Eigenschaften und Anwendung des geraden Nutbohrers
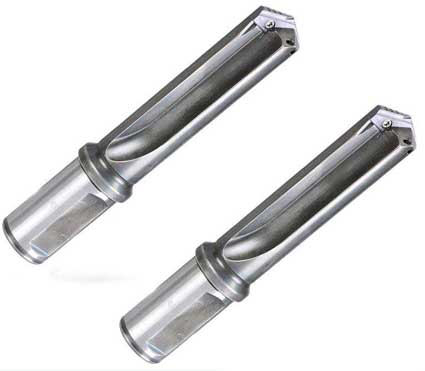
Die traditionelle Vorstellung, dass "Spiralnutenbohrer unersetzbar sind", wird jetzt durch die Bearbeitungsleistung von Geradnutenbohrern zunichte gemacht. Bei einigen Bearbeitungsanwendungen ist das Bohren mit geraden Nuten die bessere Wahl für Werkzeuge als Spiralbohrer.
Der "Pionier" moderner Geradnutenbohrer ist der Stanzbohrer. Dieser Bohrer hat eine kurze Größe, eine gute Steifigkeit und eine starke Bohrerspitze. Es eignet sich zum Bohren von harten Stahlwerkstoffen mit geringer Spindeldrehzahl und geringem Vorschub. Seine hohe Festigkeit und hohe Steifigkeit ermöglichen es, Löcher mit guter Geradheit und Rundheit zu bearbeiten. Der Grund, warum die Matrize gute Bearbeitungsergebnisse erzielen kann, liegt darin, dass das zu bearbeitende Material bei der Konstruktion der Bohrkrone normalerweise ein Metall ist, das kurze Späne erzeugt. Die Spankontrolle bleibt ein zentrales Thema bei der Bearbeitung von Geradnutenbohrern. Das Bohren mit geraden Nuten ist am besten nur bei der Bearbeitung von Materialien möglich, die keine langen, rankenartigen Späne produzieren. Diese Materialien umfassen Gusseisen, pulverförmige Legierung (P / M), Siliciumaluminiumlegierung mit mittlerem bis hohem Siliciumgehalt (6% oder höher) und dergleichen.
Mit den Fortschritten in der Werkzeugmaschinentechnologie, der Kühlmittelzufuhrtechnologie und dem Werkzeuggeometriedesign erweitert sich jedoch das Spektrum der Bearbeitungsanwendungen für das Bohren mit geraden Nuten. Traditionell ist die Spiralnut des Bohrers für die Spanabfuhr unverzichtbar. Der Geradrillenbohrer kann nur zum Bohren von flachen Löchern mit einer Lochtiefe von 2D ~ 3D (D ist der Lochdurchmesser) auf Aluminium und Gusseisen verwendet werden. Das heute entwickelte Hochdruckkühlsystem und die höhere Spindeldrehzahl der Werkzeugmaschine haben jedoch die Spanbrech- und Spanabfuhrleistung des innengekühlten Geradnutenbohrers erheblich verbessert.
Geradnutenbohrer können unter geeigneten Bedingungen eine weitaus bessere Verarbeitungsleistung bieten als Spiralnutenbohrer. Geradnutenbohrer haben den Vorteil, dass sie Löcher mit höherer Rundheit und Geradheit bearbeiten können, und sie schneiden schneller als normale Kobalt- oder Schnellarbeitsstahlbohrer. Wenn zum Beispiel anstelle eines Spiralbohrers ein 0,39 "(φ10 mm) gerader Rillenbohrer vom Typ Guhring RT150GG zum Bearbeiten eines Aluminiumteils verwendet wird. Die Schnittgeschwindigkeit des Spiralbohrers beträgt 15 m / min (50 sfm) und die Vorschubgeschwindigkeit beträgt 0,127 mm / r (0,005 ipr). Die Schnittgeschwindigkeit des Geradnutenbohrers kann 800 sfm (245 m / min) erreichen, und die Vorschubgeschwindigkeit beträgt 0,007 ipr (0,178 mm / r). Die Schnittzeit für Geradnutenbohrungen beträgt nur 1/10 der Spiralbohrer.
Ein Teil des Grundes für das Bohren mit geraden Rillen zur deutlichen Steigerung der Bearbeitungseffizienz basiert auf der Grundkonstruktion des Bohrers - die gerade Rille bietet einen direkten Weg für die Spanabgabeöffnung. Da jedoch die Schneidkante des geraden Rillenbohrers keinen positiven Spanwinkel aufweist, ist sein Span- und Spanbruchvermögen schlecht, insbesondere wenn ein duktiles Material bearbeitet wird.
Die Schnittgeschwindigkeit (insbesondere eine ausreichend hohe Schnittgeschwindigkeit) ist ein weiterer Faktor für die erfolgreiche Anwendung des geraden Rillenbohrens. Je schneller die Schnittgeschwindigkeit ist, desto kleiner sind die gebildeten Späne. Das Geradnutenbohren erzielt eine hohe Produktivität durch schnellere Spindeldrehzahlen anstelle höherer Vorschubgeschwindigkeiten.
Viele leistungsstarke, bohrstarke Spiralbohrer weisen eine erhebliche Abschrägung der Schneidkante auf. Dies erfordert, dass der Vorschub des Bohrers in Betrieb die Fasengröße der Schneidkante überschreitet, damit die Schneidkante das Werkstückmaterial schneiden kann, anstatt es nur zu schieben. Bei einigen Bearbeitungsanwendungen und zu bearbeitenden Materialien funktioniert die Schneide des Spiralbohrers gut. Diese Spiralbohrer werden normalerweise mit einer höheren Vorschubgeschwindigkeit als die gerade Nut gebohrt, jedoch mit einer niedrigeren Schnittgeschwindigkeit als der gerade Nutbohrer.
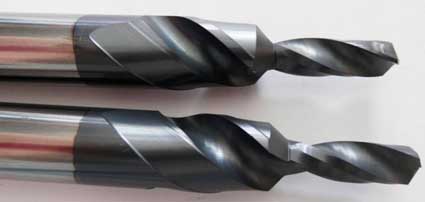
Nehmen Sie als Beispiel den Bohrprozess des Autoherstellers Saturn. Die vom Unternehmen verwendeten Bohrer wurden zuvor mit einer Schnittgeschwindigkeit von ca. 500 sfm (150 m / min) bearbeitet. Später beschlossen sie, einen Schneidetest durchzuführen, um festzustellen, wie hoch die Geschwindigkeit der Bohrer sein könnte. Als Ergebnis stellten sie fest, dass bei Erhöhung der Drehzahl die Werkzeuglebensdauer verlängert, der Bearbeitungszyklus verkürzt und der Spanabfuhrwirkungsgrad verbessert wird. Bei der Bearbeitung mit einem unbeschichteten Vollhartmetallbohrer kann die Schnittgeschwindigkeit bis zu 300 m / min (1000 sfm) betragen, während die Standzeit und die Lochqualität erheblich verbessert werden.
Durch die Verwendung einer angemessenen Kombination aus Kühlmitteldruck und Schnittgeschwindigkeit können gerade gerillte Bohrer auch Werkstückmaterialien effizient bearbeiten, die nicht unbedingt kurze Späne produzieren. Zum Beispiel ist die Wirkung der Bearbeitung von spannungsbeständigem 1144-Stahl mit geraden Rillenbohrungen sehr gut, der Spanbruch ist glatt und die Späne sind klein, und es wird keine Aufbauschneide gebildet. Der zur Bearbeitung verwendete Bohrer ist H.A.M., Der 294-0500 von Precision ist ein nicht beschichteter gerader Innenkühlbohrer: (Durchmesser φ5 mm), Bohrtiefe 48 mm, Schnittgeschwindigkeit 185 sfm (63 m / min), Vorschubgeschwindigkeit 0,003 ipr (0,076 mm / r) und Kühlmitteldruck 1500 psi . Der Gehalt an Mangansulfid in der 1144-Legierung ist hoch, was zum Spanbruch beiträgt. Um dieses Material jedoch erfolgreich zu verarbeiten, ist ein hoher Kühlmitteldruck erforderlich (erfahrungsgemäß sollte der Kühlmitteldruck über 600 psi liegen, vorzugsweise bei 1000 psi, 1200 psi oder höher).
Beim Bohren mit geraden Nuten kann neben der Spankontrolle auch die Aufbauschneide ein Problem darstellen. Dies liegt daran, dass das Material des entfernten Werkstücks die Schneidkante passiert, wenn es aus der geraden Schlitzbohrmitte austritt und in Richtung des Bohrmeißels des Bohrmeißels gedrückt wird. Eine Möglichkeit, die Bildung von Aufbauschneiden zu vermeiden, ist die Verwendung eines Bohrers mit glatter Oberfläche und hoher Oberflächengüte. Die Verwendung von beschichteten Bohrern hilft auch, die Bildung von Aufbauschneiden zu verhindern. Molybdändisulfid (MoS2) -Beschichtungen, die in der Aluminiumverarbeitung weit verbreitet sind, haben ähnliche Eigenschaften wie Teflon und lassen sich nicht leicht mit anderen Materialien verbinden. Die Verwendung solcher beschichteten Bohrer eignet sich hervorragend für Anwendungen, bei denen die Bildung von Aufbauschneiden verhindert werden muss.
Die gerade gebohrte Bohrerspitzenstruktur ermöglicht das Schärfen von zwei Kanten an der Außenkante jeder geraden Nut. Da der Bohrer vier Berührungspunkte mit dem Werkstück hat, ist der Bohrer während der Bearbeitung stabiler, was die Bearbeitungsgenauigkeit verbessert.
Der große Scheitelwinkel des Geradrillenbohrers trägt auch zur Verbesserung seiner Verarbeitbarkeit bei. Zum Beispiel hat H.A.M. Der Standard-Geradschnittbohrer von Precision verwendet einen 140-Grad-Scheitelpunkt, ähnlich einem separaten Spitzenbohrer, der mit sehr geringem Schub gebohrt werden kann. Darüber hinaus sorgt der große Scheitelwinkel dafür, dass der gesamte Durchmesser des Bohrers schnell mit dem Werkstückmaterial in Eingriff kommt, wodurch die Möglichkeit des "Ablaufens" des Bohrers minimiert wird.
In vielen Bearbeitungssituationen ist es am besten, zuerst ein Startloch (Vorloch) mit einem Pilotbohrer (Zentrierbohrer) zu bearbeiten, dessen Scheitelwinkel größer ist als der Scheitelwinkel des Hartmetall-Geradnutenbohrers. Auf diese Weise kann sichergestellt werden, dass der Mittelpunkt des Bohrers (horizontale Kante) des Geradnutenbohrers zuerst in die Vorbohrung eintritt, um einen Kantenbruch zu vermeiden, der durch den ersten Kontakt der spröden Hartmetallschneide mit dem Werkstück verursacht wird . Eine weitere Strategie für das Bohren mit geraden Nuten besteht darin, die Lochposition einfach vor dem Bohren zu bestimmen. Denn selbst die Oberfläche des bearbeiteten Werkstücks kann Defekte aufweisen, und der Bediener muss das Loch nur mit dem Bohrer berühren, um seine Position zu bestimmen. Solange die horizontale Kante des Meißels das Werkstück zuerst berührt, "weicht" der Meißel nicht ab und das Positionierungsloch kann eine ähnliche Rolle wie eine Bohrbüchse spielen.
Die bei der Bearbeitung von Löchern mit einem Durchmesser von 10 mm auf Gusseisen mit drei verschiedenen Bohrern gemessene Geradheit des Lochs zeigt Folgendes an: Der Spiralnutenbohrer aus Schnellarbeitsstahl hat eine Schnittgeschwindigkeit von 30 m / min und eine Vorschubgeschwindigkeit von 195 mm / min. Die externe Kühlmethode wird übernommen, und die Verarbeitungsqualität des Lochs erreicht IT12. Der Vollhartmetall-Spiralnutenbohrer hat eine Schnittgeschwindigkeit von 295sfm (90m / min). Die Vorschubgeschwindigkeit beträgt 34,5 ipm (876 mm / min), und die interne Kühlmethode beträgt 440 psi / 2,4 gpm mit dem Kühlmitteldruck. Die Verarbeitungsqualität der Bohrung erreicht IT9; Der Geradnutenbohrer hat eine Schnittgeschwindigkeit von 130 m / min, eine Vorschubgeschwindigkeit von 845 mm / min und eine interne Kühlmethode mit einem Kühlmitteldruck von 3,2 g / min. Die Verarbeitungsqualität der Bohrung erreicht IT8.
Viele Leute bezeichnen alle Bohrer mit gerader Nut als "G-Bohrer", aber dies ist nicht wahr. Tatsächlich sind „G-Bohrer“ nur die Handelsnamen für eine von Accuromm USA Int. Die Außenkante des Endes eines solchen Bohrers kann die Wand des Lochs quetschen.
Vergleichen Sie das Lochwandfinish, das mit verschiedenen Lochbearbeitungswerkzeugen erzielt werden kann. Hochgeschwindigkeitsstahlbohrer haben im Allgemeinen einen Wert von ca. 125 U / min, Hartmetall-Spiralnuten-Hochleistungsbohrer von ca. 63 U / min und Dreischlitz-Reibahlen von ca. 32 U / min. Der G-Bohrer kann 16 U / min oder weniger erreichen und hat den Endbearbeitungsgrad erreicht.
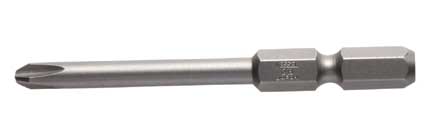
Um Bohrungen unterschiedlicher Qualität zu bearbeiten, hat Accuromm verschiedene Bohrer entwickelt. Die G-Bohrer des Unternehmens erfüllen im Allgemeinen die Anforderungen der H9-Toleranznorm für die Lochbearbeitung, während die G-7-Bohrer des Unternehmens Bohren und Reiben kombinieren, um die H7-Toleranzanforderungen zu erfüllen. Beispielsweise nannte Accuromm ein Beispiel für ein Bearbeitungsverfahren, bei dem ein Bohrer mit gerader Nut einen Spiralbohrer auf einem Aluminiumwerkstoff ersetzt. Der Durchmesser des Bohrers G beträgt 0,394 "(φ 10 mm), die Schnittgeschwindigkeit beträgt 330 ft. / Min (100 m / min) und die Vorschubmenge beträgt 0,008 ipr (0,20 mm / r). Die Ergebnisse zeigen, dass die Lochbearbeitungsgenauigkeit erheblich verbessert wird und der Öffnungsfehler von ursprünglich ± 0,0032 "(0,08 mm) auf ± 0,0012" (0,03 mm) verringert wird. Bei gleichen Schnittparametern wie bei einem G-7-Bohrer kann der Öffnungsfehler auf ± 0,02 mm (0,0008 ") reduziert werden. Da die Bohrqualität von Geradnutenbohrern hoch ist, ist sie auch für die Bearbeitung anderer Löcher hilfreich. Accuromm weist darauf hin, dass seine hervorragende Maßgenauigkeit die Gewindebohrungslebensdauer um etwa 50% erhöhen kann, wenn Gewindebohrungen erforderlich sind, die mit geraden Rillenbohrern bearbeitet wurden.
Die Verbesserung der Leistung von Schneidwerkzeugen erfordert fast immer einen engeren Bereich von zu bearbeitenden Objekten. Gerade Nutenbohren ist zwar kein Allzweckwerkzeug, sein Einsatzbereich erweitert sich jedoch. Durch die Verbreitung des geraden Nutenbohrens können erhebliche Vorteile hinsichtlich der Verbesserung der Bearbeitungseffizienz und der Verbesserung der Werkstückqualität erzielt werden.
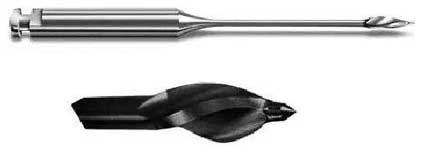
H.A.M. Precisions integraler Hartmetall-Stufenbohrer "Muilt-Drill" mit gerader Rille verwendet eine TiAlN-Beschichtung und ein internes Kühlkanaldesign, das zum Bohren, Stufenbohren und Anfasen von kurzspanenden Aluminiumlegierungsmaterialien geeignet ist.
Das Spezialwerkzeug "Insatiable G-Spot" von Competitive Carbide Int. kombiniert den geraden G-Spot-Bohrer des Unternehmens mit dem inneren Hohlraumfräser. Eine Vielzahl von Bearbeitungen der Werkstückgeometrie kann mit einem einzigen Werkzeug durchgeführt werden. Das Werkzeug kann insgesamt neun Bearbeitungsvorgänge ausführen, darunter Bohren, Anfasen und Bohren mit Außendurchmesser (OD), Anfasen und Bohren mit Innendurchmesser (ID) und Drehen mit Außendurchmesser (Vorbearbeitung von Gewindewerkstücken). Da die Kontaktfläche zwischen Werkzeug und Werkstück groß ist und der Außendurchmesser des Bohrers an 4 Stellen mit dem Werkstück in Kontakt steht. Das zweiteilige Werkzeug hilft dabei, die Position des Werkstücks beizubehalten und dem Werkstück eine zusätzliche Klemmwirkung zu verleihen. Da der Bohrer mit gerader Nut 2 Riemen hat, kann das Werkzeug nicht nur Löcher bohren, sondern auch die Löcher zusammendrücken. Dies bedeutet, dass das fertige Loch ein höheres Finish und eine bessere Geradheit aufweist und die spezifischen Größenanforderungen des Lochs besser erfüllen kann als ein herkömmlicher Bohrer mit nur einer Schneidkante. Das Composite-Werkzeug Insatiable G-Spot kann mindestens 3 bis 4 Werkzeuge ersetzen. Wenn also das Originalwerkzeug verwendet wird, dauert es 3-mal, das Werkzeug zu wechseln und 4 Bearbeitungsvorgänge abzuschließen. Daher ist die Verwendung eines solchen multifunktionalen Verbundwerkzeugs zur Verbesserung der Verarbeitungseffizienz und zur Verkürzung der Verarbeitungszeit vorteilhaft.