Blechverarbeitungs prozess
Mit der Entwicklung der heutigen Gesellschaft wird sich auch die Blechindustrie schnell entwickeln. Heute umfasst Blech alle Bereiche des Lebens. Für jedes Blechteil hat es einen bestimmten Bearbeitungsprozess. Der sogenannte Prozessablauf, um den Blechbearbeitungsprozess zu verstehen, müssen wir zuerst die Wahl der Blechwerkstoffe kennen.
Auswahl der Materialien
Die üblicherweise verwendeten Materialien für Bleche sind kaltgewalzte Bleche (SPCC), warmgewalzte Bleche (SHCC), verzinkte Bleche (SECC, SGCC), Kupfer (CU) -Messing, Beryllium-Kupfer, Aluminiumbleche (6061, 6063, Hartaluminium) usw.), Aluminiumprofile, Edelstahl (Spiegel, gebürstete Oberfläche, matte Oberfläche), abhängig von der Rolle des Produkts, die Wahl der Materialien ist unterschiedlich, in der Regel müssen die Verwendung des Produkts und die Kosten zu berücksichtigen.
1. Kaltgewalztes Platte SPCC: hauptsächlich für Galvanisieren und Backen von Farbe Teile, geringe Kosten, einfache Formung, Material Dicke ≤ 3,2 mm.
2. Warmgewalzte Platte SHCC: Material T ≥ 3,0 mm, auch für die Galvanisierung, Lackteile, kostengünstig, aber schwer zu formen, hauptsächlich flache Teile verwendet.
3. Galvanisiertes Blatt SECC, SGCC: SECC elektrolytische Platte trennte N-Material, P-Material, N-Material ist nicht hauptsächlich für Oberflächenbehandlung, hohe Kosten, P-Material für das Sprühen von Teilen.
4. Kupfer: Die Hauptverwendung von leitfähigen Materialien, die Oberflächenbehandlung ist Nickel, Chrom oder keine Behandlung, hohe Kosten.
5. Aluminiumplatte: im Allgemeinen für Oberflächenchromat (J11-A), Oxidation (leitfähige Oxidation, chemische Oxidation), hohe Kosten, Silberbeschichtung, Vernickelung.
6. Aluminiumprofil: Das Material mit komplexer Querschnittstruktur ist in einer Vielzahl von Baugruppenträgern am meisten benutzt. Oberflächenbehandlung mit Aluminiumplatte.
7. Edelstahl: Hauptsächlich ohne Oberflächenbehandlung, hohe Kosten verwendet.
Zeichnungsüberprüfung
Um den technologischen Prozess des Teils zu schreiben, müssen wir zunächst die verschiedenen technischen Anforderungen der Teilezeichnung kennen; Die Zeichnungsprüfung ist der wichtigste Teil des Prozessablaufs der Teile.
1. Überprüfen Sie, ob die Zeichnungen vollständig sind.
2. Die Ansichtsbeziehung der Zeichnungen, ob die Beschriftungen klar und vollständig sind und die Maßeinheiten sind markiert.
3. Assembly Beziehung, Montage Anforderungen Fokus Größe.
4. Der Unterschied zwischen neuen und alten Zeichnungen.
5. Übersetzung von Fremdsprachen.
6. Diagrammcode-Konvertierung
7. Zeichnungsprobleme und Feedback.
8. Material
9. Qualitätsanforderungen und Prozessanforderungen
10. Die offiziellen Freigabezeichnungen, werden mit Qualitätskontrollkapitel gestempelt.
Erweitern Sie Notizen
Erweiterte Zeichnung ist ein Plan (2D), der sich entsprechend der Teilezeichnung (3D) erweitert
1. Erweitern Sie den praktischen Weg, um Material und Bearbeitbarkeit zu sparen
2. Wählen Sie angemessen Lücken und Ränder, T = 2,0 oder weniger Abstand 0,2, T = 2-3 Abstand 0,5, Kantenumwicklung mit kurzer Kante (Doorboard)
3. Betrachten Sie die Toleranzdimensionen vernünftig: Negative Differenz, um am Ende zu gehen, positive Differenz, um die Hälfte zu gehen; Lochgröße: positive Differenz geht bis zum Ende, negative Differenz nimmt die Hälfte.
4. Burr-Richtung
5. Extrudieren, Drucknieten, Stanzpunkte (Taschen) und andere Position Richtungen, zeichnen Sie eine Schnittansicht
6. Überprüfen Sie Material, Plattendicke, Dickentoleranz
7. Sonderwinkel, Innenradius des Biegewinkels (normalerweise R = 0,5)
8. Wenn fehleranfällige (ähnliche Asymmetrie) sollte auf die Aufforderung konzentrieren
9. Platz zum Hinzufügen einer vergrößerten Ansicht in größerer Größe
10. Notwendigkeit, Schutzplatz zu sein, um Logo zu sein
Blechbearbeitungsprozess
Je nach dem Unterschied in der Struktur der Blechteile kann der Prozessablauf unterschiedlich sein, aber die Summe überschreitet nicht die folgenden Punkte.
1, Blanking: Blanking Weg gibt es verschiedene, hauptsächlich auf folgende Weise
1> Scheren: Scheren werden verwendet, um Streifen aus einfachen Materialien zu schneiden. Es wird hauptsächlich für die Formgebung und Bearbeitung von Rohlings verwendet. Die Kosten sind niedrig und die Genauigkeit ist weniger als 0,2. Es können jedoch nur Rohlinge oder Blöcke ohne Löcher oder Ecken bearbeitet werden.
2> Punch: Es ist die Verwendung von Punch, um die flachen Teile der Teile zu teilen, nachdem sie auf der Platte entfaltet wurden, um alle Arten von Formen zu bilden. Die Vorteile sind kurze Arbeitszeiten, hohe Effizienz, hohe Präzision, geringe Kosten und für die Massenproduktion geeignet. Notwendigkeit, die Form zu entwerfen.
3> NC-Ausblendung, NC-Ausblendung zuerst, um das NC-Programm zu schreiben, mit Programmiersoftware, Die entwickelte Zeichnung wird als ein erkennbares Programm von der NC-Nummer Zeichenmaschine geschrieben. Gemäß diesen Programmen kann es verwendet werden, um flache Komponenten verschiedener Formen einzeln auf die flache Platte zu stanzen, aber seine Struktur wird durch die Struktur der Schneidvorrichtung beeinflusst. Die Kosten sind niedrig und die Genauigkeit beträgt 0,15.
4. Laser Blanking: Es nutzt ein Laser-Schneidverfahren, um die Form seiner flachen Platte auf einer großen flachen Platte zu schneiden. Sie müssen ein Laserprogramm wie NCblanking schreiben. Es kann eine Vielzahl von komplexen Formen von flachen Teilen, hohe Kosten, Genauigkeit von 0,1 sein.
5> Säge: Hauptsächlich unter dem Aluminium, Vierkantrohr, Rohr, Rundstab und dergleichen, kostengünstig, geringe Präzision.
2. Monteur: Senkbohrung, Gewindebohren, Reiben, Bohren
Der Senkwinkel beträgt im Allgemeinen 120 ° C für das Nieten, 90 ° für die Senkschrauben und das Gewinde für die unteren Bohrungen.
3. Bördeln: Auch als Ziehloch, Bördeln bezeichnet, wird ein größeres Loch in ein kleineres Basisloch gezeichnet und dann geklopft. Verwenden Sie hauptsächlich Bleche mit relativ dünner Plattendicke, um die Festigkeit und die Anzahl der Gewindegänge zu erhöhen, um ein Verrutschen zu vermeiden. Im Allgemeinen für relativ dünne Plattendicke verwendet, seine normale flache Loch Bördelung, die Dicke ändert sich nicht, Dicke von 30-40% ist erlaubt, Höhe 40-60% höher als normale Flanschhöhe zu erhalten. Mit einem Druck von 50% kann die maximale Flanschhöhe erreicht werden. Wenn die Plattendicke groß ist, wie 2,0, 2,5 usw., kann die Plattendicke direkt abgegriffen werden.
4. stanzen: Ist die Verwendung von Formenbau Prozess, die allgemeine Stanzbearbeitung Stanzen, Schneiden Winkel, Ausstanzen, Schlaghöcker (Beulen), Stanzen reißen, zeichnen Löcher, Formen und andere Verarbeitungsmethoden. Die Verarbeitung muss eine entsprechende Form haben, um den Vorgang zu vervollständigen, wie beispielsweise Stanzen des Stanzwerkzeugs, des konvexen Beutelwerkzeugs, des Reißwerkzeugs, des Sauglochwerkzeugs, des Formwerkzeugs usw. Der Betrieb berücksichtigt hauptsächlich die Position und Richtung.
5. Drucknieten: Es gibt Drucknietmuttern, Schrauben, lose, etc. durch die hydraulische Drucknietmaschine oder den Stempel, um den Vorgang zu vervollständigen, es an den Blechteilen zu vernieten, achten Sie auf Direktionalität.
6. Biegen: Beim Biegen wird ein 2D-Teil zu einem 3D-Teil gefaltet. Die Bearbeitung erfordert ein Faltbett und einen entsprechenden Biegestempel und hat auch eine bestimmte Biegefolge. Das Prinzip ist die erste Falte, die das nächste Messer nicht stört.
Die Anzahl der Biegungen wird berechnet, indem die Rillenbreite mit dem Sechsfachen der Dicke von T = 3,0 mm oder weniger berechnet wird. Wie: T = 1,0, V = 6,0 F = 1,8, T = 1,2, V = 8, F = 2,2, T = 1,5, V = 10, F = 2,7, T = 2,0, V = 12, F = 4.0
Folding Bett Schimmel Klassifizierung, gerade Messer, Machete (80 ° C, 30 ° C)
Wenn die Aluminiumplatte gebogen wird, gibt es einen Riss, der die Breite der unteren Formnut vergrößern kann, um die obere Form R zu erhöhen (Glühen kann Risse vermeiden).
Beachten Sie beim Biegen: Ich plane Oberfläche, benötige Plattendicke, Menge; II Biegerichtung
Biegewinkel; IV Biegegröße; VI Aussehen, galvanisch verchromte Teile dürfen nicht geknickt werden.
Der Zusammenhang zwischen Biege- und Nietvorgang: Unter normalen Umständen zuerst vernieten, dann biegen. Wenn das Material jedoch nach dem Nieten gepresst wird, muss es gefaltet und dann gepresst werden. In einigen Fällen sind Biegen, Nieten und Nachbiegen erforderlich.
6. Schweißen: Auch als Spleißen bezeichnet, ist ein Herstellungsverfahren und eine Technik zum Verbinden von Metallen oder anderen thermoplastischen Materialien, wie Kunststoffen, durch Erhitzen, hohe Temperatur oder hohen Druck.
1> Klassifizierung: ein Schmelzschweißen: Argon Lichtbogenschweißen, CO2-Schweißen, Gasschweißen, Handschweißen
b. Druckschweißen: Punktschweißen, Stumpfschweißen, Stoßschweißen
c. Löten: elektrochromes Schweißen, Kupferdraht
2> schweißmethoden: ein CO2 gas abgeschirmt schweißen
b. Argon-Lichtbogenschweißen
c. Punktschweißen
d. Roboterschweißen
Die Wahl des Schweißverfahrens basiert auf den tatsächlichen Anforderungen und Materialien. Im Allgemeinen wird das CO2-Gasabschirmschweißen für Eisenblech-Schweißbohrungen verwendet; Argon-Lichtbogenschweißen für Edelstahl, Aluminiumschweißen. Roboterschweißen spart Arbeitsstunden, verbessert die Arbeitseffizienz und Schweißqualität und reduziert die Arbeitsintensität.
3> schweißsymbole: Δ kehlnaht, Ä, ich schweißen, V schweißen, einseitige V schweißen (V) mit stumpfen V schweiß (V), punktschweißen (O), steckerschweißen oder schlitzschweißung (Π), Crimp (χ) , Einseitige V-Schweißung mit stumpfen Kanten (V), U-förmige Schweißung mit stumpfen, J-förmigen Schweißen mit stumpfen, Back-End-Schweißen, Fracturing
4> Pfeillinien und Anschlüsse
5> Fehlende Schweißnähte und deren Vermeidung
Punktschweißen: Unzureichende Festigkeit kann Stöße treffen, Schweißbereich aufstellen
CO2-Schweißen: hohe Produktivität, geringer Energieverbrauch, geringe Kosten, starke Rostbeständigkeit
Argon Lichtbogenschweißen: geringe Auflösungstiefe, langsame Schweißgeschwindigkeit, geringe Effizienz, hohe Produktionskosten, Wolfram-Clip-Defekte, aber mit guter Schweißqualität, können NE-Metalle, wie Aluminium, Kupfer, Magnesium und so weiter geschweißt werden.
6> Schweißverformung verursacht: unzureichende Vorbereitung vor dem Schweißen, muss die Befestigung erhöhen
Schweißvorrichtung schlechter Verbesserungsprozess
Schlechte Schweißsequenz
7> Schweißverformungseffekt Positive Methode: Flammeneffektmethode
Vibrationsmethode
Hämmern
Künstliches Altern
Auswahl der Materialien
Die üblicherweise verwendeten Materialien für Bleche sind kaltgewalzte Bleche (SPCC), warmgewalzte Bleche (SHCC), verzinkte Bleche (SECC, SGCC), Kupfer (CU) -Messing, Beryllium-Kupfer, Aluminiumbleche (6061, 6063, Hartaluminium) usw.), Aluminiumprofile, Edelstahl (Spiegel, gebürstete Oberfläche, matte Oberfläche), abhängig von der Rolle des Produkts, die Wahl der Materialien ist unterschiedlich, in der Regel müssen die Verwendung des Produkts und die Kosten zu berücksichtigen.
1. Kaltgewalztes Platte SPCC: hauptsächlich für Galvanisieren und Backen von Farbe Teile, geringe Kosten, einfache Formung, Material Dicke ≤ 3,2 mm.
2. Warmgewalzte Platte SHCC: Material T ≥ 3,0 mm, auch für die Galvanisierung, Lackteile, kostengünstig, aber schwer zu formen, hauptsächlich flache Teile verwendet.
3. Galvanisiertes Blatt SECC, SGCC: SECC elektrolytische Platte trennte N-Material, P-Material, N-Material ist nicht hauptsächlich für Oberflächenbehandlung, hohe Kosten, P-Material für das Sprühen von Teilen.
4. Kupfer: Die Hauptverwendung von leitfähigen Materialien, die Oberflächenbehandlung ist Nickel, Chrom oder keine Behandlung, hohe Kosten.
5. Aluminiumplatte: im Allgemeinen für Oberflächenchromat (J11-A), Oxidation (leitfähige Oxidation, chemische Oxidation), hohe Kosten, Silberbeschichtung, Vernickelung.
6. Aluminiumprofil: Das Material mit komplexer Querschnittstruktur ist in einer Vielzahl von Baugruppenträgern am meisten benutzt. Oberflächenbehandlung mit Aluminiumplatte.
7. Edelstahl: Hauptsächlich ohne Oberflächenbehandlung, hohe Kosten verwendet.
Zeichnungsüberprüfung
Um den technologischen Prozess des Teils zu schreiben, müssen wir zunächst die verschiedenen technischen Anforderungen der Teilezeichnung kennen; Die Zeichnungsprüfung ist der wichtigste Teil des Prozessablaufs der Teile.
1. Überprüfen Sie, ob die Zeichnungen vollständig sind.
2. Die Ansichtsbeziehung der Zeichnungen, ob die Beschriftungen klar und vollständig sind und die Maßeinheiten sind markiert.
3. Assembly Beziehung, Montage Anforderungen Fokus Größe.
4. Der Unterschied zwischen neuen und alten Zeichnungen.
5. Übersetzung von Fremdsprachen.
6. Diagrammcode-Konvertierung
7. Zeichnungsprobleme und Feedback.
8. Material
9. Qualitätsanforderungen und Prozessanforderungen
10. Die offiziellen Freigabezeichnungen, werden mit Qualitätskontrollkapitel gestempelt.
Erweitern Sie Notizen
Erweiterte Zeichnung ist ein Plan (2D), der sich entsprechend der Teilezeichnung (3D) erweitert
1. Erweitern Sie den praktischen Weg, um Material und Bearbeitbarkeit zu sparen
2. Wählen Sie angemessen Lücken und Ränder, T = 2,0 oder weniger Abstand 0,2, T = 2-3 Abstand 0,5, Kantenumwicklung mit kurzer Kante (Doorboard)
3. Betrachten Sie die Toleranzdimensionen vernünftig: Negative Differenz, um am Ende zu gehen, positive Differenz, um die Hälfte zu gehen; Lochgröße: positive Differenz geht bis zum Ende, negative Differenz nimmt die Hälfte.
4. Burr-Richtung
5. Extrudieren, Drucknieten, Stanzpunkte (Taschen) und andere Position Richtungen, zeichnen Sie eine Schnittansicht
6. Überprüfen Sie Material, Plattendicke, Dickentoleranz
7. Sonderwinkel, Innenradius des Biegewinkels (normalerweise R = 0,5)
8. Wenn fehleranfällige (ähnliche Asymmetrie) sollte auf die Aufforderung konzentrieren
9. Platz zum Hinzufügen einer vergrößerten Ansicht in größerer Größe
10. Notwendigkeit, Schutzplatz zu sein, um Logo zu sein
Blechbearbeitungsprozess
Je nach dem Unterschied in der Struktur der Blechteile kann der Prozessablauf unterschiedlich sein, aber die Summe überschreitet nicht die folgenden Punkte.
1, Blanking: Blanking Weg gibt es verschiedene, hauptsächlich auf folgende Weise
1> Scheren: Scheren werden verwendet, um Streifen aus einfachen Materialien zu schneiden. Es wird hauptsächlich für die Formgebung und Bearbeitung von Rohlings verwendet. Die Kosten sind niedrig und die Genauigkeit ist weniger als 0,2. Es können jedoch nur Rohlinge oder Blöcke ohne Löcher oder Ecken bearbeitet werden.
2> Punch: Es ist die Verwendung von Punch, um die flachen Teile der Teile zu teilen, nachdem sie auf der Platte entfaltet wurden, um alle Arten von Formen zu bilden. Die Vorteile sind kurze Arbeitszeiten, hohe Effizienz, hohe Präzision, geringe Kosten und für die Massenproduktion geeignet. Notwendigkeit, die Form zu entwerfen.
3> NC-Ausblendung, NC-Ausblendung zuerst, um das NC-Programm zu schreiben, mit Programmiersoftware, Die entwickelte Zeichnung wird als ein erkennbares Programm von der NC-Nummer Zeichenmaschine geschrieben. Gemäß diesen Programmen kann es verwendet werden, um flache Komponenten verschiedener Formen einzeln auf die flache Platte zu stanzen, aber seine Struktur wird durch die Struktur der Schneidvorrichtung beeinflusst. Die Kosten sind niedrig und die Genauigkeit beträgt 0,15.
4. Laser Blanking: Es nutzt ein Laser-Schneidverfahren, um die Form seiner flachen Platte auf einer großen flachen Platte zu schneiden. Sie müssen ein Laserprogramm wie NCblanking schreiben. Es kann eine Vielzahl von komplexen Formen von flachen Teilen, hohe Kosten, Genauigkeit von 0,1 sein.
5> Säge: Hauptsächlich unter dem Aluminium, Vierkantrohr, Rohr, Rundstab und dergleichen, kostengünstig, geringe Präzision.
2. Monteur: Senkbohrung, Gewindebohren, Reiben, Bohren
Der Senkwinkel beträgt im Allgemeinen 120 ° C für das Nieten, 90 ° für die Senkschrauben und das Gewinde für die unteren Bohrungen.
3. Bördeln: Auch als Ziehloch, Bördeln bezeichnet, wird ein größeres Loch in ein kleineres Basisloch gezeichnet und dann geklopft. Verwenden Sie hauptsächlich Bleche mit relativ dünner Plattendicke, um die Festigkeit und die Anzahl der Gewindegänge zu erhöhen, um ein Verrutschen zu vermeiden. Im Allgemeinen für relativ dünne Plattendicke verwendet, seine normale flache Loch Bördelung, die Dicke ändert sich nicht, Dicke von 30-40% ist erlaubt, Höhe 40-60% höher als normale Flanschhöhe zu erhalten. Mit einem Druck von 50% kann die maximale Flanschhöhe erreicht werden. Wenn die Plattendicke groß ist, wie 2,0, 2,5 usw., kann die Plattendicke direkt abgegriffen werden.
4. stanzen: Ist die Verwendung von Formenbau Prozess, die allgemeine Stanzbearbeitung Stanzen, Schneiden Winkel, Ausstanzen, Schlaghöcker (Beulen), Stanzen reißen, zeichnen Löcher, Formen und andere Verarbeitungsmethoden. Die Verarbeitung muss eine entsprechende Form haben, um den Vorgang zu vervollständigen, wie beispielsweise Stanzen des Stanzwerkzeugs, des konvexen Beutelwerkzeugs, des Reißwerkzeugs, des Sauglochwerkzeugs, des Formwerkzeugs usw. Der Betrieb berücksichtigt hauptsächlich die Position und Richtung.
5. Drucknieten: Es gibt Drucknietmuttern, Schrauben, lose, etc. durch die hydraulische Drucknietmaschine oder den Stempel, um den Vorgang zu vervollständigen, es an den Blechteilen zu vernieten, achten Sie auf Direktionalität.
6. Biegen: Beim Biegen wird ein 2D-Teil zu einem 3D-Teil gefaltet. Die Bearbeitung erfordert ein Faltbett und einen entsprechenden Biegestempel und hat auch eine bestimmte Biegefolge. Das Prinzip ist die erste Falte, die das nächste Messer nicht stört.
Die Anzahl der Biegungen wird berechnet, indem die Rillenbreite mit dem Sechsfachen der Dicke von T = 3,0 mm oder weniger berechnet wird. Wie: T = 1,0, V = 6,0 F = 1,8, T = 1,2, V = 8, F = 2,2, T = 1,5, V = 10, F = 2,7, T = 2,0, V = 12, F = 4.0
Folding Bett Schimmel Klassifizierung, gerade Messer, Machete (80 ° C, 30 ° C)
Wenn die Aluminiumplatte gebogen wird, gibt es einen Riss, der die Breite der unteren Formnut vergrößern kann, um die obere Form R zu erhöhen (Glühen kann Risse vermeiden).
Beachten Sie beim Biegen: Ich plane Oberfläche, benötige Plattendicke, Menge; II Biegerichtung
Biegewinkel; IV Biegegröße; VI Aussehen, galvanisch verchromte Teile dürfen nicht geknickt werden.
Der Zusammenhang zwischen Biege- und Nietvorgang: Unter normalen Umständen zuerst vernieten, dann biegen. Wenn das Material jedoch nach dem Nieten gepresst wird, muss es gefaltet und dann gepresst werden. In einigen Fällen sind Biegen, Nieten und Nachbiegen erforderlich.
6. Schweißen: Auch als Spleißen bezeichnet, ist ein Herstellungsverfahren und eine Technik zum Verbinden von Metallen oder anderen thermoplastischen Materialien, wie Kunststoffen, durch Erhitzen, hohe Temperatur oder hohen Druck.
1> Klassifizierung: ein Schmelzschweißen: Argon Lichtbogenschweißen, CO2-Schweißen, Gasschweißen, Handschweißen
b. Druckschweißen: Punktschweißen, Stumpfschweißen, Stoßschweißen
c. Löten: elektrochromes Schweißen, Kupferdraht
2> schweißmethoden: ein CO2 gas abgeschirmt schweißen
b. Argon-Lichtbogenschweißen
c. Punktschweißen
d. Roboterschweißen
Die Wahl des Schweißverfahrens basiert auf den tatsächlichen Anforderungen und Materialien. Im Allgemeinen wird das CO2-Gasabschirmschweißen für Eisenblech-Schweißbohrungen verwendet; Argon-Lichtbogenschweißen für Edelstahl, Aluminiumschweißen. Roboterschweißen spart Arbeitsstunden, verbessert die Arbeitseffizienz und Schweißqualität und reduziert die Arbeitsintensität.
3> schweißsymbole: Δ kehlnaht, Ä, ich schweißen, V schweißen, einseitige V schweißen (V) mit stumpfen V schweiß (V), punktschweißen (O), steckerschweißen oder schlitzschweißung (Π), Crimp (χ) , Einseitige V-Schweißung mit stumpfen Kanten (V), U-förmige Schweißung mit stumpfen, J-förmigen Schweißen mit stumpfen, Back-End-Schweißen, Fracturing
4> Pfeillinien und Anschlüsse
5> Fehlende Schweißnähte und deren Vermeidung
Punktschweißen: Unzureichende Festigkeit kann Stöße treffen, Schweißbereich aufstellen
CO2-Schweißen: hohe Produktivität, geringer Energieverbrauch, geringe Kosten, starke Rostbeständigkeit
Argon Lichtbogenschweißen: geringe Auflösungstiefe, langsame Schweißgeschwindigkeit, geringe Effizienz, hohe Produktionskosten, Wolfram-Clip-Defekte, aber mit guter Schweißqualität, können NE-Metalle, wie Aluminium, Kupfer, Magnesium und so weiter geschweißt werden.
6> Schweißverformung verursacht: unzureichende Vorbereitung vor dem Schweißen, muss die Befestigung erhöhen
Schweißvorrichtung schlechter Verbesserungsprozess
Schlechte Schweißsequenz
7> Schweißverformungseffekt Positive Methode: Flammeneffektmethode
Vibrationsmethode
Hämmern
Künstliches Altern
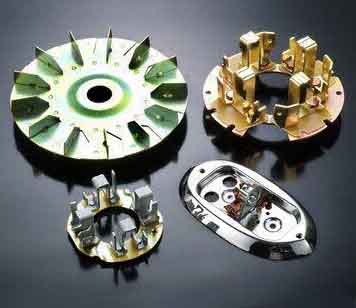