GM-Huelsen-Teil-Herstellungsprozess-Analyse
Die Werkstücklänge beträgt 46mm; die äußere Kreisgröße beträgt 64 mm und die Rauheitsanforderung ist Ra 1,6, was eine Endbearbeitung erfordert;
Innenloch: Das linke Ende ist eine Länge von 23 mm (einschließlich C1.5-Fase),
Nenndurchmesser 27 mm, Steigung 1,5, Toleranzklasse 6H gewöhnliche Gewinde; das rechte Ende ist ein konisches Loch mit einer Neigung von 1: 5. Bei den abgerundeten Ecken von R6 beträgt die Rauheit der Verjüngung Ra1,6 und erfordert eine Endbearbeitung.
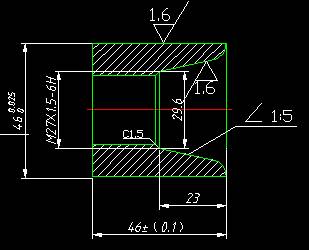
Die Figur zeigt ein einfaches Hülsenteil, bei dem eine Mehrzahl von Durchmesserdimensionen und axialen Abmessungen höhere Anforderungen an die Maßhaltigkeit und die Oberflächenrauhigkeit haben und die Dimension des Teils vollständig markiert ist, was die Anforderungen an die Dimensionierung der NC erfüllt Bearbeitung;
Die Konturbeschreibung ist klar und vollständig; Das Material des Teils ist Stahl Nr. 45, und die Bearbeitungs- und Schneidleistung ist gut. Die Wärmebehandlung: Modulationsbehandlung, HRC25-35 hat keine Anforderungen an die Härte.
Hülsenteil ist eine maschinell bearbeitete Form der Bearbeitung. Zusätzlich zu der Größe und Formgenauigkeit des Hülsenteils wird das innere Loch allgemein als eine Referenz für die Montage verwendet. die Lochdurchmesser-Toleranzklasse ist im Allgemeinen IT7, die Präzisionsbuchse kann IT6 einnehmen, und die Lochformgenauigkeit muss innerhalb der Öffnungstoleranz gesteuert werden.
Bei längeren Büchsen müssen zusätzlich zu den Rundheitsanforderungen die Zylindrizität der inneren Lochfläche, der Rundlauf und die Vertikalität der inneren Lochachse der Stirnfläche sowie die Parallelität der beiden Stirnflächen berücksichtigt werden.
(B) Klemmlösung des Hülsenteils
Der Hülsenteil innerhalb und außerhalb des Kreises, die Endfläche und die Bezugsachse haben gewisse Genauigkeitsanforderungen, der Umrißteil der Feinreferenz kann den äußeren Kreis wählen, aber oft mit der Mittellinie und einer Endfläche für die Endbezugsreferenz . Für verschiedene Teile der Struktur ist es nicht möglich, ein Prozessschema zu verwenden, um seine Genauigkeitsanforderungen zu gewährleisten.
Entsprechend den konstruktiven Merkmalen des Hülsenteils können Dreibackenfutter, Vierbackenfutter oder Stirnplattenklemmung bei der CNC-Bearbeitung eingesetzt werden. Aufgrund des Fehlers in der Zentriergenauigkeit der Backenfutter ist es nicht zum Nachspannen von Werkstücken mit hohen Koaxialitätsanforderungen geeignet. Beim Dreibacken-Einspannen kann der Hülsenteil einmal bearbeitet werden, um die inneren und äußeren Kreisendflächen zu vervollständigen, zu fasen und zu schneiden. Größere Teile verwenden häufig Vier-Krallen- oder Plattenklemmung; Für weiche Teile kann eine weiche Backenspannung verwendet werden. Klemmung kann auch auf der Spindel verwendet werden; Bei einem komplexeren Hülsenteil werden manchmal spezielle Befestigungen zum Klemmen verwendet.
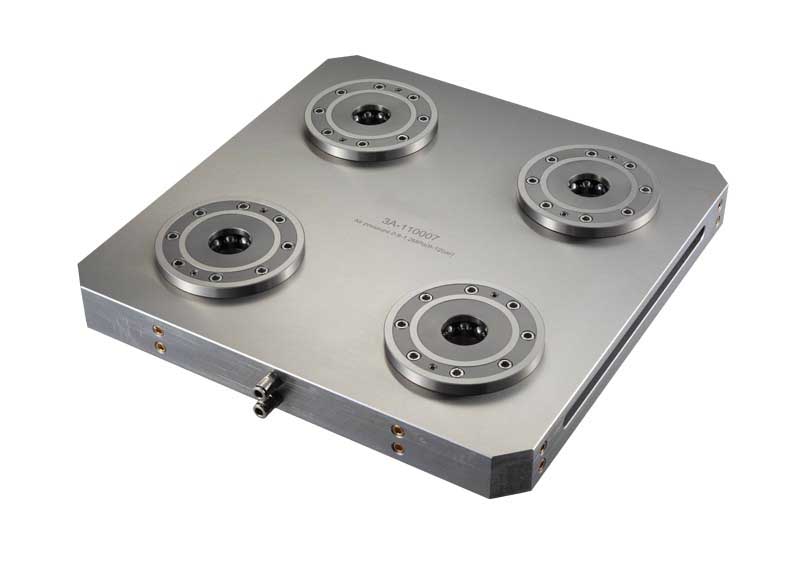
zylindrisches äußeres Hülsenteilbearbeitungswerkzeug, selbe wie Wellenteile. Die Verarbeitung der inneren Bohrung ist eines der Merkmale des Hülsenteils. Entsprechend den Prozessanforderungen für den Innenlochprozess gibt es viele Bearbeitungsmethoden wie Bohren, Reiben, Bohren, Schleifen, Ziehen von Löchern und Schleifen von Löchern.
hülsenteil umfasst im allgemeinen interne und externe kreise, kegel, bögen, schlitze, löcher, fäden und andere strukturen. Entsprechend den verarbeitung anforderungen, die allgemein verwendeten werkzeuge umfassen bohren bohrwerkzeuge, feine bohren werkzeuge, interne bohrwerkzeuge, innengewindedrehen werkzeuge und speziell geformte Drehwerkzeuge.
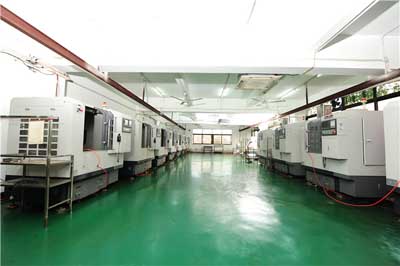
(D) Auswahl der Schnittmenge
Entsprechend den Anforderungen an die Oberflächenqualität, Werkzeugmaterial und Werkstückmaterial, siehe Schnittdaten - Handbuch oder zugehörige Daten zur Auswahl der Schnittgeschwindigkeit und des Vorschubs pro Umdrehung, Berechnung der Spindeldrehzahl und des Vorschubs (der Berechnungsprozess entfällt) und Füllen der Ergebnisse in die Prozesskarte.
Die Wahl der Schnitttiefe variiert je nach Grob- und Feinbearbeitung. Wenn die Steifigkeit des Prozesssystems und die Leistung der Maschine während des Schruppen erlauben, nehmen Sie eine möglichst große Schnitttiefe, um die Anzahl der Zuführungen zu reduzieren. Um die Oberflächenrauheit der Teile zu gewährleisten, beträgt die Schnitttiefe bei der Fertigbearbeitung im Allgemeinen 0,1-0,4 mm.
(E) Auswahl der Schneidflüssigkeit
Der Hülsenteil hat größere Schwierigkeiten bei der CNC-Bearbeitung als Wellenteile. Aufgrund der Merkmale des Hülsenteils ist das Schneidfluid nicht leicht in den Schneidbereich zu erreichen, die Schneidflächentemperatur ist hoch und der Verschleiß des Schneidwerkzeugs ist relativ ernst. Um die Bearbeitungsverzerrung des Werkstücks zu reduzieren und die Bearbeitungsgenauigkeit zu verbessern, sollte eine geeignete Schneidflüssigkeits-Gießposition gemäß verschiedenen Werkstückmaterialien ausgewählt werden.
(F) Füllen Sie Verarbeitungswerkzeuge und Operationskarten aus
(1) Gemäß der Verarbeitungssequenz werden die Verarbeitungsinhalte jedes Schritts, das verwendete Werkzeug und die Menge an Schnittgut usw. in die CNC-Bearbeitungs-Prozesskarte gefüllt.
(2) Fügen Sie für jeden Schritt den Werkzeugtyp, den Einlegetyp, die Klingennummer und den Spitzenradius des ausgewählten Werkzeugs in die CNC-Werkzeugkarte ein.
(3) Zeichnen der Route jedes Arbeitsschritts in einen Dateipfadplan.
CNC-Werkzeugkarte
Produktname und -code |
Beispiele für CNC-Drehtechnologie |
Teilname |
Überwurfmutter |
Artikelnummer |
|
Programmnummer |
|
||||||||||||
Schrittnummer |
Werkzeugnummer |
Werkzeugspezifikation und Name (mm) |
Menge |
Bearbeitungsfläche |
Schneidenradius (mm) |
Hinweis |
|||||||||||||
1 |
T01 |
45 ° externes Drehwerkzeug1 |
Drehende Stirnfläche und zylindrische Oberfläche |
0.5 |
|
||||||||||||||
2 |
T02 |
Ø4 Zentrierbohrer |
1 |
Bohrung Ø4 bohren |
|
|
|||||||||||||
3 |
T03 |
Ø 23.5 Spiralbohrer |
1 |
Bohren |
|
|
|||||||||||||
4 |
T04 |
Bohrwerkzeug |
1 |
Grobe Bohrung und innere konische Fläche |
0.4 |
|
|||||||||||||
5 |
T05 |
Bohrwerkzeug |
1 |
Feine Bohrung und innere konische Fläche |
0.2 |
|
|||||||||||||
6 |
T06 |
Innengewindedrehwerkzeug |
1 |
Drehen der Innengewinde- und Gewindebohrungsfase |
0.3 |
|
|||||||||||||
hergestellt von |
Liu Xin |
Rezension |
|
Genehmigt |
|
Insgesamt eine Seite |
Erste Seite |
CNC-Bearbeitungskarte
Kangding metal |
CNC-Bearbeitungskarte |
Produktname oder -code |
einstellen |
Materialien |
Artikelnummer |
|||||||||||||||||
Beispiele für CNC-Drehtechnologie |
Kegelmuttersatz |
45 # Stahl |
|
|||||||||||||||||||
Angestellten ID |
Programmnummer |
Geräte-Nummer |
Verwenden Sie Ausrüstung |
|
Werkstatt |
|||||||||||||||||
|
O0010 |
|
CK6140 |
|
CNC Center |
|||||||||||||||||
Schrittnummer |
Schritt Inhalt |
Werkzeugnummer |
Werkzeugspezifikationen (mm) |
Spindeldrehzahl (U / min) |
Vorschubgeschwindigkeit f / (mm / r) |
Schnitttiefe ap / mm |
Hinweis |
|||||||||||||||
1 |
Flache Endfläche |
T01 |
25×25 |
350 |
|
1 |
Manuell
|
|||||||||||||||
2 |
Zentrierbohrung bohren |
T02 |
Ø4 |
800 |
|
2 |
Manuell |
|||||||||||||||
3 |
Bohren |
T03 |
Ø 20 |
200 |
|
15 |
Manuell | |||||||||||||||
4 |
Schwerer Bohrlochkreis (invertierter) Winkel und Steigung |
T04 |
20×20 |
500 |
40 |
0.8 |
automatisch |
|||||||||||||||
5 |
Innenlochbohrung rechts und innen, garantierte Steilheit (1: 5), Ra6 |
T05 |
20×20 |
800 |
40 |
0.2 |
automatisch |
|||||||||||||||
6 |
grobe äußere Oberfläche zu drehen |
T01 |
25×25 |
500 |
40 |
1.5 |
automatisch |
|||||||||||||||
7 |
Drehen Sie die andere Seite des Autos, um die Länge zu gewährleisten |
T01 |
25×25 |
500 |
|
|
Manuell |
|||||||||||||||
8 |
grob drehendes Innengewinde |
T06 |
16×16 |
500 |
|
0.4 |
automatisch |
|||||||||||||||
9 |
Innengewinde drehen |
T06 |
16×16 |
800 |
|
0.1 |
automatisch | |||||||||||||||
10 |
Endbearbeitung der äußeren Oberfläche |
T01 |
25×25 |
1000 |
|
|
Manuell |
|||||||||||||||
hergestellt von |
Liu Xin |
|
|
Genehmigt |
|
Insgesamt eine Seite |
Erste Seite |
Tabelle 4-4
(g) Verarbeitungsprogrammierung der HülsenteileO0010 Programmnummer
N001 G21 G99 G97 G40; Initialisierungsprozedur
N002 M03 S500 T0404; Spindeldrehung, Geschwindigkeit 500, Nr. 4 Messer und Werkzeugkompensation
N003 G00 X23 Z2; Schneller Positionierzyklus Start (23,2)
N004 G71 U1.0 R0.5; Raue Bohrung
N005 G71 P006 Q014 U-0,3 W0,1 F0,15; Rohbohren, X-Richtung Rand 0,3 mm, Z-Richtung Rand 0,1 mm
N006 G00 X46 Z2; Annäherung an die zu bearbeitende Oberfläche
N007 G01 Z0; Annäherung an die zu bearbeitende Oberfläche
N008 G02 X34 Z-6 R6; Gegen den Uhrzeigersinn drehen auf (34, -6), Radius: R6
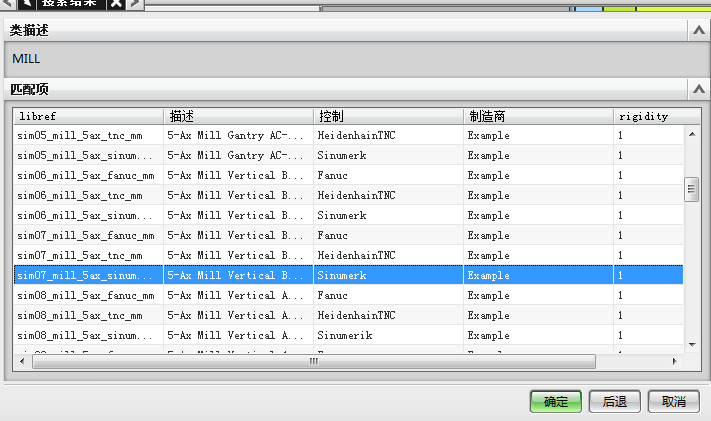
N09 G01 X29.6 Z-23; Gerader Weg zum Punkt (29.6, -23)
N010 X26.55; Gerade zu Punkt (26.55, -23)
N011 X25.05 Z-24.5; Gerader Weg zum Punkt (25.05, -24.5)
N012 Z-46; Gerade zu Punkt (25.05, -46)
N013 X0; Zurück zum Punkt (0, -46)
N014 G00 Z50; Schnelles Zurückziehen auf Z50
N015 X100; Zum Werkzeugwechselpunkt zurückfahren
N016 M05; Spindel steht fest
N017 G21 G97 G99 G40; Initialisierungsprozedur
N018 M03 S800 T0505; Spindelvorlauf, Geschwindigkeit 800, Werkzeug Nr. 5 und Werkzeugkorrektur
N019 G00 X23 Z2; Start des schnellen Positionierzyklus (23,2)
N020 G70 P006 Q014 F0.15; Feine Bohrung
N021 G00 X100; Zum Werkzeugwechselpunkt zurückfahren
N022 M05; Spindel stoppen
N023 G21 G97 G99 G40; Initialisierungsprozedur
N024 M03 S500 T0101; Spindeldrehzahl, Geschwindigkeit 500, Wechsel Nr. 1 Messer und Werkzeugkorrektur
N025 G00 X48Z2; Schnelle Positionierung
N026 G01 Z-32; Gerade zu Punkt (48, -32)
N027 U2 Gerade zum Punkt (50, -32)
N028 G00 Z2; Schnelle Positionierung zum Punkt (50,2)
N029 G01 X46.5; Gerader Weg zum Punkt (46.5,2)
N030 Z-32; Geradeaus zum Punkt (46,5, -32)
N031 U4; Gerade zu Punkt (50, -32)
N032 G00 Z2; Schnelle Positionierung zum Punkt (50,2)
N033 X100, Z50; Schnelle Positionierung zum Werkzeugwechselpunkt
N034 MO3; Spindel steht fest
N035 M05; Programm gestoppt
O0011 Programmnummer (Innengewinde drehen)
N001 G21 G99 G97 G40; Initialisierungsprozedur
N002 M03 S500 T0101; Spindeldrehung, Geschwindigkeit 500, Nr. 1 Messer und Werkzeugkompensation
N003 G00 X48Z2; Schnelle Positionierung
N004 G01 Z-32; Geradeaus zum Punkt (48, -32)
N026 M05; Programm gestoppt