mit anorganischen Zusätzen bei normaler Temperatur wurden zum Waschen verwendet. Um den Zweck der weißen Farbe von Edelstahl zu erreichen. Nach der Verarbeitung sieht es im Grunde wie eine matte Farbe aus. Diese Methode eignet sich eher für große und komplexe Produkte.
1.2.2 Lichtbehandlung von Oberflächenspiegel aus Edelstahl: Je nach Komplexität der Edelstahlprodukte und unterschiedliche Anforderungen der Benutzer können mechanische Polieren, chemisches Polieren, elektrochemisches Polieren und andere Methoden verwendet werden, um den spiegelnden Glanz zu erreichen.
1.2.3 Oberflächenfärbung: Edelstahlfärbung verleiht rostfreien Stahlprodukten nicht nur verschiedene Farben, sondern erhöht auch die Farbvielfalt von Produkten und verbessert die Verschleißfestigkeit und Korrosionsbeständigkeit von Produkten.
Edelstahl Färbung Methoden sind wie folgt:
(1) chemische Oxidationsfärbung;
(2) elektrochemisches Oxidationsfärbungsverfahren;
(3) Ionenabscheidungs-Oxidfärbeverfahren;
(4) Hochtemperatur-Oxidationsfärbeverfahren;
(5) Gasphasen-Crack-Färbeverfahren.
Die verschiedenen Methoden sind wie folgt:
1) Chemische Oxidationsfärbung: In einer bestimmten Lösung umfasst die Farbe des durch chemische Oxidation gebildeten Films das Dichromatverfahren, das gemischte Natriumsalzverfahren, das Schwefelungsverfahren, das Säureoxidationsverfahren und das alkalische Oxidationsverfahren. Im Allgemeinen wird INCO häufiger verwendet, aber um sicherzustellen, dass die Farbe einer Charge von Produkten konsistent ist, müssen Referenzelektroden zur Kontrolle verwendet werden.
(2) Elektrochemische Färbung: Es ist die Farbe des Films, der durch elektrochemische Oxidation in einer spezifischen Lösung gebildet wird.
(3) Ionenabscheidung Oxid Färbung chemische Methode: Das Edelstahlwerkstück in einer Vakuumbeschichtungsanlage für Vakuumverdampfungsbeschichtung angeordnet ist. Zum Beispiel: Titan-überzogene Uhrengehäuse, Uhrenarmbänder, sind in der Regel goldgelb. Diese Methode eignet sich zur Verarbeitung großer Produktmengen. Aufgrund der großen Investition und der hohen Kosten sind Kleinserienprodukte unwirtschaftlich.