Drehen
Was dreht Drehen?
Drehen bezieht sich auf die Drehbearbeitung, die Teil der mechanischen Bearbeitung ist. Die Drehbearbeitung verwendet hauptsächlich Drehwerkzeuge, um das Werkstück zu drehen. Drehmaschinen werden hauptsächlich zur Bearbeitung von Wellen, Scheiben, Mänteln und anderen Werkstücken mit rotierenden Oberflächen verwendet. Sie sind die am weitesten verbreitete Art von Werkzeugmaschinen in Maschinenfabriken und Reparaturfabriken.
Technischer Brief
Auf der Drehbank werden die Form und die Größe des Rohlings durch die Drehbewegung des Werkstücks und die lineare oder gekrümmte Bewegung des Werkzeugs verändert, und es wird bearbeitet, um die Anforderungen der Zeichnungen zu erfüllen.
Drehen ist ein Verfahren zum Schneiden eines Werkstücks durch Drehen eines Werkstücks relativ zu einem Werkzeug auf einer Drehbank. Die Schneidenergie des Drehens wird hauptsächlich durch das Werkstück anstelle des Werkzeugs bereitgestellt. Drehen ist die grundlegendste und gängigste Methode des Schneidens und nimmt in der Produktion eine sehr wichtige Position ein. Das Drehen eignet sich für die Bearbeitung von Drehflächen. Die meisten Werkstücke mit einer Drehfläche können durch Drehen bearbeitet werden. Als innere und äußere zylindrische Oberflächen, innere und äußere konische Oberflächen, Endoberflächen, Nuten, Gewinde und rotierende Formungsoberflächen werden hauptsächlich Drehwerkzeuge verwendet. Drehmaschinen sind die am weitesten verbreitete Kategorie in allen Arten von spanenden Werkzeugmaschinen und machen etwa 50% der Gesamtzahl der Werkzeugmaschinen aus. Die Drehmaschine kann verwendet werden, um ein Werkstück mit einem Drehwerkzeug zu drehen, kann aber auch Bohrer, Reibahlen, Gewindebohrer und Rändelwerkzeuge zum Bohren, Reiben, Gewindeschneiden und Rändeln verwenden. Je nach den verschiedenen Eigenschaften des Verfahrens, des Layouts und der Strukturmerkmale können die Drehmaschinen in Horizontaldrehmaschinen, Bodenrotationsmaschinen, Vertikaldrehmaschinen, Revolverdrehmaschinen und Doppeldrehmaschinen, von denen die meisten Horizontaldrehmaschinen sind, unterteilt werden.
Technisches Problem
Die Drehbearbeitung ist der am weitesten verbreitete Typ in der Maschinenbauindustrie. Die Anzahl der Drehmaschinen ist groß, die Anzahl der Personen ist groß und die Verarbeitungsbreite ist groß. Es werden viele Werkzeuge und Vorrichtungen verwendet. Daher sind die sicherheitstechnischen und technischen Aspekte des Drehens besonders wichtig. Die wichtigsten Aufgaben sind wie folgt:
1, Späneschaden und Schutzmaßnahmen.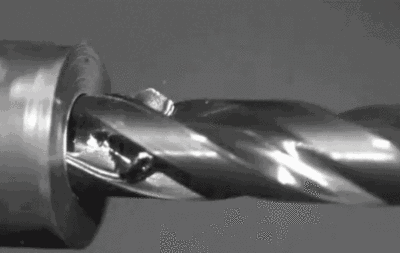
Die Stahlteile, die auf der Drehmaschine bearbeitet werden, sind flexibler, und die während des Drehens erzeugten Späne sind plastisch gekräuselt und haben scharfe Kanten. Beim Hochgeschwindigkeitsschneiden von Stahlteilen entstehen rote Hot-Spots und lange Späne, die sich sehr leicht verletzen und oft um Werkstücke, Drehwerkzeuge und Werkzeughalter gewickelt werden. Daher sollte der Haken rechtzeitig in der Arbeit gereinigt oder abgezogen werden. Wenn nötig, sollte es gestoppt und gelöscht werden. Es darf jedoch nicht von Hand entfernt oder gebrochen werden. Um Späneschäden zu verhindern, werden häufig Spänebrechen, Spänestromkontrolle und verschiedene Schutzschikanen eingesetzt. Die Spanbrechmaßnahme besteht darin, Spanbrecher oder Stufen auf dem Drehwerkzeug zu schleifen; Verwenden Sie einen geeigneten Spanbrecher und klemmen Sie das Werkzeug mechanisch fest.
2, Werkstückmontage.
Beim Drehen kommt es zu vielen Unfällen, wie zum Beispiel einer Beschädigung der Werkzeugmaschine aufgrund eines unsachgemäßen Einbaus des Werkstücks, eines Brechens oder Zusammenstürzens des Werkzeugs und eines Herausfallens oder Herausfliegens aus dem Werkstück.
Um eine sichere Produktion von Drehungen zu gewährleisten, muss daher beim Beladen von Werkstücken besondere Aufmerksamkeit geschenkt werden. Für Teile unterschiedlicher Größen und Formen müssen geeignete Vorrichtungen verwendet werden, unabhängig von der Verbindung von Dreibacken- und Vierbackenspannfuttern oder speziellen Vorrichtungen und Spindeln. Werkstücke müssen zwangsgeklemmt und geklemmt werden und große Werkstücke können geklemmt und ummantelt werden.
Wenn das Werkstück mit einer hohen Geschwindigkeit gedreht wird und die Schneidkraft ausgeübt wird, wird es nicht verschoben, fällt ab und schleudert nicht. Bei Bedarf kann es durch den oberen Mittel- und Mittelrahmen verstärkt werden. Verriegelung, sofort nach dem Entfernen des Schraubenschlüssels.
3, sicherer Betrieb.
Vor der Arbeit müssen wir die Maschine vollständig inspizieren und bestätigen, dass sie für die Verwendung geeignet ist. Die Montage des Werkstücks und des Werkzeugs stellt sicher, dass die Position korrekt, fest und zuverlässig ist. Während der Bearbeitung muss das Werkzeug beim Werkzeugwechsel, beim Be- und Entladen des Werkstücks und beim Messen des Werkstücks angehalten werden. Das Werkstück darf beim Drehen nicht mit der Hand berührt oder mit Baumwolle abgewischt werden. Um die Schnittgeschwindigkeit, Vorschubgeschwindigkeit und Spannungstiefe richtig zu wählen, ist keine Überlastbearbeitung erlaubt. Es dürfen keine Werkstücke, Arbeitsklammern und andere Ablagerungen auf der Werkzeugauflage und der Bettoberfläche platziert werden. Wenn Sie eine Reibe verwenden, bewegen Sie das Drehwerkzeug in eine sichere Position, mit der rechten Hand auf der Vorderseite und der linken Hand auf der Rückseite, um zu verhindern, dass die Ärmel eingreifen. Die Werkzeugmaschine muss jemanden haben, der für den Gebrauch und die Wartung verantwortlich ist, und anderes Personal darf sie nicht benutzen.
Vorsichtsmaßnahmen
Der Prozess der CNC-Drehbearbeitung ist ähnlich dem von gewöhnlichen Drehmaschinen. Aufgrund der Tatsache, dass die CNC-Drehmaschine einmal installiert ist und alle Dreharbeiten automatisch abgeschlossen werden, sollten die folgenden Aspekte beachtet werden.
1. Angemessene Wahl der Schnittmenge:
Für das hocheffiziente Schneiden von Metall sind die zu bearbeitenden Materialien, Schneidwerkzeuge und Schneidbedingungen drei Hauptfaktoren. Diese bestimmen Bearbeitungszeit, Standzeit und Bearbeitungsqualität. Die wirtschaftliche und effektive Verarbeitungsmethode muss eine vernünftige Wahl der Schnittbedingungen sein. Die drei Elemente der Schneidbedingungen: Schnittgeschwindigkeit, Vorschubgeschwindigkeit und Schnitttiefe verursachen direkt Werkzeugschäden. Mit der Erhöhung der Schneidgeschwindigkeit wird die Temperatur der Werkzeugspitze erhöht und es wird mechanischer, chemischer und thermischer Verschleiß erzeugt. Schnittgeschwindigkeit um 20% erhöht, Standzeit um 1/2 reduziert. Der Vorschubzustand und der Verschleiß hinter dem Werkzeug werden in einem sehr kleinen Bereich erzeugt. Die Vorschubgeschwindigkeit ist jedoch groß, die Schneidtemperatur steigt an und der hintere Verschleiß ist groß. Es hat weniger Einfluss auf das Werkzeug als die Schnittgeschwindigkeit. Die Wirkung des tiefen Schneidens auf das Schneidwerkzeug Obwohl es keine Schnittgeschwindigkeit und Vorschubmenge gibt, hat das zu schneidende Material bei geringer Schnitttiefe eine gehärtete Schicht, die sich auch auf die Lebensdauer des Schneidwerkzeugs auswirkt. Der Benutzer wählt die zu verwendende Schnittgeschwindigkeit basierend auf dem zu bearbeitenden Material, Härte, Schneidbedingung, Materialtyp, Vorschubmenge, Schnitttiefe und dergleichen. Die Auswahl der am besten geeigneten Verarbeitungsbedingungen wird auf der Grundlage dieser Faktoren ausgewählt. Regelmäßiger und stabiler Verschleiß ist die ideale Voraussetzung, um die Lebenserwartung zu erreichen. Im tatsächlichen Betrieb hängt die Wahl der Werkzeugstandzeit jedoch vom Werkzeugverschleiß, der Größe der bearbeiteten Maschine, der Oberflächenqualität, dem Schneidgeräusch und der Bearbeitungswärme ab. Bei der Festlegung der Verarbeitungsbedingungen ist es erforderlich, die Forschung nach den tatsächlichen Bedingungen durchzuführen. Für schwer zu bearbeitende Materialien wie Edelstahl und hitzebeständige Legierungen können Kühlmittel oder starre Klingen verwendet werden.
2. Angemessene Wahl der Werkzeuge:
(1) Wählen Sie beim Schruppen ein Werkzeug mit hoher Festigkeit und guter Haltbarkeit, um den Anforderungen einer großen Schnitttiefe und einer großen Vorschubmenge beim Schruppen gerecht zu werden.
(2) Nach dem Drehen müssen Werkzeuge mit hoher Präzision und guter Haltbarkeit ausgewählt werden, um die Bearbeitungsgenauigkeit zu gewährleisten.
(3) Um die Werkzeugwechselzeit zu reduzieren und die Werkzeugeinstellung zu erleichtern, sollten Klemme und Klinge so weit wie möglich verwendet werden.
3. Wählen Sie die Leuchte angemessen aus:
(1) Versuchen Sie, eine universelle Vorrichtung zu verwenden, um das Werkstück einzuspannen, um spezielle Befestigungen zu vermeiden;
(2) Die Teilepositionierungsreferenz stimmt überein, um den Positionierungsfehler zu reduzieren.
4. Bestimmen Sie die Verarbeitungsroute:
Die Bearbeitungsroute ist die Bahn und die Richtung des Werkzeugs relativ zu dem Teil der indexgesteuerten Werkzeugmaschinenbearbeitung.
(1) Es sollte in der Lage sein, Verarbeitungsgenauigkeit und Anforderungen an die Oberflächenrauhigkeit zu gewährleisten;
(2) Die Verarbeitungsstrecke sollte so weit wie möglich verkürzt werden, um die Leerlaufzeit des Werkzeugs zu verringern.
5. Bearbeitungsweg und Bearbeitungszugabe:
Unter der Bedingung, dass CNC-Drehmaschinen keine universelle Verwendung gefunden haben, sollte im Allgemeinen eine übermäßige Toleranz für Rohlinge, insbesondere die Erlaubnis zum Schmieden und Gießen von Hardcover, auf gewöhnlichen Drehmaschinen bearbeitet werden. Wenn Sie die CNC-Drehbearbeitung verwenden müssen, müssen Sie auf die flexible Anordnung des Programms achten.
6. Fixture Installationspunkte:
Die Verbindung zwischen dem Hydrodehnspannfutter und dem hydraulischen Spannzylinder wird durch die Zugstange erreicht. Die wichtigsten Punkte der hydraulischen Futterspannung sind wie folgt:
Entfernen Sie zuerst die Mutter des Hydraulikzylinders mit einer Hand, entfernen Sie das Zugrohr und ziehen Sie das Spannfutter vom hinteren Ende der Spindel ab. Entfernen Sie dann die Befestigungsschraube des Spannfutters, um das Spannfutter zu entfernen.
Allgemeine Regeln
Allgemeine Verarbeitungsverfahren für die Verarbeitung aktivieren (JB / T9168.2-1998)
Werkzeugeinstellung
1) Der Werkzeugschaft ragt aus dem Werkzeughalter und sollte nicht zu lang sein. Die allgemeine Länge sollte die 1,5-fache Höhe der Werkzeugleiste nicht überschreiten (außer Loch, Schlitz usw.)
2) Die Mittellinie des Drehwerkzeughalters sollte senkrecht oder parallel zur Schnittrichtung sein.
3) Einstellung der Höhe der Messerspitze:
(1) Wenn eine Fläche gedreht wird, eine konische Fläche gedreht wird, Gewinde gedreht werden, eine Formfläche gedreht wird und ein festes Werkstück geschnitten wird, sollte die Schneidkante im Allgemeinen auf der gleichen Höhe wie die Werkstückachse sein.
(2) Das Schrupprad, das Schlichtloch und die Werkzeugspitze sollten generell etwas höher als die Werkstückachse sein.
(3) Wenn der schlanke Schaft, das raue Loch und das hohle Werkstück abgeschnitten werden, sollte die Werkzeugspitze im Allgemeinen etwas niedriger als die Werkstückachse sein.
4) Die Winkelhalbierende des Gewindewinkels des Gewindedrehwerkzeugs sollte senkrecht zur Werkstückachse stehen.
5) Beim Einsetzen des Drehwerkzeugs sollte die Unterlegscheibe unter der Werkzeugleiste klein und flach sein, und die Schraube, die das Drehwerkzeug drückt, sollte festgezogen werden.
Montage des Werkstücks
1) Bei Verwendung eines Drei-Backen-Zentrierspannfutters zum Spannen von Werkstücken zum Schruppen und Schlichten, wenn der Werkstückdurchmesser kleiner als 30 mm ist, darf die Überhanglänge nicht größer als das 5-fache des Durchmessers sein, wenn der Werkstückdurchmesser größer als 30 mm ist , Seine Überhanglänge sollte nicht mehr als das 3-fache des Durchmessers betragen.
2) Bei Verwendung eines Vierbacken-Einfachspannfutters, einer Planscheibe, eines Winkeleisens (Biegeplatte) usw. zum Spannen von unregelmäßig gewichteten Werkstücken muss Gewicht hinzugefügt werden.
3) Bei der Bearbeitung eines Schaft-Werkstücks an der Spitze der Welle muss die Reitstockmittelachse vor dem Drehen mit der Achse der Drehmaschinenspindel übereinstimmen.
Bei der Verarbeitung sollte darauf geachtet werden, dass die obere Dichtigkeit eingestellt wird, wobei der obere Totpunkt und der mittlere Rahmen beachtet werden sollten Schmierung
5) Bei Verwendung des Reitstocks sollte die Hülse so kurz wie möglich sein, um Vibrationen zu reduzieren.
6) Wenn die Vertikaldrehmaschine festgeklemmt ist, ist die Auflagefläche klein und die Werkstückhöhe ist hoch, die erhöhte Klaue sollte verwendet werden, und das Werkstück sollte an der geeigneten Stelle mit einer Zugstange oder einer Pressplatte gedrückt werden.
7) Beim Drehen von Rädern und Gussstücken muss die unfertige Oberfläche korrigiert werden, um nach der Bearbeitung eine gleichmäßige Wandstärke zu gewährleisten.
Drehung
1) Beim Drehen der Stufenwelle sollte generell der Teil mit dem größeren Durchmesser zuerst gedreht werden und der Teil mit dem kleineren Durchmesser sollte später gedreht werden, um die Steifigkeit während des Drehens sicherzustellen.
2) wenn die Welle Schneidnuten an einem Werkstück aufweist, die vor dem Fertigbearbeiten auszuführen sind, um eine Verformung des Werkstücks zu verhindern.
3) Wenn eine Gewindewelle fein gedreht wird,
Nach dem Einfädeln wird der nicht gewindete Teil präzisionsgedreht.
4) vor dem Bohren sollte die Stirnfläche des Werkstücks flachgedreht werden. Bohren Sie bei Bedarf zuerst das mittlere Loch.
5) Beim Bohren tiefer Löcher wird in der Regel zuerst das Pilotloch gebohrt.
6) Beim Drehen von (Φ10-Φ20) mm Löchern sollte der Durchmesser des Werkzeugschaftes das 0,6-0,7 fache des Durchmessers der bearbeiteten Bohrung betragen; Wenn der Durchmesser des Lochs größer als 20 mm ist, sollte der Messerhalter mit Klemmkopf verwendet werden.
7) Beim Drehen einer Mehrkopf- oder Mehrkopfschraube Nach dem Einstellen der Wechselräder einen Probeschnitt durchführen.
8) Wenn Sie den Drehautomaten verwenden, stellen Sie die relative Position des Werkzeugs und des Werkstücks entsprechend der Einstellkarte der Werkzeugmaschine ein. Nach der Einstellung ist es notwendig, das Probedrehen durchzuführen. Nachdem das erste Stück qualifiziert wurde, kann es bearbeitet werden; Während des Bearbeitungsprozesses wird immer der Verschleiß des Werkzeugs, die Werkstückgröße und die Oberflächenrauhigkeit berücksichtigt.
9) Beim Einschalten einer Vertikaldrehmaschine darf der Balken beim Einstellen des Messerhalters nicht frei bewegt werden. Beim Einschalten der Vertikaldrehmaschine darf der Querträger nach dem Einstellen der Werkzeugablage nicht beliebig bewegt werden.
10) Wenn die relevante Oberfläche des Werkstücks Positionstoleranzen aufweist, wird das Drehen in einer einzigen Spannung so weit wie möglich durchgeführt.
11) Beim Drehen eines Stirnradzahnrohlings müssen die Bohrung und die Referenzstirnfläche in einer Aufspannung bearbeitet werden. Wenn nötig, sollte die Markierungslinie nahe dem Ende des Zahnrad-Indexkreises gezeichnet werden.
Fehlerkompensation
Moderne Maschinenbautechnologie entwickelt sich zu hoher Effizienz, hoher Qualität, hoher Präzision, hoher Integration und hoher Intelligenz. Die Präzisions- und Ultrapräzisionsbearbeitungstechnologie ist zur wichtigsten Komponente und Richtung der Entwicklung im modernen Maschinenbau geworden und hat sich zu einer Schlüsseltechnologie für die Verbesserung der internationalen Wettbewerbsfähigkeit entwickelt. Der sich drehende Bearbeitungsfehler ist mit der umfangreichen Anwendung der Präzisionsbearbeitung ein heißes Forschungsthema geworden. Da thermische Fehler und geometrische Fehler für die meisten der verschiedenen Fehler in der Werkzeugmaschine verantwortlich sind, ist die Reduzierung dieser zwei Fehler, insbesondere der thermischen Fehler, das Hauptziel geworden. Fehlerkompensationstechnologie (ECT) entstand mit der kontinuierlichen Entwicklung von Wissenschaft und Technologie. Die durch die thermische Verformung der Werkzeugmaschine verursachten Verluste sind beträchtlich. Daher ist es extrem notwendig, ein hochpräzises, kostengünstiges thermisches Fehlerkompensationssystem zu entwickeln, das die tatsächlichen Produktionsanforderungen der Fabrik erfüllen kann, um thermische Fehler zwischen der Spindel (oder dem Werkstück) und dem Schneidwerkzeug zu korrigieren. Um die Genauigkeit von Werkzeugmaschinen zu verbessern, Abfall zu reduzieren, Produktionseffizienz zu erhöhen und wirtschaftliche Vorteile.
Grundlegende Definition
Die Grunddefinition der Fehlerkompensation besteht darin, künstlich einen neuen Fehler zu erzeugen, um den ursprünglichen Fehler, der derzeit ein Problem darstellt, zu löschen oder stark zu reduzieren. Durch Analyse, Statistik, Induktion und Beherrschung der Eigenschaften und Gesetzmäßigkeiten des ursprünglichen Fehlers wurde das mathematische Fehlermodell erstellt, um zu versuchen, den künstlich erzeugten Fehler gleich dem ursprünglichen Fehler und in der entgegengesetzten Richtung zu machen, wodurch der Bearbeitungsfehler reduziert und verbessert wurde die Maßgenauigkeit des Teils.
Die früheste Fehlerkompensation wurde durch Hardware erreicht. Hardware-Kompensation ist eine mechanische feste Kompensation. Um den Korrekturbetrag zu ändern, wenn sich der Werkzeugmaschinenfehler ändert, müssen Sie Teile, Kalibrierungsregeln neu erstellen oder den Kompensationsmechanismus neu einstellen. Die Hardware-Kompensation hat auch den Nachteil, zufällige Fehler und mangelnde Flexibilität nicht zu lösen.
[1] Die Entwicklung der Softwarekompensation ist durch den umfassenden Einsatz modernster Technologie und Computersteuerungstechnologie verschiedener Disziplinen gekennzeichnet, um die Genauigkeit von Werkzeugmaschinen ohne Änderungen an der Werkzeugmaschine selbst zu verbessern. Die Software-Kompensation überwindet viele der Schwierigkeiten und Nachteile der Hardware-Kompensation und bringt die Vergütungstechnologie auf eine neue Stufe.
Charakteristisch
Fehlerkompensation (Technologie) hat zwei Hauptmerkmale: Wissenschaft und Technik.
Die schnelle Entwicklung der wissenschaftlichen Fehlerkompensationstechnologie hat die Theorie des mechanischen Präzisionsdesigns, der Präzisionsmessung und der gesamten Feinmechanik stark bereichert und ist zu einem wichtigen Zweig dieser Disziplin geworden. Techniken, die sich auf die Fehlerkompensation beziehen, umfassen Erkennungstechnologie, Sensortechnologie, Signalverarbeitungstechnologie, photoelektrische Technologie, Materialtechnologie, Computertechnologie und Steuerungstechnologie. Als Technologiezweig hat die Fehlerkompensationstechnologie ihre eigenen unabhängigen Inhalte und Eigenschaften. Weitere Forschungen über Fehlerkompensationstechniken, um sie theoretisch und systematisch zu machen, werden von großer wissenschaftlicher Bedeutung sein.
Die technische Bedeutung der technischen Fehlerkompensationstechnologie ist sehr bedeutend, sie enthält drei Bedeutungsebenen:
Erstens kann die Verwendung der Fehlerkompensationstechnologie leicht das Niveau an Genauigkeit erreichen, das "harte Technologie" kosten kann, um zu erreichen;
Die zweite ist die Verwendung von Fehlerkompensationstechniken, die das Niveau an Genauigkeit lösen können, das "harte Technologie" normalerweise nicht erreichen kann;
Drittens, wenn die Fehlerkompensationstechnologie unter gewissen Genauigkeitsanforderungen eingesetzt wird, können die Kosten der Instrumenten- und Geräteherstellung stark reduziert werden, was sehr signifikante wirtschaftliche Vorteile hat.
Drehbearbeitung thermische Fehlererzeugung und -klassifizierung
Mit der weiteren Verbesserung der Präzisionsanforderungen der Werkzeugmaschine wird der Anteil thermischer Fehler am Gesamtfehler weiter zunehmen. Die thermische Verformung der Werkzeugmaschine ist zu einem Haupthindernis geworden, um die Bearbeitungsgenauigkeit zu verbessern. Der thermische Fehler der Werkzeugmaschine wird hauptsächlich durch die thermische Verformung der Werkzeugmaschinenkomponenten verursacht, die durch Wärmequellen innerhalb und außerhalb der Maschine verursacht wird, wie Motoren, Lager, Getriebeteile, Hydrauliksysteme, Umgebungstemperatur und Kühlmittel. Der Werkzeugmaschinengeometriefehler ergibt sich aus den Fertigungsfehlern der Werkzeugmaschine, dem Anpassungsfehler zwischen den Werkzeugmaschinenkomponenten, der dynamischen und statischen Verschiebung der Werkzeugmaschinenkomponenten und so weiter.
Grundlegende Methode der Fehlerkompensation
Zusammenfassend und in Bezug genommene Referenzen zeigen, dass der Abbiegefehler im Allgemeinen durch die folgenden Faktoren verursacht wird:
Thermischer Verformungsfehler der Werkzeugmaschine;
Geometrische Fehler in Teilen und Strukturen von Werkzeugmaschinen;
Schnittkraft induzierter Fehler;
Werkzeugabnutzungsfehler;
Andere Fehlerquellen, wie Servofehler in Werkzeugmaschinenachsen, CNC-Interpolationsalgorithmusfehler usw.
Es gibt zwei grundlegende Methoden zur Verbesserung der Werkzeugmaschinengenauigkeit: Fehlervermeidungsmethode und Fehlerkompensationsmethode.
Das Fehlervermeidungsverfahren versucht, mögliche Fehlerquellen durch Entwurfs- und Herstellungsansätze zu beseitigen oder zu reduzieren. Das Fehlerverhinderungsverfahren ist wirksam, um den Temperaturanstieg der Wärmequelle zu verringern, das Temperaturfeld auszugleichen und die thermische Verformung der Werkzeugmaschine in einem gewissen Ausmaß zu verringern. Es ist jedoch unmöglich, die thermische Verformung vollständig zu eliminieren, und die Kosten sind sehr teuer; Die Anwendung des thermischen Fehlerausgleichsgesetzes eröffnet eine effektive und kostengünstige Möglichkeit, die Genauigkeit von Werkzeugmaschinen zu verbessern.
Zugehörige Schlussfolgerungen
Die Erforschung von Bearbeitungsfehlern ist die wichtigste Komponente und Richtung der Entwicklung im modernen Maschinenbau und hat sich zu einer Schlüsseltechnologie für die Verbesserung der internationalen Wettbewerbsfähigkeit entwickelt. Der Fehler wird auf viele Arten erzeugt. Die Analyse und Erforschung von thermischen Fehlern ist hilfreich, um die Drehpräzision und die technischen Anforderungen zu verbessern.
Die Fehlerkompensationstechnologie kann die hohe Präzision und niedrigen Kosten der tatsächlichen Produktionsanforderungen der Fabrik erfüllen. Die thermische Fehlerkompensationstechnologie kann den thermischen Driftfehler zwischen der Spindel (oder dem Werkstück) und dem Schneidwerkzeug korrigieren, die Bearbeitungsgenauigkeit der Werkzeugmaschine verbessern, Abfallprodukte reduzieren, die Produktionseffizienz erhöhen und wirtschaftliche Vorteile bieten.
häufiges Problem
Wenn die gewöhnliche Drehmaschine einen großen Gewindegang dreht, tritt manchmal eine Sattelvibration auf, und die Bearbeitungsoberfläche ist gewellt, und die schwere ist ein Frakturiermesser.
Und wenn sie geschnitten werden, haben die Arbeiter oft ein Messer oder ein Schnittmesserphänomen.
Es gibt viele Gründe für die obigen Probleme. Jetzt diskutieren wir hauptsächlich das Phänomen und die Lösungen, indem wir die Kraftbedingungen der Werkzeuge analysieren.
1. Die Ursache des Problems und seine Ursachen
wir wissen:
Wenn ein Gewinde mit einer kleinen Steigung gedreht wird, wird im allgemeinen ein Verfahren zum Schneiden eines geraden Messers (ein geradliniger Vorschub in der Richtung senkrecht zu der Werkstückachse) verwendet;
Wenn ein Gewinde mit einer großen Steigung gedreht wird, werden oft die Messermethoden des linken und rechten Messers verwendet, um die Schneidkraft zu reduzieren. (Durch Bewegen des kleinen Skateboards, um das Fadendrehwerkzeug mit der linken bzw. rechten Schneide zu schneiden).
Beim Drehen des Fadens wird die Bewegung des Sattels durch die Drehung der langen Schraube erreicht, um die Bewegung der Öffnungs- und Schließmutter zu steuern. Am Lager der langen Schraube gibt es ein axiales Spiel, und zwischen der langen Schraube und der Öffnungsmutter besteht ein axiales Spiel. Wenn die rechte Hauptschneide der rechtshändigen Schnecke durch das Links-Rechts-Entgratschneidverfahren stark bearbeitet wird, wird das Werkzeug der Kraft P ausgesetzt, die ihm vom Werkstück gegeben wird (wobei die Reibung zwischen dem Span und der Spanfläche ignoriert wird). und die Kraft P wird in eine axiale Komponente Px und eine radiale Komponente zerlegt, wobei die axiale Komponente Px und der Vorschub des Werkzeugs in der gleichen Richtung das Werkzeug über diese axiale Komponente Px zum Sattel führt. Somit wird der Bettsattel zur Seite des Spalts gedrückt, um schnelle und schnelle Bewegungen vor und zurück zu machen. Infolgedessen wird das Werkzeug hin- und herbewegt, und die Bearbeitungsoberfläche ist gewellt und sogar gebrochen. Beim Schneiden mit der linken Hauptschneide gibt es jedoch kein solches Phänomen. Beim Schneiden mit der linken Hauptschneide ist die axiale Kraftkomponente Px des Werkzeugs entgegengesetzt zur Vorschubrichtung und die Freiraumrichtung ist eliminiert. Zu diesem Zeitpunkt bewegt sich der Sattel mit einer gleichmäßigen Geschwindigkeit. .
Beim Abschneiden wird die Bewegung der mittleren Gleitplatte durch die Drehung der mittleren Gleitplattenschraube, die die Mutter antreibt, erreicht. Es gibt ein axiales Spiel am Schraubenwellenlager und ein axiales Spiel zwischen der Schraubenwelle und der Mutter. Beim Schneiden auf einer Drehbank wird die Spanfläche des Werkzeugs (mit der vorderen Ecke) der durch das Werkstück gegebenen Kraft P ausgesetzt (unter Ignorierung der Reibung zwischen dem Span und der Spanfläche). Zerlegt die Kraft P in Kraft Pz und Radialkraft. Die radiale Komponente ist die gleiche wie die Schneidrichtung des Schneidwerkzeugs. Es zeigt auf das Werkstück und schiebt das Werkzeug auf das Werkstück zu. Dies führt dazu, dass sich der mittlere Schlitten in die Richtung des Spiels bewegt, was das Biegen (Brechen) des Messers oder des Werkstücks verursacht.
Beim Abschneiden wird die Bewegung der mittleren Gleitplatte durch die Drehung der mittleren Gleitplattenschraube, die die Mutter antreibt, erreicht. Es gibt ein axiales Spiel am Schraubenwellenlager und ein axiales Spiel zwischen der Schraubenwelle und der Mutter. Beim Schneiden auf einer Drehbank wird die Spanfläche des Werkzeugs (mit der vorderen Ecke) der durch das Werkstück gegebenen Kraft P ausgesetzt (unter Ignorierung der Reibung zwischen dem Span und der Spanfläche). Zerlegt die Kraft P in Kraft Pz und Radialkraft. Die radiale Komponente ist die gleiche wie die Schneidrichtung des Schneidwerkzeugs. Es zeigt auf das Werkstück und schiebt das Werkzeug auf das Werkstück zu. Dies führt dazu, dass sich der mittlere Schlitten in die Richtung des Spiels bewegt, was das Biegen (Brechen) des Messers oder des Werkstücks verursacht.
2. Lösung
Wenn die Wendelsteigung größer ist und das Gewinde der linken und rechten Ausschneidemethode verwendet wird, sollte zusätzlich zur Einstellung der relevanten Parameter der Drehmaschine der Abstand zwischen dem Sattel und der Bettschiene eingestellt werden, um ihn etwas enger zu machen. Um die Reibung während der Bewegung zu erhöhen, wird die Möglichkeit von Turbulenzen im Sattel reduziert, aber dieser Spalt kann nicht zu fest eingestellt werden, so dass es angemessen ist, den Sattel gleichmäßig zu schütteln.
Stelle den Abstand des mittleren Skateboards ein, um den Abstand zu minimieren. Passe die Dichtigkeit des kleinen Skateboards an, um es etwas fester zu machen, um ein Drehen des Drehwerkzeugs beim Drehen zu verhindern. Die Länge des Werkstücks und der Werkzeugleiste sollte so weit wie möglich verkürzt werden, und die linke Hauptklinge sollte so weit wie möglich verwendet werden; Beim Schneiden mit der rechten Hauptklinge ist es notwendig, die Anzahl der Rückmesser zu reduzieren; Erhöhen Sie den Spanwinkel der rechten Hauptschneide. Die Kante der Schneidkante sollte gerade und scharf sein, um die axiale Kraftkomponente Px des Werkzeugs zu reduzieren. Je größer der Spanwinkel der rechten Hauptklinge, desto besser.
Drehen bezieht sich auf die Drehbearbeitung, die Teil der mechanischen Bearbeitung ist. Die Drehbearbeitung verwendet hauptsächlich Drehwerkzeuge, um das Werkstück zu drehen. Drehmaschinen werden hauptsächlich zur Bearbeitung von Wellen, Scheiben, Mänteln und anderen Werkstücken mit rotierenden Oberflächen verwendet. Sie sind die am weitesten verbreitete Art von Werkzeugmaschinen in Maschinenfabriken und Reparaturfabriken.
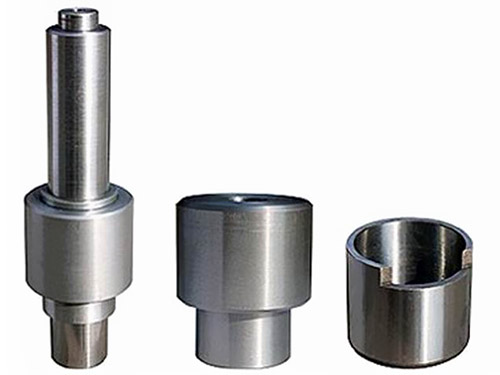
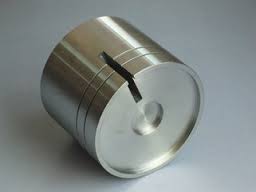
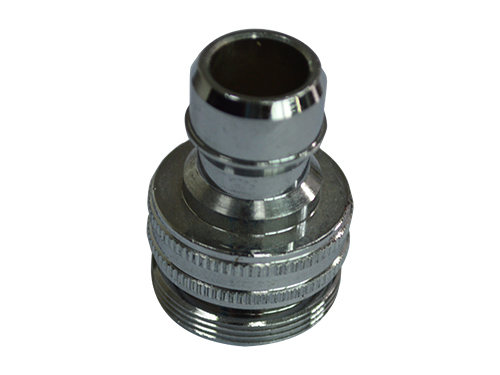
Technischer Brief
Auf der Drehbank werden die Form und die Größe des Rohlings durch die Drehbewegung des Werkstücks und die lineare oder gekrümmte Bewegung des Werkzeugs verändert, und es wird bearbeitet, um die Anforderungen der Zeichnungen zu erfüllen.
Drehen ist ein Verfahren zum Schneiden eines Werkstücks durch Drehen eines Werkstücks relativ zu einem Werkzeug auf einer Drehbank. Die Schneidenergie des Drehens wird hauptsächlich durch das Werkstück anstelle des Werkzeugs bereitgestellt. Drehen ist die grundlegendste und gängigste Methode des Schneidens und nimmt in der Produktion eine sehr wichtige Position ein. Das Drehen eignet sich für die Bearbeitung von Drehflächen. Die meisten Werkstücke mit einer Drehfläche können durch Drehen bearbeitet werden. Als innere und äußere zylindrische Oberflächen, innere und äußere konische Oberflächen, Endoberflächen, Nuten, Gewinde und rotierende Formungsoberflächen werden hauptsächlich Drehwerkzeuge verwendet. Drehmaschinen sind die am weitesten verbreitete Kategorie in allen Arten von spanenden Werkzeugmaschinen und machen etwa 50% der Gesamtzahl der Werkzeugmaschinen aus. Die Drehmaschine kann verwendet werden, um ein Werkstück mit einem Drehwerkzeug zu drehen, kann aber auch Bohrer, Reibahlen, Gewindebohrer und Rändelwerkzeuge zum Bohren, Reiben, Gewindeschneiden und Rändeln verwenden. Je nach den verschiedenen Eigenschaften des Verfahrens, des Layouts und der Strukturmerkmale können die Drehmaschinen in Horizontaldrehmaschinen, Bodenrotationsmaschinen, Vertikaldrehmaschinen, Revolverdrehmaschinen und Doppeldrehmaschinen, von denen die meisten Horizontaldrehmaschinen sind, unterteilt werden.
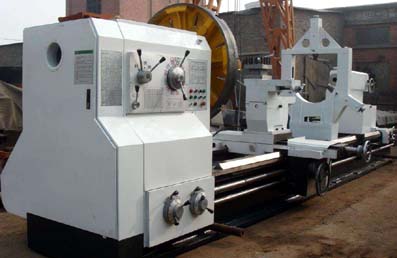
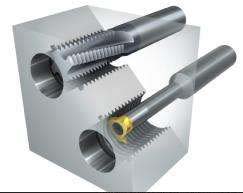
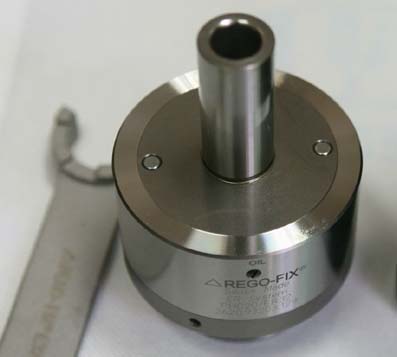
Technisches Problem
Die Drehbearbeitung ist der am weitesten verbreitete Typ in der Maschinenbauindustrie. Die Anzahl der Drehmaschinen ist groß, die Anzahl der Personen ist groß und die Verarbeitungsbreite ist groß. Es werden viele Werkzeuge und Vorrichtungen verwendet. Daher sind die sicherheitstechnischen und technischen Aspekte des Drehens besonders wichtig. Die wichtigsten Aufgaben sind wie folgt:
1, Späneschaden und Schutzmaßnahmen.
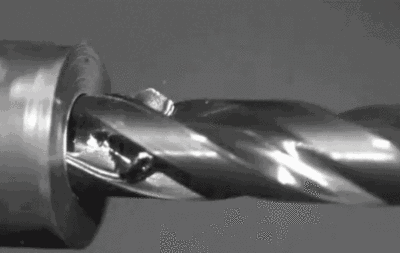
Die Stahlteile, die auf der Drehmaschine bearbeitet werden, sind flexibler, und die während des Drehens erzeugten Späne sind plastisch gekräuselt und haben scharfe Kanten. Beim Hochgeschwindigkeitsschneiden von Stahlteilen entstehen rote Hot-Spots und lange Späne, die sich sehr leicht verletzen und oft um Werkstücke, Drehwerkzeuge und Werkzeughalter gewickelt werden. Daher sollte der Haken rechtzeitig in der Arbeit gereinigt oder abgezogen werden. Wenn nötig, sollte es gestoppt und gelöscht werden. Es darf jedoch nicht von Hand entfernt oder gebrochen werden. Um Späneschäden zu verhindern, werden häufig Spänebrechen, Spänestromkontrolle und verschiedene Schutzschikanen eingesetzt. Die Spanbrechmaßnahme besteht darin, Spanbrecher oder Stufen auf dem Drehwerkzeug zu schleifen; Verwenden Sie einen geeigneten Spanbrecher und klemmen Sie das Werkzeug mechanisch fest.
2, Werkstückmontage.
Beim Drehen kommt es zu vielen Unfällen, wie zum Beispiel einer Beschädigung der Werkzeugmaschine aufgrund eines unsachgemäßen Einbaus des Werkstücks, eines Brechens oder Zusammenstürzens des Werkzeugs und eines Herausfallens oder Herausfliegens aus dem Werkstück.
Um eine sichere Produktion von Drehungen zu gewährleisten, muss daher beim Beladen von Werkstücken besondere Aufmerksamkeit geschenkt werden. Für Teile unterschiedlicher Größen und Formen müssen geeignete Vorrichtungen verwendet werden, unabhängig von der Verbindung von Dreibacken- und Vierbackenspannfuttern oder speziellen Vorrichtungen und Spindeln. Werkstücke müssen zwangsgeklemmt und geklemmt werden und große Werkstücke können geklemmt und ummantelt werden.
Wenn das Werkstück mit einer hohen Geschwindigkeit gedreht wird und die Schneidkraft ausgeübt wird, wird es nicht verschoben, fällt ab und schleudert nicht. Bei Bedarf kann es durch den oberen Mittel- und Mittelrahmen verstärkt werden. Verriegelung, sofort nach dem Entfernen des Schraubenschlüssels.
3, sicherer Betrieb.
Vor der Arbeit müssen wir die Maschine vollständig inspizieren und bestätigen, dass sie für die Verwendung geeignet ist. Die Montage des Werkstücks und des Werkzeugs stellt sicher, dass die Position korrekt, fest und zuverlässig ist. Während der Bearbeitung muss das Werkzeug beim Werkzeugwechsel, beim Be- und Entladen des Werkstücks und beim Messen des Werkstücks angehalten werden. Das Werkstück darf beim Drehen nicht mit der Hand berührt oder mit Baumwolle abgewischt werden. Um die Schnittgeschwindigkeit, Vorschubgeschwindigkeit und Spannungstiefe richtig zu wählen, ist keine Überlastbearbeitung erlaubt. Es dürfen keine Werkstücke, Arbeitsklammern und andere Ablagerungen auf der Werkzeugauflage und der Bettoberfläche platziert werden. Wenn Sie eine Reibe verwenden, bewegen Sie das Drehwerkzeug in eine sichere Position, mit der rechten Hand auf der Vorderseite und der linken Hand auf der Rückseite, um zu verhindern, dass die Ärmel eingreifen. Die Werkzeugmaschine muss jemanden haben, der für den Gebrauch und die Wartung verantwortlich ist, und anderes Personal darf sie nicht benutzen.
Vorsichtsmaßnahmen
Der Prozess der CNC-Drehbearbeitung ist ähnlich dem von gewöhnlichen Drehmaschinen. Aufgrund der Tatsache, dass die CNC-Drehmaschine einmal installiert ist und alle Dreharbeiten automatisch abgeschlossen werden, sollten die folgenden Aspekte beachtet werden.
1. Angemessene Wahl der Schnittmenge:
Für das hocheffiziente Schneiden von Metall sind die zu bearbeitenden Materialien, Schneidwerkzeuge und Schneidbedingungen drei Hauptfaktoren. Diese bestimmen Bearbeitungszeit, Standzeit und Bearbeitungsqualität. Die wirtschaftliche und effektive Verarbeitungsmethode muss eine vernünftige Wahl der Schnittbedingungen sein. Die drei Elemente der Schneidbedingungen: Schnittgeschwindigkeit, Vorschubgeschwindigkeit und Schnitttiefe verursachen direkt Werkzeugschäden. Mit der Erhöhung der Schneidgeschwindigkeit wird die Temperatur der Werkzeugspitze erhöht und es wird mechanischer, chemischer und thermischer Verschleiß erzeugt. Schnittgeschwindigkeit um 20% erhöht, Standzeit um 1/2 reduziert. Der Vorschubzustand und der Verschleiß hinter dem Werkzeug werden in einem sehr kleinen Bereich erzeugt. Die Vorschubgeschwindigkeit ist jedoch groß, die Schneidtemperatur steigt an und der hintere Verschleiß ist groß. Es hat weniger Einfluss auf das Werkzeug als die Schnittgeschwindigkeit. Die Wirkung des tiefen Schneidens auf das Schneidwerkzeug Obwohl es keine Schnittgeschwindigkeit und Vorschubmenge gibt, hat das zu schneidende Material bei geringer Schnitttiefe eine gehärtete Schicht, die sich auch auf die Lebensdauer des Schneidwerkzeugs auswirkt. Der Benutzer wählt die zu verwendende Schnittgeschwindigkeit basierend auf dem zu bearbeitenden Material, Härte, Schneidbedingung, Materialtyp, Vorschubmenge, Schnitttiefe und dergleichen. Die Auswahl der am besten geeigneten Verarbeitungsbedingungen wird auf der Grundlage dieser Faktoren ausgewählt. Regelmäßiger und stabiler Verschleiß ist die ideale Voraussetzung, um die Lebenserwartung zu erreichen. Im tatsächlichen Betrieb hängt die Wahl der Werkzeugstandzeit jedoch vom Werkzeugverschleiß, der Größe der bearbeiteten Maschine, der Oberflächenqualität, dem Schneidgeräusch und der Bearbeitungswärme ab. Bei der Festlegung der Verarbeitungsbedingungen ist es erforderlich, die Forschung nach den tatsächlichen Bedingungen durchzuführen. Für schwer zu bearbeitende Materialien wie Edelstahl und hitzebeständige Legierungen können Kühlmittel oder starre Klingen verwendet werden.
2. Angemessene Wahl der Werkzeuge:
(1) Wählen Sie beim Schruppen ein Werkzeug mit hoher Festigkeit und guter Haltbarkeit, um den Anforderungen einer großen Schnitttiefe und einer großen Vorschubmenge beim Schruppen gerecht zu werden.
(2) Nach dem Drehen müssen Werkzeuge mit hoher Präzision und guter Haltbarkeit ausgewählt werden, um die Bearbeitungsgenauigkeit zu gewährleisten.
(3) Um die Werkzeugwechselzeit zu reduzieren und die Werkzeugeinstellung zu erleichtern, sollten Klemme und Klinge so weit wie möglich verwendet werden.
3. Wählen Sie die Leuchte angemessen aus:
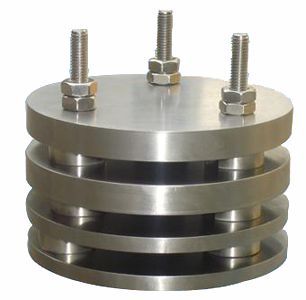
(2) Die Teilepositionierungsreferenz stimmt überein, um den Positionierungsfehler zu reduzieren.
4. Bestimmen Sie die Verarbeitungsroute:
Die Bearbeitungsroute ist die Bahn und die Richtung des Werkzeugs relativ zu dem Teil der indexgesteuerten Werkzeugmaschinenbearbeitung.
(1) Es sollte in der Lage sein, Verarbeitungsgenauigkeit und Anforderungen an die Oberflächenrauhigkeit zu gewährleisten;
(2) Die Verarbeitungsstrecke sollte so weit wie möglich verkürzt werden, um die Leerlaufzeit des Werkzeugs zu verringern.
5. Bearbeitungsweg und Bearbeitungszugabe:
Unter der Bedingung, dass CNC-Drehmaschinen keine universelle Verwendung gefunden haben, sollte im Allgemeinen eine übermäßige Toleranz für Rohlinge, insbesondere die Erlaubnis zum Schmieden und Gießen von Hardcover, auf gewöhnlichen Drehmaschinen bearbeitet werden. Wenn Sie die CNC-Drehbearbeitung verwenden müssen, müssen Sie auf die flexible Anordnung des Programms achten.
6. Fixture Installationspunkte:
Die Verbindung zwischen dem Hydrodehnspannfutter und dem hydraulischen Spannzylinder wird durch die Zugstange erreicht. Die wichtigsten Punkte der hydraulischen Futterspannung sind wie folgt:
Entfernen Sie zuerst die Mutter des Hydraulikzylinders mit einer Hand, entfernen Sie das Zugrohr und ziehen Sie das Spannfutter vom hinteren Ende der Spindel ab. Entfernen Sie dann die Befestigungsschraube des Spannfutters, um das Spannfutter zu entfernen.
Allgemeine Regeln
Allgemeine Verarbeitungsverfahren für die Verarbeitung aktivieren (JB / T9168.2-1998)
Werkzeugeinstellung
1) Der Werkzeugschaft ragt aus dem Werkzeughalter und sollte nicht zu lang sein. Die allgemeine Länge sollte die 1,5-fache Höhe der Werkzeugleiste nicht überschreiten (außer Loch, Schlitz usw.)
2) Die Mittellinie des Drehwerkzeughalters sollte senkrecht oder parallel zur Schnittrichtung sein.
3) Einstellung der Höhe der Messerspitze:
(1) Wenn eine Fläche gedreht wird, eine konische Fläche gedreht wird, Gewinde gedreht werden, eine Formfläche gedreht wird und ein festes Werkstück geschnitten wird, sollte die Schneidkante im Allgemeinen auf der gleichen Höhe wie die Werkstückachse sein.
(2) Das Schrupprad, das Schlichtloch und die Werkzeugspitze sollten generell etwas höher als die Werkstückachse sein.
(3) Wenn der schlanke Schaft, das raue Loch und das hohle Werkstück abgeschnitten werden, sollte die Werkzeugspitze im Allgemeinen etwas niedriger als die Werkstückachse sein.
4) Die Winkelhalbierende des Gewindewinkels des Gewindedrehwerkzeugs sollte senkrecht zur Werkstückachse stehen.
5) Beim Einsetzen des Drehwerkzeugs sollte die Unterlegscheibe unter der Werkzeugleiste klein und flach sein, und die Schraube, die das Drehwerkzeug drückt, sollte festgezogen werden.
Montage des Werkstücks
1) Bei Verwendung eines Drei-Backen-Zentrierspannfutters zum Spannen von Werkstücken zum Schruppen und Schlichten, wenn der Werkstückdurchmesser kleiner als 30 mm ist, darf die Überhanglänge nicht größer als das 5-fache des Durchmessers sein, wenn der Werkstückdurchmesser größer als 30 mm ist , Seine Überhanglänge sollte nicht mehr als das 3-fache des Durchmessers betragen.
2) Bei Verwendung eines Vierbacken-Einfachspannfutters, einer Planscheibe, eines Winkeleisens (Biegeplatte) usw. zum Spannen von unregelmäßig gewichteten Werkstücken muss Gewicht hinzugefügt werden.
3) Bei der Bearbeitung eines Schaft-Werkstücks an der Spitze der Welle muss die Reitstockmittelachse vor dem Drehen mit der Achse der Drehmaschinenspindel übereinstimmen.
Bei der Verarbeitung sollte darauf geachtet werden, dass die obere Dichtigkeit eingestellt wird, wobei der obere Totpunkt und der mittlere Rahmen beachtet werden sollten Schmierung
5) Bei Verwendung des Reitstocks sollte die Hülse so kurz wie möglich sein, um Vibrationen zu reduzieren.
6) Wenn die Vertikaldrehmaschine festgeklemmt ist, ist die Auflagefläche klein und die Werkstückhöhe ist hoch, die erhöhte Klaue sollte verwendet werden, und das Werkstück sollte an der geeigneten Stelle mit einer Zugstange oder einer Pressplatte gedrückt werden.
7) Beim Drehen von Rädern und Gussstücken muss die unfertige Oberfläche korrigiert werden, um nach der Bearbeitung eine gleichmäßige Wandstärke zu gewährleisten.
Drehung
1) Beim Drehen der Stufenwelle sollte generell der Teil mit dem größeren Durchmesser zuerst gedreht werden und der Teil mit dem kleineren Durchmesser sollte später gedreht werden, um die Steifigkeit während des Drehens sicherzustellen.
2) wenn die Welle Schneidnuten an einem Werkstück aufweist, die vor dem Fertigbearbeiten auszuführen sind, um eine Verformung des Werkstücks zu verhindern.
3) Wenn eine Gewindewelle fein gedreht wird,
Nach dem Einfädeln wird der nicht gewindete Teil präzisionsgedreht.
4) vor dem Bohren sollte die Stirnfläche des Werkstücks flachgedreht werden. Bohren Sie bei Bedarf zuerst das mittlere Loch.
5) Beim Bohren tiefer Löcher wird in der Regel zuerst das Pilotloch gebohrt.
6) Beim Drehen von (Φ10-Φ20) mm Löchern sollte der Durchmesser des Werkzeugschaftes das 0,6-0,7 fache des Durchmessers der bearbeiteten Bohrung betragen; Wenn der Durchmesser des Lochs größer als 20 mm ist, sollte der Messerhalter mit Klemmkopf verwendet werden.
7) Beim Drehen einer Mehrkopf- oder Mehrkopfschraube Nach dem Einstellen der Wechselräder einen Probeschnitt durchführen.
8) Wenn Sie den Drehautomaten verwenden, stellen Sie die relative Position des Werkzeugs und des Werkstücks entsprechend der Einstellkarte der Werkzeugmaschine ein. Nach der Einstellung ist es notwendig, das Probedrehen durchzuführen. Nachdem das erste Stück qualifiziert wurde, kann es bearbeitet werden; Während des Bearbeitungsprozesses wird immer der Verschleiß des Werkzeugs, die Werkstückgröße und die Oberflächenrauhigkeit berücksichtigt.
9) Beim Einschalten einer Vertikaldrehmaschine darf der Balken beim Einstellen des Messerhalters nicht frei bewegt werden. Beim Einschalten der Vertikaldrehmaschine darf der Querträger nach dem Einstellen der Werkzeugablage nicht beliebig bewegt werden.
10) Wenn die relevante Oberfläche des Werkstücks Positionstoleranzen aufweist, wird das Drehen in einer einzigen Spannung so weit wie möglich durchgeführt.
11) Beim Drehen eines Stirnradzahnrohlings müssen die Bohrung und die Referenzstirnfläche in einer Aufspannung bearbeitet werden. Wenn nötig, sollte die Markierungslinie nahe dem Ende des Zahnrad-Indexkreises gezeichnet werden.
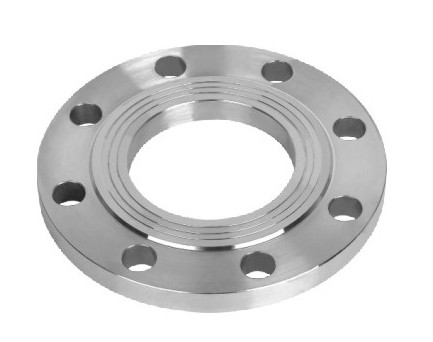
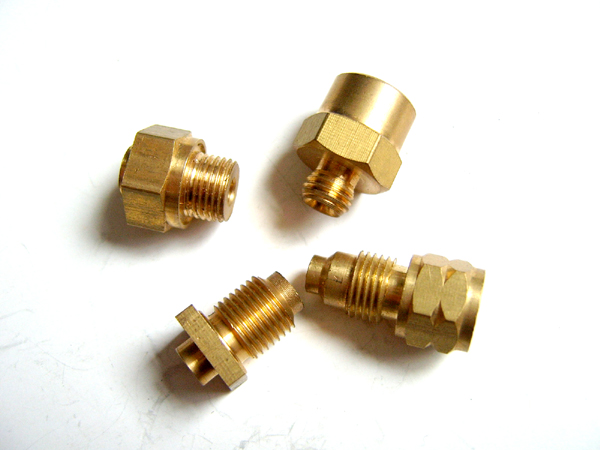
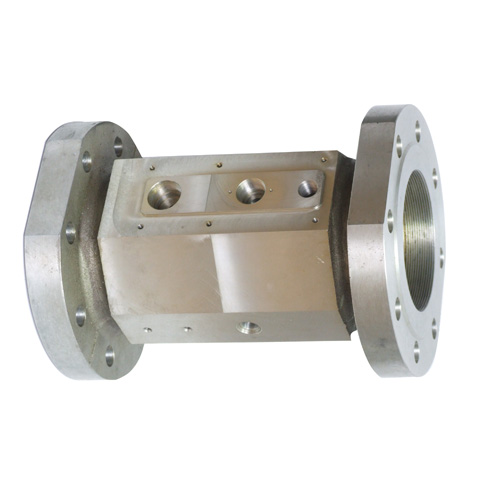
Moderne Maschinenbautechnologie entwickelt sich zu hoher Effizienz, hoher Qualität, hoher Präzision, hoher Integration und hoher Intelligenz. Die Präzisions- und Ultrapräzisionsbearbeitungstechnologie ist zur wichtigsten Komponente und Richtung der Entwicklung im modernen Maschinenbau geworden und hat sich zu einer Schlüsseltechnologie für die Verbesserung der internationalen Wettbewerbsfähigkeit entwickelt. Der sich drehende Bearbeitungsfehler ist mit der umfangreichen Anwendung der Präzisionsbearbeitung ein heißes Forschungsthema geworden. Da thermische Fehler und geometrische Fehler für die meisten der verschiedenen Fehler in der Werkzeugmaschine verantwortlich sind, ist die Reduzierung dieser zwei Fehler, insbesondere der thermischen Fehler, das Hauptziel geworden. Fehlerkompensationstechnologie (ECT) entstand mit der kontinuierlichen Entwicklung von Wissenschaft und Technologie. Die durch die thermische Verformung der Werkzeugmaschine verursachten Verluste sind beträchtlich. Daher ist es extrem notwendig, ein hochpräzises, kostengünstiges thermisches Fehlerkompensationssystem zu entwickeln, das die tatsächlichen Produktionsanforderungen der Fabrik erfüllen kann, um thermische Fehler zwischen der Spindel (oder dem Werkstück) und dem Schneidwerkzeug zu korrigieren. Um die Genauigkeit von Werkzeugmaschinen zu verbessern, Abfall zu reduzieren, Produktionseffizienz zu erhöhen und wirtschaftliche Vorteile.
Grundlegende Definition
Die Grunddefinition der Fehlerkompensation besteht darin, künstlich einen neuen Fehler zu erzeugen, um den ursprünglichen Fehler, der derzeit ein Problem darstellt, zu löschen oder stark zu reduzieren. Durch Analyse, Statistik, Induktion und Beherrschung der Eigenschaften und Gesetzmäßigkeiten des ursprünglichen Fehlers wurde das mathematische Fehlermodell erstellt, um zu versuchen, den künstlich erzeugten Fehler gleich dem ursprünglichen Fehler und in der entgegengesetzten Richtung zu machen, wodurch der Bearbeitungsfehler reduziert und verbessert wurde die Maßgenauigkeit des Teils.
Die früheste Fehlerkompensation wurde durch Hardware erreicht. Hardware-Kompensation ist eine mechanische feste Kompensation. Um den Korrekturbetrag zu ändern, wenn sich der Werkzeugmaschinenfehler ändert, müssen Sie Teile, Kalibrierungsregeln neu erstellen oder den Kompensationsmechanismus neu einstellen. Die Hardware-Kompensation hat auch den Nachteil, zufällige Fehler und mangelnde Flexibilität nicht zu lösen.
[1] Die Entwicklung der Softwarekompensation ist durch den umfassenden Einsatz modernster Technologie und Computersteuerungstechnologie verschiedener Disziplinen gekennzeichnet, um die Genauigkeit von Werkzeugmaschinen ohne Änderungen an der Werkzeugmaschine selbst zu verbessern. Die Software-Kompensation überwindet viele der Schwierigkeiten und Nachteile der Hardware-Kompensation und bringt die Vergütungstechnologie auf eine neue Stufe.
Charakteristisch
Fehlerkompensation (Technologie) hat zwei Hauptmerkmale: Wissenschaft und Technik.
Die schnelle Entwicklung der wissenschaftlichen Fehlerkompensationstechnologie hat die Theorie des mechanischen Präzisionsdesigns, der Präzisionsmessung und der gesamten Feinmechanik stark bereichert und ist zu einem wichtigen Zweig dieser Disziplin geworden. Techniken, die sich auf die Fehlerkompensation beziehen, umfassen Erkennungstechnologie, Sensortechnologie, Signalverarbeitungstechnologie, photoelektrische Technologie, Materialtechnologie, Computertechnologie und Steuerungstechnologie. Als Technologiezweig hat die Fehlerkompensationstechnologie ihre eigenen unabhängigen Inhalte und Eigenschaften. Weitere Forschungen über Fehlerkompensationstechniken, um sie theoretisch und systematisch zu machen, werden von großer wissenschaftlicher Bedeutung sein.
Die technische Bedeutung der technischen Fehlerkompensationstechnologie ist sehr bedeutend, sie enthält drei Bedeutungsebenen:
Erstens kann die Verwendung der Fehlerkompensationstechnologie leicht das Niveau an Genauigkeit erreichen, das "harte Technologie" kosten kann, um zu erreichen;
Die zweite ist die Verwendung von Fehlerkompensationstechniken, die das Niveau an Genauigkeit lösen können, das "harte Technologie" normalerweise nicht erreichen kann;
Drittens, wenn die Fehlerkompensationstechnologie unter gewissen Genauigkeitsanforderungen eingesetzt wird, können die Kosten der Instrumenten- und Geräteherstellung stark reduziert werden, was sehr signifikante wirtschaftliche Vorteile hat.
Drehbearbeitung thermische Fehlererzeugung und -klassifizierung
Mit der weiteren Verbesserung der Präzisionsanforderungen der Werkzeugmaschine wird der Anteil thermischer Fehler am Gesamtfehler weiter zunehmen. Die thermische Verformung der Werkzeugmaschine ist zu einem Haupthindernis geworden, um die Bearbeitungsgenauigkeit zu verbessern. Der thermische Fehler der Werkzeugmaschine wird hauptsächlich durch die thermische Verformung der Werkzeugmaschinenkomponenten verursacht, die durch Wärmequellen innerhalb und außerhalb der Maschine verursacht wird, wie Motoren, Lager, Getriebeteile, Hydrauliksysteme, Umgebungstemperatur und Kühlmittel. Der Werkzeugmaschinengeometriefehler ergibt sich aus den Fertigungsfehlern der Werkzeugmaschine, dem Anpassungsfehler zwischen den Werkzeugmaschinenkomponenten, der dynamischen und statischen Verschiebung der Werkzeugmaschinenkomponenten und so weiter.
Grundlegende Methode der Fehlerkompensation
Zusammenfassend und in Bezug genommene Referenzen zeigen, dass der Abbiegefehler im Allgemeinen durch die folgenden Faktoren verursacht wird:
Thermischer Verformungsfehler der Werkzeugmaschine;
Geometrische Fehler in Teilen und Strukturen von Werkzeugmaschinen;
Schnittkraft induzierter Fehler;
Werkzeugabnutzungsfehler;
Andere Fehlerquellen, wie Servofehler in Werkzeugmaschinenachsen, CNC-Interpolationsalgorithmusfehler usw.
Es gibt zwei grundlegende Methoden zur Verbesserung der Werkzeugmaschinengenauigkeit: Fehlervermeidungsmethode und Fehlerkompensationsmethode.
Das Fehlervermeidungsverfahren versucht, mögliche Fehlerquellen durch Entwurfs- und Herstellungsansätze zu beseitigen oder zu reduzieren. Das Fehlerverhinderungsverfahren ist wirksam, um den Temperaturanstieg der Wärmequelle zu verringern, das Temperaturfeld auszugleichen und die thermische Verformung der Werkzeugmaschine in einem gewissen Ausmaß zu verringern. Es ist jedoch unmöglich, die thermische Verformung vollständig zu eliminieren, und die Kosten sind sehr teuer; Die Anwendung des thermischen Fehlerausgleichsgesetzes eröffnet eine effektive und kostengünstige Möglichkeit, die Genauigkeit von Werkzeugmaschinen zu verbessern.
Zugehörige Schlussfolgerungen
Die Erforschung von Bearbeitungsfehlern ist die wichtigste Komponente und Richtung der Entwicklung im modernen Maschinenbau und hat sich zu einer Schlüsseltechnologie für die Verbesserung der internationalen Wettbewerbsfähigkeit entwickelt. Der Fehler wird auf viele Arten erzeugt. Die Analyse und Erforschung von thermischen Fehlern ist hilfreich, um die Drehpräzision und die technischen Anforderungen zu verbessern.
Die Fehlerkompensationstechnologie kann die hohe Präzision und niedrigen Kosten der tatsächlichen Produktionsanforderungen der Fabrik erfüllen. Die thermische Fehlerkompensationstechnologie kann den thermischen Driftfehler zwischen der Spindel (oder dem Werkstück) und dem Schneidwerkzeug korrigieren, die Bearbeitungsgenauigkeit der Werkzeugmaschine verbessern, Abfallprodukte reduzieren, die Produktionseffizienz erhöhen und wirtschaftliche Vorteile bieten.
häufiges Problem
Wenn die gewöhnliche Drehmaschine einen großen Gewindegang dreht, tritt manchmal eine Sattelvibration auf, und die Bearbeitungsoberfläche ist gewellt, und die schwere ist ein Frakturiermesser.
Und wenn sie geschnitten werden, haben die Arbeiter oft ein Messer oder ein Schnittmesserphänomen.
Es gibt viele Gründe für die obigen Probleme. Jetzt diskutieren wir hauptsächlich das Phänomen und die Lösungen, indem wir die Kraftbedingungen der Werkzeuge analysieren.
1. Die Ursache des Problems und seine Ursachen
wir wissen:
Wenn ein Gewinde mit einer kleinen Steigung gedreht wird, wird im allgemeinen ein Verfahren zum Schneiden eines geraden Messers (ein geradliniger Vorschub in der Richtung senkrecht zu der Werkstückachse) verwendet;
Wenn ein Gewinde mit einer großen Steigung gedreht wird, werden oft die Messermethoden des linken und rechten Messers verwendet, um die Schneidkraft zu reduzieren. (Durch Bewegen des kleinen Skateboards, um das Fadendrehwerkzeug mit der linken bzw. rechten Schneide zu schneiden).
Beim Drehen des Fadens wird die Bewegung des Sattels durch die Drehung der langen Schraube erreicht, um die Bewegung der Öffnungs- und Schließmutter zu steuern. Am Lager der langen Schraube gibt es ein axiales Spiel, und zwischen der langen Schraube und der Öffnungsmutter besteht ein axiales Spiel. Wenn die rechte Hauptschneide der rechtshändigen Schnecke durch das Links-Rechts-Entgratschneidverfahren stark bearbeitet wird, wird das Werkzeug der Kraft P ausgesetzt, die ihm vom Werkstück gegeben wird (wobei die Reibung zwischen dem Span und der Spanfläche ignoriert wird). und die Kraft P wird in eine axiale Komponente Px und eine radiale Komponente zerlegt, wobei die axiale Komponente Px und der Vorschub des Werkzeugs in der gleichen Richtung das Werkzeug über diese axiale Komponente Px zum Sattel führt. Somit wird der Bettsattel zur Seite des Spalts gedrückt, um schnelle und schnelle Bewegungen vor und zurück zu machen. Infolgedessen wird das Werkzeug hin- und herbewegt, und die Bearbeitungsoberfläche ist gewellt und sogar gebrochen. Beim Schneiden mit der linken Hauptschneide gibt es jedoch kein solches Phänomen. Beim Schneiden mit der linken Hauptschneide ist die axiale Kraftkomponente Px des Werkzeugs entgegengesetzt zur Vorschubrichtung und die Freiraumrichtung ist eliminiert. Zu diesem Zeitpunkt bewegt sich der Sattel mit einer gleichmäßigen Geschwindigkeit. .
Beim Abschneiden wird die Bewegung der mittleren Gleitplatte durch die Drehung der mittleren Gleitplattenschraube, die die Mutter antreibt, erreicht. Es gibt ein axiales Spiel am Schraubenwellenlager und ein axiales Spiel zwischen der Schraubenwelle und der Mutter. Beim Schneiden auf einer Drehbank wird die Spanfläche des Werkzeugs (mit der vorderen Ecke) der durch das Werkstück gegebenen Kraft P ausgesetzt (unter Ignorierung der Reibung zwischen dem Span und der Spanfläche). Zerlegt die Kraft P in Kraft Pz und Radialkraft. Die radiale Komponente ist die gleiche wie die Schneidrichtung des Schneidwerkzeugs. Es zeigt auf das Werkstück und schiebt das Werkzeug auf das Werkstück zu. Dies führt dazu, dass sich der mittlere Schlitten in die Richtung des Spiels bewegt, was das Biegen (Brechen) des Messers oder des Werkstücks verursacht.
Beim Abschneiden wird die Bewegung der mittleren Gleitplatte durch die Drehung der mittleren Gleitplattenschraube, die die Mutter antreibt, erreicht. Es gibt ein axiales Spiel am Schraubenwellenlager und ein axiales Spiel zwischen der Schraubenwelle und der Mutter. Beim Schneiden auf einer Drehbank wird die Spanfläche des Werkzeugs (mit der vorderen Ecke) der durch das Werkstück gegebenen Kraft P ausgesetzt (unter Ignorierung der Reibung zwischen dem Span und der Spanfläche). Zerlegt die Kraft P in Kraft Pz und Radialkraft. Die radiale Komponente ist die gleiche wie die Schneidrichtung des Schneidwerkzeugs. Es zeigt auf das Werkstück und schiebt das Werkzeug auf das Werkstück zu. Dies führt dazu, dass sich der mittlere Schlitten in die Richtung des Spiels bewegt, was das Biegen (Brechen) des Messers oder des Werkstücks verursacht.
2. Lösung
Wenn die Wendelsteigung größer ist und das Gewinde der linken und rechten Ausschneidemethode verwendet wird, sollte zusätzlich zur Einstellung der relevanten Parameter der Drehmaschine der Abstand zwischen dem Sattel und der Bettschiene eingestellt werden, um ihn etwas enger zu machen. Um die Reibung während der Bewegung zu erhöhen, wird die Möglichkeit von Turbulenzen im Sattel reduziert, aber dieser Spalt kann nicht zu fest eingestellt werden, so dass es angemessen ist, den Sattel gleichmäßig zu schütteln.
Stelle den Abstand des mittleren Skateboards ein, um den Abstand zu minimieren. Passe die Dichtigkeit des kleinen Skateboards an, um es etwas fester zu machen, um ein Drehen des Drehwerkzeugs beim Drehen zu verhindern. Die Länge des Werkstücks und der Werkzeugleiste sollte so weit wie möglich verkürzt werden, und die linke Hauptklinge sollte so weit wie möglich verwendet werden; Beim Schneiden mit der rechten Hauptklinge ist es notwendig, die Anzahl der Rückmesser zu reduzieren; Erhöhen Sie den Spanwinkel der rechten Hauptschneide. Die Kante der Schneidkante sollte gerade und scharf sein, um die axiale Kraftkomponente Px des Werkzeugs zu reduzieren. Je größer der Spanwinkel der rechten Hauptklinge, desto besser.