Schweissen von Aluminium und Aluminiumlegierungen
■ Analyse Materialanalyse
Reines industrielles Aluminium hat die allgemeinen Eigenschaften von Aluminium, niedrige Dichte, gute elektrische und thermische Leitfähigkeit, gute Antikorrosionsleistung, gute Plastikverarbeitungsleistung, kann in Platten, Streifen, Folien und Extrusionsprodukte, etc. verarbeitet werden, kann Gasschweißen sein , Argon-Lichtbogenschweißen, Punktschweißen. Industriereines Aluminium kann nicht wärmegefestigt werden, kann die Festigkeit durch Kaltverformung erhöhen, die einzige Wärmebehandlungsform ist Glühen, die Anfangstemperatur der Rekristallisation ist mit dem Gehalt an Verunreinigungen und dem Grad der Verformung verbunden und beträgt im Allgemeinen etwa 200 ° C . Die geglühte Folie hat σb = 80 bis 100 MPa, σ0,2 = 30 bis 50 MPa, ζ = 35% bis 40% und HB = 25 bis 30. Nach 60% bis 80% Kaltverformung kann, obwohl sie erhöht werden kann 150 bis 180 MPa sinkt die Enthalpie auf 1% bis 1,5%. Eine Erhöhung des Gehalts an Eisen- und Siliziumverunreinigungen kann die Festigkeit erhöhen, aber die Plastizität, elektrische Leitfähigkeit und Korrosionsbeständigkeit verringern.
Das Folgende ist die chemische Zusammensetzung des Ausgangsmaterials
Tabelle 2-1 Chemische Zusammensetzung des Grundmaterials (L2) (GB / T3190-1996)
■ Analyse der Schweißbarkeit von Aluminium
I. Analyse der physikalischen und chemischen Eigenschaften
Der Schmelzpunkt von reinem Aluminium ist niedrig (660 ° C). Beim Schmelzen ändert sich die Farbe nicht, es ist schwierig, das Schmelzbad zu beobachten, und es ist leicht, während des Schweißens zusammenzubrechen und durchzubrennen. Die Wärmeleitfähigkeit ist dreimal so hoch wie bei kohlenstoffarmem Stahl, die Wärmeabfuhr ist schnell und es ist nicht einfach, beim Schweißen zu schmelzen. Der lineare Ausdehnungskoeffizient ist doppelt so groß wie der von kohlenstoffarmem Stahl und wird beim Schweißen leicht verformt. Es wird leicht zu einem dichten, hochschmelzenden Oxidfilm Al 2 O 3 (Schmelzpunkt 2050 ° C) an der Luft oxidiert. Es ist infusibel und nicht leitend. Es kann zu nicht geschmolzenem Schlackeneinschluss und instabilem Schweißen während des Schweißens führen. Daher ist die Schweißbarkeit von reinem Aluminium schlechter als die von kohlenstoffarmem Stahl. Daher umfassen die Schweißeigenschaften von reinem Aluminium hauptsächlich: leichte Oxidation während des Schweißprozesses, hoher Energieverbrauch, einfache Erzeugung von Poren (hauptsächlich Wasserstoffgasporen), leichte Bildung von Heißrissen beim Schweißen, leichtes Erweichen von Schweißverbindungen, Schweißverbindungen reduzierte Korrosionsbeständigkeit.
1, einfache Oxidation
Aluminium 1060 und Sauerstoffaffinität ist sehr groß, bei Raumtemperatur, Aluminium leicht zusammen oxidiert, die Bildung eines dichten Al2O3 Film auf der Oberfläche von Aluminium, kann die fortgesetzte Oxidation von Metall verhindern, ist vorteilhaft für die natürliche Korrosionsschutz, aber es hat Schwierigkeiten beim Schweißen gebracht. Dies liegt an dem hohen Schmelzpunkt des Aluminiumoxidfilms (etwa 2050ºC), der weit über dem Schmelzpunkt des Aluminiums 1060 liegt, und an der hohen Dichte von 3,95 bis 4,10 g / m², die etwa dem 1,4-fachen des Aluminiums entspricht 1060, plus eine sehr hohe Wärmeleitfähigkeit von 1060. Schweißen Es ist leicht, Nicht-Fusionsphänomene zu verursachen, und es ist auch wahrscheinlich, dass es zu Einschlüssen von Schweißmetall wird und Schlackeneinschlussdefekte bildet. Gleichzeitig kann der Oxidfilm mehr Feuchtigkeit absorbieren, während das Schweißen dazu führt, dass die Schweißnaht Poren erzeugt.
2, einfach Luftloch zu produzieren
Da Aluminium 1060 keinen Kohlenstoff enthält, gibt es keine Bedingung für die Bildung von CO-Luftlöchern, und Stickstoff ist in Aluminium unlöslich, so dass allgemein angenommen wird, dass der Hauptgrund für die Erzeugung von Luftlöchern durch Aluminium 1060 Wasserstoff ist. Wasserstoff ist in flüssigem Aluminium weitgehend löslich und in festem Aluminium nahezu unlöslich. Bei hohen Schweißtemperaturen nimmt die Löslichkeit von Wasserstoff in flüssigem Aluminium stark ab. Wenn sich das Badmetall in übersättigtem Wasserstoff löst, fällt übersättigter Wasserstoff aus dem flüssigen Metall aus und bildet mit einer bestimmten Abkühlgeschwindigkeit winzige Blasen. Die Ausscheidung von Wasserstoff beim Erstarrungsprozess von Aluminiumschmelzen bildet einerseits neue, kleine, kleine Bläschen und dehnt sich andererseits in bereits gebildete winzige Bläschen aus und wächst. Gleichzeitig schwebt die Blase aufgrund der geringen relativen Dichte von Aluminium 1060 langsam. Wenn die Abkühlgeschwindigkeit höher ist, entweichen die Blasen nicht aus dem Schmelzbad und hinterlassen nach dem Erstarren das Luftloch in der Schweißnaht. Wenn der Erstarrungsprozess des Schmelzbades relativ langsam ist, wird genug Zeit dafür sein, dass die Wasserstoffblasen aus dem Schmelzbad entweichen und kein Luftloch in der Schweißnaht gebildet wird. Wenn andererseits die Erstarrungsgeschwindigkeit des geschmolzenen Pools sehr schnell ist, kann Wasserstoff nicht aus dem flüssigen Metall ausgefällt werden, sondern die übersättigte feste Lösung wird in dem geschmolzenen Aluminium gebildet, und das Gas wird nicht ausgefällt, um ein Luftloch zu bilden . Es ist ersichtlich, dass die Abkühlrate eine der wichtigen Bedingungen ist, die die Erzeugung von Luftlöchern beeinflussen.
3, Schweißen heißer Sprung
Aluminium 1060 nicht wärmehärtende Legierungen erzeugen selten Risse während des Schmelzschweißens. Risse können nur auftreten, wenn der Verunreinigungsgehalt den spezifizierten Bereich überschreitet oder wenn die Steifigkeit hoch ist. Die Ursache der thermischen Rissbildung in Aluminium 1060 hängt mit seiner Zusammensetzung und Schweißspannung zusammen. Da Aluminium 1060 einen linearen Ausdehnungskoeffizienten hat, der fast das Doppelte von Eisen ist, und seine Erstarrungsschrumpfung doppelt so groß ist wie die von Eisen, ist die Schweißspannung der Aluminiumschweißverbindung groß.
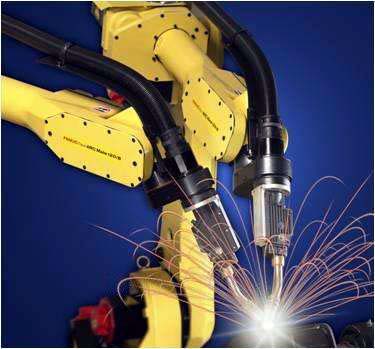
4, hohe Wärmeleitfähigkeit und Leitfähigkeit
Die Wärmeleitfähigkeit von Aluminium 1060 ist sehr groß, etwa viermal so hoch wie die von Stahl, und seine Wärmekapazität ist fast doppelt so hoch wie die von Stahl. Daher verbraucht das Schweißen von Aluminium 1060 mehr Wärme als Stahl. Um hochwertige Schweißverbindungen zu erhalten, ist es notwendig, eine Wärmequelle mit konzentrierter Energie und großer Leistung zu verwenden, um ein normales Schweißen durchzuführen, insbesondere wenn die Werkstückdicke groß ist. Aluminium 1060 hat eine gute elektrische Leitfähigkeit, und Widerstandsschweißen erfordert mehr Leistung.
5, hohe Temperatur macht die Stärke und die Plastizität niedrig
Die Stärke und Plastizität von Aluminium 1060 bei hohen Temperaturen ist sehr gering, wie 370 ° C Stärke ist nur etwa 1 MPa, kann oft nicht das Gewicht der flüssigen Pool, Zerstörung der Bildung von Schweißgut, manchmal auch den Zusammenbruch der Metall schweißen und durchbrennen.
6, keine Farbänderung
Wenn Aluminium 1060 von fest zu flüssig wechselt, gibt es keine offensichtliche Farbänderung, so dass es nicht einfach ist, die Temperatur des Bades zu beurteilen. Wenn die Temperatur ansteigt, nimmt außerdem die Festigkeit von Aluminium 1060 ab. Daher ist es schwierig, die Erwärmungstemperatur während des Schweißens zu erfassen, und es ist oft nicht möglich, den Durchbrand aufgrund einer zu hohen Temperatur wahrzunehmen.
Im Allgemeinen hat Aluminium 1060 eine gute Schweißbarkeit. Solange die obigen Schweißeigenschaften richtig gewählt sind, können das Schweißverfahren, das Schweißmaterial, das Vorschweißreinigungs- und Schweißvorgangsprozeß geeignet verwendet werden, um eine gute Schweißverbindung zu erhalten.
Die Dicke des Mantels beträgt 16 mm. Vor dem Schweißen sollte es zur Vermeidung von Heißrissen mit einer Vorwärmtemperatur von 120-140 ° C vorgewärmt werden.
(2) Unsachgemäße Schweißverfahren
Wenn zum Beispiel die Energie der Unterpulver-Schweißlinie groß ist, wird eine grobe Kornstruktur in der Wärmeeinflusszone der durch die Schweißwärme beeinflussten Zone auftreten, und die Zähigkeit der Wärmeeinflusszone wird reduziert. Die Energie des Elektroschlackeschweißens ist sogar größer als die des Unterpulverschweißens. Die Körner in der Wärmeeinflusszone sind gröber und die Zähigkeit ist deutlicher reduziert. Daher werden die Körner nach dem automatischen Argon-Lichtbogenschweißen von reinem Aluminium üblicherweise durch Normalisieren verfeinert, um die Zähigkeit zu verbessern.
Schweißprozess-Plan
Die Schweißanlage ist eine MIG-Schutzgasschweißmaschine NB-500 mit einem Stromregelbereich von 50 bis 500A. Der Durchmesser des Schweißdrahtes ist Φ1,6mm und das Schutzgas, Argon, hat eine Reinheit von nicht weniger als 99,96%. Der Grund für seine Wahl ist wie folgt:
(1) Neben dem CO2-Schutzgasschweißen können nahezu alle Schweißverfahren zum Schweißen von Aluminium und Aluminiumlegierungen verwendet werden, aber Aluminium und Aluminiumlegierungen sind für verschiedene Schweißverfahren unterschiedlich geeignet, und verschiedene Schweißverfahren haben ihre eigenen Anwendungen.
Gasschweißen und Elektroden-Lichtbogenschweißverfahren sind einfach und leicht zu bedienen. Gasschweißen kann verwendet werden, um das Schweißen von dünnen Aluminiumplatten und Gussstücken, die keine hohe Schweißqualität erfordern, zu reparieren. Schweißelektroden-Lichtbogenschweißen kann zum Schweißen von Aluminiumlegierungsgussteilen verwendet werden. Schutzgasschweißen ist TIG-Schweißen und MIG-Schweißen, sie sind die am häufigsten verwendeten Aluminium-und Aluminium-Legierung Schweißverfahren. Von der "Kathodenreinigungs" -Rolle und dem Wolfram-Maximalstrom wird im Allgemeinen Wolfram-Lichtbogenschweißen verwendet. Da es unter dem guten Schutz des Argonschweißens steht, kann das Schmelzbad vor Sauerstoff, Wasserstoff und anderen schädlichen Gasen geschützt werden. Der Argon-Lichtbogenschweißstrom ist stabil, die Wärme ist konzentriert, das Schweißgewebe ist kompakt, das Aussehen ist schön, die Festigkeit und die Plastizität sind hoch und die Verformung des Werkstücks ist gering.
Aufgrund des begrenzten Stroms von Wolfram ist jedoch die Eindringkraft des Lichtbogens gering und die Produktivität ist gering. Daher wird es im Allgemeinen zum Schweißen dünner Platten mit einer Dicke von 6 mm oder weniger verwendet.
MIG-Lichtbogenleistung, Wärmekonzentration, Wärmeeinflusszone ist klein, die Produktivität kann mehr als dreimal höher sein als beim WIG-Schweißen. Daher ist es für das Schweißen von dicken Plattenstrukturen geeignet. Es kann Aluminium- und Aluminiumlegierungsplatten unter 50 mm schweißen. Das Schweißen von 30 mm dicken Aluminiumplatten kann ohne Vorwärmung erfolgen. Das halbautomatische MIG-Schweißen wird hauptsächlich für das Heftschweißen, intermittierende kleine Schweißnähte und das Schweißen von unregelmäßig geformten Werkstücken verwendet.
(2) Die Wärmeleitfähigkeit und die spezifische Wärmekapazität von Aluminium und seinen Legierungen sind mehr als zweimal niedriger als die von Kohlenstoffstahl und niedrig legiertem Stahl. Die Wärmeleitfähigkeit von Aluminium ist mehr als zehnmal höher als die von austenitischem Edelstahl. Im Schweißprozess wird eine große Menge an Wärmeenergie schnell auf das Innere des Matrixmetalls übertragen. Daher wird beim Schweißen von Aluminium und Aluminiumlegierungen die Energie in der Metallschmelze verbraucht, und in anderen Metallteilen wird mehr Wärme verbraucht.
Diese Art von nutzlosem Energieverbrauch ist wichtiger als Stahlschweißen. Um qualitativ hochwertige Schweißverbindungen zu erhalten, sollte es möglich sein, energiekonzentrierte Hochleistungsenergien sowie Vorwärm- und andere technologische Maßnahmen zu verwenden.
MIG-Schweißen im Vergleich mit WIG-Schweißen, MIG-Schweißen der minimalen Heizfläche von 10-4 cm2, die maximale Leistungsdichte von 104 ~ 105W • cm-2, Die minimale Heizfläche von WIG-Schweißen ist 10-3cm2, und die maximale Leistungsdichte ist 1,5-104 W • cm-2. Daher ist es besser, MIG-Schweißen zu verwenden.
(3) Auswahl des Schweißdrahts aus Aluminium und Aluminiumlegierungen Neben der Berücksichtigung einer guten Schweißprozessleistung sollten die Zugfestigkeit und die Plastizität (durch Biegeprüfung) der Stoßverbindung die spezifizierten Anforderungen gemäß den Anforderungen des Behälters erfüllen. Bei Schiffen mit Korrosionsbeständigkeitsanforderungen sollte die Korrosionsbeständigkeit der Schweißverbindungen ebenfalls bei oder nahe bei der des Grundmetalls liegen. Daher basiert die Auswahl des Schweißdrahtes hauptsächlich auf den folgenden Prinzipien:
1. Die Reinheit von reinem Aluminium Schweißdraht ist in der Regel nicht niedriger als die des Grundmetalls;
2. Die chemische Zusammensetzung des Aluminiumlegierungs-Schweißdrahts entspricht im Allgemeinen dem Grundmetall oder ist diesem ähnlich;
3. Der Gehalt an korrosionsbeständigen Elementen (Magnesium, Mangan, Silizium usw.) in Aluminiumlegierungs-Schweißdrähten ist im Allgemeinen nicht niedriger als der von Grundmetall;
4. Wenn das unähnliche Aluminium geschweißt wird, sollte der Schweißdraht entsprechend dem Grundmaterial mit hoher Korrosionsbeständigkeit und hoher Festigkeit ausgewählt werden;
5. Hochfeste Aluminiumlegierungen, die keine Korrosionsbeständigkeit erfordern (wärmebehandelte verstärkte Aluminiumlegierungen), können unterschiedliche Legierungsdrähte, wie z. B. SAlSi-1, verwenden, die eine gute Rissbeständigkeit aufweisen und eine geringere Festigkeit als das Basismetall aufweisen können.
Entsprechend der Verwendung von Aluminium-Lagertanks, in Übereinstimmung mit den oben genannten Prinzipien (gleiche Stärke, etc.), wird der Draht jetzt als SAl-2 gewählt, dessen Aluminiumgehalt ist höher als 1060 (L2) industriell reines Aluminium, um Gewährleistung der Korrosionsbeständigkeit von Schweißverbindungen. .
(4) Schutzgasauswahl
Aluminium und Aluminiumlegierung MIG-Schweißen, nur mit Inertgas Argon oder Helium, wird kein reaktives Gas verwendet. Obwohl Argon oder Helium ein Schutzgas ist, sind seine physikalischen Eigenschaften unterschiedlich und daher ist seine Prozessleistung ebenfalls unterschiedlich. Die Dichte von Argon ist etwa 1,4 mal so hoch wie die von Luft, schwerer als Luft; Die Dichte von Helium ist etwa 0,14 mal so hoch wie die von Luft, leichter als Luft. Beim Schweißen in der flachen Schweißposition sinkt das Argongas und treibt die Luft weg. Dies schützt den Lichtbogen und deckt die Schweißzone ab. Wenn Heliumgasschutz gewählt wird, wird die gleiche Schutzwirkung erhalten. Die Strömung und der Verbrauch von Heliumgas ist etwa 2 bis 3 mal höher als die von Argongas.
Außerdem ist die Wärmeleitfähigkeit von Helium höher als die von Argon, und ein Lichtbogenplasma mit einer gleichmäßigeren Energieverteilung kann erzeugt werden. Das Argon-Lichtbogenplasma hat eine hohe Zentrumsenergie der Lichtbogensäule und seine periphere Energie ist niedrig. Daher ist die Form der Schweißnaht während des Xenon-Lichtbogen-MIG-Schweißens durch ein tiefes Eindringen und ein weites Schmelzen gekennzeichnet, und der Boden der Schweißnaht ist ein Kreisbogen. Die Mitte der Schweißnaht des Argon-MIG-Schweißens hat jedoch eine schmale und tiefe "fingerähnliche" Durchdringung mit einer flacheren Penetration auf beiden Seiten.
Das Ionisationspotential von Helium ist höher als das von Argon. Wenn die Lichtbogenlänge und der Schweißstrom konstant sind, ist die Lichtbogenspannung des Heliumgasschutzes höher als die des Argonlichtbogens. Bei reinem Helium-Schutz-MIG-Schweißen ist es somit schwierig, einen axialen Strahlübergang zu erreichen, häufig treten Spritzer und rauhe Schweißflächen auf. Argon-geschütztes MIG-Schweißen ist leichter zu erreichen Jet-Übergang.
Aufgrund der niedrigen Lichtbogenspannung und der niedrigen Lichtbogenenergiedichte des MIG-Argon-Lichtbogenschweißens ist der Lichtbogen stabil und hat nur wenige Spritzer, so dass er für das Schweißen dünner Teile geeignet ist. MIG-Xenon-Lichtbogenschweißen hat eine hohe Energiedichte und eignet sich zum Schweißen dicker Teile, aber der Lichtbogen ist nicht stabil genug und Helium ist teuer.
Die maximale Wandstärke dieses Produkts beträgt 16 mm. Verwenden Sie daher Argon als Schutzgas.
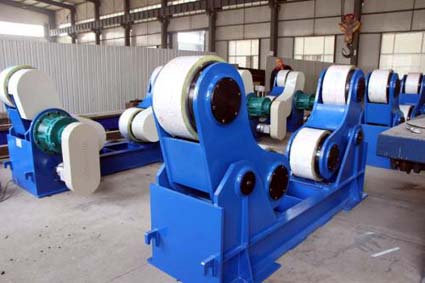
3. Vorbereitung vor dem Schweißen
(1) Nutform, Fugenform und -größe
Nutform, Fugenform und -größe hängen von der Dicke der Aluminiumschweißung, der Schweißposition, der Tröpfchentransferform und dem Schweißprozess ab.
Wenn Schweißnahtdicke, Schweißposition und Schweißprozess festgelegt sind, ist die Form der Tropfenübertragung eine wichtige Voraussetzung für die Bestimmung der Form der Parameter Nut und Schweißprozess.
Die Form der Tropfenübertragung beim MIG-Schweißen und die Stabilität des Prozesses sind der Schlüssel für die Eignung des MIG-Schweißverfahrens. Wenn der Schweißstrom von klein auf groß ansteigt, wechselt der Tröpfchenübergang vom kurzschlußartigen Übergang zum tropfenförmigen Übergang zum Einspritzübergang (Schießtröpfchenübergang, Strahlübergangsrichtung). Der Kurzschlussübergang gilt nur für das MIG-Schweißen von dünnwandigen Teilen mit einer Materialstärke von 1 bis 2 mm. Der Einspritzübergangsprozess ist relativ stabil und kann zum MIG-Schweißen von Aluminiummaterialien mit unterschiedlicher Dicke verwendet werden. Zwischen dem Kurzschlussübergang und dem Jet-Übergang gibt es eine Sub-Jet-Übergangszone, in der trotz der kurzen Lichtbogenlänge kein Kurzschluss auftritt. Selbst wenn sich die Lichtbogenlänge ändert, können Strom und Spannung unverändert bleiben. Selbst bei einer konstanten Stromquelle (tiefe externe Tropfeneigenschaften) kann der Lichtbogen selbstregulierend sein, der Schweißprozess ist stabil und die Schweißnaht ist gleichmäßig und schön geformt. Die Praxis zeigt, dass beim MIG-Schweißen von Aluminium mit Subjet-Übergang die Schweißleistung höher und die Schweißqualität besser ist. MIG-Schweißen, die allgemeine Verwendung von DC-Reverse-Verbindung, verwenden Sie nicht DC positiv oder AC, automatisches Schweißen und halbautomatisches Schweißen zwei Möglichkeiten.
Einsatz in Form von Jet-Übergang, die Übergangszeit der Injektion, enge und tiefe Schweißnaht leicht präsentiert Finger Penetration, beide Seiten der schlechten Penetration, Porosität Risse und andere Mängel schweißen. Wenn Subjet-Übergänge verwendet werden, ist die Lichtbogenlänge kürzer, die Lichtbogenspannung ist niedriger, der Lichtbogen wird leicht detoniert und die Tröpfchen am Ende des Drahtes wachsen so groß wie der Durchmesser des Drahtes, wenn er zum Schmelzbad übergeht entlang der Achse. Während dieser Zeit kann ein kurzzeitiger Kurzschluss auftreten. Beim Sub-Jet-Übergang-MIG-Schweißen ist die Kathodenzerstäubungsfläche groß, der Badschutzeffekt ist gut, die Schweißnaht ist gut ausgebildet und die Schweißnahtdefekte sind klein. Aus diesem Grund sollten Aluminium-Lagertanks die oben genannten Probleme bei der Auswahl der Schweißparameter und des Nutdesigns vollständig berücksichtigen.
(2) Reinigung vor dem Schweißen
Der Oxidfilm und Verunreinigungen auf der Oberfläche der Aluminiumschweißung und des Drahtes können dazu führen, dass sich die statische Krümmung des Lichtbogens während des MIG-Schweißprozesses nach unten bewegt. Als Ergebnis steigt der Schweißstrom plötzlich an, die Schmelzgeschwindigkeit des Drahtes steigt an und der Lichtbogen verlängert sich.
An diesem Punkt änderte sich auch der Klang des Bogens von dem rhythmischen Summen zu dem harten Rufen. Daher sollten MIG-Schweißteile und Drahtoberflächen streng gereinigt werden, wobei die Qualität der Reinigung direkt die Qualität der Schweißprozesse und -verbindungen beeinflusst, wie zum Beispiel die Tendenz der Schweißnahtporosität und der mechanischen Eigenschaften. MIG-Schweißen von Schweißnähten und Drahtoberflächenreinigung, oft mit chemischen Reinigungs- und mechanischen Reinigungsmethoden. Zur gleichen Zeit, Aluminium-und Aluminiumlegierung Schweißdraht ist am besten zu verwenden, eine glatte, glatte, helle "Trilight" Schweißdraht mit speziellen Oberflächenbehandlung.
1. Chemische Reinigung
Hohe chemische Reinigungseffizienz, stabile Qualität, geeignet für sauberen Schweißdraht und kleine Abmessungen, Serienfertigung von Werkstücken. Verfügbare Dip-Methode und Scrub-Methode zwei. Man kann Aceton, Benzin, Kerosin und andere organische Lösungsmittel auf die Oberfläche des Öls verwenden, bei 40 ° C ~ 70 ° C 5% ~ 10% NaOH-Lösung alkalisch waschen 3min ~ 7min (etwas länger, aber nicht mehr als 20min reines Aluminium ), mit Wasser gespült, dann mit 30% HNO3-Lösung bei Raumtemperatur bis 60 ° C für 1 Minute bis 3 Minuten gebeizt, mit fließendem Wasser gespült, an der Luft getrocknet oder bei niedriger Temperatur getrocknet.
2. mechanische Reinigung
Mechanische Reinigung wird oft verwendet, wenn das Werkstück eine große Größe, einen langen Produktionszyklus, mehrschichtiges Schweißen oder chemische Reinigung aufweist. Verwenden Sie zuerst Aceton, Benzin und andere organische Lösungsmittel, um die Oberfläche abzuwischen, um Öl zu entfernen. Verwenden Sie dann direkt eine Kupferdrahtbürste mit einem Durchmesser von 0,15 mm bis 0,20 mm oder eine Edelstahldrahtbürste, bis der Metallglanz freiliegt. Im Allgemeinen ist es nicht geeignet, mit einer Schleifscheibe oder gewöhnlichem Sandpapier zu schleifen, um zu vermeiden, dass die Sandpartikel auf der Metalloberfläche verbleiben, und die Defekte, wie Schlackeneinschluss, werden beim Schweißen erzeugt. Zusätzlich kann die zu schweißende Oberfläche mit einem Spatel, einer Feile oder dergleichen gereinigt werden.
Nachdem das Werkstück und der Schweißdraht gereinigt und gereinigt wurden, wird während der Lagerung ein Oxidfilm regeneriert. Insbesondere in feuchter Umgebung wächst der Oxidfilm in einer Umgebung, die durch Säuren, Alkalien und andere Dämpfe verunreinigt ist, schneller. Daher sollte nach dem Reinigen und Reinigen von Werkstücken und Schweißdraht die Lagerzeit vor dem Schweißen so weit wie möglich verkürzt werden. In feuchten Klimazonen sollte das Schweißen in der Regel innerhalb von 4 Stunden nach der Reinigung durchgeführt werden. Nach der Reinigung, wenn die Lagerzeit zu lang ist (wie mehr als 24 Stunden) sollte erneut behandelt werden.
Der Reinigungsplan dieser Tanks ist:
Oxide und andere Verunreinigungen innerhalb von 50 mm von der Nut und deren Umfang sollten gereinigt werden. Verwenden Sie zuerst ein Edelstahldrahtrad mit einem Durchmesser von weniger als 0,2 mm zum Reinigen und dann zur chemischen Reinigung. Schweißdraht wird nur chemisch gereinigt. Die gereinigte Nut sollte innerhalb von 2 Stunden geschweißt werden, und der freiliegende Draht in der Atmosphäre nach dem Waschen und Trocknen sollte nicht länger als 4 Stunden sein.
Die chemischen Reinigungsparameter von Aluminiumtanks sind in Tabelle 1 gezeigt:
4. Vorbereitung der Prozessausrüstung
Die für das MIG-Schweißen erforderliche Prozessausrüstung umfasst Schweißwagen und -schienen, Manipulatoren, Positionierer, Rollenträger und Klemmen für Schweißungen. Die Hauptschweißnähte für Aluminium-Lagertanks sind einseitige und einlagige Schweißnähte mit V-Nut. Um eine Penetration sicherzustellen und ein Auslaufen von Metall in das Schmelzbad zu verhindern, wird ein Verfahren zum Hinzufügen einer Rückseiten-Flachdichtung angewendet. Hier nur die Hauptwerkzeugauswahl.
(1) Zwischenlagen
MIG-Schweißen, wie TIG-Schweißen, erfordert manchmal eine Rückseitenschweißung, da die MIG-Schweißleistung größer ist, die Durchdringungsfähigkeit ist stärker. Das Rückenpolster ist nicht nur vorteilhaft, um ein Auslaufen von Metall im Bad zu verhindern, sondern hilft auch, die Größe der Verbindung zu reduzieren . Die Betriebsbedingungen sind entspannter, und die Anforderungen an das Betriebsverhalten können angemessen reduziert werden. Die Längs- und Umfangsschweißnähte des Aluminiumlagers bestehen alle aus temporären Pads und das Material ist das gleiche wie das Basismetall, das nicht nur das Schmelzbad verschmutzen, sondern auch die Wärmeableitung erleichtern kann. Die Rückdichtung ist in der Reifenbefestigung der Schweißkonstruktion installiert, entspricht der Schweißnahtposition und ist fest an den gegenüberliegenden Seiten der beiden Teile angebracht. Nach dem Schweißen wird es von der Schweißkonstruktion getrennt.
(2) Rollenwagen
Der Rollenwagen ist eine häufig verwendete Prozessausrüstung für die Herstellung von Druckbehältern. Der Schweißwalzenrahmen treibt die Walze durch den Motor und nutzt die Reibung zwischen der Antriebsrolle und dem Schweißstück, um die Verdrängungsmaschine anzutreiben, die das rohrförmige Schweißstück mit einer bestimmten Geschwindigkeit dreht. Der Schweißrollenrahmen, der bei der Schweißproduktion verwendet wird, besteht normalerweise aus einem Paar aktiver Rollenrahmen und einem Paar passiver Rollenrahmen.
Der Schweißwalzenrahmen wird hauptsächlich für die Montage und das Schweißen von zylindrischen Fässern verwendet. Wenn das rohrförmige Umfangsschweißen durchgeführt wird, wird, da sich der Zylinder auf der Walze dreht, das Allpositionsschweißen der ringförmigen Schweißnaht zu flachem Schweißen geändert, was zur Verbesserung der Qualität der Schweißnaht und der Schweißproduktivität günstig ist. Wenn die Installationshöhen des aktiven Rollenhalters und des passiven Rollenhalters unterschiedlich sind, kann auch die Montage und das Verschweißen des Konus und des Zylinderschweißteils mit ungleichem Durchmesser durchgeführt werden. Für rechteckige Schweißteile und unregelmäßig geformte Schweißteile können sie in speziellen Ringklemmen oder auf Rollenwagen montiert werden.
Schweißwalzenrahmen kann unterteilt werden in:
Universal-Schweißrollenrahmen und Spezial-Schweißrollenrahmen werden jetzt universell eingesetzt. Die am häufigsten verwendeten universellen Schweißrollenwagen in der industriellen Produktion lassen sich in zwei Kategorien einteilen: Einer ist ein sich selbst einstellender Schweißwalzenrahmen und der andere ist ein einstellbarer Schweißwalzenrahmen.
Die Charakteristik des selbsteinstellenden Schweißwalzenrahmens besteht darin, dass jeder Walzenrahmen aus zwei Sätzen von Doppelwalzen besteht. Jede Gruppe von Rollenhaltern kann sich zentriert an ihrem Drehpunkt drehen, so dass sie sich an verschiedene Durchmesser von Schweißungen über einen relativ großen Bereich anpassen kann, ohne den Abstand zwischen den beiden Rollensätzen zu ändern. Beim Schweißen von Schweißverbindungen mit kleinem Durchmesser kann der äußere Kreis der Schweißverbindung jedoch nur in Kontakt mit den zwei Rollen jedes Paares von Rollenrahmen stehen, und die Belastbarkeit des Rollenrahmens wird entsprechend auf 75% der Nennlast reduziert .
Der selbsteinstellende Schweißwalzenrahmen nimmt normalerweise den Doppelantriebsübertragungsmodus an. Der Motor überträgt das Drehmoment auf die beiden Sätze von Rollen durch das sekundäre Reduzierstück und die Verbindungswelle, um eine sanfte Rotationsgeschwindigkeit zu erreichen. Der Antriebsmotor kann eine elektromagnetische stufenlose Geschwindigkeitsregelung oder eine stufenlose Geschwindigkeitsregelung des Wechselrichters verwenden.
Die Eigenschaft des einstellbaren Schweißwalzenrahmens besteht darin, dass der Abstand zwischen den Walzen jedes Walzenrahmens einstellbar ist, um sich an Schweißstücke mit unterschiedlichem Durchmesser anzupassen. Der Walzenabstand kann durch verschiedene Verfahren eingestellt werden. Die einfachste Methode besteht darin, zwei Reihen von Bolzenlöchern mit demselben Lochabstand auf der Oberfläche des Rollenlagers zu bohren. Der Rollensitz wird in die entsprechende Lochposition entsprechend dem Durchmesser der Schweißkonstruktion eingebaut. Schraube fixiert. Wenn sich der Durchmesser des zu schweißenden Werkstücks ständig ändert, kann die Spindelsteigung über die Spindelsteigung eingestellt werden. Für das Anwendungsgebiet mit einer kleinen Auswahl von Schweißdurchmessern kann der Verbindungsmechanismus verwendet werden, um den Radabstand einzustellen, was sehr einfach ist und zusätzliche Zeit spart.
Der einstellbare Schweißrollenrahmen verwendet normalerweise ein Paar von aktiven Rollenrahmen und ein Paar von passiven Rollenrahmen, um Montage- und Schweißvorgänge durchzuführen. Der aktive Rollenwagen kann in Einzelantrieb und Doppelantrieb unterteilt werden. Beide Motoren können synchron über elektronische Schaltungen gestartet werden. Der Vorteil des Doppelantriebs besteht darin, dass die Schweißkonstruktion reibungslos rotiert und das Prellen verhindert. China hat den Industriestandard JB / T9187-1999 für das Schweißen von Rollenwagen entwickelt. Unter dem Gesichtspunkt der Sicherheit und unter Berücksichtigung der vernünftigen Wahl der Radantriebsleistung legt der Industriestandard JB / T9187 auch fest, dass der Umschlingungswinkel α der Mitte des Rades zur Mitte der Schweißkonstruktion innerhalb des Bereichs von 45 ° bis 110 °. In der eigentlichen Schweißproduktion ist das Auswahlverfahren für den Schweißwalzenrahmen wie folgt:
1. Gemäß Spezifikation und Gewicht der Schweißkonstruktion, die im Produktionsprogramm der Fabrik angegeben ist, und der monatlichen Produktionskapazität werden die Spezifikationen des Schweißwalzenrahmens, die Nennlastkapazität und die zu bestückende Menge vorläufig bestimmt.
2. Die Struktur der Walze wird nach dem Gewicht der Schweißkonstruktion und der Art des Materials bestimmt. Für Druckbehälter aus Edelstahl, Titanlegierung und Aluminiumlegierung müssen Gummi- oder Polyurethanräder verwendet werden.
3. Bestimmen Sie nach der anzuwendenden Schweißverfahrensmethode die Anforderungen für den Drehzahlbereich des Schweißwalzenrahmens und andere technische Eigenschaften.
4. Entsprechend den Qualitätsanforderungen der Schweißnaht sollte die Regelgenauigkeit der Walzenbahngeschwindigkeit des Schweißwalzenrahmens vorgeschlagen werden.
5. sollte die Arbeitsumgebung berücksichtigen.
In Anbetracht der Vielseitigkeit, nimmt der Aluminium-Speichertank den einstellbaren Schweißwalzenrahmen des Typs EB-10TN an, seine technischen Parameter sind:
Maximale Last 5t, maximale Rotationskapazität 10t, Rollenbahngeschwindigkeit 70-1200mm / min,
Werkstückdurchmesser 150-4000 mm, Anzahl der Gummiräder 6, Achsabstand zwischen den Rädern 410 bis 1810,
Abmessungen: Antriebsrad 3300 × 890, angetriebenes Rad 2600 × 500 × 515, Rollendurchmesser (Gummirad 350),
Gewicht: Antriebsrad 600, passives Rad 400.
(3) Schweißmanipulator
Schweißgerät, auch Schweißgerätesteuerung genannt, liefert präzise den Schweißkopf und hält ihn in der Position, in der er geschweißt werden soll. Oder bei der ausgewählten Schweißgeschwindigkeit wird der Schweißkopf entlang der spezifizierten Bewegungsbahn bewegt, und die Schweißkopfverdrängungsmaschine, die den Schweißvorgang abschließt, wird angepaßt. In Verbindung mit dem Schweißpositionierer können verschiedene Schweißnähte wie automatisches Schweißen von Längsfugen, Ringfugen, Stoßfugen, Kehlnähten und beliebigen Schweißnähten ausgeführt werden. Es ist auch möglich, automatische Oberflächen- und Schneidprozesse auf der Werkstückoberfläche durchzuführen.
Es gibt viele Arten von Schweißmanipulatoren, und die folgenden Typen sind üblich: Manipulatoren vom Plattformtyp, Auslegermanipulatoren, Teleskoparmmanipulatoren, Tür- und Brückenmanipulatoren usw.
Der Plattformmanipulator wird hauptsächlich zum Schweißen von äußeren Längsnähten und äußeren Ringnähten von zylindrischen Behältern verwendet. Der Auslegermanipulator wird hauptsächlich zum Schweißen der inneren Längsnaht und der inneren ringförmigen Naht des Behälters verwendet. Der Teleskoparmtyp hat viele Vorteile. Zusätzlich zu den ersten beiden können Sie auch Vorgänge wie Schneiden, Schleifen und Fehlererkennung durchführen. Es wird vorgeschlagen, einen Teleskoparmmanipulator zu verwenden.
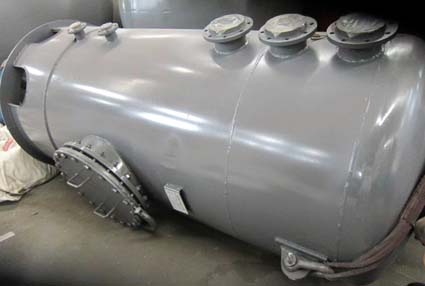
5. Montage und Schweißen
Der Aluminium-Vorratstank besteht aus einem Zylinderkörper, einem Dichtkopf und einem Verbindungsrohr. Der Aluminiumlagertank wird separat zusammengebaut und geschweißt, und dann werden der Zylinderkörper, der Dichtungskopf und das Verbindungsrohr zusammengeschweißt.
Aber das Hauptkraftelement ist der Kopf und der Zylinder. Als nächstes erklären wir den Herstellungsprozess von Aluminium Lagertanks durch den spezifischen Produktionsprozess von Kopf und Zylinder.
(1) Kopfherstellung
Der Aluminiumtank hat eine ovale Kopfstruktur. Je nach Größe kann reines Aluminium 1060 (L2) mit einer Größe von -16 × 2000 × 5800 mm zum Pressformen verwendet werden. Der spezifische Prozess ist wie folgt:
Materialauswahl → Nachprüfung → Nivellieren → Zeichnen → Unter Material → Umformen → Sekundäres Anreißen → Kopfwaage Schneiden → Ringnutbearbeitung → Schneiden (Löcher) → Lochbearbeitung → Nachprüfmaße → Reinigen vor dem Schweißen → Montieren.
Die Qualität von reinem Aluminium 1060 (L2) sollte die Qualität erfüllen, die von nationalen Standards gefordert wird.
Der elliptische Kopf ist rund, bevor er gedrückt wird. Gemäß der Formel Dp = k (Dn + δ) + 2h beträgt die entwickelte Größe Φ1258mm. Nach Berücksichtigung der Schrumpfung und der Bearbeitungszugabe beträgt die Stanzgröße Φ1270mm. Kopfgröße vor der Pressung Presse poliert gerade Kante, gefolgt von der Presse, mit einem Stanz-und Pressformen.
Der geformte Kopf ist ebenfalls kantenbearbeitet, um den Zusammenbau des Zylinders zu erleichtern. Das heißt, auf der Plattform wird eine Verarbeitungspositionslinie gezeichnet, die die Höhe der geraden Kante garantiert, und sie wird ausgewählt, um die Bearbeitung des verbleibenden Betrags zum Schneiden und Abschrägen zur gleichen Zeit in dem normalen vertikalen Fahrzeug zu vervollständigen, um die Anforderungen zu erfüllen von Konstruktionszeichnungen. Nachdem der Kopf fertig ist, sollte die innere Oberfläche des Kopfes untersucht werden. Das Verfahren besteht darin, die innere Schablone mit einer Sehnenlänge gleich 3 / 4Di des Innendurchmessers des Kopfes zu prüfen.
Der maximale Abstand darf nicht größer als 1,25% des inneren Kopfflusses sein. Bei der Überprüfung muss die Schablone senkrecht zur zu messenden Oberfläche stehen.
Für den Kopf mit Flüssigkeitsauslass sind zwei Prozesse mit Ø 100 mm Lochritzen und Lochbearbeitung nach dem Schneidvorgang der Kopfstütze und dem Inspektionsprozess erforderlich.
(2) Herstellung von Rohrabschnitten
Der Aluminium Lagertank besteht aus 3 Fassabschnitten. Die 3 Zylinderabschnitte bestehen aus zwei Stück 6 × 1888 × 786 mm reiner Aluminiumplatte 1060 (L2). Jeder Abschnitt hat ein Loch, aber unterschiedliche Lochdurchmesser. Bei der Montage ist darauf zu achten, dass die drei Bohrungen direkt über dem Zylinder liegen und die Längsfugen der drei Zylinderabschnitte auf dem Zylinder um einen ausreichenden Abstand versetzt sind. Daher sollte beim Schneiden von Material auf die Position der Bohrung geachtet werden. Einzelheiten finden Sie in der Prozesskarte für den Rohrabschnitt.
Der Rohrabschnitt-Herstellungsprozess ist wie folgt:
Materialauswahl → Nachtest → Nivellieren → Schreiber → Prüfen → Schneiden → Nutenbearbeitung → Reinigen vor dem Schweißen → Patchwork-Montage → Patchwork-Schweißen → Profilwalzen → Reinigen vor dem Schweißen → Längsnahtmontage → Längsnahtschweißen → Schweißnahtprüfung → Begradigen → Maße überprüfen → Montage .
Wählen Sie 6 × 1000 × 2000 mm Reinaluminium 1060 (L2) Platten, und die Qualität sollte die Qualität erfüllen, die von den nationalen Standards gefordert wird. Der Rohrabschnitt wird in der Regel auf einer Wickelmaschine gewalzt. Da der innere Durchmesser des Rohrabschnitts viel größer ist als die Wanddicke, wird daher die Entwicklungslänge L des Rohrrohlings als der mittlere Durchmesser Dp des Rohrabschnitts berechnet.
Das heißt, L = πDp = π (Dg + δ) = 3787 mm Dg - der Innendurchmesser des Rohrabschnitts δ - die Wanddicke des Rohrabschnitts
Nachdem der Rohrabschnitt entfaltet ist, ist er rechteckig, und seine Stanzgröße sollte auch die Schrumpfung und Bearbeitungszugabe berücksichtigen und beachten, dass die Entfaltungsrichtung des Rohrabschnitts mit der Richtung der Walzfaser der Platte übereinstimmt. Die Linie enthält die Schneidpositionslinie, die Kantenlinie, die Lochmittellinie und die Positionslinie, und die Markierung ist markiert. Sollte auch die rechteckige Diagonale prüfen, Fehler ≤ 2mm.
Die Reinigungsarbeiten sollten vor dem Schweißen ausgeführt werden, und wenn das Schweißen der Baugruppe durchgeführt wird, wird das Schweißen auf der Vorderseite der Nut positioniert. Die Schweißnaht sollte dünn sein und die Länge der Heftnaht beträgt im Allgemeinen 40-60 mm.
Rohrabschnitte können auf Drei- oder Vierwalzen-Wickelmaschinen kaltgewalzt werden. Während des Walzens sollten Sie die Krümmung oft mit einer Schablone überprüfen. Der Betrag der Längsfehlausrichtung und Längsfehlausrichtung an der Längsnaht des gewirbelten Kreises muss die technischen Anforderungen erfüllen. (Montagestück Schweißspalt 0 ~ 2mm; falsche Seite <1mm; Elliptizität ≤ 1mm)
Nach dem Walzen des Rohrabschnitts sollten die Längsfugen vor dem Längsnahtschweißen zusammengefügt werden. Leverage - Schraubenspanner, Spiraldruck Pferde und andere Vorrichtungen, um die Qualitätsprobleme nach dem Walzen zu beseitigen, erfüllen die Anforderungen an die Montagetechnik für Stoßverbindungen von Längsfugen, um die Schweißqualität zu gewährleisten. Das Heftschweißen wird nach der Montage durchgeführt. Die Längsnut des Rohrabschnitts wird vor dem Walzen bearbeitet, und die Reinigung auf beiden Seiten der Nut sollte vor dem Schweißen beobachtet werden.
Die Schweißqualität der Längsverbindungen des Rohrabschnitts muss hoch sein. Während des Schweißens wurde die Schweißprüfplatte des Aluminiumlagertanks hergestellt.
Gleichzeitig wurden aufgrund der schlechten Qualität des Lichtbogenschweißens und des Lichtbogenlöschvorgangs Lichtbogenschweißplatten und Bleiplatten mit einer Länge von 100 mm, einer Breite von 80 mm und einem Werkstück an beiden Enden der Längsschweißnaht angebracht vor dem Schweißen. Siehe ABB. 2 für die Montage Bedingungen. Nach dem Verschweißen der Längsfugen des Rohrabschnitts sind zerstörungsfreie Prüfungen nach Bedarf durchzuführen und anschließend zu richten, um die Rundheitsanforderungen zu erfüllen, bevor sie an die Baugruppe gesendet werden.
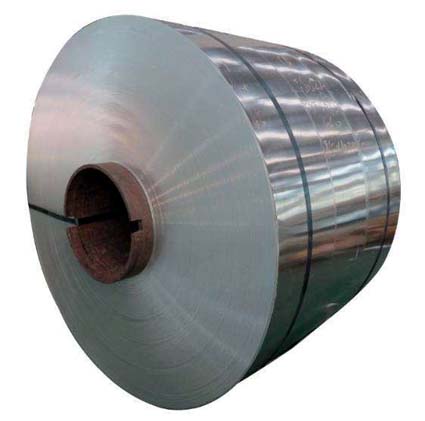
Das Folgende ist die chemische Zusammensetzung des Ausgangsmaterials
Tabelle 2-1 Chemische Zusammensetzung des Grundmaterials (L2) (GB / T3190-1996)
Grade | Al | Si | Mn | Fe | Cu |
L2 | 99.6 | 0.25 | 0.03 |
0.35 |
0.05 |
■ Analyse der Schweißbarkeit von Aluminium
I. Analyse der physikalischen und chemischen Eigenschaften
Der Schmelzpunkt von reinem Aluminium ist niedrig (660 ° C). Beim Schmelzen ändert sich die Farbe nicht, es ist schwierig, das Schmelzbad zu beobachten, und es ist leicht, während des Schweißens zusammenzubrechen und durchzubrennen. Die Wärmeleitfähigkeit ist dreimal so hoch wie bei kohlenstoffarmem Stahl, die Wärmeabfuhr ist schnell und es ist nicht einfach, beim Schweißen zu schmelzen. Der lineare Ausdehnungskoeffizient ist doppelt so groß wie der von kohlenstoffarmem Stahl und wird beim Schweißen leicht verformt. Es wird leicht zu einem dichten, hochschmelzenden Oxidfilm Al 2 O 3 (Schmelzpunkt 2050 ° C) an der Luft oxidiert. Es ist infusibel und nicht leitend. Es kann zu nicht geschmolzenem Schlackeneinschluss und instabilem Schweißen während des Schweißens führen. Daher ist die Schweißbarkeit von reinem Aluminium schlechter als die von kohlenstoffarmem Stahl. Daher umfassen die Schweißeigenschaften von reinem Aluminium hauptsächlich: leichte Oxidation während des Schweißprozesses, hoher Energieverbrauch, einfache Erzeugung von Poren (hauptsächlich Wasserstoffgasporen), leichte Bildung von Heißrissen beim Schweißen, leichtes Erweichen von Schweißverbindungen, Schweißverbindungen reduzierte Korrosionsbeständigkeit.
1, einfache Oxidation
Aluminium 1060 und Sauerstoffaffinität ist sehr groß, bei Raumtemperatur, Aluminium leicht zusammen oxidiert, die Bildung eines dichten Al2O3 Film auf der Oberfläche von Aluminium, kann die fortgesetzte Oxidation von Metall verhindern, ist vorteilhaft für die natürliche Korrosionsschutz, aber es hat Schwierigkeiten beim Schweißen gebracht. Dies liegt an dem hohen Schmelzpunkt des Aluminiumoxidfilms (etwa 2050ºC), der weit über dem Schmelzpunkt des Aluminiums 1060 liegt, und an der hohen Dichte von 3,95 bis 4,10 g / m², die etwa dem 1,4-fachen des Aluminiums entspricht 1060, plus eine sehr hohe Wärmeleitfähigkeit von 1060. Schweißen Es ist leicht, Nicht-Fusionsphänomene zu verursachen, und es ist auch wahrscheinlich, dass es zu Einschlüssen von Schweißmetall wird und Schlackeneinschlussdefekte bildet. Gleichzeitig kann der Oxidfilm mehr Feuchtigkeit absorbieren, während das Schweißen dazu führt, dass die Schweißnaht Poren erzeugt.
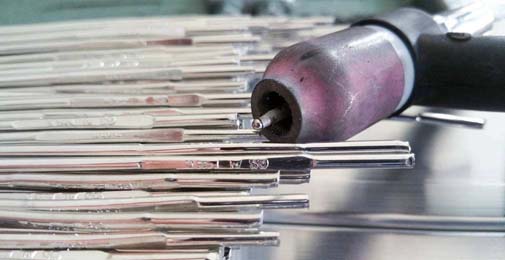
Da Aluminium 1060 keinen Kohlenstoff enthält, gibt es keine Bedingung für die Bildung von CO-Luftlöchern, und Stickstoff ist in Aluminium unlöslich, so dass allgemein angenommen wird, dass der Hauptgrund für die Erzeugung von Luftlöchern durch Aluminium 1060 Wasserstoff ist. Wasserstoff ist in flüssigem Aluminium weitgehend löslich und in festem Aluminium nahezu unlöslich. Bei hohen Schweißtemperaturen nimmt die Löslichkeit von Wasserstoff in flüssigem Aluminium stark ab. Wenn sich das Badmetall in übersättigtem Wasserstoff löst, fällt übersättigter Wasserstoff aus dem flüssigen Metall aus und bildet mit einer bestimmten Abkühlgeschwindigkeit winzige Blasen. Die Ausscheidung von Wasserstoff beim Erstarrungsprozess von Aluminiumschmelzen bildet einerseits neue, kleine, kleine Bläschen und dehnt sich andererseits in bereits gebildete winzige Bläschen aus und wächst. Gleichzeitig schwebt die Blase aufgrund der geringen relativen Dichte von Aluminium 1060 langsam. Wenn die Abkühlgeschwindigkeit höher ist, entweichen die Blasen nicht aus dem Schmelzbad und hinterlassen nach dem Erstarren das Luftloch in der Schweißnaht. Wenn der Erstarrungsprozess des Schmelzbades relativ langsam ist, wird genug Zeit dafür sein, dass die Wasserstoffblasen aus dem Schmelzbad entweichen und kein Luftloch in der Schweißnaht gebildet wird. Wenn andererseits die Erstarrungsgeschwindigkeit des geschmolzenen Pools sehr schnell ist, kann Wasserstoff nicht aus dem flüssigen Metall ausgefällt werden, sondern die übersättigte feste Lösung wird in dem geschmolzenen Aluminium gebildet, und das Gas wird nicht ausgefällt, um ein Luftloch zu bilden . Es ist ersichtlich, dass die Abkühlrate eine der wichtigen Bedingungen ist, die die Erzeugung von Luftlöchern beeinflussen.
3, Schweißen heißer Sprung
Aluminium 1060 nicht wärmehärtende Legierungen erzeugen selten Risse während des Schmelzschweißens. Risse können nur auftreten, wenn der Verunreinigungsgehalt den spezifizierten Bereich überschreitet oder wenn die Steifigkeit hoch ist. Die Ursache der thermischen Rissbildung in Aluminium 1060 hängt mit seiner Zusammensetzung und Schweißspannung zusammen. Da Aluminium 1060 einen linearen Ausdehnungskoeffizienten hat, der fast das Doppelte von Eisen ist, und seine Erstarrungsschrumpfung doppelt so groß ist wie die von Eisen, ist die Schweißspannung der Aluminiumschweißverbindung groß.
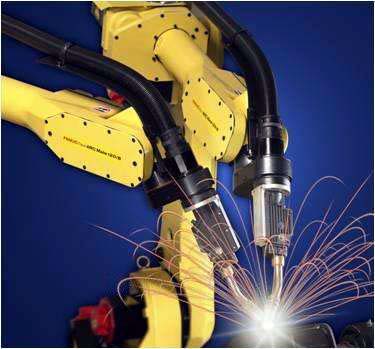
4, hohe Wärmeleitfähigkeit und Leitfähigkeit
Die Wärmeleitfähigkeit von Aluminium 1060 ist sehr groß, etwa viermal so hoch wie die von Stahl, und seine Wärmekapazität ist fast doppelt so hoch wie die von Stahl. Daher verbraucht das Schweißen von Aluminium 1060 mehr Wärme als Stahl. Um hochwertige Schweißverbindungen zu erhalten, ist es notwendig, eine Wärmequelle mit konzentrierter Energie und großer Leistung zu verwenden, um ein normales Schweißen durchzuführen, insbesondere wenn die Werkstückdicke groß ist. Aluminium 1060 hat eine gute elektrische Leitfähigkeit, und Widerstandsschweißen erfordert mehr Leistung.
5, hohe Temperatur macht die Stärke und die Plastizität niedrig
Die Stärke und Plastizität von Aluminium 1060 bei hohen Temperaturen ist sehr gering, wie 370 ° C Stärke ist nur etwa 1 MPa, kann oft nicht das Gewicht der flüssigen Pool, Zerstörung der Bildung von Schweißgut, manchmal auch den Zusammenbruch der Metall schweißen und durchbrennen.
6, keine Farbänderung
Wenn Aluminium 1060 von fest zu flüssig wechselt, gibt es keine offensichtliche Farbänderung, so dass es nicht einfach ist, die Temperatur des Bades zu beurteilen. Wenn die Temperatur ansteigt, nimmt außerdem die Festigkeit von Aluminium 1060 ab. Daher ist es schwierig, die Erwärmungstemperatur während des Schweißens zu erfassen, und es ist oft nicht möglich, den Durchbrand aufgrund einer zu hohen Temperatur wahrzunehmen.
Im Allgemeinen hat Aluminium 1060 eine gute Schweißbarkeit. Solange die obigen Schweißeigenschaften richtig gewählt sind, können das Schweißverfahren, das Schweißmaterial, das Vorschweißreinigungs- und Schweißvorgangsprozeß geeignet verwendet werden, um eine gute Schweißverbindung zu erhalten.
Die Dicke des Mantels beträgt 16 mm. Vor dem Schweißen sollte es zur Vermeidung von Heißrissen mit einer Vorwärmtemperatur von 120-140 ° C vorgewärmt werden.
(2) Unsachgemäße Schweißverfahren
Wenn zum Beispiel die Energie der Unterpulver-Schweißlinie groß ist, wird eine grobe Kornstruktur in der Wärmeeinflusszone der durch die Schweißwärme beeinflussten Zone auftreten, und die Zähigkeit der Wärmeeinflusszone wird reduziert. Die Energie des Elektroschlackeschweißens ist sogar größer als die des Unterpulverschweißens. Die Körner in der Wärmeeinflusszone sind gröber und die Zähigkeit ist deutlicher reduziert. Daher werden die Körner nach dem automatischen Argon-Lichtbogenschweißen von reinem Aluminium üblicherweise durch Normalisieren verfeinert, um die Zähigkeit zu verbessern.
Schweißprozess-Plan
Die Schweißanlage ist eine MIG-Schutzgasschweißmaschine NB-500 mit einem Stromregelbereich von 50 bis 500A. Der Durchmesser des Schweißdrahtes ist Φ1,6mm und das Schutzgas, Argon, hat eine Reinheit von nicht weniger als 99,96%. Der Grund für seine Wahl ist wie folgt:
(1) Neben dem CO2-Schutzgasschweißen können nahezu alle Schweißverfahren zum Schweißen von Aluminium und Aluminiumlegierungen verwendet werden, aber Aluminium und Aluminiumlegierungen sind für verschiedene Schweißverfahren unterschiedlich geeignet, und verschiedene Schweißverfahren haben ihre eigenen Anwendungen.
Gasschweißen und Elektroden-Lichtbogenschweißverfahren sind einfach und leicht zu bedienen. Gasschweißen kann verwendet werden, um das Schweißen von dünnen Aluminiumplatten und Gussstücken, die keine hohe Schweißqualität erfordern, zu reparieren. Schweißelektroden-Lichtbogenschweißen kann zum Schweißen von Aluminiumlegierungsgussteilen verwendet werden. Schutzgasschweißen ist TIG-Schweißen und MIG-Schweißen, sie sind die am häufigsten verwendeten Aluminium-und Aluminium-Legierung Schweißverfahren. Von der "Kathodenreinigungs" -Rolle und dem Wolfram-Maximalstrom wird im Allgemeinen Wolfram-Lichtbogenschweißen verwendet. Da es unter dem guten Schutz des Argonschweißens steht, kann das Schmelzbad vor Sauerstoff, Wasserstoff und anderen schädlichen Gasen geschützt werden. Der Argon-Lichtbogenschweißstrom ist stabil, die Wärme ist konzentriert, das Schweißgewebe ist kompakt, das Aussehen ist schön, die Festigkeit und die Plastizität sind hoch und die Verformung des Werkstücks ist gering.
Aufgrund des begrenzten Stroms von Wolfram ist jedoch die Eindringkraft des Lichtbogens gering und die Produktivität ist gering. Daher wird es im Allgemeinen zum Schweißen dünner Platten mit einer Dicke von 6 mm oder weniger verwendet.
MIG-Lichtbogenleistung, Wärmekonzentration, Wärmeeinflusszone ist klein, die Produktivität kann mehr als dreimal höher sein als beim WIG-Schweißen. Daher ist es für das Schweißen von dicken Plattenstrukturen geeignet. Es kann Aluminium- und Aluminiumlegierungsplatten unter 50 mm schweißen. Das Schweißen von 30 mm dicken Aluminiumplatten kann ohne Vorwärmung erfolgen. Das halbautomatische MIG-Schweißen wird hauptsächlich für das Heftschweißen, intermittierende kleine Schweißnähte und das Schweißen von unregelmäßig geformten Werkstücken verwendet.
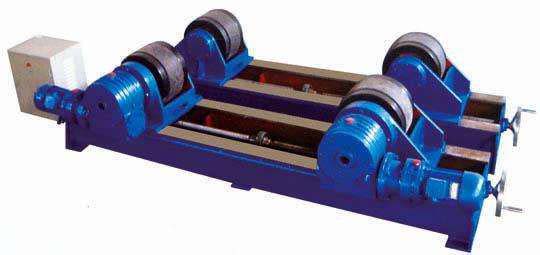
Diese Art von nutzlosem Energieverbrauch ist wichtiger als Stahlschweißen. Um qualitativ hochwertige Schweißverbindungen zu erhalten, sollte es möglich sein, energiekonzentrierte Hochleistungsenergien sowie Vorwärm- und andere technologische Maßnahmen zu verwenden.
MIG-Schweißen im Vergleich mit WIG-Schweißen, MIG-Schweißen der minimalen Heizfläche von 10-4 cm2, die maximale Leistungsdichte von 104 ~ 105W • cm-2, Die minimale Heizfläche von WIG-Schweißen ist 10-3cm2, und die maximale Leistungsdichte ist 1,5-104 W • cm-2. Daher ist es besser, MIG-Schweißen zu verwenden.
(3) Auswahl des Schweißdrahts aus Aluminium und Aluminiumlegierungen Neben der Berücksichtigung einer guten Schweißprozessleistung sollten die Zugfestigkeit und die Plastizität (durch Biegeprüfung) der Stoßverbindung die spezifizierten Anforderungen gemäß den Anforderungen des Behälters erfüllen. Bei Schiffen mit Korrosionsbeständigkeitsanforderungen sollte die Korrosionsbeständigkeit der Schweißverbindungen ebenfalls bei oder nahe bei der des Grundmetalls liegen. Daher basiert die Auswahl des Schweißdrahtes hauptsächlich auf den folgenden Prinzipien:
1. Die Reinheit von reinem Aluminium Schweißdraht ist in der Regel nicht niedriger als die des Grundmetalls;
2. Die chemische Zusammensetzung des Aluminiumlegierungs-Schweißdrahts entspricht im Allgemeinen dem Grundmetall oder ist diesem ähnlich;
3. Der Gehalt an korrosionsbeständigen Elementen (Magnesium, Mangan, Silizium usw.) in Aluminiumlegierungs-Schweißdrähten ist im Allgemeinen nicht niedriger als der von Grundmetall;
4. Wenn das unähnliche Aluminium geschweißt wird, sollte der Schweißdraht entsprechend dem Grundmaterial mit hoher Korrosionsbeständigkeit und hoher Festigkeit ausgewählt werden;
5. Hochfeste Aluminiumlegierungen, die keine Korrosionsbeständigkeit erfordern (wärmebehandelte verstärkte Aluminiumlegierungen), können unterschiedliche Legierungsdrähte, wie z. B. SAlSi-1, verwenden, die eine gute Rissbeständigkeit aufweisen und eine geringere Festigkeit als das Basismetall aufweisen können.
Entsprechend der Verwendung von Aluminium-Lagertanks, in Übereinstimmung mit den oben genannten Prinzipien (gleiche Stärke, etc.), wird der Draht jetzt als SAl-2 gewählt, dessen Aluminiumgehalt ist höher als 1060 (L2) industriell reines Aluminium, um Gewährleistung der Korrosionsbeständigkeit von Schweißverbindungen. .
(4) Schutzgasauswahl
Aluminium und Aluminiumlegierung MIG-Schweißen, nur mit Inertgas Argon oder Helium, wird kein reaktives Gas verwendet. Obwohl Argon oder Helium ein Schutzgas ist, sind seine physikalischen Eigenschaften unterschiedlich und daher ist seine Prozessleistung ebenfalls unterschiedlich. Die Dichte von Argon ist etwa 1,4 mal so hoch wie die von Luft, schwerer als Luft; Die Dichte von Helium ist etwa 0,14 mal so hoch wie die von Luft, leichter als Luft. Beim Schweißen in der flachen Schweißposition sinkt das Argongas und treibt die Luft weg. Dies schützt den Lichtbogen und deckt die Schweißzone ab. Wenn Heliumgasschutz gewählt wird, wird die gleiche Schutzwirkung erhalten. Die Strömung und der Verbrauch von Heliumgas ist etwa 2 bis 3 mal höher als die von Argongas.
Außerdem ist die Wärmeleitfähigkeit von Helium höher als die von Argon, und ein Lichtbogenplasma mit einer gleichmäßigeren Energieverteilung kann erzeugt werden. Das Argon-Lichtbogenplasma hat eine hohe Zentrumsenergie der Lichtbogensäule und seine periphere Energie ist niedrig. Daher ist die Form der Schweißnaht während des Xenon-Lichtbogen-MIG-Schweißens durch ein tiefes Eindringen und ein weites Schmelzen gekennzeichnet, und der Boden der Schweißnaht ist ein Kreisbogen. Die Mitte der Schweißnaht des Argon-MIG-Schweißens hat jedoch eine schmale und tiefe "fingerähnliche" Durchdringung mit einer flacheren Penetration auf beiden Seiten.
Das Ionisationspotential von Helium ist höher als das von Argon. Wenn die Lichtbogenlänge und der Schweißstrom konstant sind, ist die Lichtbogenspannung des Heliumgasschutzes höher als die des Argonlichtbogens. Bei reinem Helium-Schutz-MIG-Schweißen ist es somit schwierig, einen axialen Strahlübergang zu erreichen, häufig treten Spritzer und rauhe Schweißflächen auf. Argon-geschütztes MIG-Schweißen ist leichter zu erreichen Jet-Übergang.
Aufgrund der niedrigen Lichtbogenspannung und der niedrigen Lichtbogenenergiedichte des MIG-Argon-Lichtbogenschweißens ist der Lichtbogen stabil und hat nur wenige Spritzer, so dass er für das Schweißen dünner Teile geeignet ist. MIG-Xenon-Lichtbogenschweißen hat eine hohe Energiedichte und eignet sich zum Schweißen dicker Teile, aber der Lichtbogen ist nicht stabil genug und Helium ist teuer.
Die maximale Wandstärke dieses Produkts beträgt 16 mm. Verwenden Sie daher Argon als Schutzgas.
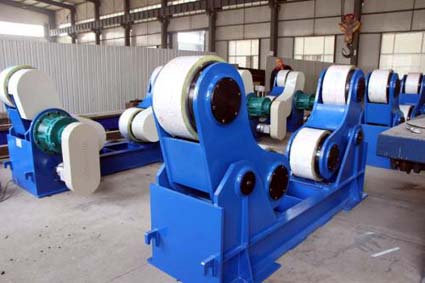
3. Vorbereitung vor dem Schweißen
(1) Nutform, Fugenform und -größe
Nutform, Fugenform und -größe hängen von der Dicke der Aluminiumschweißung, der Schweißposition, der Tröpfchentransferform und dem Schweißprozess ab.
Wenn Schweißnahtdicke, Schweißposition und Schweißprozess festgelegt sind, ist die Form der Tropfenübertragung eine wichtige Voraussetzung für die Bestimmung der Form der Parameter Nut und Schweißprozess.
Die Form der Tropfenübertragung beim MIG-Schweißen und die Stabilität des Prozesses sind der Schlüssel für die Eignung des MIG-Schweißverfahrens. Wenn der Schweißstrom von klein auf groß ansteigt, wechselt der Tröpfchenübergang vom kurzschlußartigen Übergang zum tropfenförmigen Übergang zum Einspritzübergang (Schießtröpfchenübergang, Strahlübergangsrichtung). Der Kurzschlussübergang gilt nur für das MIG-Schweißen von dünnwandigen Teilen mit einer Materialstärke von 1 bis 2 mm. Der Einspritzübergangsprozess ist relativ stabil und kann zum MIG-Schweißen von Aluminiummaterialien mit unterschiedlicher Dicke verwendet werden. Zwischen dem Kurzschlussübergang und dem Jet-Übergang gibt es eine Sub-Jet-Übergangszone, in der trotz der kurzen Lichtbogenlänge kein Kurzschluss auftritt. Selbst wenn sich die Lichtbogenlänge ändert, können Strom und Spannung unverändert bleiben. Selbst bei einer konstanten Stromquelle (tiefe externe Tropfeneigenschaften) kann der Lichtbogen selbstregulierend sein, der Schweißprozess ist stabil und die Schweißnaht ist gleichmäßig und schön geformt. Die Praxis zeigt, dass beim MIG-Schweißen von Aluminium mit Subjet-Übergang die Schweißleistung höher und die Schweißqualität besser ist. MIG-Schweißen, die allgemeine Verwendung von DC-Reverse-Verbindung, verwenden Sie nicht DC positiv oder AC, automatisches Schweißen und halbautomatisches Schweißen zwei Möglichkeiten.
Einsatz in Form von Jet-Übergang, die Übergangszeit der Injektion, enge und tiefe Schweißnaht leicht präsentiert Finger Penetration, beide Seiten der schlechten Penetration, Porosität Risse und andere Mängel schweißen. Wenn Subjet-Übergänge verwendet werden, ist die Lichtbogenlänge kürzer, die Lichtbogenspannung ist niedriger, der Lichtbogen wird leicht detoniert und die Tröpfchen am Ende des Drahtes wachsen so groß wie der Durchmesser des Drahtes, wenn er zum Schmelzbad übergeht entlang der Achse. Während dieser Zeit kann ein kurzzeitiger Kurzschluss auftreten. Beim Sub-Jet-Übergang-MIG-Schweißen ist die Kathodenzerstäubungsfläche groß, der Badschutzeffekt ist gut, die Schweißnaht ist gut ausgebildet und die Schweißnahtdefekte sind klein. Aus diesem Grund sollten Aluminium-Lagertanks die oben genannten Probleme bei der Auswahl der Schweißparameter und des Nutdesigns vollständig berücksichtigen.
(2) Reinigung vor dem Schweißen
Der Oxidfilm und Verunreinigungen auf der Oberfläche der Aluminiumschweißung und des Drahtes können dazu führen, dass sich die statische Krümmung des Lichtbogens während des MIG-Schweißprozesses nach unten bewegt. Als Ergebnis steigt der Schweißstrom plötzlich an, die Schmelzgeschwindigkeit des Drahtes steigt an und der Lichtbogen verlängert sich.
An diesem Punkt änderte sich auch der Klang des Bogens von dem rhythmischen Summen zu dem harten Rufen. Daher sollten MIG-Schweißteile und Drahtoberflächen streng gereinigt werden, wobei die Qualität der Reinigung direkt die Qualität der Schweißprozesse und -verbindungen beeinflusst, wie zum Beispiel die Tendenz der Schweißnahtporosität und der mechanischen Eigenschaften. MIG-Schweißen von Schweißnähten und Drahtoberflächenreinigung, oft mit chemischen Reinigungs- und mechanischen Reinigungsmethoden. Zur gleichen Zeit, Aluminium-und Aluminiumlegierung Schweißdraht ist am besten zu verwenden, eine glatte, glatte, helle "Trilight" Schweißdraht mit speziellen Oberflächenbehandlung.
1. Chemische Reinigung
Hohe chemische Reinigungseffizienz, stabile Qualität, geeignet für sauberen Schweißdraht und kleine Abmessungen, Serienfertigung von Werkstücken. Verfügbare Dip-Methode und Scrub-Methode zwei. Man kann Aceton, Benzin, Kerosin und andere organische Lösungsmittel auf die Oberfläche des Öls verwenden, bei 40 ° C ~ 70 ° C 5% ~ 10% NaOH-Lösung alkalisch waschen 3min ~ 7min (etwas länger, aber nicht mehr als 20min reines Aluminium ), mit Wasser gespült, dann mit 30% HNO3-Lösung bei Raumtemperatur bis 60 ° C für 1 Minute bis 3 Minuten gebeizt, mit fließendem Wasser gespült, an der Luft getrocknet oder bei niedriger Temperatur getrocknet.
2. mechanische Reinigung
Mechanische Reinigung wird oft verwendet, wenn das Werkstück eine große Größe, einen langen Produktionszyklus, mehrschichtiges Schweißen oder chemische Reinigung aufweist. Verwenden Sie zuerst Aceton, Benzin und andere organische Lösungsmittel, um die Oberfläche abzuwischen, um Öl zu entfernen. Verwenden Sie dann direkt eine Kupferdrahtbürste mit einem Durchmesser von 0,15 mm bis 0,20 mm oder eine Edelstahldrahtbürste, bis der Metallglanz freiliegt. Im Allgemeinen ist es nicht geeignet, mit einer Schleifscheibe oder gewöhnlichem Sandpapier zu schleifen, um zu vermeiden, dass die Sandpartikel auf der Metalloberfläche verbleiben, und die Defekte, wie Schlackeneinschluss, werden beim Schweißen erzeugt. Zusätzlich kann die zu schweißende Oberfläche mit einem Spatel, einer Feile oder dergleichen gereinigt werden.
Nachdem das Werkstück und der Schweißdraht gereinigt und gereinigt wurden, wird während der Lagerung ein Oxidfilm regeneriert. Insbesondere in feuchter Umgebung wächst der Oxidfilm in einer Umgebung, die durch Säuren, Alkalien und andere Dämpfe verunreinigt ist, schneller. Daher sollte nach dem Reinigen und Reinigen von Werkstücken und Schweißdraht die Lagerzeit vor dem Schweißen so weit wie möglich verkürzt werden. In feuchten Klimazonen sollte das Schweißen in der Regel innerhalb von 4 Stunden nach der Reinigung durchgeführt werden. Nach der Reinigung, wenn die Lagerzeit zu lang ist (wie mehr als 24 Stunden) sollte erneut behandelt werden.
Der Reinigungsplan dieser Tanks ist:
Oxide und andere Verunreinigungen innerhalb von 50 mm von der Nut und deren Umfang sollten gereinigt werden. Verwenden Sie zuerst ein Edelstahldrahtrad mit einem Durchmesser von weniger als 0,2 mm zum Reinigen und dann zur chemischen Reinigung. Schweißdraht wird nur chemisch gereinigt. Die gereinigte Nut sollte innerhalb von 2 Stunden geschweißt werden, und der freiliegende Draht in der Atmosphäre nach dem Waschen und Trocknen sollte nicht länger als 4 Stunden sein.
Die chemischen Reinigungsparameter von Aluminiumtanks sind in Tabelle 1 gezeigt:
Tabelle 1 Parameter für die chemische Reinigung von Aluminium-Tankrillen
|
||||
Reinigungsreihenfolge und Inhalt | Lösungsname | Lösungskonzentration /% | Lösungstemperatur / ° C | Reinigungszeit / min |
Reinigungsnut und -draht | NaOH | 5 | 50~60 | 1~1.5 |
Waschen | Tap water | — | >10 | 2~3 |
Reinigungsnut und -draht | NaOH | 25~30 | >10 | 1~2 |
Waschen | Tap water | — | >10 | 2~3 |
Trocknen | Das Werkstück wird mit ölfreier Heißluft getrocknet und der Draht getrocknet und 1 Stunde bei 200 ° C getrocknet. |
4. Vorbereitung der Prozessausrüstung
Die für das MIG-Schweißen erforderliche Prozessausrüstung umfasst Schweißwagen und -schienen, Manipulatoren, Positionierer, Rollenträger und Klemmen für Schweißungen. Die Hauptschweißnähte für Aluminium-Lagertanks sind einseitige und einlagige Schweißnähte mit V-Nut. Um eine Penetration sicherzustellen und ein Auslaufen von Metall in das Schmelzbad zu verhindern, wird ein Verfahren zum Hinzufügen einer Rückseiten-Flachdichtung angewendet. Hier nur die Hauptwerkzeugauswahl.
(1) Zwischenlagen
MIG-Schweißen, wie TIG-Schweißen, erfordert manchmal eine Rückseitenschweißung, da die MIG-Schweißleistung größer ist, die Durchdringungsfähigkeit ist stärker. Das Rückenpolster ist nicht nur vorteilhaft, um ein Auslaufen von Metall im Bad zu verhindern, sondern hilft auch, die Größe der Verbindung zu reduzieren . Die Betriebsbedingungen sind entspannter, und die Anforderungen an das Betriebsverhalten können angemessen reduziert werden. Die Längs- und Umfangsschweißnähte des Aluminiumlagers bestehen alle aus temporären Pads und das Material ist das gleiche wie das Basismetall, das nicht nur das Schmelzbad verschmutzen, sondern auch die Wärmeableitung erleichtern kann. Die Rückdichtung ist in der Reifenbefestigung der Schweißkonstruktion installiert, entspricht der Schweißnahtposition und ist fest an den gegenüberliegenden Seiten der beiden Teile angebracht. Nach dem Schweißen wird es von der Schweißkonstruktion getrennt.
(2) Rollenwagen
Der Rollenwagen ist eine häufig verwendete Prozessausrüstung für die Herstellung von Druckbehältern. Der Schweißwalzenrahmen treibt die Walze durch den Motor und nutzt die Reibung zwischen der Antriebsrolle und dem Schweißstück, um die Verdrängungsmaschine anzutreiben, die das rohrförmige Schweißstück mit einer bestimmten Geschwindigkeit dreht. Der Schweißrollenrahmen, der bei der Schweißproduktion verwendet wird, besteht normalerweise aus einem Paar aktiver Rollenrahmen und einem Paar passiver Rollenrahmen.
Der Schweißwalzenrahmen wird hauptsächlich für die Montage und das Schweißen von zylindrischen Fässern verwendet. Wenn das rohrförmige Umfangsschweißen durchgeführt wird, wird, da sich der Zylinder auf der Walze dreht, das Allpositionsschweißen der ringförmigen Schweißnaht zu flachem Schweißen geändert, was zur Verbesserung der Qualität der Schweißnaht und der Schweißproduktivität günstig ist. Wenn die Installationshöhen des aktiven Rollenhalters und des passiven Rollenhalters unterschiedlich sind, kann auch die Montage und das Verschweißen des Konus und des Zylinderschweißteils mit ungleichem Durchmesser durchgeführt werden. Für rechteckige Schweißteile und unregelmäßig geformte Schweißteile können sie in speziellen Ringklemmen oder auf Rollenwagen montiert werden.
Schweißwalzenrahmen kann unterteilt werden in:
Universal-Schweißrollenrahmen und Spezial-Schweißrollenrahmen werden jetzt universell eingesetzt. Die am häufigsten verwendeten universellen Schweißrollenwagen in der industriellen Produktion lassen sich in zwei Kategorien einteilen: Einer ist ein sich selbst einstellender Schweißwalzenrahmen und der andere ist ein einstellbarer Schweißwalzenrahmen.
Die Charakteristik des selbsteinstellenden Schweißwalzenrahmens besteht darin, dass jeder Walzenrahmen aus zwei Sätzen von Doppelwalzen besteht. Jede Gruppe von Rollenhaltern kann sich zentriert an ihrem Drehpunkt drehen, so dass sie sich an verschiedene Durchmesser von Schweißungen über einen relativ großen Bereich anpassen kann, ohne den Abstand zwischen den beiden Rollensätzen zu ändern. Beim Schweißen von Schweißverbindungen mit kleinem Durchmesser kann der äußere Kreis der Schweißverbindung jedoch nur in Kontakt mit den zwei Rollen jedes Paares von Rollenrahmen stehen, und die Belastbarkeit des Rollenrahmens wird entsprechend auf 75% der Nennlast reduziert .
Der selbsteinstellende Schweißwalzenrahmen nimmt normalerweise den Doppelantriebsübertragungsmodus an. Der Motor überträgt das Drehmoment auf die beiden Sätze von Rollen durch das sekundäre Reduzierstück und die Verbindungswelle, um eine sanfte Rotationsgeschwindigkeit zu erreichen. Der Antriebsmotor kann eine elektromagnetische stufenlose Geschwindigkeitsregelung oder eine stufenlose Geschwindigkeitsregelung des Wechselrichters verwenden.
Die Eigenschaft des einstellbaren Schweißwalzenrahmens besteht darin, dass der Abstand zwischen den Walzen jedes Walzenrahmens einstellbar ist, um sich an Schweißstücke mit unterschiedlichem Durchmesser anzupassen. Der Walzenabstand kann durch verschiedene Verfahren eingestellt werden. Die einfachste Methode besteht darin, zwei Reihen von Bolzenlöchern mit demselben Lochabstand auf der Oberfläche des Rollenlagers zu bohren. Der Rollensitz wird in die entsprechende Lochposition entsprechend dem Durchmesser der Schweißkonstruktion eingebaut. Schraube fixiert. Wenn sich der Durchmesser des zu schweißenden Werkstücks ständig ändert, kann die Spindelsteigung über die Spindelsteigung eingestellt werden. Für das Anwendungsgebiet mit einer kleinen Auswahl von Schweißdurchmessern kann der Verbindungsmechanismus verwendet werden, um den Radabstand einzustellen, was sehr einfach ist und zusätzliche Zeit spart.
Der einstellbare Schweißrollenrahmen verwendet normalerweise ein Paar von aktiven Rollenrahmen und ein Paar von passiven Rollenrahmen, um Montage- und Schweißvorgänge durchzuführen. Der aktive Rollenwagen kann in Einzelantrieb und Doppelantrieb unterteilt werden. Beide Motoren können synchron über elektronische Schaltungen gestartet werden. Der Vorteil des Doppelantriebs besteht darin, dass die Schweißkonstruktion reibungslos rotiert und das Prellen verhindert. China hat den Industriestandard JB / T9187-1999 für das Schweißen von Rollenwagen entwickelt. Unter dem Gesichtspunkt der Sicherheit und unter Berücksichtigung der vernünftigen Wahl der Radantriebsleistung legt der Industriestandard JB / T9187 auch fest, dass der Umschlingungswinkel α der Mitte des Rades zur Mitte der Schweißkonstruktion innerhalb des Bereichs von 45 ° bis 110 °. In der eigentlichen Schweißproduktion ist das Auswahlverfahren für den Schweißwalzenrahmen wie folgt:
1. Gemäß Spezifikation und Gewicht der Schweißkonstruktion, die im Produktionsprogramm der Fabrik angegeben ist, und der monatlichen Produktionskapazität werden die Spezifikationen des Schweißwalzenrahmens, die Nennlastkapazität und die zu bestückende Menge vorläufig bestimmt.
2. Die Struktur der Walze wird nach dem Gewicht der Schweißkonstruktion und der Art des Materials bestimmt. Für Druckbehälter aus Edelstahl, Titanlegierung und Aluminiumlegierung müssen Gummi- oder Polyurethanräder verwendet werden.
3. Bestimmen Sie nach der anzuwendenden Schweißverfahrensmethode die Anforderungen für den Drehzahlbereich des Schweißwalzenrahmens und andere technische Eigenschaften.
4. Entsprechend den Qualitätsanforderungen der Schweißnaht sollte die Regelgenauigkeit der Walzenbahngeschwindigkeit des Schweißwalzenrahmens vorgeschlagen werden.
5. sollte die Arbeitsumgebung berücksichtigen.
In Anbetracht der Vielseitigkeit, nimmt der Aluminium-Speichertank den einstellbaren Schweißwalzenrahmen des Typs EB-10TN an, seine technischen Parameter sind:
Maximale Last 5t, maximale Rotationskapazität 10t, Rollenbahngeschwindigkeit 70-1200mm / min,
Werkstückdurchmesser 150-4000 mm, Anzahl der Gummiräder 6, Achsabstand zwischen den Rädern 410 bis 1810,
Abmessungen: Antriebsrad 3300 × 890, angetriebenes Rad 2600 × 500 × 515, Rollendurchmesser (Gummirad 350),
Gewicht: Antriebsrad 600, passives Rad 400.
(3) Schweißmanipulator
Schweißgerät, auch Schweißgerätesteuerung genannt, liefert präzise den Schweißkopf und hält ihn in der Position, in der er geschweißt werden soll. Oder bei der ausgewählten Schweißgeschwindigkeit wird der Schweißkopf entlang der spezifizierten Bewegungsbahn bewegt, und die Schweißkopfverdrängungsmaschine, die den Schweißvorgang abschließt, wird angepaßt. In Verbindung mit dem Schweißpositionierer können verschiedene Schweißnähte wie automatisches Schweißen von Längsfugen, Ringfugen, Stoßfugen, Kehlnähten und beliebigen Schweißnähten ausgeführt werden. Es ist auch möglich, automatische Oberflächen- und Schneidprozesse auf der Werkstückoberfläche durchzuführen.
Es gibt viele Arten von Schweißmanipulatoren, und die folgenden Typen sind üblich: Manipulatoren vom Plattformtyp, Auslegermanipulatoren, Teleskoparmmanipulatoren, Tür- und Brückenmanipulatoren usw.
Der Plattformmanipulator wird hauptsächlich zum Schweißen von äußeren Längsnähten und äußeren Ringnähten von zylindrischen Behältern verwendet. Der Auslegermanipulator wird hauptsächlich zum Schweißen der inneren Längsnaht und der inneren ringförmigen Naht des Behälters verwendet. Der Teleskoparmtyp hat viele Vorteile. Zusätzlich zu den ersten beiden können Sie auch Vorgänge wie Schneiden, Schleifen und Fehlererkennung durchführen. Es wird vorgeschlagen, einen Teleskoparmmanipulator zu verwenden.
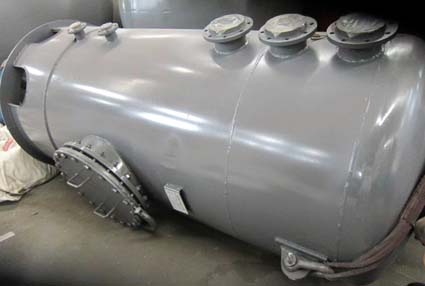
5. Montage und Schweißen
Der Aluminium-Vorratstank besteht aus einem Zylinderkörper, einem Dichtkopf und einem Verbindungsrohr. Der Aluminiumlagertank wird separat zusammengebaut und geschweißt, und dann werden der Zylinderkörper, der Dichtungskopf und das Verbindungsrohr zusammengeschweißt.
Aber das Hauptkraftelement ist der Kopf und der Zylinder. Als nächstes erklären wir den Herstellungsprozess von Aluminium Lagertanks durch den spezifischen Produktionsprozess von Kopf und Zylinder.
(1) Kopfherstellung
Der Aluminiumtank hat eine ovale Kopfstruktur. Je nach Größe kann reines Aluminium 1060 (L2) mit einer Größe von -16 × 2000 × 5800 mm zum Pressformen verwendet werden. Der spezifische Prozess ist wie folgt:
Materialauswahl → Nachprüfung → Nivellieren → Zeichnen → Unter Material → Umformen → Sekundäres Anreißen → Kopfwaage Schneiden → Ringnutbearbeitung → Schneiden (Löcher) → Lochbearbeitung → Nachprüfmaße → Reinigen vor dem Schweißen → Montieren.
Die Qualität von reinem Aluminium 1060 (L2) sollte die Qualität erfüllen, die von nationalen Standards gefordert wird.
Der elliptische Kopf ist rund, bevor er gedrückt wird. Gemäß der Formel Dp = k (Dn + δ) + 2h beträgt die entwickelte Größe Φ1258mm. Nach Berücksichtigung der Schrumpfung und der Bearbeitungszugabe beträgt die Stanzgröße Φ1270mm. Kopfgröße vor der Pressung Presse poliert gerade Kante, gefolgt von der Presse, mit einem Stanz-und Pressformen.
Der geformte Kopf ist ebenfalls kantenbearbeitet, um den Zusammenbau des Zylinders zu erleichtern. Das heißt, auf der Plattform wird eine Verarbeitungspositionslinie gezeichnet, die die Höhe der geraden Kante garantiert, und sie wird ausgewählt, um die Bearbeitung des verbleibenden Betrags zum Schneiden und Abschrägen zur gleichen Zeit in dem normalen vertikalen Fahrzeug zu vervollständigen, um die Anforderungen zu erfüllen von Konstruktionszeichnungen. Nachdem der Kopf fertig ist, sollte die innere Oberfläche des Kopfes untersucht werden. Das Verfahren besteht darin, die innere Schablone mit einer Sehnenlänge gleich 3 / 4Di des Innendurchmessers des Kopfes zu prüfen.
Der maximale Abstand darf nicht größer als 1,25% des inneren Kopfflusses sein. Bei der Überprüfung muss die Schablone senkrecht zur zu messenden Oberfläche stehen.
Für den Kopf mit Flüssigkeitsauslass sind zwei Prozesse mit Ø 100 mm Lochritzen und Lochbearbeitung nach dem Schneidvorgang der Kopfstütze und dem Inspektionsprozess erforderlich.
(2) Herstellung von Rohrabschnitten
Der Aluminium Lagertank besteht aus 3 Fassabschnitten. Die 3 Zylinderabschnitte bestehen aus zwei Stück 6 × 1888 × 786 mm reiner Aluminiumplatte 1060 (L2). Jeder Abschnitt hat ein Loch, aber unterschiedliche Lochdurchmesser. Bei der Montage ist darauf zu achten, dass die drei Bohrungen direkt über dem Zylinder liegen und die Längsfugen der drei Zylinderabschnitte auf dem Zylinder um einen ausreichenden Abstand versetzt sind. Daher sollte beim Schneiden von Material auf die Position der Bohrung geachtet werden. Einzelheiten finden Sie in der Prozesskarte für den Rohrabschnitt.
Der Rohrabschnitt-Herstellungsprozess ist wie folgt:
Materialauswahl → Nachtest → Nivellieren → Schreiber → Prüfen → Schneiden → Nutenbearbeitung → Reinigen vor dem Schweißen → Patchwork-Montage → Patchwork-Schweißen → Profilwalzen → Reinigen vor dem Schweißen → Längsnahtmontage → Längsnahtschweißen → Schweißnahtprüfung → Begradigen → Maße überprüfen → Montage .
Wählen Sie 6 × 1000 × 2000 mm Reinaluminium 1060 (L2) Platten, und die Qualität sollte die Qualität erfüllen, die von den nationalen Standards gefordert wird. Der Rohrabschnitt wird in der Regel auf einer Wickelmaschine gewalzt. Da der innere Durchmesser des Rohrabschnitts viel größer ist als die Wanddicke, wird daher die Entwicklungslänge L des Rohrrohlings als der mittlere Durchmesser Dp des Rohrabschnitts berechnet.
Das heißt, L = πDp = π (Dg + δ) = 3787 mm Dg - der Innendurchmesser des Rohrabschnitts δ - die Wanddicke des Rohrabschnitts
Nachdem der Rohrabschnitt entfaltet ist, ist er rechteckig, und seine Stanzgröße sollte auch die Schrumpfung und Bearbeitungszugabe berücksichtigen und beachten, dass die Entfaltungsrichtung des Rohrabschnitts mit der Richtung der Walzfaser der Platte übereinstimmt. Die Linie enthält die Schneidpositionslinie, die Kantenlinie, die Lochmittellinie und die Positionslinie, und die Markierung ist markiert. Sollte auch die rechteckige Diagonale prüfen, Fehler ≤ 2mm.
Die Reinigungsarbeiten sollten vor dem Schweißen ausgeführt werden, und wenn das Schweißen der Baugruppe durchgeführt wird, wird das Schweißen auf der Vorderseite der Nut positioniert. Die Schweißnaht sollte dünn sein und die Länge der Heftnaht beträgt im Allgemeinen 40-60 mm.
Rohrabschnitte können auf Drei- oder Vierwalzen-Wickelmaschinen kaltgewalzt werden. Während des Walzens sollten Sie die Krümmung oft mit einer Schablone überprüfen. Der Betrag der Längsfehlausrichtung und Längsfehlausrichtung an der Längsnaht des gewirbelten Kreises muss die technischen Anforderungen erfüllen. (Montagestück Schweißspalt 0 ~ 2mm; falsche Seite <1mm; Elliptizität ≤ 1mm)
Nach dem Walzen des Rohrabschnitts sollten die Längsfugen vor dem Längsnahtschweißen zusammengefügt werden. Leverage - Schraubenspanner, Spiraldruck Pferde und andere Vorrichtungen, um die Qualitätsprobleme nach dem Walzen zu beseitigen, erfüllen die Anforderungen an die Montagetechnik für Stoßverbindungen von Längsfugen, um die Schweißqualität zu gewährleisten. Das Heftschweißen wird nach der Montage durchgeführt. Die Längsnut des Rohrabschnitts wird vor dem Walzen bearbeitet, und die Reinigung auf beiden Seiten der Nut sollte vor dem Schweißen beobachtet werden.
Die Schweißqualität der Längsverbindungen des Rohrabschnitts muss hoch sein. Während des Schweißens wurde die Schweißprüfplatte des Aluminiumlagertanks hergestellt.
Gleichzeitig wurden aufgrund der schlechten Qualität des Lichtbogenschweißens und des Lichtbogenlöschvorgangs Lichtbogenschweißplatten und Bleiplatten mit einer Länge von 100 mm, einer Breite von 80 mm und einem Werkstück an beiden Enden der Längsschweißnaht angebracht vor dem Schweißen. Siehe ABB. 2 für die Montage Bedingungen. Nach dem Verschweißen der Längsfugen des Rohrabschnitts sind zerstörungsfreie Prüfungen nach Bedarf durchzuführen und anschließend zu richten, um die Rundheitsanforderungen zu erfüllen, bevor sie an die Baugruppe gesendet werden.