Formulieren CNC-Dreh Prozess
3.1 Angemessene Auswahl von Werkzeugmaschinen
Am besten eignen sich CNC-Werkzeugmaschinen für die Bearbeitung von Teilen mit folgenden Eigenschaften:
(1) Teile für Multi-Varietät, Kleinserienproduktion oder Versuchsproduktion neuer Produkte.
(2) Teile mit komplexen Konturen oder hohen Anforderungen an die Bearbeitungsgenauigkeit.
(3) Bei der Bearbeitung mit normalen Werkzeugmaschinen werden Teile verwendet, die eine teure Prozessausrüstung (Werkzeuge, Vorrichtungen und Matrizen) erfordern.
(4) Teile, die viele Male geändert werden müssen.
(5) der Wert von teuren, kann nicht schief gehen, wenn Schlüsselteile bearbeitet werden.
(6) Dringend benötigte Teile mit dem kürzesten Produktionszyklus.
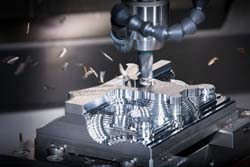
3.2 Prozessanalyse von CNC-Bearbeitungsteilen
(1) Die Größenangaben auf der Teilezeichnung sollten nach dem Prinzip der komfortablen Programmierung erfolgen
(2) Der strukturelle Ablauf jedes Teils des Teils sollte den Eigenschaften der numerischen Steuerungsverarbeitung entsprechen
3.3 Auswahl der Verarbeitungsmethoden und Festlegung der Bearbeitungspläne
(1) Auswahl der Verarbeitungsmethoden
Das Prinzip der Auswahl der Bearbeitungsmethoden ist: Gleichzeitig sind die Anforderungen an Bearbeitungsgenauigkeit und Oberflächenrauhigkeit gewährleistet. Außerdem sollten Produktivität und wirtschaftliche Anforderungen berücksichtigt werden. und die tatsächliche Situation der bestehenden Produktionsanlagen.
(2) Das Prinzip der Bestimmung des Bearbeitungsplans
Die Oberflächenbearbeitung mit hoher Präzision an Teilen wird oft durch Schruppen, Halbfertigbearbeitung und Endbearbeitung erreicht. Für diese Oberflächen wird der endgültige Arbeitsplan basierend auf Qualitätsanforderungen, Maschinenbedingungen und Knüppelbedingungen bestimmt.
Bei der Bestimmung des Bearbeitungsplans sollten zunächst die Verarbeitungsmethoden, die zum Erfüllen dieser Anforderungen erforderlich sind, zunächst gemäß den Anforderungen der Genauigkeit und der Oberflächenrauhigkeit der Hauptoberfläche bestimmt werden. An diesem Punkt müssen wir die Rationalität und Wirtschaftlichkeit des Einsatzes von CNC-Werkzeugmaschinen betrachten und den Funktionen von CNC-Werkzeugmaschinen volles Spiel verleihen. Im Prinzip führen CNC-Werkzeugmaschinen nur eine kompliziertere Teilebearbeitung und eine wichtige Referenzteilbearbeitung durch.
3.4 Aufteilung von Prozessen und Arbeitsschritten
(a) Aufteilung der Prozesse
(1) Der Prozess wird durch die Positionierung der Teile geteilt. Aufgrund der unterschiedlichen Formen jedes Teils unterscheiden sich die technischen Anforderungen jeder Oberfläche. Daher werden die Positionierungsmethoden in der Verarbeitung unterschiedlich sein. Wenn das Teil im Allgemeinen bearbeitet wird, wird die innere Form positioniert; Wenn die innere Struktur des Teils bearbeitet ist, wird die äußere Form positioniert. Der Prozess kann nach den verschiedenen Positionierungsmethoden unterteilt werden.
(2) durch die grobe und feine Bearbeitungsschrittteilung
Wenn der Prozess nach Faktoren wie der Bearbeitungsgenauigkeit, der Steifigkeit und der Verformung des Teils unterteilt wird, kann der Prozess nach dem Prinzip der Grob- und Feinbearbeitung getrennt werden, dh das Schruppen wird zuerst durchgeführt und dann wird das Schlichten durchgeführt durchgeführt. Für die Bearbeitung können verschiedene Maschinen oder unterschiedliche Werkzeuge verwendet werden. Normalerweise ist es in einer Installation nicht erlaubt, die Oberfläche eines Teils eines Teils zu bearbeiten und dann die andere Oberfläche des Teils zu bearbeiten.
Um die Anzahl der Werkzeugwechsel zu reduzieren, verkürzen Sie die Leerlaufzeit und reduzieren unnötige Positionierfehler. Gemäß dem Verfahren, das gleiche Werkzeug zu verwenden und den Bearbeitungsprozess zu konzentrieren, kann der Bearbeitungsprozess der Teile geteilt werden. Verwenden Sie nach Möglichkeit dasselbe Werkzeug, um alle Positionen zu bearbeiten, die bearbeitet werden können, ersetzen Sie dann das andere Werkzeug und bearbeiten Sie den Rest des Teils. Diese Methode wird häufig in speziellen CNC-Werkzeugmaschinen und Bearbeitungszentren verwendet.
(b) Die Aufteilung der Arbeitsschritte
Die Einteilung der Arbeitsschritte wird hauptsächlich in Bezug auf Bearbeitungsgenauigkeit und Produktionseffizienz betrachtet. In einem Prozess ist es oft notwendig, verschiedene Schneidwerkzeuge und Schnittmengen zu verwenden, um unterschiedliche Oberflächen zu bearbeiten. Um die Analyse und Beschreibung komplexer Teile zu erleichtern, ist sie in Schritte innerhalb des Prozesses unterteilt.
Das Prinzip der Arbeitsteilung ist:
(1) Die gleiche Oberfläche wird durch Schruppen, Vorschlichten und Schlichten fertiggestellt. Oder alle maschinell bearbeiteten Oberflächen werden zuerst aufgeraut und dann getrennt bearbeitet.
(2) Für ein Teil, das sowohl eine Fräsebene als auch eine Bohrfläche aufweist, kann es durch Bohren zuerst nach dem Fräsen der Ebene bearbeitet werden. Da das Verfahren in Schritte unterteilt ist, kann die Bearbeitungsgenauigkeit des Lochs verbessert werden. Aufgrund der großen Schnittkräfte beim Fräsen von Teilen sind Teile anfällig für Verformungen. Nachdem die erste Ebene gefräst und das Loch gebohrt ist, ist es möglich, die Verformung für eine gewisse Zeit wiederherzustellen und den Einfluss der Verformung auf die Genauigkeit der Bohrung zu reduzieren.
(3) Drücken Sie das Werkzeug, um den Schritt zu teilen.
Die Rotationszeit einiger Werkzeugmaschinentabellen ist kürzer als die Zeit des Werkzeugwechsels. Je nach Einsatz von Werkzeugen kann es in Stufen unterteilt werden, um die Anzahl der Werkzeugwechsel zu reduzieren und die Bearbeitungseffizienz zu verbessern.
3.5 Teile Installation und Fixture Auswahl
(A) Das Grundprinzip der Positionierung und Installation
(1) Bemühen sich, Designkriterien zu vereinheitlichen, Benchmarks zu bearbeiten und Berechnungsbenchmarks zu programmieren.
(2) Minimiere die Anzahl der Klemmungen. Nachdem die Positionierung so weit wie möglich durchgeführt wurde, werden alle zu bearbeitenden Flächen bearbeitet.
(3) Vermeiden Sie die Besetzung von Maschinen und passen Sie die Bearbeitungspläne manuell an. Um der Effektivität von CNC-Werkzeugmaschinen volles Spiel zu geben.
(B) Grundprinzipien der Auswahl der Vorrichtungen Die Eigenschaften der numerischen Steuerung erfordern zwei Anforderungen an die Vorrichtungen:
Die erste besteht darin sicherzustellen, dass die Koordinatenrichtung der Spannvorrichtung und die Koordinatenrichtung der Werkzeugmaschine relativ konstant sind;
Die zweite besteht darin, die dimensionale Beziehung zwischen dem Teil und dem Maschinenkoordinatensystem zu koordinieren.
Zusätzlich sollten folgende Punkte berücksichtigt werden:
(B) Grundprinzipien für die Auswahl von Leuchten
Die Eigenschaften der CNC-Bearbeitung legen zwei Anforderungen an die Vorrichtungen fest:
Die erste besteht darin sicherzustellen, dass die Koordinatenrichtung der Spannvorrichtung und die Koordinatenrichtung der Werkzeugmaschine relativ konstant sind;
Die zweite besteht darin, die dimensionale Beziehung zwischen dem Teil und dem Maschinenkoordinatensystem zu koordinieren. Zusätzlich sollten folgende Punkte berücksichtigt werden:
(1) Wenn das Teileverarbeitungsvolumen nicht groß ist, sollte es versuchen, Kombinationsvorrichtungen, einstellbare Vorrichtungen oder andere Universalvorrichtungen zu verwenden, um die Produktionsvorbereitungszeit zu verkürzen und Produktionskosten zu sparen.
(2) Erwägen Sie, spezielle Vorrichtungen nur in der Serienproduktion zu verwenden.
(3) Das Laden und Entladen von Teilen sollte schnell, bequem und zuverlässig sein, um die Pausenzeit von CNC-Werkzeugmaschinen zu verkürzen.
(4) Die Komponenten auf der Vorrichtung dürfen die Bearbeitung der Teile auf der Oberfläche des Teils nicht beeinträchtigen. Die Klammern sollten offen sein, und ihre Positionierung der Komponenten des Klemmmechanismus darf den Lauf des Werkzeugs während der Bearbeitung nicht beeinträchtigen.
(3) Bestimmen Sie die Vorschubgeschwindigkeit f (mm / min oder mm / r)
Die Vorschubgeschwindigkeit ist ein wichtiger Parameter für die Schnittmenge von CNC-Werkzeugmaschinen.
Hauptsächlich basierend auf den Teilen der Bearbeitungsgenauigkeit und Oberflächenrauhigkeit sowie den Materialeigenschaften des Werkzeugs und der zu wählenden Teile. Wenn die Anforderungen an die Bearbeitungsgenauigkeit und die Oberflächenrauheit hoch sind, sollte die Vorschubgeschwindigkeit f kleiner gewählt werden. Die maximale Vorschubgeschwindigkeit wird durch die Steifigkeit der Werkzeugmaschine und die Leistung des Vorschubsystems bestimmt und hängt von der Größe des Impulsäquivalents des numerischen Steuersystems ab.
3.7 Bestimmung von Fräspunkten und Werkzeugwechselpunkten
Das Prinzip der Wahl eines Fräserpunktes ist:
(1) Der ausgewählte Schneidepunkt bezieht sich auf mathematische Verarbeitung und vereinfachte Programmierung.
(2) Der Schneidpunkt wird einfach an der Maschine kalibriert.
(3) Einfache Überprüfung während der Verarbeitung.
(4) Der Verarbeitungsfehler ist klein.
3.8 Bestimmung der Verarbeitungsroute
Das Prinzip der Bestimmung der Verarbeitungsroute ist:
(1) Sicherstellen der Bearbeitungsgenauigkeit und Oberflächenrauhigkeit der Teile.
(2) Bequeme numerische Berechnungen, die den Programmieraufwand reduzieren.
(3) Kürzen Sie die Verarbeitungsbetriebsroute und reduzieren Sie den Leerlaufbetriebsplan.
Bei der Festlegung des Bearbeitungsweges müssen wir auch die Bearbeitungszugabe der Teile und die Steifigkeit der Werkzeugmaschinen und Schneidwerkzeuge berücksichtigen. Sie müssen feststellen, ob es sich um einen einzelnen Durchlauf oder mehrere Durchgänge handelt, um den Schneidevorgang abzuschließen. Und in der CNC-Fräsbearbeitung zu bestimmen, ist der Einsatz von Reverse-Fräsen oder Fräsen und so weiter.
Am besten eignen sich CNC-Werkzeugmaschinen für die Bearbeitung von Teilen mit folgenden Eigenschaften:
(1) Teile für Multi-Varietät, Kleinserienproduktion oder Versuchsproduktion neuer Produkte.
(2) Teile mit komplexen Konturen oder hohen Anforderungen an die Bearbeitungsgenauigkeit.
(3) Bei der Bearbeitung mit normalen Werkzeugmaschinen werden Teile verwendet, die eine teure Prozessausrüstung (Werkzeuge, Vorrichtungen und Matrizen) erfordern.
(4) Teile, die viele Male geändert werden müssen.
(5) der Wert von teuren, kann nicht schief gehen, wenn Schlüsselteile bearbeitet werden.
(6) Dringend benötigte Teile mit dem kürzesten Produktionszyklus.
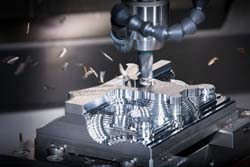
3.2 Prozessanalyse von CNC-Bearbeitungsteilen
(1) Die Größenangaben auf der Teilezeichnung sollten nach dem Prinzip der komfortablen Programmierung erfolgen
(2) Der strukturelle Ablauf jedes Teils des Teils sollte den Eigenschaften der numerischen Steuerungsverarbeitung entsprechen
3.3 Auswahl der Verarbeitungsmethoden und Festlegung der Bearbeitungspläne
(1) Auswahl der Verarbeitungsmethoden
Das Prinzip der Auswahl der Bearbeitungsmethoden ist: Gleichzeitig sind die Anforderungen an Bearbeitungsgenauigkeit und Oberflächenrauhigkeit gewährleistet. Außerdem sollten Produktivität und wirtschaftliche Anforderungen berücksichtigt werden. und die tatsächliche Situation der bestehenden Produktionsanlagen.
(2) Das Prinzip der Bestimmung des Bearbeitungsplans
Die Oberflächenbearbeitung mit hoher Präzision an Teilen wird oft durch Schruppen, Halbfertigbearbeitung und Endbearbeitung erreicht. Für diese Oberflächen wird der endgültige Arbeitsplan basierend auf Qualitätsanforderungen, Maschinenbedingungen und Knüppelbedingungen bestimmt.
Bei der Bestimmung des Bearbeitungsplans sollten zunächst die Verarbeitungsmethoden, die zum Erfüllen dieser Anforderungen erforderlich sind, zunächst gemäß den Anforderungen der Genauigkeit und der Oberflächenrauhigkeit der Hauptoberfläche bestimmt werden. An diesem Punkt müssen wir die Rationalität und Wirtschaftlichkeit des Einsatzes von CNC-Werkzeugmaschinen betrachten und den Funktionen von CNC-Werkzeugmaschinen volles Spiel verleihen. Im Prinzip führen CNC-Werkzeugmaschinen nur eine kompliziertere Teilebearbeitung und eine wichtige Referenzteilbearbeitung durch.
3.4 Aufteilung von Prozessen und Arbeitsschritten
(a) Aufteilung der Prozesse
(1) Der Prozess wird durch die Positionierung der Teile geteilt. Aufgrund der unterschiedlichen Formen jedes Teils unterscheiden sich die technischen Anforderungen jeder Oberfläche. Daher werden die Positionierungsmethoden in der Verarbeitung unterschiedlich sein. Wenn das Teil im Allgemeinen bearbeitet wird, wird die innere Form positioniert; Wenn die innere Struktur des Teils bearbeitet ist, wird die äußere Form positioniert. Der Prozess kann nach den verschiedenen Positionierungsmethoden unterteilt werden.
(2) durch die grobe und feine Bearbeitungsschrittteilung
Wenn der Prozess nach Faktoren wie der Bearbeitungsgenauigkeit, der Steifigkeit und der Verformung des Teils unterteilt wird, kann der Prozess nach dem Prinzip der Grob- und Feinbearbeitung getrennt werden, dh das Schruppen wird zuerst durchgeführt und dann wird das Schlichten durchgeführt durchgeführt. Für die Bearbeitung können verschiedene Maschinen oder unterschiedliche Werkzeuge verwendet werden. Normalerweise ist es in einer Installation nicht erlaubt, die Oberfläche eines Teils eines Teils zu bearbeiten und dann die andere Oberfläche des Teils zu bearbeiten.
Um die Anzahl der Werkzeugwechsel zu reduzieren, verkürzen Sie die Leerlaufzeit und reduzieren unnötige Positionierfehler. Gemäß dem Verfahren, das gleiche Werkzeug zu verwenden und den Bearbeitungsprozess zu konzentrieren, kann der Bearbeitungsprozess der Teile geteilt werden. Verwenden Sie nach Möglichkeit dasselbe Werkzeug, um alle Positionen zu bearbeiten, die bearbeitet werden können, ersetzen Sie dann das andere Werkzeug und bearbeiten Sie den Rest des Teils. Diese Methode wird häufig in speziellen CNC-Werkzeugmaschinen und Bearbeitungszentren verwendet.
(b) Die Aufteilung der Arbeitsschritte
Die Einteilung der Arbeitsschritte wird hauptsächlich in Bezug auf Bearbeitungsgenauigkeit und Produktionseffizienz betrachtet. In einem Prozess ist es oft notwendig, verschiedene Schneidwerkzeuge und Schnittmengen zu verwenden, um unterschiedliche Oberflächen zu bearbeiten. Um die Analyse und Beschreibung komplexer Teile zu erleichtern, ist sie in Schritte innerhalb des Prozesses unterteilt.
Das Prinzip der Arbeitsteilung ist:
(1) Die gleiche Oberfläche wird durch Schruppen, Vorschlichten und Schlichten fertiggestellt. Oder alle maschinell bearbeiteten Oberflächen werden zuerst aufgeraut und dann getrennt bearbeitet.
(2) Für ein Teil, das sowohl eine Fräsebene als auch eine Bohrfläche aufweist, kann es durch Bohren zuerst nach dem Fräsen der Ebene bearbeitet werden. Da das Verfahren in Schritte unterteilt ist, kann die Bearbeitungsgenauigkeit des Lochs verbessert werden. Aufgrund der großen Schnittkräfte beim Fräsen von Teilen sind Teile anfällig für Verformungen. Nachdem die erste Ebene gefräst und das Loch gebohrt ist, ist es möglich, die Verformung für eine gewisse Zeit wiederherzustellen und den Einfluss der Verformung auf die Genauigkeit der Bohrung zu reduzieren.
(3) Drücken Sie das Werkzeug, um den Schritt zu teilen.
Die Rotationszeit einiger Werkzeugmaschinentabellen ist kürzer als die Zeit des Werkzeugwechsels. Je nach Einsatz von Werkzeugen kann es in Stufen unterteilt werden, um die Anzahl der Werkzeugwechsel zu reduzieren und die Bearbeitungseffizienz zu verbessern.
3.5 Teile Installation und Fixture Auswahl
(A) Das Grundprinzip der Positionierung und Installation
(1) Bemühen sich, Designkriterien zu vereinheitlichen, Benchmarks zu bearbeiten und Berechnungsbenchmarks zu programmieren.
(2) Minimiere die Anzahl der Klemmungen. Nachdem die Positionierung so weit wie möglich durchgeführt wurde, werden alle zu bearbeitenden Flächen bearbeitet.
(3) Vermeiden Sie die Besetzung von Maschinen und passen Sie die Bearbeitungspläne manuell an. Um der Effektivität von CNC-Werkzeugmaschinen volles Spiel zu geben.
(B) Grundprinzipien der Auswahl der Vorrichtungen Die Eigenschaften der numerischen Steuerung erfordern zwei Anforderungen an die Vorrichtungen:
Die erste besteht darin sicherzustellen, dass die Koordinatenrichtung der Spannvorrichtung und die Koordinatenrichtung der Werkzeugmaschine relativ konstant sind;
Die zweite besteht darin, die dimensionale Beziehung zwischen dem Teil und dem Maschinenkoordinatensystem zu koordinieren.
Zusätzlich sollten folgende Punkte berücksichtigt werden:
(B) Grundprinzipien für die Auswahl von Leuchten
Die Eigenschaften der CNC-Bearbeitung legen zwei Anforderungen an die Vorrichtungen fest:
Die erste besteht darin sicherzustellen, dass die Koordinatenrichtung der Spannvorrichtung und die Koordinatenrichtung der Werkzeugmaschine relativ konstant sind;
Die zweite besteht darin, die dimensionale Beziehung zwischen dem Teil und dem Maschinenkoordinatensystem zu koordinieren. Zusätzlich sollten folgende Punkte berücksichtigt werden:
(1) Wenn das Teileverarbeitungsvolumen nicht groß ist, sollte es versuchen, Kombinationsvorrichtungen, einstellbare Vorrichtungen oder andere Universalvorrichtungen zu verwenden, um die Produktionsvorbereitungszeit zu verkürzen und Produktionskosten zu sparen.
(2) Erwägen Sie, spezielle Vorrichtungen nur in der Serienproduktion zu verwenden.
(3) Das Laden und Entladen von Teilen sollte schnell, bequem und zuverlässig sein, um die Pausenzeit von CNC-Werkzeugmaschinen zu verkürzen.
(4) Die Komponenten auf der Vorrichtung dürfen die Bearbeitung der Teile auf der Oberfläche des Teils nicht beeinträchtigen. Die Klammern sollten offen sein, und ihre Positionierung der Komponenten des Klemmmechanismus darf den Lauf des Werkzeugs während der Bearbeitung nicht beeinträchtigen.
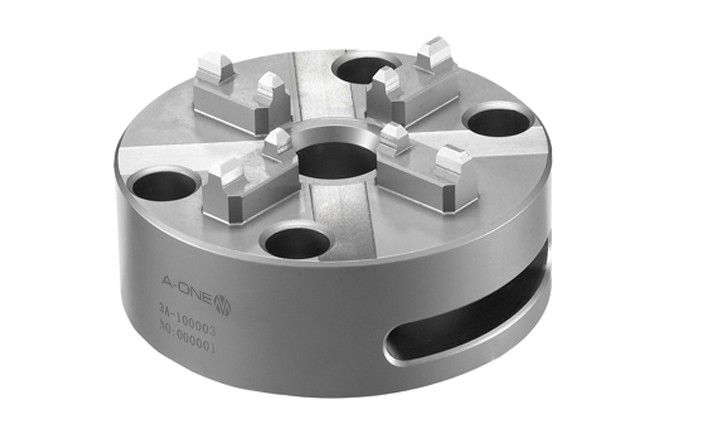
3.6 Werkzeugauswahl und Schnittgeschwindigkeitsbestimmung
(a) die Wahl des Werkzeugs
CNC-Bearbeitungswerkzeuge erfordern den Einsatz neuer hochwertiger Materialien. Das allgemeine Prinzip besteht darin, Carbid so weit wie möglich zu verwenden. Für die Präzisionsbearbeitung können auch Keramik-, CBN- und Diamantwerkzeuge mit besserer Leistung und Verschleißfestigkeit ausgewählt und Werkzeugparameter optimiert werden.
(II) Bestimmung der Schnittmenge
Das Prinzip der vernünftigen Wahl der Schnittmenge ist: Beim Schruppen wird hauptsächlich die Produktivität erhöht, aber auch die Verarbeitungskosten sollten berücksichtigt werden. Bei den Vorbehandlungs- und Endbearbeitungsverfahren sollten die Effizienz, Wirtschaftlichkeit und Verarbeitungskosten des Zuschnitts berücksichtigt werden, um die Verarbeitungsqualität zu gewährleisten.
(1) Ermitteln Sie die Schnitttiefe t (mm). Im Falle von Werkzeugmaschinen, Werkstücken und Werkzeugsteifigkeiten, soweit zulässig, sollte der zu bearbeitende Rand mit der geringsten Anzahl von Zuführungen entfernt werden. Es ist am besten, den Restbetrag auf einmal zu entfernen, um die Produktionseffizienz zu erhöhen.
(2) Ermitteln Sie die Schnittgeschwindigkeit V (m / min). Die Erhöhung der Schnittgeschwindigkeit kann auch die Produktionseffizienz erhöhen. Aber die effektivsten Maßnahmen, um die Produktivität zu verbessern oder sollte so weit wie möglich mit einer großen Schnitttiefe t.
(a) die Wahl des Werkzeugs
CNC-Bearbeitungswerkzeuge erfordern den Einsatz neuer hochwertiger Materialien. Das allgemeine Prinzip besteht darin, Carbid so weit wie möglich zu verwenden. Für die Präzisionsbearbeitung können auch Keramik-, CBN- und Diamantwerkzeuge mit besserer Leistung und Verschleißfestigkeit ausgewählt und Werkzeugparameter optimiert werden.
(II) Bestimmung der Schnittmenge
Das Prinzip der vernünftigen Wahl der Schnittmenge ist: Beim Schruppen wird hauptsächlich die Produktivität erhöht, aber auch die Verarbeitungskosten sollten berücksichtigt werden. Bei den Vorbehandlungs- und Endbearbeitungsverfahren sollten die Effizienz, Wirtschaftlichkeit und Verarbeitungskosten des Zuschnitts berücksichtigt werden, um die Verarbeitungsqualität zu gewährleisten.
(1) Ermitteln Sie die Schnitttiefe t (mm). Im Falle von Werkzeugmaschinen, Werkstücken und Werkzeugsteifigkeiten, soweit zulässig, sollte der zu bearbeitende Rand mit der geringsten Anzahl von Zuführungen entfernt werden. Es ist am besten, den Restbetrag auf einmal zu entfernen, um die Produktionseffizienz zu erhöhen.
(2) Ermitteln Sie die Schnittgeschwindigkeit V (m / min). Die Erhöhung der Schnittgeschwindigkeit kann auch die Produktionseffizienz erhöhen. Aber die effektivsten Maßnahmen, um die Produktivität zu verbessern oder sollte so weit wie möglich mit einer großen Schnitttiefe t.
(3) Bestimmen Sie die Vorschubgeschwindigkeit f (mm / min oder mm / r)
Die Vorschubgeschwindigkeit ist ein wichtiger Parameter für die Schnittmenge von CNC-Werkzeugmaschinen.
Hauptsächlich basierend auf den Teilen der Bearbeitungsgenauigkeit und Oberflächenrauhigkeit sowie den Materialeigenschaften des Werkzeugs und der zu wählenden Teile. Wenn die Anforderungen an die Bearbeitungsgenauigkeit und die Oberflächenrauheit hoch sind, sollte die Vorschubgeschwindigkeit f kleiner gewählt werden. Die maximale Vorschubgeschwindigkeit wird durch die Steifigkeit der Werkzeugmaschine und die Leistung des Vorschubsystems bestimmt und hängt von der Größe des Impulsäquivalents des numerischen Steuersystems ab.
3.7 Bestimmung von Fräspunkten und Werkzeugwechselpunkten
Das Prinzip der Wahl eines Fräserpunktes ist:
(1) Der ausgewählte Schneidepunkt bezieht sich auf mathematische Verarbeitung und vereinfachte Programmierung.
(2) Der Schneidpunkt wird einfach an der Maschine kalibriert.
(3) Einfache Überprüfung während der Verarbeitung.
(4) Der Verarbeitungsfehler ist klein.
3.8 Bestimmung der Verarbeitungsroute
Das Prinzip der Bestimmung der Verarbeitungsroute ist:
(1) Sicherstellen der Bearbeitungsgenauigkeit und Oberflächenrauhigkeit der Teile.
(2) Bequeme numerische Berechnungen, die den Programmieraufwand reduzieren.
(3) Kürzen Sie die Verarbeitungsbetriebsroute und reduzieren Sie den Leerlaufbetriebsplan.
Bei der Festlegung des Bearbeitungsweges müssen wir auch die Bearbeitungszugabe der Teile und die Steifigkeit der Werkzeugmaschinen und Schneidwerkzeuge berücksichtigen. Sie müssen feststellen, ob es sich um einen einzelnen Durchlauf oder mehrere Durchgänge handelt, um den Schneidevorgang abzuschließen. Und in der CNC-Fräsbearbeitung zu bestimmen, ist der Einsatz von Reverse-Fräsen oder Fräsen und so weiter.
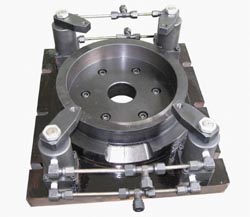