Verbesserung der Leistung von Folgeverbundwerkzeugen
Das progressive Stanzen ist eine kostengünstige und sichere Methode zur Herstellung von Bauteilen. Sorgfältige Konstruktion und Konstruktion der Werkzeuge gewährleisten eine optimale Leistung.
Eine Folgeform führt eine Reihe grundlegender Blechbearbeitungen an zwei oder mehr Stationen in der Form während jedes Pressenhubs durch. Diese gleichzeitigen Vorgänge erzeugen ein Teil aus einem Materialstreifen, der sich durch die Matrize bewegt. Jede Arbeitsstation führt einen oder mehrere Stanzvorgänge durch, aber der Streifen muss sich von der ersten Station durch jede nachfolgende Station bewegen, um ein vollständiges Teil herzustellen. Träger, die aus einem oder mehreren Materialstreifen bestehen, die zwischen den Teilen verbleiben, sorgen für die Bewegung der Teile von einer Matrizenstation zur nächsten. Diese Trägerstreifen werden in der letzten Werkzeugstation von den Teilen getrennt.
Es gibt sechs Elemente, die beim Entwerfen und Erstellen einer fortschrittlichen Form berücksichtigt werden sollten, um die Leistung zu maximieren:
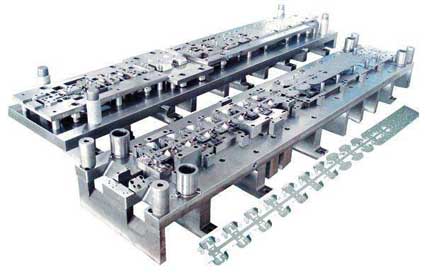
Teiledruck interpretieren
Ausgangsmaterial in die Form
Teilelifter und Teilefütterung
Flexible Teileträger
Obere Druckstücke
Gezeichnete Muscheln.
Interpretation des Teiledrucks
Der erste Schritt bei der richtigen Gestaltung einer progressiven Form ist die korrekte Analyse des Teiledrucks. Der Werkzeugkonstrukteur muss den Druck interpretieren, um die Funktion des Teils zu bestimmen, indem er nach Materialien, kritischen Oberflächen, Lochgröße und -position, Gratposition, Kornrichtungsanforderungen, Oberflächengüte und anderen Faktoren sucht.
Der Formenbauer muss das Teil gut verstehen, insbesondere wenn es unregelmäßige Formen und Konturen aufweist. Moderne computergezeichnete Drucke erschweren dies jedoch, da computergezeichnete Teiledaten direkt auf den Formkonstruktionscomputer heruntergeladen werden können. Infolgedessen kann es sein, dass der Konstrukteur wichtige Teileigenschaften nicht genau kennt.
Außerdem sind viele computergezeichnete Teile schwieriger zu verstehen, da häufig nur eine Oberfläche gezeigt wird und es sich um die Innen- oder Außenfläche handeln kann. Computerzeichnungen zeigen häufig alle Linien, einschließlich verborgener Merkmale, als durchgezogene Linien anstelle von gepunkteten Linien. Dies führt zu Auslegungsfehlern, was wiederum zu Fehlern beim Formenbau führt.
Um komplexe Teileformen besser zu verstehen, ist es hilfreich, ein "Visier" -Modell des Teils unter Verwendung von Wachsplatten, Gummihäuten oder Holzmodellen zu erstellen. Die Maßgenauigkeit ist für diese Modelle nicht kritisch, da sie hauptsächlich zur Visualisierung des Teils verwendet werden. Gummihäute und Wachsplatten können auch zum Entwickeln von Vorformlingsformen und zum Entwickeln der besten Positionen für das Teil verwendet werden, wenn es die einzelnen Formvorgänge in der Folgeform durchläuft.
Ausgangsmaterial in der Form
Es muss darauf geachtet werden, dass der Streifen richtig in die Form eingelegt wird. Durch eine falsche Positionierung des vorderen Bandendes wird die Form in den ersten 10 Hüben der Presse stärker beschädigt als bei den nächsten 100.000 Hüben.
"Einlauf" -Anzeigen müssen große Zuleitungen und einen Vorsprung aufweisen, um das Zuleitungsende des Spulenstreifens zu stützen, wenn dieser in die Form eingeführt wird. Große Zuleitungen an den Messgeräten sind wichtig, damit die Person, die das Werkzeug einrichtet, nicht in das Werkzeug greifen muss und um die Zeit zu minimieren, die erforderlich ist, um einen neuen Streifen in das Werkzeug einzuführen. Außerdem sollte eine Lehre einstellbar sein, um Abweichungen in der Bandbreite auszugleichen.
Die Position der Vorderkante des Streifens ist für den ersten Pressenhub kritisch und muss für jede Formstation bestimmt werden, um sicherzustellen, dass Stanzstempel keine Teillöcher in die Vorderkante schneiden. Dies kann zu einer Durchbiegung des Stempels führen oder zu einem teilweisen Schnitt mit Schneidstempeln, was zu einer unausgeglichenen Seitenbelastung führen kann, wenn der Streifen durch die Form läuft. Jede dieser Bedingungen kann zu einer Verschiebung des Verhältnisses von Stempel zu Form führen, die ein Abscheren der Stempel verursachen kann.
Eine falsche Anordnung der Vorderkante des Streifens kann auch zu einem unausgeglichenen Formungs- oder Bördelzustand führen, der die obere Form in Bezug auf die untere Form verschieben kann. Es sollten Absätze erforderlich sein, um diese Seitenbelastung aufzunehmen, insbesondere wenn dicke Materialien geformt werden.
Eine Teilungskerbe und ein Teilungsstopp können einen physischen Punkt zum Lokalisieren und Steuern der Vorderkante des Streifens bereitstellen. Messingschilder oder Markierungsnuten können ebenfalls eine visuelle Position bereitstellen, diese sind jedoch nicht so genau oder effektiv wie ein Pitch-Notch-Stop. Es kann verhindert werden, dass die Presse mit einem kurzen Vorschub oder einem Übervorschub betrieben wird, indem der Pitch-Stop an einem Drehpunkt angebracht und mit einem Endschalter überwacht wird
Teilelifter und Teilezuführung
Progressive Formen erfordern oft, dass der Streifen von der normalen Formarbeitsebene auf die Vorschubebene angehoben wird, bevor die Bandzufuhr stattfindet. Dies kann von einer kleinen Menge - um Schnitt- und Stanzgrate zu entfernen - bis zu mehreren Zoll variieren, damit Teileformen die Form entfernen können.
Normalerweise sollten alle Heber auf die gleiche Höhe steigen, damit der Streifen beim Vorschub in einer ebenen Ebene abgestützt wird. Der Streifen darf nicht zwischen den Hebern durchhängen. Andernfalls werden Teile aus ihrem korrekten Stationsabstand herausgezogen. Stangenlifter bieten guten Halt und sind besser als Federstifte oder runde Lifter, die an einer Seite des Streifens eingekerbt sind.
Oft ermöglicht ein gutes Stangenliftsystem höhere Pressengeschwindigkeiten, da Vorschubprobleme beseitigt werden. Obwohl die anfänglichen Kosten mehr als bei runden Hebegeräten betragen, ist die Leistung besser und die Rüstzeit wird verkürzt.
As the strip is started into the lead-in gauges, the strip should be able to feed automatically through all the following die stations without requiring manual alignment in each set of gauges and lifters. The strip also must be balanced on the lifters so that it does not fall to one side during feed. A retainer cap can be mounted on the top of the outside bar lifters. This produces a groove that captures the strip during feed and prevents strip buckling.
Mess- und Hebebedingungen können während des Formenbaus simuliert werden, indem ein Stück Transparentpapier auf die Breite des Streifens zugeschnitten wird. Die Vorderkante des Papiers wird über der Draufsicht des Formdesigns an der Stelle platziert, an der sich der Streifen für den ersten Pressenhub befindet. Anschließend wird das Papier mit allen Vorgängen markiert, die an der ersten Formstation ausgeführt werden, z. B. Ausklinken und Stanzen. Der Papierstreifen wird dann zur zweiten Station in der Zeichnung bewegt, und die Vorgänge für die erste und die zweite Station werden markiert. Dieser Vorgang wird in allen Werkzeugstationen wiederholt, um zu veranschaulichen, wie der echte Teilestreifen aussehen wird, wenn er in das Werkzeug eingelassen wird, und um die Angemessenheit von Messgeräten und Hebern zu bestimmen.
Flexible Teileträger
Um den Streifen in einer Folgeform von einer Station zur nächsten zu transportieren, muss etwas Material zwischen den Teilen auf dem Streifen verbleiben. Dieses Trägermaterial kann über die Breite des Streifens fest sein oder es kann sich um ein oder mehrere schmale Materialbänder handeln, siehe Teilträgerseitenleiste.
Bei vielen Teilen muss die Kante des Rohlings beim Bördeln, Formen oder Ziehen nach innen fließen. Dies kann erfordern, dass sich der Träger während des Formvorgangs zur Seite bewegt oder sich vertikal biegt oder beides. Im Träger muss eine flexible Schlaufe vorhanden sein, um das Biegen und Bewegen des Rohlings zu ermöglichen, ohne die angrenzenden Teile aus der Position zu ziehen.
Ein weiteres Problem ist das vertikale "Atmen" von Teilen in Formstationen während des Schließens und Öffnens der Form im Pressenhub. Beispielsweise findet eine vertikale Atmung zwischen den Ziehstationen von Teilen statt, die mehr als eine Ziehung benötigen, um das Teil fertigzustellen. Vertikales Atmen tritt auch auf, wenn ein Flansch in einer progressiven Formstation "nach oben" geformt wird, die an Stationen angrenzt, die obere Druckkissen verwenden, um die angrenzenden Teile nach unten zu halten.
Es ist wichtig, das Biegen des Trägers während des Aufwärtshubs der Presse sowie während des Abwärtshubs zu berücksichtigen, da die Wirkung unterschiedlich sein kann. Dies kann in der Entwurfsphase simuliert werden, indem der Querschnitt des Teils, die Druckkissen und die stationär montierten Stähle auf separaten Papierblättern skizziert werden und diese Blätter dann in Schichten übereinander über die Form gelegt werden Schnittansichten. Diese Bleche werden dann relativ zueinander nach unten bewegt, um zu simulieren, wie sich die obere Form während des Abwärtshubs der Presse schließen würde. Dies zeigt die relative Position des Teils beim Schließen der Form und während des umgekehrten Vorgangs beim Öffnen des Formstempels.
Allen Folgeprägeformen gemeinsam ist das Material, das die Teile beim Durchlauf durch die Form von Station zu Station transportiert. Dieses Material ist unter verschiedenen Begriffen wie Träger, Bahn, Streifen, Krawatte, Befestigung usw. bekannt. In diesem Fall wird der Begriff Träger verwendet, für den es fünf grundlegende Stile gibt:
Solider Träger - Alle erforderlichen Arbeiten können am Teil ohne vorheriges Beschneiden ausgeführt werden. Das Teil wird im letzten Arbeitsgang abgeschnitten oder ausgestanzt.
Mittelträger - Die Peripherie des Teils ist beschnitten. Lassen Sie nur eine schmale Krawatte in der Mitte des Teils. Dadurch können Arbeiten rund um das Teil ausgeführt werden. Ein breiter Mittelträger ermöglicht das Beschneiden nur an den Seiten des Teils.
Lanze und Trage in der Mitte - Der Streifen wird zwischen die Teile gestochen, wobei ein schmaler Bereich in der Nähe der Mitte verbleibt, um die Teile zu tragen.
Dadurch werden Materialabfälle zwischen den Teilen vermieden.
Äußere Träger - Die Träger sind an den Seiten des Teils angebracht, sodass die Arbeit in der Mitte des Teils ausgeführt werden kann.
Einseitiger Träger - Das Teil wird ganz oder teilweise durch die Form geführt, wobei sich der Träger nur auf einer Seite befindet. Dies ermöglicht das Arbeiten an drei Seiten des Teils.
Die Art oder Form des Trägers hängt davon ab, was das Teil benötigt, wenn es sich von Station zu Station in der Form bewegt. Die Materialbreite kann fest bleiben, wenn beim Schließen der Form keine Materialbewegung erforderlich ist, oder sie kann gekerbt werden, um einen, zwei oder sogar drei Träger zwischen den Teilen zu erzeugen.
Die Träger können gerade sein, ein Zick-Zack-Muster bilden oder Schleifen zwischen den Teilen aufweisen, je nachdem, wo Befestigungspunkte an dem Teil vorhanden sind oder welchen Abstand das Formwerkzeug benötigt. Wenn das Teil geformt, gebördelt oder zu einer Schale gezogen wird, muss sich der Träger möglicherweise seitwärts oder auf und ab bewegen, wenn sich die Form schließt und öffnet.
Wenn sich der Träger beim Formen bewegt, muss er normalerweise gebogen oder gedehnt werden. Unabhängig von der Durchbiegung der Träger besteht ihre Schlüsselfunktion darin, die Teile nahe genug an die nächste Station zu bringen, damit Piloten, Messgeräte und Ortungsgeräte die Teile beim Schließen der Form genau an ihren Platz bringen können.
Wenn der Träger eine dauerhafte Dehnung erfährt, können die Teile zu weit voranschreiten, um in die nächste Station zu passen, oder wenn die Form zwei Träger aufweist, kann ein Träger eine dauerhafte Dehnung ohne Dehnung im anderen Träger entwickeln. Dadurch wird im Streifen eine Kantenwölbung erzeugt, die dazu führt, dass der Streifen nach einer Seite abweicht. Dies führt zu einer schlechten Teilelage.
Ein gedehnter Träger kann durch Einlegen einer Vertiefung in den Träger auf die richtige Länge gekürzt werden. Wenn sich bei einem Mittelträger oder einem einseitigen Träger eine Wölbung entwickelt, kann der Streifen durch Einkerbung oder Einkerbung einer Seite des Trägers begradigt werden. Konstruieren Sie die Grübchen- und Rillstempel so, dass sie für die Position leicht seitlich und für die Tiefe vertikal eingestellt werden können.
Die Kantenwölbung des Materials, wenn es vom Coil geliefert wird, kann dazu führen, dass sich der Streifen in den Lauflehren festsetzt, die das Material während des Vorschubzyklus führen. Diese Bindung kann zum Knicken der Träger führen, was zu kurzen Vorschüben führt. Oft hilft es, die Führungskante der Lehren zwischen den Stationen zu entlasten und die Kontrolle über die Lehren am Arbeitsplatz zu verschärfen.
Eine andere Möglichkeit besteht darin, den Sturz zu beseitigen, indem am Anfang der Form beide Seiten des Materials abgeschnitten werden. Durch Hinzufügen von Anschlägen am Ende dieser Trimmnuten können sie als Pitch-Control-Nuten verwendet werden, um ein Überfahren des Vorschubs zu verhindern.
Optimales Trägerprofil
Das optimale Trägerprofil wird durch einige der folgenden Bedingungen beeinflusst:
Befestigungspunkte zum Teil:
Wenn zwei Träger verwendet werden, versuchen Sie, das Profil und die Länge der Träger in etwa gleich zu halten, damit die Auswirkung der Trägerbiegung nahezu ausgeglichen ist.
Abstand für Stempel- und Matrizenblöcke:
Stanzblöcke, die sich unter dem Schaft erstrecken, oder Matrizenblöcke, die sich über dem Schaft erstrecken, wenn sich die Matrize schließt, erfordern einen Abstand zu den Teilen und den Trägern. Wenn eine Schleife des Trägers Blöcke stört, kann es möglich sein, die Schleife vertikal auszubilden, um einen Freiraum zu schaffen.
Dicke des Materials:
Bei großen Teilen mit dünnem Material sind möglicherweise Versteifungswülste erforderlich, um dem Träger für die Materialzufuhr mehr Festigkeit zu verleihen. Eine weitere Methode zur Versteifung und Bandführung besteht darin, die Kante des Materials zu lanzen und zu bördeln, was auch als Fortschrittskerbe verwendet werden kann.
Die Summe des Streifens: Schwere Teile in langen Formen erfordern mehr Kraft, um den Streifen durch die Form zu drücken. Das Gewicht ist jedoch normalerweise dickes Material und dickes Material ist steifer als dünnes Material. Als Faustregel gelten flexible Träger für
Materialien von 0,020 Zoll bis 0,060 Zoll sind etwa 3/16 Zoll bis 5/16 Zoll breit. Für Materialstärken oberhalb und unterhalb dieses Dickenbereichs Träger
width ist ein "Best Judgement Call".
Abhängig von allen beteiligten Formfaktoren sollten die Träger unter normalen Bedingungen über ihre gesamte Länge eine gleichmäßige Breite aufweisen, insbesondere jedoch im Bereich des Biegens. Da fast jede Materialzuführung Material durch die Form schiebt, anstatt das Material zu ziehen, muss der Träger stark genug sein, um die Teile vollständig durch die Form zu schieben.
Ein Erfassungsschalter, der durch einen vollständigen Vorschub des Streifens am Ausgang der Form betätigt wird, kann ein Knicken erfassen. Wenn die Wirkung der Form während des Schließens oder Öffnens der Presse erfordert, dass sich die Träger biegen, konstruieren Sie den Träger mit Schlaufen, die lang genug sind, um sich zu biegen, ohne zu brechen, aber dennoch stark genug sind, um alle Teile bis zum vollständigen Fortschreiten zu befördern. Wenn zwei flexible Träger nicht stark genug sind, um den Streifen zuzuführen, sollten Sie drei Träger in Betracht ziehen.
Versuchen Sie, die Radien in Flex-Loops so groß wie möglich zu machen. Scharfe Ecken oder kleine Radien konzentrieren die Biegebeanspruchung und machen sie zum ersten Bruchpunkt beim Biegen des Trägers. Vermeiden Sie auch Stufen oder Kerben in den Kanten des Trägers.
Obere Druckpads
Aufgrund der Größe oder Funktion erfordern viele progressive Formen zwei oder mehr Druckkissen in der oberen Form. Jeder erfordert möglicherweise eine andere Verfahrstrecke, um die Arbeit in der einzelnen Formstation auszuführen, wie z. B. Beschneiden oder Formen oder Ziehen.
Die oberen Druckkissen werden jedoch häufig verwendet, um die Materialheber nach unten zu drücken, indem sie gegen die Leiste gedrückt werden, wodurch die Heber nach unten gedrückt werden. In dieser Situation sollten alle Druckstücke, die die Materialheber nach unten drücken, den gleichen Verfahrweg haben. Wenn die oberen Druckkissen unterschiedliche Strecken zurücklegen, wird der Streifen nicht gleichmäßig nach unten gedrückt. Dies kann benachbarte Teile aus der Folge herausziehen, was es schwierig macht, die Teile nach dem Vorschubzyklus in ihrer richtigen Stationsposition zu lokalisieren.
Wenn für das Teil ein Flansch geformt werden muss, muss der Teileträger eine flexible Schlaufe aufweisen, um ein vertikales Atmen des Teils zu ermöglichen, oder einen Druckstempel / ein Druckkissen mit demselben Hub wie die anderen Druckkissen bereitstellen. Die Kraft, die der Druckstempel / das Druckkissen benötigt, muss ausreichen, um die Flansche während des Abwärtshubs auszubilden, während der Stempel / das Druckkissen in der ausgefahrenen Position ist. Dies verhindert, dass der Streifen vertikal atmet, wenn er vom Vorschubniveau auf das normale Arbeitsniveau heruntergedrückt wird.
Wenn der Streifen das Arbeitsniveau erreicht, stoppt der unter Druck stehende Stempel / Block seine Abwärtsbewegung, während die obere Form zum Stanzen, Trimmen, Abwärtsbördeln und für andere Vorgänge weiter abwärts bewegt wird. Federn oder Stickstoffflaschen können für den Druck in diesen Druckstationen verwendet werden. Sie müssen jedoch über eine ausreichende Vorspannkraft verfügen, um die Flansche zu formen und das untere Greifkissen zusammenzuklappen, bevor das obere Stempelkissen zurücktritt.
Zuginstanz
Tensile Instance werden erzeugt, wenn das Bandmaterial von einer flachen Ebene in eine zylindrische Form geändert wird. Während des Ziehvorgangs wird der "Durchmesser" des Rohlings auf den "Umfang" der Schale reduziert. Wenn der Umfang während des Materialflusses nach innen verringert wird, geht der äußere Teil des Materials in eine Seiten- oder Kantenkompression über.
Wenn diese Kompression zu groß wird, als dass das Material flach bleiben könnte, beginnt es sich zu falten oder zu knittern. Um dies zu verhindern, kann das Material in einem kontrollierten Spalt zwischen einem Ziehring und einem Druckkissen fließen. Die beiden Hauptursachen für ein Versagen beim Zeichnen einer Schale sind ein Überschreiten des Prozentsatzes, in dem der Durchmesser des Rohlings (oder der Schale) verringert ist, und ein falscher Radius des Ziehrings.
Es gibt eine Grenze dafür, wie weit Metall nach innen fließt, wenn vom Rohlingsdurchmesser zum ersten Ziehdurchmesser und von einem gezogenen Schalendurchmesser zu einem kleineren Schalendurchmesser gezogen wird. Dies wird als Prozentsatz der Ziehungsverringerung ausgedrückt. Der maximale Prozentsatz der Reduktion wird durch den Materialfluss nach innen begrenzt, der bewirkt, dass das Metall komprimiert wird, was wiederum einen Strömungswiderstand verursacht. Zu viel Widerstand führt zu einem Bruch in der Nähe des Deckels der Schale, der den schwächsten Spannungsbereich darstellt.
Der Prozentsatz der Reduktion variiert mit der Metalldicke. Beispielsweise variiert bei einem Tiefziehstahlrohling der Prozentsatz der Verringerung des Durchmessers der ersten Ziehschale von 32 Prozent für 0,015 Zoll. dickes Material auf 48 Prozent für 0,125 Zoll. dickes Material.
Der Ziehring hat einen minimalen und einen maximalen Ziehradius, die den Materialfluss steuern. Beim Tiefziehen von Stahlteilen variiert der richtige Radius zwischen 5 und 32 Zoll. Minimum bis 1/4 Zoll Maximum für 0,015 Zoll. Lager und 11/32-in. Minimum bis 15/32 Zoll Maximum für 0,125 Zoll. Stock.
Wenn der Radius zu klein ist, fließt das Metall nicht gut, was den Strömungswiderstand erhöht und zu übermäßiger Ausdünnung oder Brüchen in der Nähe des Becherkopfs führt. Wenn der Radius zu groß ist, knittert das Metall, nachdem es die Klemmstelle zwischen dem Ziehring und dem Druckkissen verlassen hat und bevor es in die vertikale Wand des Bechers geformt wird.
Die normale Tendenz besteht darin, den Radius zu klein zu machen, weil "es einfach ist, den Radius während des Probierens zu vergrößern und es schwierig ist, einen kleineren Radius zu machen". Das Ergebnis ist, dass die Tasse unnötig belastet wird, was zu übermäßiger Ausdünnung oder Brüchen führt. Das Problem eines ungenauen Prozentsatzes der Verkleinerung oder eines ungenauen Ziehradius in der ersten Ziehstation tritt häufig nicht in der ersten Ziehstation, sondern in einer späteren Nachziehstation auf, so dass viel Zeit für die Suche nach der falschen Station aufgewendet wird .
Eine Folgeform führt eine Reihe grundlegender Blechbearbeitungen an zwei oder mehr Stationen in der Form während jedes Pressenhubs durch. Diese gleichzeitigen Vorgänge erzeugen ein Teil aus einem Materialstreifen, der sich durch die Matrize bewegt. Jede Arbeitsstation führt einen oder mehrere Stanzvorgänge durch, aber der Streifen muss sich von der ersten Station durch jede nachfolgende Station bewegen, um ein vollständiges Teil herzustellen. Träger, die aus einem oder mehreren Materialstreifen bestehen, die zwischen den Teilen verbleiben, sorgen für die Bewegung der Teile von einer Matrizenstation zur nächsten. Diese Trägerstreifen werden in der letzten Werkzeugstation von den Teilen getrennt.
Es gibt sechs Elemente, die beim Entwerfen und Erstellen einer fortschrittlichen Form berücksichtigt werden sollten, um die Leistung zu maximieren:
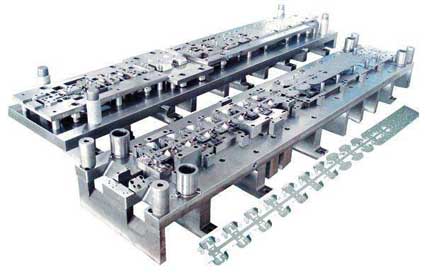
Teiledruck interpretieren
Ausgangsmaterial in die Form
Teilelifter und Teilefütterung
Flexible Teileträger
Obere Druckstücke
Gezeichnete Muscheln.
Interpretation des Teiledrucks
Der erste Schritt bei der richtigen Gestaltung einer progressiven Form ist die korrekte Analyse des Teiledrucks. Der Werkzeugkonstrukteur muss den Druck interpretieren, um die Funktion des Teils zu bestimmen, indem er nach Materialien, kritischen Oberflächen, Lochgröße und -position, Gratposition, Kornrichtungsanforderungen, Oberflächengüte und anderen Faktoren sucht.
Der Formenbauer muss das Teil gut verstehen, insbesondere wenn es unregelmäßige Formen und Konturen aufweist. Moderne computergezeichnete Drucke erschweren dies jedoch, da computergezeichnete Teiledaten direkt auf den Formkonstruktionscomputer heruntergeladen werden können. Infolgedessen kann es sein, dass der Konstrukteur wichtige Teileigenschaften nicht genau kennt.
Außerdem sind viele computergezeichnete Teile schwieriger zu verstehen, da häufig nur eine Oberfläche gezeigt wird und es sich um die Innen- oder Außenfläche handeln kann. Computerzeichnungen zeigen häufig alle Linien, einschließlich verborgener Merkmale, als durchgezogene Linien anstelle von gepunkteten Linien. Dies führt zu Auslegungsfehlern, was wiederum zu Fehlern beim Formenbau führt.
Um komplexe Teileformen besser zu verstehen, ist es hilfreich, ein "Visier" -Modell des Teils unter Verwendung von Wachsplatten, Gummihäuten oder Holzmodellen zu erstellen. Die Maßgenauigkeit ist für diese Modelle nicht kritisch, da sie hauptsächlich zur Visualisierung des Teils verwendet werden. Gummihäute und Wachsplatten können auch zum Entwickeln von Vorformlingsformen und zum Entwickeln der besten Positionen für das Teil verwendet werden, wenn es die einzelnen Formvorgänge in der Folgeform durchläuft.
Ausgangsmaterial in der Form
Es muss darauf geachtet werden, dass der Streifen richtig in die Form eingelegt wird. Durch eine falsche Positionierung des vorderen Bandendes wird die Form in den ersten 10 Hüben der Presse stärker beschädigt als bei den nächsten 100.000 Hüben.
"Einlauf" -Anzeigen müssen große Zuleitungen und einen Vorsprung aufweisen, um das Zuleitungsende des Spulenstreifens zu stützen, wenn dieser in die Form eingeführt wird. Große Zuleitungen an den Messgeräten sind wichtig, damit die Person, die das Werkzeug einrichtet, nicht in das Werkzeug greifen muss und um die Zeit zu minimieren, die erforderlich ist, um einen neuen Streifen in das Werkzeug einzuführen. Außerdem sollte eine Lehre einstellbar sein, um Abweichungen in der Bandbreite auszugleichen.
Die Position der Vorderkante des Streifens ist für den ersten Pressenhub kritisch und muss für jede Formstation bestimmt werden, um sicherzustellen, dass Stanzstempel keine Teillöcher in die Vorderkante schneiden. Dies kann zu einer Durchbiegung des Stempels führen oder zu einem teilweisen Schnitt mit Schneidstempeln, was zu einer unausgeglichenen Seitenbelastung führen kann, wenn der Streifen durch die Form läuft. Jede dieser Bedingungen kann zu einer Verschiebung des Verhältnisses von Stempel zu Form führen, die ein Abscheren der Stempel verursachen kann.
Eine falsche Anordnung der Vorderkante des Streifens kann auch zu einem unausgeglichenen Formungs- oder Bördelzustand führen, der die obere Form in Bezug auf die untere Form verschieben kann. Es sollten Absätze erforderlich sein, um diese Seitenbelastung aufzunehmen, insbesondere wenn dicke Materialien geformt werden.
Eine Teilungskerbe und ein Teilungsstopp können einen physischen Punkt zum Lokalisieren und Steuern der Vorderkante des Streifens bereitstellen. Messingschilder oder Markierungsnuten können ebenfalls eine visuelle Position bereitstellen, diese sind jedoch nicht so genau oder effektiv wie ein Pitch-Notch-Stop. Es kann verhindert werden, dass die Presse mit einem kurzen Vorschub oder einem Übervorschub betrieben wird, indem der Pitch-Stop an einem Drehpunkt angebracht und mit einem Endschalter überwacht wird
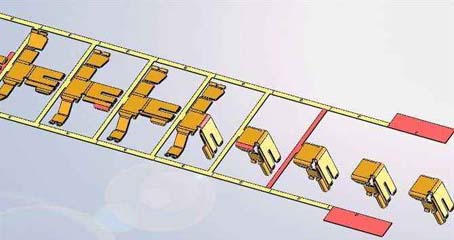
Teilelifter und Teilezuführung
Progressive Formen erfordern oft, dass der Streifen von der normalen Formarbeitsebene auf die Vorschubebene angehoben wird, bevor die Bandzufuhr stattfindet. Dies kann von einer kleinen Menge - um Schnitt- und Stanzgrate zu entfernen - bis zu mehreren Zoll variieren, damit Teileformen die Form entfernen können.
Normalerweise sollten alle Heber auf die gleiche Höhe steigen, damit der Streifen beim Vorschub in einer ebenen Ebene abgestützt wird. Der Streifen darf nicht zwischen den Hebern durchhängen. Andernfalls werden Teile aus ihrem korrekten Stationsabstand herausgezogen. Stangenlifter bieten guten Halt und sind besser als Federstifte oder runde Lifter, die an einer Seite des Streifens eingekerbt sind.
Oft ermöglicht ein gutes Stangenliftsystem höhere Pressengeschwindigkeiten, da Vorschubprobleme beseitigt werden. Obwohl die anfänglichen Kosten mehr als bei runden Hebegeräten betragen, ist die Leistung besser und die Rüstzeit wird verkürzt.
As the strip is started into the lead-in gauges, the strip should be able to feed automatically through all the following die stations without requiring manual alignment in each set of gauges and lifters. The strip also must be balanced on the lifters so that it does not fall to one side during feed. A retainer cap can be mounted on the top of the outside bar lifters. This produces a groove that captures the strip during feed and prevents strip buckling.
Mess- und Hebebedingungen können während des Formenbaus simuliert werden, indem ein Stück Transparentpapier auf die Breite des Streifens zugeschnitten wird. Die Vorderkante des Papiers wird über der Draufsicht des Formdesigns an der Stelle platziert, an der sich der Streifen für den ersten Pressenhub befindet. Anschließend wird das Papier mit allen Vorgängen markiert, die an der ersten Formstation ausgeführt werden, z. B. Ausklinken und Stanzen. Der Papierstreifen wird dann zur zweiten Station in der Zeichnung bewegt, und die Vorgänge für die erste und die zweite Station werden markiert. Dieser Vorgang wird in allen Werkzeugstationen wiederholt, um zu veranschaulichen, wie der echte Teilestreifen aussehen wird, wenn er in das Werkzeug eingelassen wird, und um die Angemessenheit von Messgeräten und Hebern zu bestimmen.
Flexible Teileträger
Um den Streifen in einer Folgeform von einer Station zur nächsten zu transportieren, muss etwas Material zwischen den Teilen auf dem Streifen verbleiben. Dieses Trägermaterial kann über die Breite des Streifens fest sein oder es kann sich um ein oder mehrere schmale Materialbänder handeln, siehe Teilträgerseitenleiste.
Bei vielen Teilen muss die Kante des Rohlings beim Bördeln, Formen oder Ziehen nach innen fließen. Dies kann erfordern, dass sich der Träger während des Formvorgangs zur Seite bewegt oder sich vertikal biegt oder beides. Im Träger muss eine flexible Schlaufe vorhanden sein, um das Biegen und Bewegen des Rohlings zu ermöglichen, ohne die angrenzenden Teile aus der Position zu ziehen.
Ein weiteres Problem ist das vertikale "Atmen" von Teilen in Formstationen während des Schließens und Öffnens der Form im Pressenhub. Beispielsweise findet eine vertikale Atmung zwischen den Ziehstationen von Teilen statt, die mehr als eine Ziehung benötigen, um das Teil fertigzustellen. Vertikales Atmen tritt auch auf, wenn ein Flansch in einer progressiven Formstation "nach oben" geformt wird, die an Stationen angrenzt, die obere Druckkissen verwenden, um die angrenzenden Teile nach unten zu halten.
Es ist wichtig, das Biegen des Trägers während des Aufwärtshubs der Presse sowie während des Abwärtshubs zu berücksichtigen, da die Wirkung unterschiedlich sein kann. Dies kann in der Entwurfsphase simuliert werden, indem der Querschnitt des Teils, die Druckkissen und die stationär montierten Stähle auf separaten Papierblättern skizziert werden und diese Blätter dann in Schichten übereinander über die Form gelegt werden Schnittansichten. Diese Bleche werden dann relativ zueinander nach unten bewegt, um zu simulieren, wie sich die obere Form während des Abwärtshubs der Presse schließen würde. Dies zeigt die relative Position des Teils beim Schließen der Form und während des umgekehrten Vorgangs beim Öffnen des Formstempels.
Allen Folgeprägeformen gemeinsam ist das Material, das die Teile beim Durchlauf durch die Form von Station zu Station transportiert. Dieses Material ist unter verschiedenen Begriffen wie Träger, Bahn, Streifen, Krawatte, Befestigung usw. bekannt. In diesem Fall wird der Begriff Träger verwendet, für den es fünf grundlegende Stile gibt:
Solider Träger - Alle erforderlichen Arbeiten können am Teil ohne vorheriges Beschneiden ausgeführt werden. Das Teil wird im letzten Arbeitsgang abgeschnitten oder ausgestanzt.
Mittelträger - Die Peripherie des Teils ist beschnitten. Lassen Sie nur eine schmale Krawatte in der Mitte des Teils. Dadurch können Arbeiten rund um das Teil ausgeführt werden. Ein breiter Mittelträger ermöglicht das Beschneiden nur an den Seiten des Teils.
Lanze und Trage in der Mitte - Der Streifen wird zwischen die Teile gestochen, wobei ein schmaler Bereich in der Nähe der Mitte verbleibt, um die Teile zu tragen.
Dadurch werden Materialabfälle zwischen den Teilen vermieden.
Äußere Träger - Die Träger sind an den Seiten des Teils angebracht, sodass die Arbeit in der Mitte des Teils ausgeführt werden kann.
Einseitiger Träger - Das Teil wird ganz oder teilweise durch die Form geführt, wobei sich der Träger nur auf einer Seite befindet. Dies ermöglicht das Arbeiten an drei Seiten des Teils.
Die Art oder Form des Trägers hängt davon ab, was das Teil benötigt, wenn es sich von Station zu Station in der Form bewegt. Die Materialbreite kann fest bleiben, wenn beim Schließen der Form keine Materialbewegung erforderlich ist, oder sie kann gekerbt werden, um einen, zwei oder sogar drei Träger zwischen den Teilen zu erzeugen.
Die Träger können gerade sein, ein Zick-Zack-Muster bilden oder Schleifen zwischen den Teilen aufweisen, je nachdem, wo Befestigungspunkte an dem Teil vorhanden sind oder welchen Abstand das Formwerkzeug benötigt. Wenn das Teil geformt, gebördelt oder zu einer Schale gezogen wird, muss sich der Träger möglicherweise seitwärts oder auf und ab bewegen, wenn sich die Form schließt und öffnet.
Wenn sich der Träger beim Formen bewegt, muss er normalerweise gebogen oder gedehnt werden. Unabhängig von der Durchbiegung der Träger besteht ihre Schlüsselfunktion darin, die Teile nahe genug an die nächste Station zu bringen, damit Piloten, Messgeräte und Ortungsgeräte die Teile beim Schließen der Form genau an ihren Platz bringen können.
Wenn der Träger eine dauerhafte Dehnung erfährt, können die Teile zu weit voranschreiten, um in die nächste Station zu passen, oder wenn die Form zwei Träger aufweist, kann ein Träger eine dauerhafte Dehnung ohne Dehnung im anderen Träger entwickeln. Dadurch wird im Streifen eine Kantenwölbung erzeugt, die dazu führt, dass der Streifen nach einer Seite abweicht. Dies führt zu einer schlechten Teilelage.
Ein gedehnter Träger kann durch Einlegen einer Vertiefung in den Träger auf die richtige Länge gekürzt werden. Wenn sich bei einem Mittelträger oder einem einseitigen Träger eine Wölbung entwickelt, kann der Streifen durch Einkerbung oder Einkerbung einer Seite des Trägers begradigt werden. Konstruieren Sie die Grübchen- und Rillstempel so, dass sie für die Position leicht seitlich und für die Tiefe vertikal eingestellt werden können.
Die Kantenwölbung des Materials, wenn es vom Coil geliefert wird, kann dazu führen, dass sich der Streifen in den Lauflehren festsetzt, die das Material während des Vorschubzyklus führen. Diese Bindung kann zum Knicken der Träger führen, was zu kurzen Vorschüben führt. Oft hilft es, die Führungskante der Lehren zwischen den Stationen zu entlasten und die Kontrolle über die Lehren am Arbeitsplatz zu verschärfen.
Eine andere Möglichkeit besteht darin, den Sturz zu beseitigen, indem am Anfang der Form beide Seiten des Materials abgeschnitten werden. Durch Hinzufügen von Anschlägen am Ende dieser Trimmnuten können sie als Pitch-Control-Nuten verwendet werden, um ein Überfahren des Vorschubs zu verhindern.
Optimales Trägerprofil
Das optimale Trägerprofil wird durch einige der folgenden Bedingungen beeinflusst:
Befestigungspunkte zum Teil:
Wenn zwei Träger verwendet werden, versuchen Sie, das Profil und die Länge der Träger in etwa gleich zu halten, damit die Auswirkung der Trägerbiegung nahezu ausgeglichen ist.
Abstand für Stempel- und Matrizenblöcke:
Stanzblöcke, die sich unter dem Schaft erstrecken, oder Matrizenblöcke, die sich über dem Schaft erstrecken, wenn sich die Matrize schließt, erfordern einen Abstand zu den Teilen und den Trägern. Wenn eine Schleife des Trägers Blöcke stört, kann es möglich sein, die Schleife vertikal auszubilden, um einen Freiraum zu schaffen.
Dicke des Materials:
Bei großen Teilen mit dünnem Material sind möglicherweise Versteifungswülste erforderlich, um dem Träger für die Materialzufuhr mehr Festigkeit zu verleihen. Eine weitere Methode zur Versteifung und Bandführung besteht darin, die Kante des Materials zu lanzen und zu bördeln, was auch als Fortschrittskerbe verwendet werden kann.
Die Summe des Streifens: Schwere Teile in langen Formen erfordern mehr Kraft, um den Streifen durch die Form zu drücken. Das Gewicht ist jedoch normalerweise dickes Material und dickes Material ist steifer als dünnes Material. Als Faustregel gelten flexible Träger für
Materialien von 0,020 Zoll bis 0,060 Zoll sind etwa 3/16 Zoll bis 5/16 Zoll breit. Für Materialstärken oberhalb und unterhalb dieses Dickenbereichs Träger
width ist ein "Best Judgement Call".
Abhängig von allen beteiligten Formfaktoren sollten die Träger unter normalen Bedingungen über ihre gesamte Länge eine gleichmäßige Breite aufweisen, insbesondere jedoch im Bereich des Biegens. Da fast jede Materialzuführung Material durch die Form schiebt, anstatt das Material zu ziehen, muss der Träger stark genug sein, um die Teile vollständig durch die Form zu schieben.
Ein Erfassungsschalter, der durch einen vollständigen Vorschub des Streifens am Ausgang der Form betätigt wird, kann ein Knicken erfassen. Wenn die Wirkung der Form während des Schließens oder Öffnens der Presse erfordert, dass sich die Träger biegen, konstruieren Sie den Träger mit Schlaufen, die lang genug sind, um sich zu biegen, ohne zu brechen, aber dennoch stark genug sind, um alle Teile bis zum vollständigen Fortschreiten zu befördern. Wenn zwei flexible Träger nicht stark genug sind, um den Streifen zuzuführen, sollten Sie drei Träger in Betracht ziehen.
Versuchen Sie, die Radien in Flex-Loops so groß wie möglich zu machen. Scharfe Ecken oder kleine Radien konzentrieren die Biegebeanspruchung und machen sie zum ersten Bruchpunkt beim Biegen des Trägers. Vermeiden Sie auch Stufen oder Kerben in den Kanten des Trägers.
Obere Druckpads
Aufgrund der Größe oder Funktion erfordern viele progressive Formen zwei oder mehr Druckkissen in der oberen Form. Jeder erfordert möglicherweise eine andere Verfahrstrecke, um die Arbeit in der einzelnen Formstation auszuführen, wie z. B. Beschneiden oder Formen oder Ziehen.
Die oberen Druckkissen werden jedoch häufig verwendet, um die Materialheber nach unten zu drücken, indem sie gegen die Leiste gedrückt werden, wodurch die Heber nach unten gedrückt werden. In dieser Situation sollten alle Druckstücke, die die Materialheber nach unten drücken, den gleichen Verfahrweg haben. Wenn die oberen Druckkissen unterschiedliche Strecken zurücklegen, wird der Streifen nicht gleichmäßig nach unten gedrückt. Dies kann benachbarte Teile aus der Folge herausziehen, was es schwierig macht, die Teile nach dem Vorschubzyklus in ihrer richtigen Stationsposition zu lokalisieren.
Wenn für das Teil ein Flansch geformt werden muss, muss der Teileträger eine flexible Schlaufe aufweisen, um ein vertikales Atmen des Teils zu ermöglichen, oder einen Druckstempel / ein Druckkissen mit demselben Hub wie die anderen Druckkissen bereitstellen. Die Kraft, die der Druckstempel / das Druckkissen benötigt, muss ausreichen, um die Flansche während des Abwärtshubs auszubilden, während der Stempel / das Druckkissen in der ausgefahrenen Position ist. Dies verhindert, dass der Streifen vertikal atmet, wenn er vom Vorschubniveau auf das normale Arbeitsniveau heruntergedrückt wird.
Wenn der Streifen das Arbeitsniveau erreicht, stoppt der unter Druck stehende Stempel / Block seine Abwärtsbewegung, während die obere Form zum Stanzen, Trimmen, Abwärtsbördeln und für andere Vorgänge weiter abwärts bewegt wird. Federn oder Stickstoffflaschen können für den Druck in diesen Druckstationen verwendet werden. Sie müssen jedoch über eine ausreichende Vorspannkraft verfügen, um die Flansche zu formen und das untere Greifkissen zusammenzuklappen, bevor das obere Stempelkissen zurücktritt.
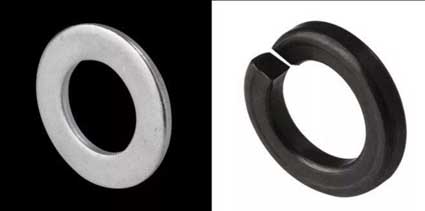
Zuginstanz
Tensile Instance werden erzeugt, wenn das Bandmaterial von einer flachen Ebene in eine zylindrische Form geändert wird. Während des Ziehvorgangs wird der "Durchmesser" des Rohlings auf den "Umfang" der Schale reduziert. Wenn der Umfang während des Materialflusses nach innen verringert wird, geht der äußere Teil des Materials in eine Seiten- oder Kantenkompression über.
Wenn diese Kompression zu groß wird, als dass das Material flach bleiben könnte, beginnt es sich zu falten oder zu knittern. Um dies zu verhindern, kann das Material in einem kontrollierten Spalt zwischen einem Ziehring und einem Druckkissen fließen. Die beiden Hauptursachen für ein Versagen beim Zeichnen einer Schale sind ein Überschreiten des Prozentsatzes, in dem der Durchmesser des Rohlings (oder der Schale) verringert ist, und ein falscher Radius des Ziehrings.
Es gibt eine Grenze dafür, wie weit Metall nach innen fließt, wenn vom Rohlingsdurchmesser zum ersten Ziehdurchmesser und von einem gezogenen Schalendurchmesser zu einem kleineren Schalendurchmesser gezogen wird. Dies wird als Prozentsatz der Ziehungsverringerung ausgedrückt. Der maximale Prozentsatz der Reduktion wird durch den Materialfluss nach innen begrenzt, der bewirkt, dass das Metall komprimiert wird, was wiederum einen Strömungswiderstand verursacht. Zu viel Widerstand führt zu einem Bruch in der Nähe des Deckels der Schale, der den schwächsten Spannungsbereich darstellt.
Der Prozentsatz der Reduktion variiert mit der Metalldicke. Beispielsweise variiert bei einem Tiefziehstahlrohling der Prozentsatz der Verringerung des Durchmessers der ersten Ziehschale von 32 Prozent für 0,015 Zoll. dickes Material auf 48 Prozent für 0,125 Zoll. dickes Material.
Der Ziehring hat einen minimalen und einen maximalen Ziehradius, die den Materialfluss steuern. Beim Tiefziehen von Stahlteilen variiert der richtige Radius zwischen 5 und 32 Zoll. Minimum bis 1/4 Zoll Maximum für 0,015 Zoll. Lager und 11/32-in. Minimum bis 15/32 Zoll Maximum für 0,125 Zoll. Stock.
Wenn der Radius zu klein ist, fließt das Metall nicht gut, was den Strömungswiderstand erhöht und zu übermäßiger Ausdünnung oder Brüchen in der Nähe des Becherkopfs führt. Wenn der Radius zu groß ist, knittert das Metall, nachdem es die Klemmstelle zwischen dem Ziehring und dem Druckkissen verlassen hat und bevor es in die vertikale Wand des Bechers geformt wird.
Die normale Tendenz besteht darin, den Radius zu klein zu machen, weil "es einfach ist, den Radius während des Probierens zu vergrößern und es schwierig ist, einen kleineren Radius zu machen". Das Ergebnis ist, dass die Tasse unnötig belastet wird, was zu übermäßiger Ausdünnung oder Brüchen führt. Das Problem eines ungenauen Prozentsatzes der Verkleinerung oder eines ungenauen Ziehradius in der ersten Ziehstation tritt häufig nicht in der ersten Ziehstation, sondern in einer späteren Nachziehstation auf, so dass viel Zeit für die Suche nach der falschen Station aufgewendet wird .
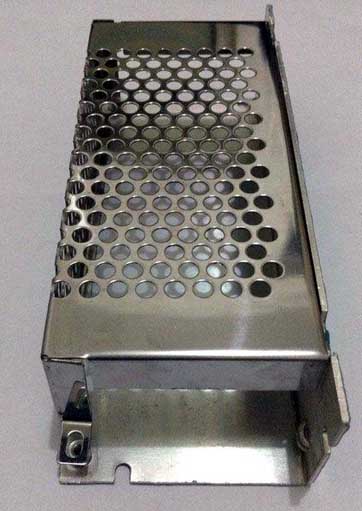