Kontinuierliches Stanzdesign von Metallgehaeuseteilen
Form und Größe der Gehäuseteile des Autotürglashebers. Wie in Abbildung 8.2.1 gezeigt,
Das material ist 08 stahlplatte, platte dicke 1,5mm, massenproduktion.
Stempelfertigung erfordert die Vorbereitung eines Stempelfertigungsprozesses.
8.2.1 Prozessanalyse von Stanzteilen
Zunächst müssen Sie die Anwendung und die technischen Anforderungen des Produkts vollständig verstehen und eine Prozessanalyse durchführen.
Das Glas an der Autotür wird vom Lifter angehoben oder abgesenkt.
Das Zusammenbaudiagramm der Lifterkomponenten ist in Abbildung 8.2.2 dargestellt. Das Stanzteil ist der Außenmantel 5 davon. Der Getriebemechanismus des Aufzugs ist im Außengehäuse untergebracht und durch drei gleichmäßig verteilte kleine Löcher ø 3,2 mm am Außengehäuseflansch mit der Türsitzplatte vernietet. Die Antriebswelle 6 ist am Stützabschnitt des rechten Endlochs φ 16,5 mm mit dem Abstand von I T11 montiert. Die Bremsdrehfeder 3, das Verbindungsstück 9 und die Spindel 4 sind mit dem Ritzel 11 gekoppelt, um den Griff 7 zu kippen. Die Antriebswelle überträgt die Kraft auf das Ritzel und treibt dann das große Zahnrad 12 an, um die Türscheibe nach oben und unten zu drücken .
Die Stanzteile sind aus 1,5 mm starken Stahlplatten gestanzt, um eine ausreichende Steifigkeit und Festigkeit zu gewährleisten.
Die Hauptverbindungsabmessungen des inneren Hohlraums des Gehäuses betragen 16,5 mm, 22,3 mm und 16 mm sind IT11-IT12.
Die Genauigkeit des Mittelkreisdurchmessers der drei kleinen Löcher φ 3,2 mm beträgt 42 ± 0,1 mm. Nach der technischen Analyse der Stanzteile sollte der Innendurchmesser von φ 22,3 mm positioniert und die hochpräzise Matrize (IT7 oder höher) gleichzeitig in einem Arbeitsgang ausgestanzt werden.
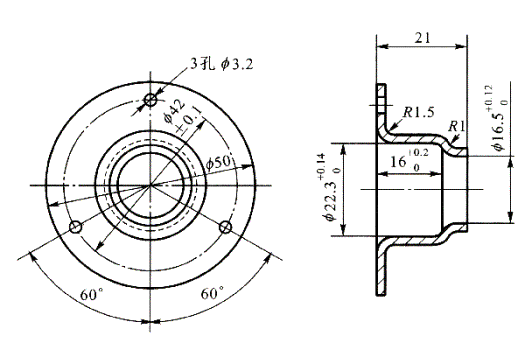
Abbildung 8.2.1 Metallgehäuse des Glashebers
Abbildung 8.2.2 Montageplan des Glashebergehäuses
8.2.2 Bestimmung des Prägeprozesses
ein. Analyse und Vergleich von Prozessplänen
Die Form des Außengehäuses weist darauf hin, dass es sich um ein Tiefziehteil handelt. Das Ziehen ist also ein grundlegender Vorgang.
Die drei kleinen Löcher im Flansch werden durch einen Stanzvorgang vervollständigt.
Das Formen des Teils φ 16,5 mm (siehe die rechte Seite von Abbildung 8.2.1) kann auf drei Arten erfolgen:
1, kann das tiefe Zeichnen des Schrittes verwenden und zur Unterseite sich drehen;
2, nachdem das Schritttiefziehen verwendet werden kann, entfernt das Stempeln den Boden;
3, können Sie die Methode des Zeichnens, des Lochens des unteren Lochs und dann des Bördelns verwenden. (Siehe Abbildung 8.2.3)
Die erste Methode hat eine höhere Qualität am Ende des Drehens, aber eine geringere Produktivität. Die Verwendung ist nicht einfach, wenn der Boden des Teils nicht hoch ist.
Bei der zweiten Methode muss der Radius der Bodenverrundung vor dem Stanzen nahe Null sein, um den Boden zu entfernen. Daher ist ein zusätzlicher Formgebungsprozess erforderlich und die Qualität kann nicht ohne weiteres garantiert werden.
Bei der dritten Methode ist zwar die Qualität des Flanschendes nicht so gut wie bei den ersten beiden, aber die Produktionseffizienz ist hoch und das Material wird geschont.
Da die Toleranz des Gehäusehöhenmaßes von 21 mm nicht hoch ist, kann der Bördelvorgang die technischen Anforderungen der Teile vollständig gewährleisten, so dass es sinnvoll ist, die Methode des Tiefziehens und anschließenden Stanzens und Bördelns anzuwenden.
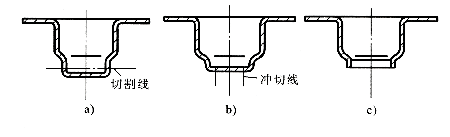
Abbildung 8.2.3 Formschema am Boden des Gehäuses
ein Schnitt; b) Stanzen; c) Stanzen Bördeln
zwei. Festlegung des Prozessplans
• Blankgröße berechnen
Vor der Berechnung der Rohteilgröße müssen Form und Größe des Halbzeugs vor dem Bördeln bestimmt und der Verformungsgrad des Bördelns berechnet werden. Bezugnehmend auf FIG. 8.2.1 beträgt die Höhenabmessung der Teile bei φ 16,5 mm: H = 21-16 = 5 mm.
Nach der Berechnungsformel des Bördelprozesses beträgt der Bördelkoeffizient K:

Die Flanschhöhe H = 5 mm; Manschettendurchmesser D = 16,5 + 1,5 = 18 mm; Biegeradius r = 1 mm; Materialstärke t = 1,5 mm in die obige Gleichung ein, um den Koeffizientenflansch zu erhalten:

Vorgestanzter Lochdurchmesser d = DK = 11 mm, d / t = 11 / 1,5 = 7,33
Überprüfen Sie den Grenzwert des Bördelkoeffizienten. Wenn der Vorstempel mit einem zylindrischen Stempel gestanzt wird, ist der Grenzflankbeiwert [K] = 0,5. Jetzt 0,61> 0,5 ist es möglich, eine Höhe von H = 5 mm durch direktes Umbördeln nach dem Stanzen zu erreichen. Form und Abmessungen der Ziehteile vor dem Bördeln sind in Abbildung 8.2.4 dargestellt.
Beim Zeichnen mit einem Zeichnungskoeffizienten nahe dem Grenzwert muss ein größerer Radius verwendet werden, um die Qualität der Zeichnung zu gewährleisten. Gegenwärtig beträgt die Materialstärke des Teils t = 1,5 mm, der Radius der Verrundung beträgt r = 2,55 mm, was ungefähr 1,5 t ist, was zu klein ist, und der Durchmesser des Teils ist klein. Es ist schwierig, die Anforderungen der Teile durch zwei Tiefziehverfahren zu erfüllen. Daher ist es notwendig, nach zwei Tiefziehvorgängen einen Formgebungsprozess durchzuführen, um einen kleineren Radius für die Mündung und den Boden zu erhalten.
In der Praxis können drei Tiefziehverfahren angewendet werden, um den Radius der Rundung zu verringern. Der Gesamtziehkoeffizient m total = 0,366 wird dem Dreiwege-Ziehprozess zugewiesen und m 1 = 0,56, m 2 = 0,805, m 3 = 0,812 können ausgewählt werden.
m 1 × m 2 × m 3 = 0,56 × 0,805 × 0,812 = 0,366
3 . Prozesskombination und Sequenzbestimmung
Für die Stanzteile mit vielen Prozessen wie dem Außenmantel kann zuerst der Grundprozess der Teile bestimmt und dann die mögliche Kombinationssortierung aller Grundprozesse in Betracht gezogen werden. Die verschiedenen auf diese Weise erhaltenen Verfahrensschemata werden analysiert und verglichen, woraus die beste für die tatsächliche Produktion geeignete Lösung bestimmt wird.
Der grundlegende Prozess des Außengehäuses ist:
Stanzen φ 65 mm, erstes Ziehen,
Das zweite Tiefziehen (siehe Abbildung 8-11b),
Das dritte Tiefziehen (siehe Abbildung 8.2.5c) und das Bodenloch φ 11 mm (siehe Abbildung 8.2.5d),
Bördelung φ 16,5 mm (siehe Abbildung 8.2.5e),
Stanzen Sie drei kleine Löcher φ 3,2 mm (siehe Abbildung 8.2.5f).
Beschneiden φ 50 mm (siehe Abbildung 8.2.5g).
Insgesamt acht grundlegende Prozesse, nach denen die folgenden fünf Prozessoptionen ausgeführt werden können:
Option 1: Die Austastung wird mit der ersten Zeichnung kombiniert (siehe Abbildung 8.2.5a), und der Rest basiert auf dem Grundprozess.
Option II:
Die Stanzung wird mit der ersten Zeichnung kombiniert, und das untere Loch mit einem Durchmesser von 11 mm wird mit dem Flansch kombiniert (siehe Abbildung 8.2.6a). Die drei kleinen Löcher φ 3,2 mm werden mit dem Beschneiden kombiniert (siehe Abbildung 8.2.6b), der Rest basiert auf dem Grundprozess. .
dritte Lösung:
Die Ausblendung wird mit der ersten Zeichnung kombiniert, und das untere Loch mit einem Durchmesser von 11 mm wird mit den drei kleinen Löchern mit einem Durchmesser von 3,2 mm kombiniert (siehe Abbildung 8.2.7a). Der Flansch wird mit der Verkleidung beschnitten (siehe Abbildung 8.2.7b), der Rest basiert auf dem Grundprozess.
Option 4:
Stanzen, erstmaliges Tiefziehen und Stanzen φ 11 mm Bodenlochverbund (siehe Abbildung 8.2.8), der Rest nach dem Grundverfahren. Option 5: Verwenden Sie den Folgeverbundstempel oder das Stempeln auf einer automatischen Presse mit mehreren Stationen.
Analyse und Vergleich der obigen fünf Schemata zeigen, dass in Schema 2 das Loch mit einem Stanzdurchmesser von 11 mm aufgrund der geringen Dicke der Formwand mit dem Flansch kombiniert ist
mm,It is smaller than the minimum wall thickness of 3.8 mm between the convex and concave molds, and the mold is easily damaged. Punching three small holes φ 3.2 mm combined with trimming, there is also the problem that the mold wall is too thin. at this timemm, Therefore, it should not be used.
mm, Sie ist kleiner als die Mindestwandstärke von 3,8 mm zwischen der konvexen und der konkaven Form und die Form kann leicht beschädigt werden. Beim Stanzen von drei kleinen Löchern ø 3,2 mm in Kombination mit dem Beschneiden besteht auch das Problem, dass die Formwand zu dünn ist. Zu diesem Zeitpunkt sollte
mm daher nicht verwendet werden.
In Option drei
Zwar löst sich der Widerspruch, dass die obige Formwand zu dünn ist. Wenn jedoch das untere Loch mit einem Durchmesser von 11 mm mit den drei kleinen Löchern mit einem Durchmesser von 3,2 mm kombiniert wird und der Flansch und die Verkleidung kombiniert werden, liegen ihre Schneidkanten nicht in der gleichen Ebene, und die Verschleißgeschwindigkeit ist unterschiedlich. Dies kann zu Unannehmlichkeiten beim Schleifen führen, und es ist schwierig, die relative Position nach dem Schleifen beizubehalten.
In Option vier
Stanzen, Erstes Tiefziehen und Stanzen φ 11 mm-Grundlochverbund, Stanzstempel und Tiefziehstempel sind integriert, was auch beim Schleifen zu Schwierigkeiten führt. Insbesondere nachdem das Bodenloch zwei- und dreimal gebohrt wurde, wirkt sich eine Änderung des Lochdurchmessers auf die Höhenabmessung des Flansches und die Qualität des Flanschabschnitts aus.
Das fünfte Schema verwendet eine progressive Düse oder eine automatische Zuführvorrichtung mit mehreren Stationen, die eine hohe Produktionseffizienz aufweist. Die Formstruktur ist komplex, der Herstellungszyklus ist lang und die Kosten sind hoch. Daher ist es nur für die Massenproduktion geeignet.
Schema 1 weist die oben genannten Mängel nicht auf, aber der Compoundierungsgrad ist niedrig und die Produktionseffizienz ist niedrig. Die Einzelprozessform weist jedoch einen einfachen Aufbau und niedrige Herstellungskosten auf, was bei der Produktion kleiner und mittlerer Chargen angemessen ist, so dass entschieden wird, das erste Schema anzuwenden. Beim dritten Tiefzieh- und Bördelvorgang kann die Form, wenn sich der Stanzhub dem Ende nähert, fest gegen das Werkstück gedrückt werden, um einen Formungseffekt zu erzielen, so dass kein zusätzlicher Formungsvorgang erforderlich ist.
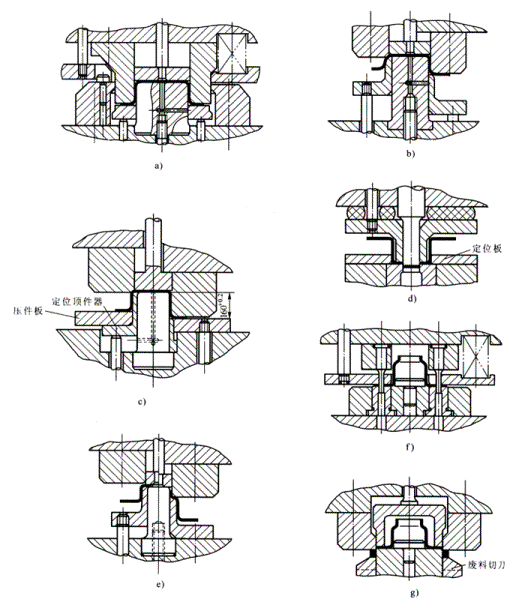
Abbildung 8.2.5 Design Stempeln Formstruktur für jeden Prozess
Das material ist 08 stahlplatte, platte dicke 1,5mm, massenproduktion.
Stempelfertigung erfordert die Vorbereitung eines Stempelfertigungsprozesses.
8.2.1 Prozessanalyse von Stanzteilen
Zunächst müssen Sie die Anwendung und die technischen Anforderungen des Produkts vollständig verstehen und eine Prozessanalyse durchführen.
Das Glas an der Autotür wird vom Lifter angehoben oder abgesenkt.
Das Zusammenbaudiagramm der Lifterkomponenten ist in Abbildung 8.2.2 dargestellt. Das Stanzteil ist der Außenmantel 5 davon. Der Getriebemechanismus des Aufzugs ist im Außengehäuse untergebracht und durch drei gleichmäßig verteilte kleine Löcher ø 3,2 mm am Außengehäuseflansch mit der Türsitzplatte vernietet. Die Antriebswelle 6 ist am Stützabschnitt des rechten Endlochs φ 16,5 mm mit dem Abstand von I T11 montiert. Die Bremsdrehfeder 3, das Verbindungsstück 9 und die Spindel 4 sind mit dem Ritzel 11 gekoppelt, um den Griff 7 zu kippen. Die Antriebswelle überträgt die Kraft auf das Ritzel und treibt dann das große Zahnrad 12 an, um die Türscheibe nach oben und unten zu drücken .
Die Stanzteile sind aus 1,5 mm starken Stahlplatten gestanzt, um eine ausreichende Steifigkeit und Festigkeit zu gewährleisten.
Die Hauptverbindungsabmessungen des inneren Hohlraums des Gehäuses betragen 16,5 mm, 22,3 mm und 16 mm sind IT11-IT12.
Um die Koaxialität zwischen Trägerteil und Hülse nach dem Nieten und Fixieren zu gewährleisten. Die relative Position zwischen den drei kleinen Löchern mit einem Durchmesser von 3,2 mm und einem Durchmesser von 16,5 mm ist genau, und der Durchmesser des Mittelkreises für kleine Löcher beträgt 42 ± 0,1 mm. T10-Ebene.
Dieser Teil ist ein rotierender Körper, dessen Form durch ein angeflanschtes zylindrisches Stück gekennzeichnet ist.
Die Hauptform und -größe kann durch einen Ziehvorgang wie Ziehen, Bördeln, Stanzen und dergleichen erhalten werden.
Als Zeichengröße sind die relativen Werte geeignet und der Zeichenprozess ist besser.
Die Toleranzanforderungen für φ 22,3 mm und 16 mm sind zu hoch. Der Radius der Verrundung am Boden und an der Mündung des Tiefziehteils ist ebenfalls klein, daher sollte er nach dem Ziehen hinzugefügt und die Form mit hoher Präzision und kleinem Spalt verwendet werden.
Dieser Teil ist ein rotierender Körper, dessen Form durch ein angeflanschtes zylindrisches Stück gekennzeichnet ist.
Die Hauptform und -größe kann durch einen Ziehvorgang wie Ziehen, Bördeln, Stanzen und dergleichen erhalten werden.
Als Zeichengröße sind die relativen Werte geeignet und der Zeichenprozess ist besser.
Die Toleranzanforderungen für φ 22,3 mm und 16 mm sind zu hoch. Der Radius der Verrundung am Boden und an der Mündung des Tiefziehteils ist ebenfalls klein, daher sollte er nach dem Ziehen hinzugefügt und die Form mit hoher Präzision und kleinem Spalt verwendet werden.
Die Genauigkeit des Mittelkreisdurchmessers der drei kleinen Löcher φ 3,2 mm beträgt 42 ± 0,1 mm. Nach der technischen Analyse der Stanzteile sollte der Innendurchmesser von φ 22,3 mm positioniert und die hochpräzise Matrize (IT7 oder höher) gleichzeitig in einem Arbeitsgang ausgestanzt werden.
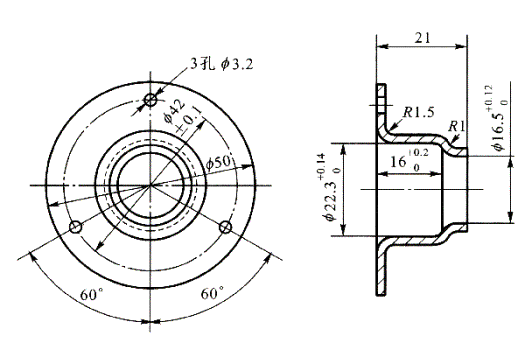
Abbildung 8.2.1 Metallgehäuse des Glashebers
Abbildung 8.2.2 Montageplan des Glashebergehäuses
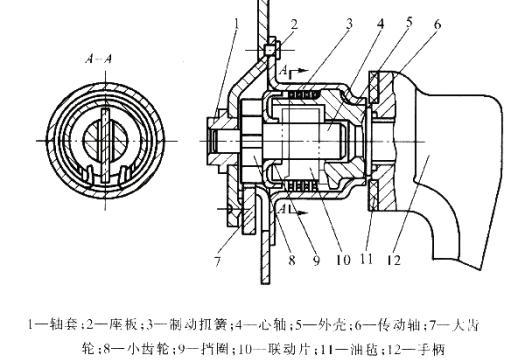
1, Buchsen. 2, Sitzplatte. 3, Bremsendrehfeder. 4, der Dorn. 5 das äußere Gehäuse. 6 die Antriebswelle. 7, großes Zahnrad. 8, Ritzel. 9 den Haltering. 10, Verknüpfungsfilm. 11, Linoleum. 12 ist der Griff
8.2.2 Bestimmung des Prägeprozesses
ein. Analyse und Vergleich von Prozessplänen
Die Form des Außengehäuses weist darauf hin, dass es sich um ein Tiefziehteil handelt. Das Ziehen ist also ein grundlegender Vorgang.
Die drei kleinen Löcher im Flansch werden durch einen Stanzvorgang vervollständigt.
Das Formen des Teils φ 16,5 mm (siehe die rechte Seite von Abbildung 8.2.1) kann auf drei Arten erfolgen:
1, kann das tiefe Zeichnen des Schrittes verwenden und zur Unterseite sich drehen;
2, nachdem das Schritttiefziehen verwendet werden kann, entfernt das Stempeln den Boden;
3, können Sie die Methode des Zeichnens, des Lochens des unteren Lochs und dann des Bördelns verwenden. (Siehe Abbildung 8.2.3)
Die erste Methode hat eine höhere Qualität am Ende des Drehens, aber eine geringere Produktivität. Die Verwendung ist nicht einfach, wenn der Boden des Teils nicht hoch ist.
Bei der zweiten Methode muss der Radius der Bodenverrundung vor dem Stanzen nahe Null sein, um den Boden zu entfernen. Daher ist ein zusätzlicher Formgebungsprozess erforderlich und die Qualität kann nicht ohne weiteres garantiert werden.
Bei der dritten Methode ist zwar die Qualität des Flanschendes nicht so gut wie bei den ersten beiden, aber die Produktionseffizienz ist hoch und das Material wird geschont.
Da die Toleranz des Gehäusehöhenmaßes von 21 mm nicht hoch ist, kann der Bördelvorgang die technischen Anforderungen der Teile vollständig gewährleisten, so dass es sinnvoll ist, die Methode des Tiefziehens und anschließenden Stanzens und Bördelns anzuwenden.
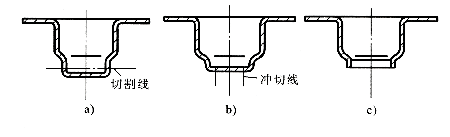
Abbildung 8.2.3 Formschema am Boden des Gehäuses
ein Schnitt; b) Stanzen; c) Stanzen Bördeln
zwei. Festlegung des Prozessplans
• Blankgröße berechnen
Vor der Berechnung der Rohteilgröße müssen Form und Größe des Halbzeugs vor dem Bördeln bestimmt und der Verformungsgrad des Bördelns berechnet werden. Bezugnehmend auf FIG. 8.2.1 beträgt die Höhenabmessung der Teile bei φ 16,5 mm: H = 21-16 = 5 mm.
Nach der Berechnungsformel des Bördelprozesses beträgt der Bördelkoeffizient K:

Die Flanschhöhe H = 5 mm; Manschettendurchmesser D = 16,5 + 1,5 = 18 mm; Biegeradius r = 1 mm; Materialstärke t = 1,5 mm in die obige Gleichung ein, um den Koeffizientenflansch zu erhalten:

Vorgestanzter Lochdurchmesser d = DK = 11 mm, d / t = 11 / 1,5 = 7,33
Überprüfen Sie den Grenzwert des Bördelkoeffizienten. Wenn der Vorstempel mit einem zylindrischen Stempel gestanzt wird, ist der Grenzflankbeiwert [K] = 0,5. Jetzt 0,61> 0,5 ist es möglich, eine Höhe von H = 5 mm durch direktes Umbördeln nach dem Stanzen zu erreichen. Form und Abmessungen der Ziehteile vor dem Bördeln sind in Abbildung 8.2.4 dargestellt.
Beim Zeichnen mit einem Zeichnungskoeffizienten nahe dem Grenzwert muss ein größerer Radius verwendet werden, um die Qualität der Zeichnung zu gewährleisten. Gegenwärtig beträgt die Materialstärke des Teils t = 1,5 mm, der Radius der Verrundung beträgt r = 2,55 mm, was ungefähr 1,5 t ist, was zu klein ist, und der Durchmesser des Teils ist klein. Es ist schwierig, die Anforderungen der Teile durch zwei Tiefziehverfahren zu erfüllen. Daher ist es notwendig, nach zwei Tiefziehvorgängen einen Formgebungsprozess durchzuführen, um einen kleineren Radius für die Mündung und den Boden zu erhalten.
In der Praxis können drei Tiefziehverfahren angewendet werden, um den Radius der Rundung zu verringern. Der Gesamtziehkoeffizient m total = 0,366 wird dem Dreiwege-Ziehprozess zugewiesen und m 1 = 0,56, m 2 = 0,805, m 3 = 0,812 können ausgewählt werden.
m 1 × m 2 × m 3 = 0,56 × 0,805 × 0,812 = 0,366
3 . Prozesskombination und Sequenzbestimmung
Für die Stanzteile mit vielen Prozessen wie dem Außenmantel kann zuerst der Grundprozess der Teile bestimmt und dann die mögliche Kombinationssortierung aller Grundprozesse in Betracht gezogen werden. Die verschiedenen auf diese Weise erhaltenen Verfahrensschemata werden analysiert und verglichen, woraus die beste für die tatsächliche Produktion geeignete Lösung bestimmt wird.
Der grundlegende Prozess des Außengehäuses ist:
Stanzen φ 65 mm, erstes Ziehen,
Das zweite Tiefziehen (siehe Abbildung 8-11b),
Das dritte Tiefziehen (siehe Abbildung 8.2.5c) und das Bodenloch φ 11 mm (siehe Abbildung 8.2.5d),
Bördelung φ 16,5 mm (siehe Abbildung 8.2.5e),
Stanzen Sie drei kleine Löcher φ 3,2 mm (siehe Abbildung 8.2.5f).
Beschneiden φ 50 mm (siehe Abbildung 8.2.5g).
Insgesamt acht grundlegende Prozesse, nach denen die folgenden fünf Prozessoptionen ausgeführt werden können:
Option 1: Die Austastung wird mit der ersten Zeichnung kombiniert (siehe Abbildung 8.2.5a), und der Rest basiert auf dem Grundprozess.
Option II:
Die Stanzung wird mit der ersten Zeichnung kombiniert, und das untere Loch mit einem Durchmesser von 11 mm wird mit dem Flansch kombiniert (siehe Abbildung 8.2.6a). Die drei kleinen Löcher φ 3,2 mm werden mit dem Beschneiden kombiniert (siehe Abbildung 8.2.6b), der Rest basiert auf dem Grundprozess. .
dritte Lösung:
Die Ausblendung wird mit der ersten Zeichnung kombiniert, und das untere Loch mit einem Durchmesser von 11 mm wird mit den drei kleinen Löchern mit einem Durchmesser von 3,2 mm kombiniert (siehe Abbildung 8.2.7a). Der Flansch wird mit der Verkleidung beschnitten (siehe Abbildung 8.2.7b), der Rest basiert auf dem Grundprozess.
Option 4:
Stanzen, erstmaliges Tiefziehen und Stanzen φ 11 mm Bodenlochverbund (siehe Abbildung 8.2.8), der Rest nach dem Grundverfahren. Option 5: Verwenden Sie den Folgeverbundstempel oder das Stempeln auf einer automatischen Presse mit mehreren Stationen.
Analyse und Vergleich der obigen fünf Schemata zeigen, dass in Schema 2 das Loch mit einem Stanzdurchmesser von 11 mm aufgrund der geringen Dicke der Formwand mit dem Flansch kombiniert ist
mm,It is smaller than the minimum wall thickness of 3.8 mm between the convex and concave molds, and the mold is easily damaged. Punching three small holes φ 3.2 mm combined with trimming, there is also the problem that the mold wall is too thin. at this timemm, Therefore, it should not be used.
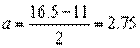
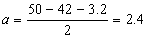
In Option drei
Zwar löst sich der Widerspruch, dass die obige Formwand zu dünn ist. Wenn jedoch das untere Loch mit einem Durchmesser von 11 mm mit den drei kleinen Löchern mit einem Durchmesser von 3,2 mm kombiniert wird und der Flansch und die Verkleidung kombiniert werden, liegen ihre Schneidkanten nicht in der gleichen Ebene, und die Verschleißgeschwindigkeit ist unterschiedlich. Dies kann zu Unannehmlichkeiten beim Schleifen führen, und es ist schwierig, die relative Position nach dem Schleifen beizubehalten.
In Option vier
Stanzen, Erstes Tiefziehen und Stanzen φ 11 mm-Grundlochverbund, Stanzstempel und Tiefziehstempel sind integriert, was auch beim Schleifen zu Schwierigkeiten führt. Insbesondere nachdem das Bodenloch zwei- und dreimal gebohrt wurde, wirkt sich eine Änderung des Lochdurchmessers auf die Höhenabmessung des Flansches und die Qualität des Flanschabschnitts aus.
Das fünfte Schema verwendet eine progressive Düse oder eine automatische Zuführvorrichtung mit mehreren Stationen, die eine hohe Produktionseffizienz aufweist. Die Formstruktur ist komplex, der Herstellungszyklus ist lang und die Kosten sind hoch. Daher ist es nur für die Massenproduktion geeignet.
Schema 1 weist die oben genannten Mängel nicht auf, aber der Compoundierungsgrad ist niedrig und die Produktionseffizienz ist niedrig. Die Einzelprozessform weist jedoch einen einfachen Aufbau und niedrige Herstellungskosten auf, was bei der Produktion kleiner und mittlerer Chargen angemessen ist, so dass entschieden wird, das erste Schema anzuwenden. Beim dritten Tiefzieh- und Bördelvorgang kann die Form, wenn sich der Stanzhub dem Ende nähert, fest gegen das Werkstück gedrückt werden, um einen Formungseffekt zu erzielen, so dass kein zusätzlicher Formungsvorgang erforderlich ist.
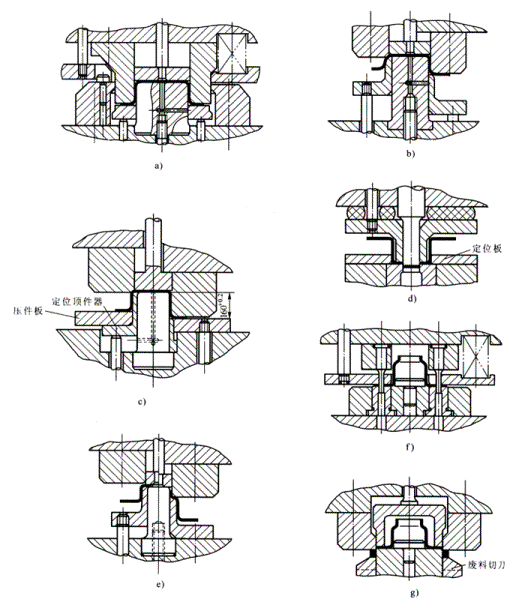
Abbildung 8.2.5 Design Stempeln Formstruktur für jeden Prozess