CNC-Bearbeitungsprozess
Verarbeitungsgrundsätze
(1) Die Verarbeitung des obigen Arbeitsverfahrens kann die Positionierung und das Festklemmen des nächsten Arbeitsvorgangs nicht beeinflussen.
(2) Zuerst innen und außen, dh der innere Hohlraum (inneres Loch) wird zuerst bearbeitet und dann wird die äußere Form bearbeitet.
(3) Prozesse, die von demselben Werkzeug oder demselben Werkzeug bearbeitet werden, werden vorzugsweise kontinuierlich ausgeführt, um Fehler zu reduzieren, die durch Neupositionierung oder Werkzeugwechsel verursacht werden.
(4) In der gleichen Installation sollte zuerst der Prozess ausgeführt werden, der die Steifigkeit des Werkstücks nur wenig beeinflusst.
Verarbeitungsroute
Die Bearbeitungsroute der CNC-Drehmaschinenzuführung bedeutet, dass das Drehwerkzeug seine Bewegung vom Werkzeugeinstellpunkt (oder dem festen Ursprung der Werkzeugmaschine) beginnt, bis es an diesen Punkt zurückkehrt und das Bearbeitungsprogramm beendet wird, einschließlich Messern Einschneiden, Schneiden Out und ein nicht schneidender freier Weg.
Der Beschickungsweg für die Endbearbeitung wird grundsätzlich entlang der Umrisse seiner Teile ausgeführt, wobei das Hauptaugenmerk des Bestimmens des Beschickungsweges darin liegt, den Beschickungsweg für Schruppen und Leerweg zu bestimmen.
In der CNC-Drehmaschinenbearbeitung folgt die Bestimmung von Bearbeitungswegen im Allgemeinen den folgenden Prinzipien:
1. Die Genauigkeit und Oberflächenrauhigkeit des zu bearbeitenden Werkstücks sollte gewährleistet sein.
2. Minimiere die Verarbeitungsroute, reduziere die Leerlaufzeit und verbessere die Effizienz der Verarbeitung.
3. Vereinfachen Sie den Arbeitsaufwand der numerischen Berechnung so weit wie möglich und vereinfachen Sie die Verarbeitung.
4. Verwenden Sie Unterprogramme für einige wiederverwendbare Programme.
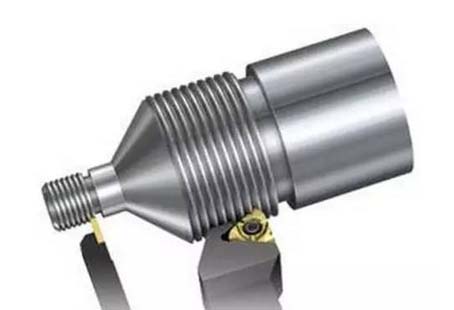
Indem das Bearbeitungsprogramm den kürzesten Vorschubweg hat, wird nicht nur die Ausführungszeit des gesamten Bearbeitungsprozesses eingespart, sondern auch der unnötige Werkzeugverbrauch und der Verschleiß gleitender Teile des Maschinenvorschubs reduziert. Der Typ der kürzesten Route und ihre Implementierung sind wie folgt:
(1) Die kürzeste Zustellroute. Der kürzeste Schneidvorschubweg kann die Produktionseffizienz effektiv erhöhen und den Werkzeugverschleiß reduzieren. Bei der Anordnung des kürzesten Schneidvorschubs muss auch die Steifigkeit und Bearbeitbarkeit des Werkstücks gewährleistet sein.
(2) Die kürzeste nicht schneidende Hubstrecke.
Mit Messerspitzen. Allgemein rechteckige Schleife beispielhaftes Aufrauen. Der Werkzeugpunkt A wird unter Berücksichtigung der Notwendigkeit eines zweckmäßigen Werkzeugwechsels während des Fertigbearbeitungsprozesses eingestellt und wird daher an einer Stelle weit entfernt von dem Rohling eingestellt. Gleichzeitig fällt der Startpunkt mit dem Werkzeugpunkt zusammen.
Richten Sie einen Werkzeugwechselpunkt geschickt ein. Um den Komfort und die Sicherheit des Werkzeugwechsels zu berücksichtigen, wird manchmal auch der Werkzeugwechselpunkt in einem Abstand von dem leeren Teil eingestellt.
An der Stelle wird dann, wenn das zweite Messer gewechselt wird, der Verlauf des nichtschneidenden Hubes während der Endbearbeitung länger sein; Wenn der Werkzeugwechselpunkt des zweiten Messers ebenfalls auf die mittlere Punktposition eingestellt ist, kann die nichtschneidende Hubstrecke verkürzt werden.
Ordnen Sie die "Null-Rückkehr" -Route vernünftig an. Beim manuellen Kompilieren komplexer Konturbearbeitungsprogramme wird der Berechnungsprozess zur einfachen Verifizierung vereinfacht. Der Programmierer legt manchmal den Endpunkt des Werkzeugs nach der Verarbeitung jedes Werkzeugs fest. Durch Ausführen einer "Zurück zu Null" -Betriebsanweisung werden alle von ihnen zu der Position der Werkzeugtrennstelle zurückgebracht, und dann wird das nachfolgende Programm ausgeführt. Dies erhöht die Entfernung der Fütterungsroute und verringert die Produktionseffizienz. Daher sollte der Abstand zwischen dem Endpunkt des vorhergehenden Messers und dem Startpunkt des nächsten Messers so kurz wie möglich sein, wenn die "Nullrückführ" -Route vernünftig angeordnet ist. Oder Null, um die kürzesten Anforderungen der Futterroute zu erfüllen. Zusätzlich wird bei der Rückkehr zum Befehl zum Schneiden des Schneidwerkzeugs der gleichzeitige Befehl "Rückkehr zu Null" der X-Achse und der Z-Achse so weit wie möglich ohne Interferenz verwendet, und der "Rücksprung" wird verwendet -to-zero "Route dieser Funktion ist die kürzeste.
(3) grober Rand raue Leiter, die Zufuhrlinie schneiden. Die Schneidvorschubrichtungen von zwei Arten von großen Rohlings sind aufgelistet. Es ist die falsche Schrittschneide, das Schneiden in der Reihenfolge von 1 Eimer 5, die restliche Menge von jedem Schnitt ist gleich, es ist der korrekte Schritt, der Zufuhrweg schneidet. Wegen des gleichen Rückens der Schneide.
(4) Kontinuierlicher Schneidvorschubweg für die Teilkonturbearbeitung. Die Endbearbeitung von Teilekonturen kann mit einer oder mehreren Messerendbearbeitungsoperationen durchgeführt werden. Das fertige Profil sollte vom letzten Messer aus kontinuierlich bearbeitet werden. Zu diesem Zeitpunkt sollte die Position des Werkzeugs richtig ausgewählt werden. Versuchen Sie nicht, Einschnitte anzuordnen und auszuschneiden, Werkzeuge zu wechseln und in kontinuierlichen Konturen zu pausieren. Um plötzliche Schnittkraftänderungen zu vermeiden und das Gleichgewicht der Prozesssysteme zu zerstören. Dies führt zu Kratzern, plötzlichen Formänderungen oder Stagnation der Teile auf der Kontur des Teils.
(5) Spezielle Futterrouten. Im CNC-Drehen, unter normalen Umständen. Der Längsvorschub des Werkzeugs wird entlang der negativen Richtung der Koordinaten durchgeführt. Es ist jedoch manchmal unangemessen, eine Fütterungsroute in ihrer üblichen negativen Richtung anzuordnen. Es kann sogar das Werkstück beschädigen.
Vorteile und Nachteile
Die CNC-Bearbeitung hat folgende Vorteile:
1. Die Anzahl der Kleider ist stark reduziert und Teile mit komplexen Formen benötigen keine komplizierten Kleider. Wenn Sie die Form und Größe von Teilen ändern möchten, müssen Sie nur das Teileverarbeitungsprogramm ändern, das für die Entwicklung und Änderung neuer Produkte geeignet ist.
2. Die Verarbeitungsqualität ist stabil, die Verarbeitungsgenauigkeit ist hoch und die Wiederholgenauigkeit ist hoch und sie kann die Verarbeitungsanforderungen des Flugzeugs erfüllen.
3. Die hohe Produktionseffizienz bei der Mehrsorten- und Kleinserienfertigung kann die Zeit für die Produktionsvorbereitung, die Werkzeugmaschineneinstellung und die Prozessinspektion verkürzen und die Schneidzeit durch den Einsatz der optimalen Schnittmenge reduzieren.
4. Bearbeitbare komplexe Oberflächen, die mit herkömmlichen Methoden schwer zu bearbeiten sind, können bearbeitet werden, und sogar bearbeitete Teile, die nicht beobachtbar sind, können bearbeitet werden. Der Nachteil der CNC-Bearbeitung besteht darin, dass Werkzeugmaschinenausrüstung teuer ist und das Wartungspersonal einen hohen Bedarf hat Niveau.
Werkzeugauswahl
1, wählen Sie das Prinzip der CNC-Werkzeug
Die Werkzeugstandzeit ist eng mit der Schnittmenge verbunden. Bei der Einstellung der Schnittmenge sollte zuerst eine angemessene Standzeit gewählt werden und eine angemessene Standzeit entsprechend dem Optimierungsziel festgelegt werden. Es ist in der Regel in die höchste Produktivität Werkzeugstandzeit und die niedrigsten Kosten Standzeit unterteilt. Ersteres wird basierend auf dem Ziel mit der geringsten Menge an Arbeitszeit pro Einheit bestimmt und Letzteres wird basierend auf dem Ziel mit den niedrigsten Prozesskosten bestimmt.
Werkzeugstandzeit abhängig von der Komplexität des Werkzeugs, der Herstellung und den Kosten des Schärfens.
Die komplexe und hochpräzise Werkzeugstandzeit sollte höher gewählt werden als bei dem einschneidigen Werkzeug. Für die Werkzeugmaschine mit indexierbaren Werkzeugen kann aufgrund der kurzen Werkzeugwechselzeit, um ihrer Schneidleistung ein volles Spiel zu geben und die Produktionseffizienz zu verbessern, die Werkzeugstandzeit niedriger gewählt werden, im Allgemeinen 15-30 Minuten dauern.
Für Werkzeuge mit mehreren Messern, Werkzeugmaschinen und automatisierten Bearbeitungswerkzeugen, die für das Laden von Werkzeugen, den Werkzeugwechsel und die Werkzeugeinstellung komplexer sind. Die Werkzeugstandzeit sollte höher gewählt werden, insbesondere sollte die Werkzeugzuverlässigkeit gewährleistet sein.
Wenn die Produktivität eines bestimmten Prozesses in einer Werkstatt die Produktivität der gesamten Werkstatt einschränkt, wird die Standzeit des Prozesses niedriger gewählt. Wenn der Aufwand der gesamten Anlage, die von einer bestimmten Prozesseinheit-Einheitszeit geteilt wird, relativ groß ist, sollte die Werkzeugstandzeit auch niedriger gewählt werden.
Im Falle einer großflächigen Endbearbeitung sollte die Werkzeugstandzeit entsprechend der Teilegenauigkeit und Oberflächenrauhigkeit bestimmt werden, um sicherzustellen, dass mindestens ein Durchgang durchgeführt wird, um einen Werkzeugwechsel während des Schneidens zu vermeiden.
Verglichen mit dem normalen Werkzeugmaschinenbearbeitungsverfahren stellt die numerische Steuerungsverarbeitung höhere Anforderungen an das Werkzeug, erfordert nicht nur eine gute, hohe Präzision, sondern erfordert auch eine stabile Größe, hohe Haltbarkeit. Die Trennung und die Reihenleistung erfordern ebenfalls eine einfache Installation und Anpassung an die hohen Effizienzanforderungen von CNC-Werkzeugmaschinen. Die für CNC-Werkzeugmaschinen ausgewählten Werkzeuge werden häufig für Materialien für Hochgeschwindigkeits-Schneidwerkzeuge (wie Hochgeschwindigkeitsstahl, feinstkörniges Hartmetall) verwendet und verwenden Wendeschneidplatten.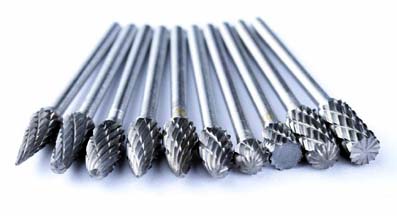
2, Wählen Sie das Werkzeug für CNC-Drehen
Cnc-Drehbank-Drehwerkzeug allgemein verwendete allgemeine Punkte: Formdrehwerkzeug, scharfes drehendes Werkzeug, Bogendrehwerkzeug und fünf Arten.
Formdrehwerkzeuge werden auch als Modelldrehwerkzeuge bezeichnet. Die Konturform der Bearbeitungsteile wird vollständig durch die Form und die Größe der Wendekante des drehenden Werkzeugs bestimmt. Beim CNC-Drehen umfassen allgemeine drehende Werkzeuge Bogenschneider mit kleinem Radius, nicht rechteckige Schlitzschneider und Fadenschneider. In CNC Bei der Bearbeitung sollte das Formwerkzeug möglichst wenig oder so wenig wie möglich verwendet werden.
Das scharfe Drehwerkzeug ist ein Drehwerkzeug, das durch eine gerade Schneide gekennzeichnet ist. Die Spitze eines solchen Drehwerkzeugs besteht aus geraden Haupt- und Nebenschneiden. Das interne und externe Drehwerkzeug 900, das linke und das rechte stirnseitige drehende, nutende (schneidende) Werkzeug und eine Vielzahl von kleinen angefasten Spitzen und die zylindrischen Lochwerkzeuge. Die Methode der Auswahl der geometrischen Parameter (hauptsächlich geometrische Winkel) des scharfen Drehens Werkzeug ist im Grunde das gleiche wie das gewöhnliche Drehen.
Jedoch sollten die Eigenschaften der CNC-Bearbeitung (wie Bearbeitungsrouten, Bearbeitungsinterferenzen usw.) umfassend berücksichtigt werden, und die Festigkeit der Werkzeugspitze selbst sollte berücksichtigt werden.
3, Wählen Sie das Werkzeug für CNC-Fräsen
Bei der Bearbeitung mit numerischer Steuerung werden die Innen- und Außenkonturen der Teile der Fräsebene und der Fräsebene üblicherweise als Flachfräser verwendet. Die empirischen Daten der relevanten Parameter des Tools sind wie folgt:
Einer besteht darin, dass der Schneiderradius RD kleiner als der minimale Krümmungsradius Rmin der inneren Konturoberfläche des Teils sein sollte, wobei im Allgemeinen RD = (0,8-0,9) Rmin genommen wird.
Die zweite ist die Bearbeitungshöhe des Teils H <(1 / 4-1 / 6) RD, um sicherzustellen, dass das Messer eine ausreichende Steifigkeit aufweist.
Drittens, wenn der Boden der inneren Nut mit einem Schaftfräser mit flachem Boden gefräst wird, muss die Unterkante der Nut mit zwei Durchgängen überlappt werden, und der Radius der Schneidkante des Werkzeugs Re = Rr, d Durchmesser ist d = 2Re = 2 (Rr), der Radius des Werkzeugs wird beim Programmieren als Re = 0,95 (Rr) angenommen.
Für einige dreidimensionale Oberflächen- und Winkelprofilbearbeitungen werden häufig Kugelfräser, Ringfräser, Trommelfräser, Kegelfräser und Scheibenfräser eingesetzt.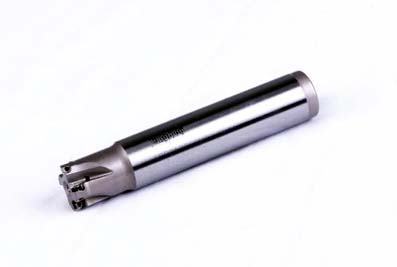
(1) Die Verarbeitung des obigen Arbeitsverfahrens kann die Positionierung und das Festklemmen des nächsten Arbeitsvorgangs nicht beeinflussen.
(2) Zuerst innen und außen, dh der innere Hohlraum (inneres Loch) wird zuerst bearbeitet und dann wird die äußere Form bearbeitet.
(3) Prozesse, die von demselben Werkzeug oder demselben Werkzeug bearbeitet werden, werden vorzugsweise kontinuierlich ausgeführt, um Fehler zu reduzieren, die durch Neupositionierung oder Werkzeugwechsel verursacht werden.
(4) In der gleichen Installation sollte zuerst der Prozess ausgeführt werden, der die Steifigkeit des Werkstücks nur wenig beeinflusst.
Verarbeitungsroute
Die Bearbeitungsroute der CNC-Drehmaschinenzuführung bedeutet, dass das Drehwerkzeug seine Bewegung vom Werkzeugeinstellpunkt (oder dem festen Ursprung der Werkzeugmaschine) beginnt, bis es an diesen Punkt zurückkehrt und das Bearbeitungsprogramm beendet wird, einschließlich Messern Einschneiden, Schneiden Out und ein nicht schneidender freier Weg.
Der Beschickungsweg für die Endbearbeitung wird grundsätzlich entlang der Umrisse seiner Teile ausgeführt, wobei das Hauptaugenmerk des Bestimmens des Beschickungsweges darin liegt, den Beschickungsweg für Schruppen und Leerweg zu bestimmen.
In der CNC-Drehmaschinenbearbeitung folgt die Bestimmung von Bearbeitungswegen im Allgemeinen den folgenden Prinzipien:
1. Die Genauigkeit und Oberflächenrauhigkeit des zu bearbeitenden Werkstücks sollte gewährleistet sein.
2. Minimiere die Verarbeitungsroute, reduziere die Leerlaufzeit und verbessere die Effizienz der Verarbeitung.
3. Vereinfachen Sie den Arbeitsaufwand der numerischen Berechnung so weit wie möglich und vereinfachen Sie die Verarbeitung.
4. Verwenden Sie Unterprogramme für einige wiederverwendbare Programme.
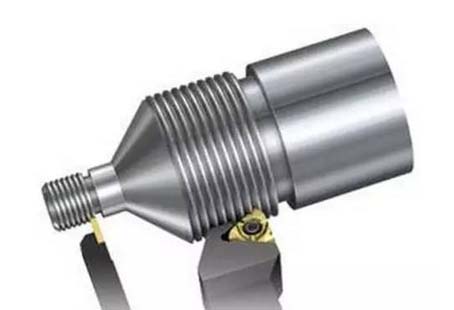
Indem das Bearbeitungsprogramm den kürzesten Vorschubweg hat, wird nicht nur die Ausführungszeit des gesamten Bearbeitungsprozesses eingespart, sondern auch der unnötige Werkzeugverbrauch und der Verschleiß gleitender Teile des Maschinenvorschubs reduziert. Der Typ der kürzesten Route und ihre Implementierung sind wie folgt:
(1) Die kürzeste Zustellroute. Der kürzeste Schneidvorschubweg kann die Produktionseffizienz effektiv erhöhen und den Werkzeugverschleiß reduzieren. Bei der Anordnung des kürzesten Schneidvorschubs muss auch die Steifigkeit und Bearbeitbarkeit des Werkstücks gewährleistet sein.
(2) Die kürzeste nicht schneidende Hubstrecke.
Mit Messerspitzen. Allgemein rechteckige Schleife beispielhaftes Aufrauen. Der Werkzeugpunkt A wird unter Berücksichtigung der Notwendigkeit eines zweckmäßigen Werkzeugwechsels während des Fertigbearbeitungsprozesses eingestellt und wird daher an einer Stelle weit entfernt von dem Rohling eingestellt. Gleichzeitig fällt der Startpunkt mit dem Werkzeugpunkt zusammen.
Richten Sie einen Werkzeugwechselpunkt geschickt ein. Um den Komfort und die Sicherheit des Werkzeugwechsels zu berücksichtigen, wird manchmal auch der Werkzeugwechselpunkt in einem Abstand von dem leeren Teil eingestellt.
An der Stelle wird dann, wenn das zweite Messer gewechselt wird, der Verlauf des nichtschneidenden Hubes während der Endbearbeitung länger sein; Wenn der Werkzeugwechselpunkt des zweiten Messers ebenfalls auf die mittlere Punktposition eingestellt ist, kann die nichtschneidende Hubstrecke verkürzt werden.
Ordnen Sie die "Null-Rückkehr" -Route vernünftig an. Beim manuellen Kompilieren komplexer Konturbearbeitungsprogramme wird der Berechnungsprozess zur einfachen Verifizierung vereinfacht. Der Programmierer legt manchmal den Endpunkt des Werkzeugs nach der Verarbeitung jedes Werkzeugs fest. Durch Ausführen einer "Zurück zu Null" -Betriebsanweisung werden alle von ihnen zu der Position der Werkzeugtrennstelle zurückgebracht, und dann wird das nachfolgende Programm ausgeführt. Dies erhöht die Entfernung der Fütterungsroute und verringert die Produktionseffizienz. Daher sollte der Abstand zwischen dem Endpunkt des vorhergehenden Messers und dem Startpunkt des nächsten Messers so kurz wie möglich sein, wenn die "Nullrückführ" -Route vernünftig angeordnet ist. Oder Null, um die kürzesten Anforderungen der Futterroute zu erfüllen. Zusätzlich wird bei der Rückkehr zum Befehl zum Schneiden des Schneidwerkzeugs der gleichzeitige Befehl "Rückkehr zu Null" der X-Achse und der Z-Achse so weit wie möglich ohne Interferenz verwendet, und der "Rücksprung" wird verwendet -to-zero "Route dieser Funktion ist die kürzeste.
(3) grober Rand raue Leiter, die Zufuhrlinie schneiden. Die Schneidvorschubrichtungen von zwei Arten von großen Rohlings sind aufgelistet. Es ist die falsche Schrittschneide, das Schneiden in der Reihenfolge von 1 Eimer 5, die restliche Menge von jedem Schnitt ist gleich, es ist der korrekte Schritt, der Zufuhrweg schneidet. Wegen des gleichen Rückens der Schneide.
(4) Kontinuierlicher Schneidvorschubweg für die Teilkonturbearbeitung. Die Endbearbeitung von Teilekonturen kann mit einer oder mehreren Messerendbearbeitungsoperationen durchgeführt werden. Das fertige Profil sollte vom letzten Messer aus kontinuierlich bearbeitet werden. Zu diesem Zeitpunkt sollte die Position des Werkzeugs richtig ausgewählt werden. Versuchen Sie nicht, Einschnitte anzuordnen und auszuschneiden, Werkzeuge zu wechseln und in kontinuierlichen Konturen zu pausieren. Um plötzliche Schnittkraftänderungen zu vermeiden und das Gleichgewicht der Prozesssysteme zu zerstören. Dies führt zu Kratzern, plötzlichen Formänderungen oder Stagnation der Teile auf der Kontur des Teils.
(5) Spezielle Futterrouten. Im CNC-Drehen, unter normalen Umständen. Der Längsvorschub des Werkzeugs wird entlang der negativen Richtung der Koordinaten durchgeführt. Es ist jedoch manchmal unangemessen, eine Fütterungsroute in ihrer üblichen negativen Richtung anzuordnen. Es kann sogar das Werkstück beschädigen.
Vorteile und Nachteile
Die CNC-Bearbeitung hat folgende Vorteile:
1. Die Anzahl der Kleider ist stark reduziert und Teile mit komplexen Formen benötigen keine komplizierten Kleider. Wenn Sie die Form und Größe von Teilen ändern möchten, müssen Sie nur das Teileverarbeitungsprogramm ändern, das für die Entwicklung und Änderung neuer Produkte geeignet ist.
2. Die Verarbeitungsqualität ist stabil, die Verarbeitungsgenauigkeit ist hoch und die Wiederholgenauigkeit ist hoch und sie kann die Verarbeitungsanforderungen des Flugzeugs erfüllen.
3. Die hohe Produktionseffizienz bei der Mehrsorten- und Kleinserienfertigung kann die Zeit für die Produktionsvorbereitung, die Werkzeugmaschineneinstellung und die Prozessinspektion verkürzen und die Schneidzeit durch den Einsatz der optimalen Schnittmenge reduzieren.
4. Bearbeitbare komplexe Oberflächen, die mit herkömmlichen Methoden schwer zu bearbeiten sind, können bearbeitet werden, und sogar bearbeitete Teile, die nicht beobachtbar sind, können bearbeitet werden. Der Nachteil der CNC-Bearbeitung besteht darin, dass Werkzeugmaschinenausrüstung teuer ist und das Wartungspersonal einen hohen Bedarf hat Niveau.
Werkzeugauswahl
1, wählen Sie das Prinzip der CNC-Werkzeug
Die Werkzeugstandzeit ist eng mit der Schnittmenge verbunden. Bei der Einstellung der Schnittmenge sollte zuerst eine angemessene Standzeit gewählt werden und eine angemessene Standzeit entsprechend dem Optimierungsziel festgelegt werden. Es ist in der Regel in die höchste Produktivität Werkzeugstandzeit und die niedrigsten Kosten Standzeit unterteilt. Ersteres wird basierend auf dem Ziel mit der geringsten Menge an Arbeitszeit pro Einheit bestimmt und Letzteres wird basierend auf dem Ziel mit den niedrigsten Prozesskosten bestimmt.
Werkzeugstandzeit abhängig von der Komplexität des Werkzeugs, der Herstellung und den Kosten des Schärfens.
Die komplexe und hochpräzise Werkzeugstandzeit sollte höher gewählt werden als bei dem einschneidigen Werkzeug. Für die Werkzeugmaschine mit indexierbaren Werkzeugen kann aufgrund der kurzen Werkzeugwechselzeit, um ihrer Schneidleistung ein volles Spiel zu geben und die Produktionseffizienz zu verbessern, die Werkzeugstandzeit niedriger gewählt werden, im Allgemeinen 15-30 Minuten dauern.
Für Werkzeuge mit mehreren Messern, Werkzeugmaschinen und automatisierten Bearbeitungswerkzeugen, die für das Laden von Werkzeugen, den Werkzeugwechsel und die Werkzeugeinstellung komplexer sind. Die Werkzeugstandzeit sollte höher gewählt werden, insbesondere sollte die Werkzeugzuverlässigkeit gewährleistet sein.
Wenn die Produktivität eines bestimmten Prozesses in einer Werkstatt die Produktivität der gesamten Werkstatt einschränkt, wird die Standzeit des Prozesses niedriger gewählt. Wenn der Aufwand der gesamten Anlage, die von einer bestimmten Prozesseinheit-Einheitszeit geteilt wird, relativ groß ist, sollte die Werkzeugstandzeit auch niedriger gewählt werden.
Im Falle einer großflächigen Endbearbeitung sollte die Werkzeugstandzeit entsprechend der Teilegenauigkeit und Oberflächenrauhigkeit bestimmt werden, um sicherzustellen, dass mindestens ein Durchgang durchgeführt wird, um einen Werkzeugwechsel während des Schneidens zu vermeiden.
Verglichen mit dem normalen Werkzeugmaschinenbearbeitungsverfahren stellt die numerische Steuerungsverarbeitung höhere Anforderungen an das Werkzeug, erfordert nicht nur eine gute, hohe Präzision, sondern erfordert auch eine stabile Größe, hohe Haltbarkeit. Die Trennung und die Reihenleistung erfordern ebenfalls eine einfache Installation und Anpassung an die hohen Effizienzanforderungen von CNC-Werkzeugmaschinen. Die für CNC-Werkzeugmaschinen ausgewählten Werkzeuge werden häufig für Materialien für Hochgeschwindigkeits-Schneidwerkzeuge (wie Hochgeschwindigkeitsstahl, feinstkörniges Hartmetall) verwendet und verwenden Wendeschneidplatten.
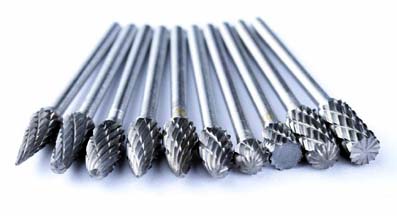
2, Wählen Sie das Werkzeug für CNC-Drehen
Cnc-Drehbank-Drehwerkzeug allgemein verwendete allgemeine Punkte: Formdrehwerkzeug, scharfes drehendes Werkzeug, Bogendrehwerkzeug und fünf Arten.
Formdrehwerkzeuge werden auch als Modelldrehwerkzeuge bezeichnet. Die Konturform der Bearbeitungsteile wird vollständig durch die Form und die Größe der Wendekante des drehenden Werkzeugs bestimmt. Beim CNC-Drehen umfassen allgemeine drehende Werkzeuge Bogenschneider mit kleinem Radius, nicht rechteckige Schlitzschneider und Fadenschneider. In CNC Bei der Bearbeitung sollte das Formwerkzeug möglichst wenig oder so wenig wie möglich verwendet werden.
Das scharfe Drehwerkzeug ist ein Drehwerkzeug, das durch eine gerade Schneide gekennzeichnet ist. Die Spitze eines solchen Drehwerkzeugs besteht aus geraden Haupt- und Nebenschneiden. Das interne und externe Drehwerkzeug 900, das linke und das rechte stirnseitige drehende, nutende (schneidende) Werkzeug und eine Vielzahl von kleinen angefasten Spitzen und die zylindrischen Lochwerkzeuge. Die Methode der Auswahl der geometrischen Parameter (hauptsächlich geometrische Winkel) des scharfen Drehens Werkzeug ist im Grunde das gleiche wie das gewöhnliche Drehen.
Jedoch sollten die Eigenschaften der CNC-Bearbeitung (wie Bearbeitungsrouten, Bearbeitungsinterferenzen usw.) umfassend berücksichtigt werden, und die Festigkeit der Werkzeugspitze selbst sollte berücksichtigt werden.
3, Wählen Sie das Werkzeug für CNC-Fräsen
Bei der Bearbeitung mit numerischer Steuerung werden die Innen- und Außenkonturen der Teile der Fräsebene und der Fräsebene üblicherweise als Flachfräser verwendet. Die empirischen Daten der relevanten Parameter des Tools sind wie folgt:
Einer besteht darin, dass der Schneiderradius RD kleiner als der minimale Krümmungsradius Rmin der inneren Konturoberfläche des Teils sein sollte, wobei im Allgemeinen RD = (0,8-0,9) Rmin genommen wird.
Die zweite ist die Bearbeitungshöhe des Teils H <(1 / 4-1 / 6) RD, um sicherzustellen, dass das Messer eine ausreichende Steifigkeit aufweist.
Drittens, wenn der Boden der inneren Nut mit einem Schaftfräser mit flachem Boden gefräst wird, muss die Unterkante der Nut mit zwei Durchgängen überlappt werden, und der Radius der Schneidkante des Werkzeugs Re = Rr, d Durchmesser ist d = 2Re = 2 (Rr), der Radius des Werkzeugs wird beim Programmieren als Re = 0,95 (Rr) angenommen.
Für einige dreidimensionale Oberflächen- und Winkelprofilbearbeitungen werden häufig Kugelfräser, Ringfräser, Trommelfräser, Kegelfräser und Scheibenfräser eingesetzt.
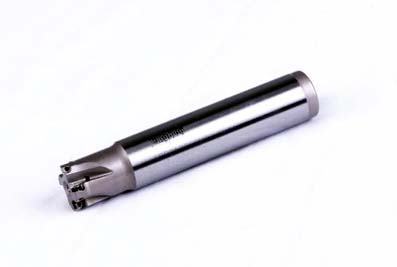
Die meisten CNC-Werkzeugmaschinen verwenden serialisierte und standardisierte Werkzeuge, und die nationalen Standard- und Serienmodelle sind für die Werkzeughalter und Schneidköpfe der indexierbaren Werkzeugmaschinen wie das externe Drehwerkzeug und das Planfräswerkzeug verfügbar. Für Bearbeitungszentren und Werkzeugmaschinen Mit automatischem Werkzeugwechsler wurden die Werkzeughalter serialisiert und standardisiert. Zum Beispiel ist der Standardcode für das Kegelschaftwerkzeugsystem TSG-JT und der Standardcode für das Werkzeugwerkzeug mit Zylinderschaft ist DSG-JZ.
Außerdem muss für das ausgewählte Werkzeug die Werkzeuggröße genau gemessen werden, um vor der Verwendung genaue Daten zu erhalten. Der Bediener gibt diese Daten in das Datensystem ein und beendet den Bearbeitungsprozess durch Aufruf des Programms, wodurch ein qualifiziertes Werkstück erzeugt wird.
Messerspitze
Von wo hat das Werkzeug begonnen, sich an die angegebene Position zu bewegen?
Daher muss zu Beginn der Programmausführung die Position des Werkzeugs im Werkstückkoordinatensystem bestimmt werden. Diese Position ist der Startpunkt des Werkzeugs relativ zum Werkstück während der Programmausführung. So heißt es der Ausgangspunkt des Programms oder die Spitze des Messers.
Dieser Startpunkt wird in der Regel vom Messer bestimmt, daher wird dieser Punkt auch Messerpunkt genannt. Bei der Programmierung muss die Position des Werkzeugpunktes korrekt gewählt werden. Das Prinzip der Werkzeugpunkteeinstellung soll die numerische Bearbeitung erleichtern und die Programmierung vereinfachen. Einfach zu korrigieren und leicht während der Verarbeitung zu überprüfen; was zu kleinen Bearbeitungsfehlern führt. Die Werkzeugschneide kann am bearbeiteten Teil oder an der Vorrichtung oder der Werkzeugmaschine eingestellt werden. Um die Bearbeitungsgenauigkeit des Werkstücks zu verbessern, sollte der Werkzeugschnittpunkt auf der Konstruktionsbasis des Werkstücks oder der Prozessbasis so weit wie möglich festgelegt werden.
Wenn die Werkzeugmaschine tatsächlich betrieben wird, kann die Messerposition des Werkzeugs auf den Werkzeugeinstellpunkt gesetzt werden, indem das Werkzeug manuell eingestellt wird. Das heißt, die "Messerposition" und der "Schneidpunkt" fallen zusammen.
Die so genannte "Messerposition" bezieht sich auf den Positionierungsreferenzpunkt des Werkzeugs. Die Werkzeugposition des Drehwerkzeugs ist die Werkzeugnase oder die Werkzeugnase.
Der Planfräser ist der Schnittpunkt der Werkzeugachse und der Werkzeuggrundfläche; Der Kugelfräser ist die Kugelmitte des Kugelkopfs und der Bohrer ist der Bohrpunkt.
Bei manueller Messerbedienung ist die Genauigkeit des Werkzeugs gering und der Wirkungsgrad niedrig. Einige Fabriken verwenden ein optisches Ausrichtwerkzeug, einen Werkzeugausrichter und ein automatisches Werkzeugeinstellgerät, um die Werkzeugsetzzeit zu reduzieren und die Genauigkeit der Werkzeugeinstellung zu erhöhen.
Wenn während der Bearbeitung ein Werkzeugwechsel erforderlich ist, sollte der Werkzeugwechselpunkt angegeben werden. Der so genannte "Werkzeugwechselpunkt" bezieht sich auf die Werkzeugwechselposition, wenn der Halter gedreht wird, der Werkzeugwechsel sollte sich außerhalb des Werkstücks oder der Vorrichtung befinden, das Werkstück nicht berühren und der andere Werkzeugwechsel soll Vorrang haben.
Schnittmenge
Bei der NC-Programmierung muss der Programmierer die Schnittmenge für jeden Prozess bestimmen und das Programm in Form von Anweisungen schreiben. Die Schnittgeschwindigkeiten umfassen die Spindeldrehzahl, die Schnitttiefe und die Vorschubgeschwindigkeit. Für unterschiedliche Bearbeitungsmethoden müssen unterschiedliche Schnittmengen gewählt werden. Das Auswahlprinzip der Schnittmenge besteht darin, die Präzision und Oberflächenrauhigkeit des Teils sicherzustellen und die Schneidleistung des Werkzeugs voll auszunutzen. Gewährleisten Sie eine angemessene Standzeit und geben Sie der Leistung der Maschine das volle Spiel, maximieren Sie die Produktivität und senken Sie die Kosten.
1, Bestimmen Sie die Spindeldrehzahl
Die Spindeldrehzahl sollte basierend auf der zulässigen Schnittgeschwindigkeit und dem Durchmesser des Werkstücks (oder des Werkzeugs) ausgewählt werden. Seine Berechnungsformel lautet: n = 1000 v / 7 1D Typ: v? Schnittgeschwindigkeit, Einheit bewegt sich m / m, abhängig von der Haltbarkeit des Werkzeugs; n Eine Spindeldrehzahl in U / min, D ist der Werkstückdurchmesser oder Werkzeugdurchmesser in mm. Berechnen Sie die Spindeldrehzahl, n, und wählen Sie schließlich die eigene oder die nächste Geschwindigkeit der Maschine.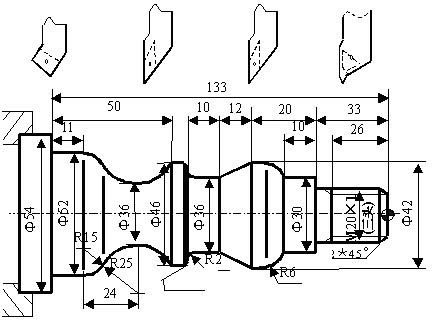
2, Bestimmen Sie die Vorschubgeschwindigkeit
Die Vorschubgeschwindigkeit ist ein wichtiger Parameter für die Schnittmenge von CNC-Werkzeugmaschinen. Sie wird hauptsächlich aufgrund der Anforderungen an die Bearbeitungsgenauigkeit und Oberflächenrauhigkeit der Teile und der Materialeigenschaften der Werkzeuge und Werkstücke ausgewählt. Die maximale Vorschubgeschwindigkeit ist durch die Steifigkeit der Maschine und die Leistung des Vorschubsystems begrenzt.
Das Prinzip zur Bestimmung der Vorschubgeschwindigkeit: Wenn die Qualitätsanforderungen des Werkstücks garantiert werden können, kann zur Steigerung der Produktionseffizienz eine höhere Vorschubgeschwindigkeit gewählt werden. Im Allgemeinen im Bereich von 100 bis 200 mm / min;
Beim Schneiden, Bearbeiten von tiefen Löchern oder Bearbeiten mit Hochgeschwindigkeits-Stahlwerkzeugen sollten niedrigere Vorschubraten gewählt werden, im Allgemeinen im Bereich von 20 bis 50 mm / min;
Wenn die Anforderungen an die Bearbeitungsgenauigkeit und die Oberflächenrauheit hoch sind, sollte die Vorschubgeschwindigkeit kleiner gewählt werden, im allgemeinen im Bereich von 20 bis 50 mm / min;
Wenn das Werkzeug im Leerlauf ist, insbesondere wenn es aus großer Entfernung "auf Null zurückkehrt", kann die höchste Vorschubgeschwindigkeit eingestellt werden, die vom numerischen Kontrollsystem der Maschine eingestellt wurde.
3, Bestimmen Sie die Tiefe des Schnittes
Die Schnitttiefe wird durch die Steifigkeit der Maschine, des Werkstücks und des Werkzeugs bestimmt. Wenn die Steifigkeit es zulässt, sollte die Schnitttiefe der Bearbeitungszugabe des Werkstücks so weit wie möglich entsprechen, was die Anzahl der Durchgänge verringern und die Produktionseffizienz erhöhen kann. Um die Qualität der bearbeiteten Oberfläche sicherzustellen, kann eine geringe Menge an Endbearbeitungszugabe übrig bleiben, im allgemeinen 0,2 bis 0,5 mm. Kurz gesagt, der spezifische Wert der Schnittmenge sollte auf der Grundlage der Leistungsfähigkeit der Werkzeugmaschine, der zugehörigen Handbücher und der praktischen Erfahrung analog ermittelt werden.
Gleichzeitig können Spindelgeschwindigkeit, Schnitttiefe und Vorschubgeschwindigkeit aufeinander abgestimmt werden, um die optimale Schnittmenge zu erhalten.
Die Schnittmenge ist nicht nur ein wichtiger Parameter, der bestimmt werden muss, bevor die Werkzeugmaschine eingestellt wird, sondern auch, ob der Wert vernünftig ist oder nicht, hat einen sehr wichtigen Einfluss auf die Bearbeitungsqualität, die Bearbeitungseffizienz und die Produktionskosten.
Der so genannte "vernünftige" Schnittbetrag bezieht sich auf die volle Nutzung der Werkzeugschneidleistung und Maschinenleistungsleistung (Leistung, Drehmoment) unter der Prämisse, die Qualität sicherzustellen, um eine hohe Produktivität und niedrige Verarbeitungskosten der Schnittmenge zu erhalten.
Außerdem muss für das ausgewählte Werkzeug die Werkzeuggröße genau gemessen werden, um vor der Verwendung genaue Daten zu erhalten. Der Bediener gibt diese Daten in das Datensystem ein und beendet den Bearbeitungsprozess durch Aufruf des Programms, wodurch ein qualifiziertes Werkstück erzeugt wird.
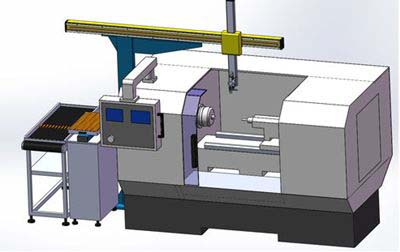
Messerspitze
Von wo hat das Werkzeug begonnen, sich an die angegebene Position zu bewegen?
Daher muss zu Beginn der Programmausführung die Position des Werkzeugs im Werkstückkoordinatensystem bestimmt werden. Diese Position ist der Startpunkt des Werkzeugs relativ zum Werkstück während der Programmausführung. So heißt es der Ausgangspunkt des Programms oder die Spitze des Messers.
Dieser Startpunkt wird in der Regel vom Messer bestimmt, daher wird dieser Punkt auch Messerpunkt genannt. Bei der Programmierung muss die Position des Werkzeugpunktes korrekt gewählt werden. Das Prinzip der Werkzeugpunkteeinstellung soll die numerische Bearbeitung erleichtern und die Programmierung vereinfachen. Einfach zu korrigieren und leicht während der Verarbeitung zu überprüfen; was zu kleinen Bearbeitungsfehlern führt. Die Werkzeugschneide kann am bearbeiteten Teil oder an der Vorrichtung oder der Werkzeugmaschine eingestellt werden. Um die Bearbeitungsgenauigkeit des Werkstücks zu verbessern, sollte der Werkzeugschnittpunkt auf der Konstruktionsbasis des Werkstücks oder der Prozessbasis so weit wie möglich festgelegt werden.
Wenn die Werkzeugmaschine tatsächlich betrieben wird, kann die Messerposition des Werkzeugs auf den Werkzeugeinstellpunkt gesetzt werden, indem das Werkzeug manuell eingestellt wird. Das heißt, die "Messerposition" und der "Schneidpunkt" fallen zusammen.
Die so genannte "Messerposition" bezieht sich auf den Positionierungsreferenzpunkt des Werkzeugs. Die Werkzeugposition des Drehwerkzeugs ist die Werkzeugnase oder die Werkzeugnase.
Der Planfräser ist der Schnittpunkt der Werkzeugachse und der Werkzeuggrundfläche; Der Kugelfräser ist die Kugelmitte des Kugelkopfs und der Bohrer ist der Bohrpunkt.
Bei manueller Messerbedienung ist die Genauigkeit des Werkzeugs gering und der Wirkungsgrad niedrig. Einige Fabriken verwenden ein optisches Ausrichtwerkzeug, einen Werkzeugausrichter und ein automatisches Werkzeugeinstellgerät, um die Werkzeugsetzzeit zu reduzieren und die Genauigkeit der Werkzeugeinstellung zu erhöhen.
Wenn während der Bearbeitung ein Werkzeugwechsel erforderlich ist, sollte der Werkzeugwechselpunkt angegeben werden. Der so genannte "Werkzeugwechselpunkt" bezieht sich auf die Werkzeugwechselposition, wenn der Halter gedreht wird, der Werkzeugwechsel sollte sich außerhalb des Werkstücks oder der Vorrichtung befinden, das Werkstück nicht berühren und der andere Werkzeugwechsel soll Vorrang haben.
Schnittmenge
Bei der NC-Programmierung muss der Programmierer die Schnittmenge für jeden Prozess bestimmen und das Programm in Form von Anweisungen schreiben. Die Schnittgeschwindigkeiten umfassen die Spindeldrehzahl, die Schnitttiefe und die Vorschubgeschwindigkeit. Für unterschiedliche Bearbeitungsmethoden müssen unterschiedliche Schnittmengen gewählt werden. Das Auswahlprinzip der Schnittmenge besteht darin, die Präzision und Oberflächenrauhigkeit des Teils sicherzustellen und die Schneidleistung des Werkzeugs voll auszunutzen. Gewährleisten Sie eine angemessene Standzeit und geben Sie der Leistung der Maschine das volle Spiel, maximieren Sie die Produktivität und senken Sie die Kosten.
1, Bestimmen Sie die Spindeldrehzahl
Die Spindeldrehzahl sollte basierend auf der zulässigen Schnittgeschwindigkeit und dem Durchmesser des Werkstücks (oder des Werkzeugs) ausgewählt werden. Seine Berechnungsformel lautet: n = 1000 v / 7 1D Typ: v? Schnittgeschwindigkeit, Einheit bewegt sich m / m, abhängig von der Haltbarkeit des Werkzeugs; n Eine Spindeldrehzahl in U / min, D ist der Werkstückdurchmesser oder Werkzeugdurchmesser in mm. Berechnen Sie die Spindeldrehzahl, n, und wählen Sie schließlich die eigene oder die nächste Geschwindigkeit der Maschine.
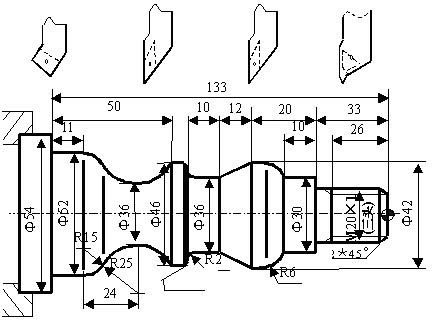
2, Bestimmen Sie die Vorschubgeschwindigkeit
Die Vorschubgeschwindigkeit ist ein wichtiger Parameter für die Schnittmenge von CNC-Werkzeugmaschinen. Sie wird hauptsächlich aufgrund der Anforderungen an die Bearbeitungsgenauigkeit und Oberflächenrauhigkeit der Teile und der Materialeigenschaften der Werkzeuge und Werkstücke ausgewählt. Die maximale Vorschubgeschwindigkeit ist durch die Steifigkeit der Maschine und die Leistung des Vorschubsystems begrenzt.
Das Prinzip zur Bestimmung der Vorschubgeschwindigkeit: Wenn die Qualitätsanforderungen des Werkstücks garantiert werden können, kann zur Steigerung der Produktionseffizienz eine höhere Vorschubgeschwindigkeit gewählt werden. Im Allgemeinen im Bereich von 100 bis 200 mm / min;
Beim Schneiden, Bearbeiten von tiefen Löchern oder Bearbeiten mit Hochgeschwindigkeits-Stahlwerkzeugen sollten niedrigere Vorschubraten gewählt werden, im Allgemeinen im Bereich von 20 bis 50 mm / min;
Wenn die Anforderungen an die Bearbeitungsgenauigkeit und die Oberflächenrauheit hoch sind, sollte die Vorschubgeschwindigkeit kleiner gewählt werden, im allgemeinen im Bereich von 20 bis 50 mm / min;
Wenn das Werkzeug im Leerlauf ist, insbesondere wenn es aus großer Entfernung "auf Null zurückkehrt", kann die höchste Vorschubgeschwindigkeit eingestellt werden, die vom numerischen Kontrollsystem der Maschine eingestellt wurde.
3, Bestimmen Sie die Tiefe des Schnittes
Die Schnitttiefe wird durch die Steifigkeit der Maschine, des Werkstücks und des Werkzeugs bestimmt. Wenn die Steifigkeit es zulässt, sollte die Schnitttiefe der Bearbeitungszugabe des Werkstücks so weit wie möglich entsprechen, was die Anzahl der Durchgänge verringern und die Produktionseffizienz erhöhen kann. Um die Qualität der bearbeiteten Oberfläche sicherzustellen, kann eine geringe Menge an Endbearbeitungszugabe übrig bleiben, im allgemeinen 0,2 bis 0,5 mm. Kurz gesagt, der spezifische Wert der Schnittmenge sollte auf der Grundlage der Leistungsfähigkeit der Werkzeugmaschine, der zugehörigen Handbücher und der praktischen Erfahrung analog ermittelt werden.
Gleichzeitig können Spindelgeschwindigkeit, Schnitttiefe und Vorschubgeschwindigkeit aufeinander abgestimmt werden, um die optimale Schnittmenge zu erhalten.
Die Schnittmenge ist nicht nur ein wichtiger Parameter, der bestimmt werden muss, bevor die Werkzeugmaschine eingestellt wird, sondern auch, ob der Wert vernünftig ist oder nicht, hat einen sehr wichtigen Einfluss auf die Bearbeitungsqualität, die Bearbeitungseffizienz und die Produktionskosten.
Der so genannte "vernünftige" Schnittbetrag bezieht sich auf die volle Nutzung der Werkzeugschneidleistung und Maschinenleistungsleistung (Leistung, Drehmoment) unter der Prämisse, die Qualität sicherzustellen, um eine hohe Produktivität und niedrige Verarbeitungskosten der Schnittmenge zu erhalten.