Einfluss der Temperatur auf die Bearbeitungsgenauigkeit bei der Bearbeitung von Prazisions Metallteile
Wir alle wissen, dass die Temperatur die Werkstoffe beeinflusst, aber wie wirkt sich die Endtemperatur auf die Verarbeitung unserer Präzisionsmetallteile aus? An der Oberfläche wird dies eine einfache Aufgabe sein, die zu kompensieren ist. Wir müssen nur den Wärmeausdehnungskoeffizienten (CTE) verwenden, das Thermometer betrachten und eine Lösung finden. Wenn es so einfach ist auf der Linie. Bevor wir diese Berechnung durchführen können, müssen wir einige weitere Variablen berücksichtigen. Hier sind die Variablen, die wir wirklich lösen müssen: Ein Teil des WAK umfasst verschiedene Materialien im selben Teil, den WAK und das Rückmeldungsmessgerät der Maschine, und die Maschinengeometrie ändert sich mit der Temperatur. Heißbearbeitungsprozess durch Schneiden von Kühl- und Schmiermitteln Wärme zuführen oder abführen.
Nachdem wir alle diese Variablen berücksichtigt haben, müssen wir die Temperatur bestimmen, bei der das Teil normalisiert werden soll.
Wie lassen sich all diese Variablen am besten steuern?
Die beste Praxis ist normalerweise, sie zu beseitigen. Stellen Sie die Umgebungstemperatur der Maschine und der Komponenten auf die gewünschte normalisierte Temperatur ein. Teile und Maschine ca. 24 Stunden bei dieser Temperatur "einweichen" lassen. Verwenden Sie Schneidkühlmittel, das auf die gleiche Temperatur wie die standardisierte Umgebung eingestellt wurde, und überwachen Sie diese Bedingungen und steuern Sie sie nach Bedarf. Dies ist die perfekte Welt, aber es ist keine Norm. Wir sehen normalerweise, dass der Teil für die Korrektur der Größe bei 20 ° C oder 68 ° F und in der Verarbeitungsumgebung bei 70 ° F bis 75 ° F ausgelegt ist. Ein Teil des CTE beträgt 1 bis 13 PPM.
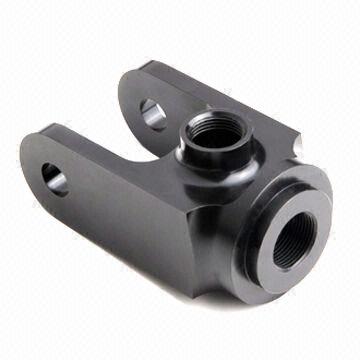
Umgebungstemperatur Regelung
Am häufigsten wird die Umgebungstemperatur geregelt, und CMS bezieht sich normalerweise auf die Spezifikationen unserer Maschinen.
Der Standard ist +/- 1 Grad Celsius oder ungefähr 3 Grad Fahrenheit. Der Stahl hat einen WAK von ungefähr 7,3 ppm / F. Für eine 10-m-Maschine mit einer Temperaturstreuung von 3 ° F = 0,0073 mm / m / 1F = 0,022 mm / m / 3F = 0,22 mm. Wie Sie sehen können, ist dies für eine 30-Fuß-Maschine ziemlich viel Übung. Flugzeugträger, Hubschrauberblätter, Flugsteuerungen und viele andere Komponenten sind so groß, dass es sich um Maschinen mit engeren Toleranzen handeln muss. Je enger Sie kontrollieren können, desto besser.
Als Anmerkung hat das Lawrence Livermore National Ignition Laboratory, das viele hochpräzise Messungen durchführt, ein 10-Meter-Würfel-Labor und bleibt zum Testen bei 0,1 Grad Fahrenheit.
Es gibt auch einige Standards, wie z. B. ASME 5.54, mit thermischer Drift als eine der Standardmessungen in der Werkzeugmaschinenanalyse.
Darüber hinaus ist auch die Art der Wärme wichtig. Durch Strahlungswärme, Konvektionswärme und Wärmeleitung reagiert das Material unterschiedlich. Ich werde hier nicht auf Details eingehen, aber die Hitze der Sonne, des Ofens, des Lüfters und der Lüftungsschlitze der Klimaanlage wird sich auf die Maschine auswirken. Inwieweit einige Hersteller flüssiges Kühlmittel selbst durch Gestelle und Antriebskomponenten laufen lassen, wird nachfolgend erläutert.
Komponenten Temperaturregelung
Eine andere Methode besteht darin, die Temperatur der Komponente zu überwachen und zu steuern. Getriebe, Motoren, Encoder und Kugelumlaufspindeln ändern sich ebenfalls mit der Temperatur. Schon seit vielen Jahren werden Kugelgewindetriebe gebohrt, durch die das Kühlmittel seine Ausdehnung steuert. Der Kugelgraphit ist gegossen und noch in einem Kühlmittelmantel enthalten, der ebenfalls ein Getriebe und einen Motor aufweist. Alle modernen Spindeln sind flüssigkeitsgekühlt oder haben eine genauere Temperaturregelung.
Bei großen Maschinen können einige dieser Methoden angewendet werden. Für die lange Achse mit mehr als 3 Metern ist die Kugelumlaufspindel jedoch keine gute Wahl. Zahnstangen und Ritzel werden häufig anstelle einer einteiligen Konstruktion verwendet. Dies ermöglicht es dem Gestell, sich mit der Maschinenstruktur zu bewegen, ohne zwei verschiedene Legierungen bekämpfen zu müssen.
Strukturelle Temperaturüberwachung
Dies ist eine Methode, mit der moderne elektronische Geräte die Strukturtemperatur überwachen und ändern können, um die im Gerät eingerichteten Algorithmen zu durchlaufen.
Der Weg, dies zu tun, besteht darin, mehrere Temperatursensoren entlang der Achse der Maschine einzurichten. Die Daten werden an die Steuerbox zurückgegeben, die die Impulssignallänge des Encoders ändert, um die thermische Bewegung in der Maschinenstruktur zu korrigieren. Dieses Gerät ist vollständig von der Maschinensteuerung getrennt. Sowohl der Temperatursensor als auch der Maschinengeber passieren diese Box. Das Gebersignal wird dann geändert und an die Steuerung zurückgesendet. Dies ist ein sehr gutes System, aber es hängt von zwei sehr wichtigen Dingen ab, um korrekt zu funktionieren:
(1) Temperaturänderungen müssen sehr langsam erfolgen
(2) Muss von Konvektionswärme, dh Luft zu Material kommen.
Die zusätzliche Bedeutung davon ist, dass das System getestet werden muss. Der Grund für die Anforderungen an die Konvektionswärme und die langsame Änderung ist, dass der Temperatursensor nur die gesamte Länge der Welle ausgleichen kann und alle Sensoren mittelt. Wir können 100 Sensoren auf der Welle platzieren. Ist jedoch ein Bereich heiß, der andere jedoch kalt, liefert das Gerät nur in bestimmten Bereichen über die gesamte Länge der Durchschnittstemperatur schlechte Ergebnisse. Derzeit baut CMS eine Maschine mit diesem System, und wir hoffen, noch vor Jahresende eine Umstellung vornehmen zu können.
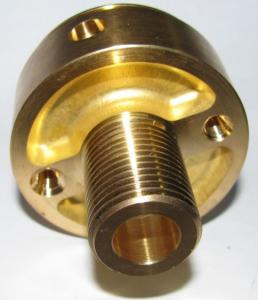
Echtzeit-Positionierungssteuerung
Dies ist derzeit der beste Weg, um Temperaturänderungen in langen Maschinen zu bewältigen. Es überrascht nicht, dass dies bei weitem das teuerste ist. Das System verwendet ein Laserinterferometer, um die von der Maschine zurückgelegte Strecke zu messen. Dies ist nicht Bestandteil der Maschinensteuerung. Es ist dasselbe Gerät, mit dem die Maschine kalibriert wird. Der Unterschied besteht darin, dass dieser Laser fest an der Maschine montiert ist und in Echtzeit online ist. Bei einer Portalmaschine mit Master-Slave-Achse sind zwei Systeme erforderlich, um die Bewegung der Achse zu korrigieren. Außerdem wird der Temperaturgradient kalibriert und eine Selbstkalibrierung durchgeführt. Die Kosten des Systems betragen ca. 100.000 USD pro Achse. Das CMS überprüft dieses System auch auf mögliche zukünftige Verfügbarkeit.
Teile sich als Variable
Wie ich bereits sagte, müssen wir darüber nachdenken. Der CTE des Geräts hat einen Wert, und einige können stark variieren. Wie kompensieren wir? Die ideale Situation ist, die Maschine und die Teile auf die gewünschte Temperatur einzustellen und sehr nah zu bleiben. Was ist jedoch, wenn die Nenntemperatur 68 ° F beträgt und die Maschine und die Teile 72 ° F haben? Derzeit gibt es mehrere Optionen. Wenn die Maschine sorgfältig auf dieser Temperatur gehalten werden soll, können wir den WAK des Materials verwenden, um die Maschine auf die korrekten Abmessungen von 72F zu kalibrieren. Das ist eine gute Lösung. Nun, wenn sich die Umgebung auf 77F ändert? Der CTE dieser Maschine wird sich ausdehnen, dh diese 30 Mikrometer, und dieser Teil wird sich um 10 Mikrometer ausdehnen. Was tun wir jetzt? Wir haben mehrere Möglichkeiten. Wir können die Maschine mit dem CTE des Teils auf diese neue Umgebung neu kalibrieren. Sie können das Teileprogramm auch skalieren, indem Sie die Bewegung des Teils von der Bewegung der Maschine abziehen und den Anteil der Gesamtgröße berechnen. Oder wir nehmen eines der aktiven Geräte zur Maschinenkompensation, die wir besprochen haben.
Option für lineare Proportionalregelung
Es gibt auch ein einfaches, effektives und kostengünstiges Gerät, das derzeit im CMS verwendet wird, um all diese verrückten Bewegungen zu korrigieren. Bevor ich dieses wunderbare Gerät beschreibe, muss ich erwähnen, dass es nur für die kleinere Längsachse von 3 Metern Länge funktioniert. Das Gerät ist eine lineare Skala mit demselben WAK wie das zu schneidende Material. Wie bereits erwähnt, haben wir die Wahl zwischen Umgebung, Komponente, Maschine oder Feedback-Gerät. In diesem Fall besteht die Waage aus einem Material mit demselben WAK-Anteil, und die Maschine kann sich in jedem Fall ausdehnen und zusammenziehen, und die Rückkopplungsvorrichtung veranlasst die Maschine nur, sich um die abgelesene Strecke zu bewegen. Eine weitere Möglichkeit besteht darin, die Waage von der Bewegung der Maschine zu isolieren und die Umgebung innerhalb oder um die Waage herum zu steuern. Dies ist der Ansatz von CMS. Wir verwenden eine Stahlbandwaage, die in einem Gehäuse eingebaut ist, das mechanisch von der Maschine getrennt ist, und wir steuern die Temperatur im Inneren des Gehäuses. Auf diese Weise wird die Maschine unabhängig von den äußeren Bedingungen immer korrekt kalibriert. Jetzt muss die Teilebewegung noch berücksichtigt werden, dies gibt uns jedoch eine geringere zu berücksichtigende Variable.
Nachdem wir alle diese Variablen berücksichtigt haben, müssen wir die Temperatur bestimmen, bei der das Teil normalisiert werden soll.
Wie lassen sich all diese Variablen am besten steuern?
Die beste Praxis ist normalerweise, sie zu beseitigen. Stellen Sie die Umgebungstemperatur der Maschine und der Komponenten auf die gewünschte normalisierte Temperatur ein. Teile und Maschine ca. 24 Stunden bei dieser Temperatur "einweichen" lassen. Verwenden Sie Schneidkühlmittel, das auf die gleiche Temperatur wie die standardisierte Umgebung eingestellt wurde, und überwachen Sie diese Bedingungen und steuern Sie sie nach Bedarf. Dies ist die perfekte Welt, aber es ist keine Norm. Wir sehen normalerweise, dass der Teil für die Korrektur der Größe bei 20 ° C oder 68 ° F und in der Verarbeitungsumgebung bei 70 ° F bis 75 ° F ausgelegt ist. Ein Teil des CTE beträgt 1 bis 13 PPM.
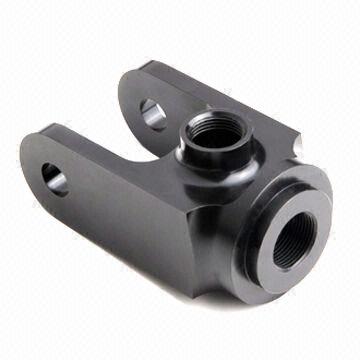
Umgebungstemperatur Regelung
Am häufigsten wird die Umgebungstemperatur geregelt, und CMS bezieht sich normalerweise auf die Spezifikationen unserer Maschinen.
Der Standard ist +/- 1 Grad Celsius oder ungefähr 3 Grad Fahrenheit. Der Stahl hat einen WAK von ungefähr 7,3 ppm / F. Für eine 10-m-Maschine mit einer Temperaturstreuung von 3 ° F = 0,0073 mm / m / 1F = 0,022 mm / m / 3F = 0,22 mm. Wie Sie sehen können, ist dies für eine 30-Fuß-Maschine ziemlich viel Übung. Flugzeugträger, Hubschrauberblätter, Flugsteuerungen und viele andere Komponenten sind so groß, dass es sich um Maschinen mit engeren Toleranzen handeln muss. Je enger Sie kontrollieren können, desto besser.
Als Anmerkung hat das Lawrence Livermore National Ignition Laboratory, das viele hochpräzise Messungen durchführt, ein 10-Meter-Würfel-Labor und bleibt zum Testen bei 0,1 Grad Fahrenheit.
Es gibt auch einige Standards, wie z. B. ASME 5.54, mit thermischer Drift als eine der Standardmessungen in der Werkzeugmaschinenanalyse.
Darüber hinaus ist auch die Art der Wärme wichtig. Durch Strahlungswärme, Konvektionswärme und Wärmeleitung reagiert das Material unterschiedlich. Ich werde hier nicht auf Details eingehen, aber die Hitze der Sonne, des Ofens, des Lüfters und der Lüftungsschlitze der Klimaanlage wird sich auf die Maschine auswirken. Inwieweit einige Hersteller flüssiges Kühlmittel selbst durch Gestelle und Antriebskomponenten laufen lassen, wird nachfolgend erläutert.
Komponenten Temperaturregelung
Eine andere Methode besteht darin, die Temperatur der Komponente zu überwachen und zu steuern. Getriebe, Motoren, Encoder und Kugelumlaufspindeln ändern sich ebenfalls mit der Temperatur. Schon seit vielen Jahren werden Kugelgewindetriebe gebohrt, durch die das Kühlmittel seine Ausdehnung steuert. Der Kugelgraphit ist gegossen und noch in einem Kühlmittelmantel enthalten, der ebenfalls ein Getriebe und einen Motor aufweist. Alle modernen Spindeln sind flüssigkeitsgekühlt oder haben eine genauere Temperaturregelung.
Bei großen Maschinen können einige dieser Methoden angewendet werden. Für die lange Achse mit mehr als 3 Metern ist die Kugelumlaufspindel jedoch keine gute Wahl. Zahnstangen und Ritzel werden häufig anstelle einer einteiligen Konstruktion verwendet. Dies ermöglicht es dem Gestell, sich mit der Maschinenstruktur zu bewegen, ohne zwei verschiedene Legierungen bekämpfen zu müssen.
Strukturelle Temperaturüberwachung
Dies ist eine Methode, mit der moderne elektronische Geräte die Strukturtemperatur überwachen und ändern können, um die im Gerät eingerichteten Algorithmen zu durchlaufen.
Der Weg, dies zu tun, besteht darin, mehrere Temperatursensoren entlang der Achse der Maschine einzurichten. Die Daten werden an die Steuerbox zurückgegeben, die die Impulssignallänge des Encoders ändert, um die thermische Bewegung in der Maschinenstruktur zu korrigieren. Dieses Gerät ist vollständig von der Maschinensteuerung getrennt. Sowohl der Temperatursensor als auch der Maschinengeber passieren diese Box. Das Gebersignal wird dann geändert und an die Steuerung zurückgesendet. Dies ist ein sehr gutes System, aber es hängt von zwei sehr wichtigen Dingen ab, um korrekt zu funktionieren:
(1) Temperaturänderungen müssen sehr langsam erfolgen
(2) Muss von Konvektionswärme, dh Luft zu Material kommen.
Die zusätzliche Bedeutung davon ist, dass das System getestet werden muss. Der Grund für die Anforderungen an die Konvektionswärme und die langsame Änderung ist, dass der Temperatursensor nur die gesamte Länge der Welle ausgleichen kann und alle Sensoren mittelt. Wir können 100 Sensoren auf der Welle platzieren. Ist jedoch ein Bereich heiß, der andere jedoch kalt, liefert das Gerät nur in bestimmten Bereichen über die gesamte Länge der Durchschnittstemperatur schlechte Ergebnisse. Derzeit baut CMS eine Maschine mit diesem System, und wir hoffen, noch vor Jahresende eine Umstellung vornehmen zu können.
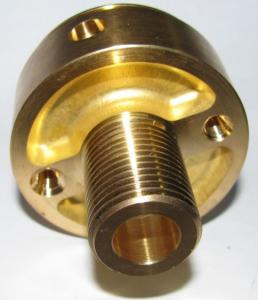
Echtzeit-Positionierungssteuerung
Dies ist derzeit der beste Weg, um Temperaturänderungen in langen Maschinen zu bewältigen. Es überrascht nicht, dass dies bei weitem das teuerste ist. Das System verwendet ein Laserinterferometer, um die von der Maschine zurückgelegte Strecke zu messen. Dies ist nicht Bestandteil der Maschinensteuerung. Es ist dasselbe Gerät, mit dem die Maschine kalibriert wird. Der Unterschied besteht darin, dass dieser Laser fest an der Maschine montiert ist und in Echtzeit online ist. Bei einer Portalmaschine mit Master-Slave-Achse sind zwei Systeme erforderlich, um die Bewegung der Achse zu korrigieren. Außerdem wird der Temperaturgradient kalibriert und eine Selbstkalibrierung durchgeführt. Die Kosten des Systems betragen ca. 100.000 USD pro Achse. Das CMS überprüft dieses System auch auf mögliche zukünftige Verfügbarkeit.
Teile sich als Variable
Wie ich bereits sagte, müssen wir darüber nachdenken. Der CTE des Geräts hat einen Wert, und einige können stark variieren. Wie kompensieren wir? Die ideale Situation ist, die Maschine und die Teile auf die gewünschte Temperatur einzustellen und sehr nah zu bleiben. Was ist jedoch, wenn die Nenntemperatur 68 ° F beträgt und die Maschine und die Teile 72 ° F haben? Derzeit gibt es mehrere Optionen. Wenn die Maschine sorgfältig auf dieser Temperatur gehalten werden soll, können wir den WAK des Materials verwenden, um die Maschine auf die korrekten Abmessungen von 72F zu kalibrieren. Das ist eine gute Lösung. Nun, wenn sich die Umgebung auf 77F ändert? Der CTE dieser Maschine wird sich ausdehnen, dh diese 30 Mikrometer, und dieser Teil wird sich um 10 Mikrometer ausdehnen. Was tun wir jetzt? Wir haben mehrere Möglichkeiten. Wir können die Maschine mit dem CTE des Teils auf diese neue Umgebung neu kalibrieren. Sie können das Teileprogramm auch skalieren, indem Sie die Bewegung des Teils von der Bewegung der Maschine abziehen und den Anteil der Gesamtgröße berechnen. Oder wir nehmen eines der aktiven Geräte zur Maschinenkompensation, die wir besprochen haben.
Option für lineare Proportionalregelung
Es gibt auch ein einfaches, effektives und kostengünstiges Gerät, das derzeit im CMS verwendet wird, um all diese verrückten Bewegungen zu korrigieren. Bevor ich dieses wunderbare Gerät beschreibe, muss ich erwähnen, dass es nur für die kleinere Längsachse von 3 Metern Länge funktioniert. Das Gerät ist eine lineare Skala mit demselben WAK wie das zu schneidende Material. Wie bereits erwähnt, haben wir die Wahl zwischen Umgebung, Komponente, Maschine oder Feedback-Gerät. In diesem Fall besteht die Waage aus einem Material mit demselben WAK-Anteil, und die Maschine kann sich in jedem Fall ausdehnen und zusammenziehen, und die Rückkopplungsvorrichtung veranlasst die Maschine nur, sich um die abgelesene Strecke zu bewegen. Eine weitere Möglichkeit besteht darin, die Waage von der Bewegung der Maschine zu isolieren und die Umgebung innerhalb oder um die Waage herum zu steuern. Dies ist der Ansatz von CMS. Wir verwenden eine Stahlbandwaage, die in einem Gehäuse eingebaut ist, das mechanisch von der Maschine getrennt ist, und wir steuern die Temperatur im Inneren des Gehäuses. Auf diese Weise wird die Maschine unabhängig von den äußeren Bedingungen immer korrekt kalibriert. Jetzt muss die Teilebewegung noch berücksichtigt werden, dies gibt uns jedoch eine geringere zu berücksichtigende Variable.