Application and Development of Titanium Alloy in Biomedical Materials
Keywords: medical titanium alloy, titanium alloy medical equipment products, titanium alloy medical accessories, surgical implant titanium alloy parts, Chinese medical titanium parts processing
Biomedical titanium alloy materials are specifically referred to as a class of functional structural materials for biomedical engineering, specifically for the production and manufacture of surgical implants and orthopedic instrument products. Titanium alloy medical device products such as artificial joints, dental implants and vascular stents are used for clinical diagnosis, treatment, repair, replacement of human tissues or organs, or to enhance the function of human tissues or organs, and their effects are irreplaceable by drugs. Medical titanium alloy materials research involves materials, physics, chemistry, biology, medicine and advanced electron microscopy and biochemical analysis. The research directions include: Alloy design and evaluation system for medical metal materials. The processing-tissue-performance relationship of the material matches the compatibility of the soft and hard tissues of the human body, and the surface modification of the material (biocompatibility, biofunctionality, biological activity, abrasion resistance, corrosion resistance, etc.). And the interaction law between the material matrix and the surface (interface).
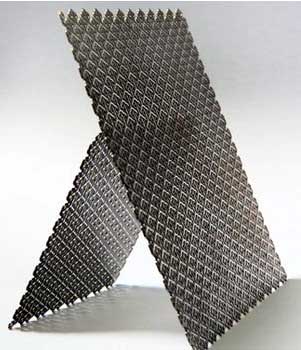
According to professional standards for surgical implants and orthopedic instruments, titanium alloy materials can be classified as "metal materials" in "surgical implant materials". Titanium alloy materials can serve as cardiovascular in non-active surgical implants, active surgical implants, and orthopedic instruments. Machining materials for implanted products such as bones and joints, bone joints, spine, orthopedic instruments, pacemakers and defibrillators, cochlear implants, and neurostimulators. The basic characteristics of biomedical titanium alloy materials are shown in Table 1 [2]. Biomedical titanium alloys can be classified into three types according to the microstructure type of the material: α type, α + β type and β type titanium alloy.
The biomedical titanium alloy is processed into an open porous, three-dimensional through structure. It facilitates the adhesion, differentiation and growth of new bone cell tissue in the body and the transport of moisture and nutrients. And its density, strength and Young's modulus can be matched to natural bone by the adjustment of porosity. Thereby the surgical implant and bone tissue are finally integrated into a special composite material, increasing the long-term stability and effectiveness of the surgical implant. Therefore, porous titanium and titanium alloys are considered to be the most attractive biomedical implant materials at present, and they are also the focus of future development. In 2003, Professor J.P. Li of the Netherlands made a porous mesh titanium alloy dental implant using the porous sponge method. It has been found that porous titanium with a pore size of 100 to 500 μm is most promising as an orthopedic dental implant material. Subsequently, Exactech Company of the United States obtained a porous surface with an average pore size of 152 μm and a porosity of 35% at the proximal end of the joint shank by titanium bead sintering. A porous surface having a pore size of 250 to 450 μm and a void ratio of 61% was also produced by a porous spraying technique. In recent years, some new technologies for porous titanium processing have emerged, which have attracted people's attention. For example, Laser Solid Forming (LSF) technology developed since the 1990s has successfully produced porous pure Ti, iNi and TC4. The porous CoCrMo/Ti6Al4V functionally graded material was prepared on the alloy and on the artificial joint cup. Huang Weidong, the State Key Laboratory of Solidification Technology, Northwestern Polytechnical University, China, is at the forefront of research in this field. It independently developed advanced laser stereo forming and repair equipment and realized commercial application for the first time in China. The research group of the Northwest Nonferrous Metals Research Institute Yu Zhentao also successfully obtained the surface porous titanium alloy material by laser etching technology. Li Yanxiang of Tsinghua University used directional solidification technology to prepare oriented porous magnesium metal materials.
Biomedical materials are an important material basis for modern clinical medicine. It is one of the frontiers and hot spots of material research in the 21st century. Biomedical materials and products are also the highest value-added high-tech products developed in the past 30 years. It has become a new pillar industry and a new economic growth point in the world.
Therefore, strengthen the effective cooperation and close cooperation between biomedical materials research units, medical device manufacturers and medical care institutions to further develop new high-quality medical titanium alloy materials. Strengthen the optimization and upgrading of traditional medical titanium alloy materials, and strive to reduce the price of medical titanium materials, To solve the human body soft and hard tissue repair and replacement products with different strength levels, good plastic toughness, anti-fatigue, rigid and flexible and physiologically compatible titanium alloy implants. Key core technologies for the processing and manufacturing of interventional materials and their medical device products. Realizing localization as soon as possible and creating national brand products will not only benefit the country but also the people.
Biomedical titanium alloy materials are specifically referred to as a class of functional structural materials for biomedical engineering, specifically for the production and manufacture of surgical implants and orthopedic instrument products. Titanium alloy medical device products such as artificial joints, dental implants and vascular stents are used for clinical diagnosis, treatment, repair, replacement of human tissues or organs, or to enhance the function of human tissues or organs, and their effects are irreplaceable by drugs. Medical titanium alloy materials research involves materials, physics, chemistry, biology, medicine and advanced electron microscopy and biochemical analysis. The research directions include: Alloy design and evaluation system for medical metal materials. The processing-tissue-performance relationship of the material matches the compatibility of the soft and hard tissues of the human body, and the surface modification of the material (biocompatibility, biofunctionality, biological activity, abrasion resistance, corrosion resistance, etc.). And the interaction law between the material matrix and the surface (interface).
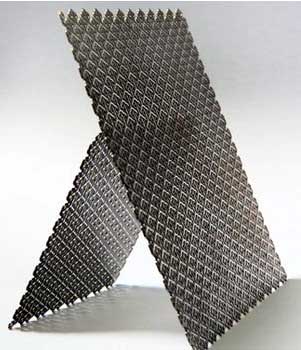
According to professional standards for surgical implants and orthopedic instruments, titanium alloy materials can be classified as "metal materials" in "surgical implant materials". Titanium alloy materials can serve as cardiovascular in non-active surgical implants, active surgical implants, and orthopedic instruments. Machining materials for implanted products such as bones and joints, bone joints, spine, orthopedic instruments, pacemakers and defibrillators, cochlear implants, and neurostimulators. The basic characteristics of biomedical titanium alloy materials are shown in Table 1 [2]. Biomedical titanium alloys can be classified into three types according to the microstructure type of the material: α type, α + β type and β type titanium alloy.
The biomedical titanium alloy is processed into an open porous, three-dimensional through structure. It facilitates the adhesion, differentiation and growth of new bone cell tissue in the body and the transport of moisture and nutrients. And its density, strength and Young's modulus can be matched to natural bone by the adjustment of porosity. Thereby the surgical implant and bone tissue are finally integrated into a special composite material, increasing the long-term stability and effectiveness of the surgical implant. Therefore, porous titanium and titanium alloys are considered to be the most attractive biomedical implant materials at present, and they are also the focus of future development. In 2003, Professor J.P. Li of the Netherlands made a porous mesh titanium alloy dental implant using the porous sponge method. It has been found that porous titanium with a pore size of 100 to 500 μm is most promising as an orthopedic dental implant material. Subsequently, Exactech Company of the United States obtained a porous surface with an average pore size of 152 μm and a porosity of 35% at the proximal end of the joint shank by titanium bead sintering. A porous surface having a pore size of 250 to 450 μm and a void ratio of 61% was also produced by a porous spraying technique. In recent years, some new technologies for porous titanium processing have emerged, which have attracted people's attention. For example, Laser Solid Forming (LSF) technology developed since the 1990s has successfully produced porous pure Ti, iNi and TC4. The porous CoCrMo/Ti6Al4V functionally graded material was prepared on the alloy and on the artificial joint cup. Huang Weidong, the State Key Laboratory of Solidification Technology, Northwestern Polytechnical University, China, is at the forefront of research in this field. It independently developed advanced laser stereo forming and repair equipment and realized commercial application for the first time in China. The research group of the Northwest Nonferrous Metals Research Institute Yu Zhentao also successfully obtained the surface porous titanium alloy material by laser etching technology. Li Yanxiang of Tsinghua University used directional solidification technology to prepare oriented porous magnesium metal materials.
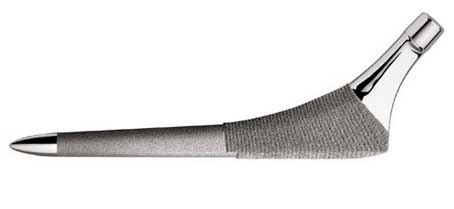
Biomedical materials are an important material basis for modern clinical medicine. It is one of the frontiers and hot spots of material research in the 21st century. Biomedical materials and products are also the highest value-added high-tech products developed in the past 30 years. It has become a new pillar industry and a new economic growth point in the world.
Therefore, strengthen the effective cooperation and close cooperation between biomedical materials research units, medical device manufacturers and medical care institutions to further develop new high-quality medical titanium alloy materials. Strengthen the optimization and upgrading of traditional medical titanium alloy materials, and strive to reduce the price of medical titanium materials, To solve the human body soft and hard tissue repair and replacement products with different strength levels, good plastic toughness, anti-fatigue, rigid and flexible and physiologically compatible titanium alloy implants. Key core technologies for the processing and manufacturing of interventional materials and their medical device products. Realizing localization as soon as possible and creating national brand products will not only benefit the country but also the people.
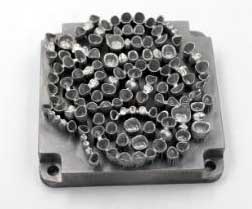