Bohren von Mikro loechern in Leiterplatten verbunden
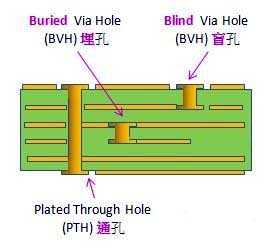
Die Spezifikationen von Leiterplatten sind komplex und es gibt viele Arten von Produkten. Das am häufigsten verwendete Verbundmaterial auf Epoxidharzbasis in Leiterplatten ist ein Mikroloch (ein kleines Loch mit einem Durchmesser von 0,6 mm oder weniger und ein Mikroloch mit einem Durchmesser von 0,3 mm oder weniger).
Die Verbundleiterplatte weist eine hohe Sprödigkeit, eine hohe Härte, eine hohe Faserfestigkeit, eine hohe Zähigkeit, eine geringe interlaminare Scherfestigkeit, eine Anisotropie, eine schlechte Wärmeleitfähigkeit und einen großen Unterschied in den Wärmeausdehnungskoeffizienten von Fasern und Harzen auf. Wenn die Schneidetemperatur hoch ist, können an der Faser-Substrat-Grenzfläche um die Schneidezone leicht thermische Spannungen erzeugt werden. Wenn die Temperatur zu hoch ist, schmilzt das Harz und haftet an der Schneide, was die Verarbeitung und die Entfernung von Spänen erschwert.
Die Schnittkraft des gebohrten Verbundmaterials ist sehr ungleichmäßig und es ist leicht, Defekte wie Delamination, Grate und Risse zu verursachen, und die Verarbeitungsqualität ist schwierig sicherzustellen. Dieses Material ist für das Werkzeug extrem abrasiv und der Werkzeugverschleiß ist ziemlich stark. Der Verschleiß des Werkzeugs führt wiederum zu größeren Schnittkräften und Wärmeentwicklung: Kann die Wärme nicht rechtzeitig abgeführt werden, führt dies zum Aufschmelzen der niedrigschmelzenden Komponente im Leiterplattenmaterial und zum Ablösen der Verbundschicht zwischen den Schichten. Daher ist es bei PCB-Verbundwerkstoffen schwierig, Nichtmetall-Verbundwerkstoffe zu verarbeiten, und der Verarbeitungsmechanismus unterscheidet sich vollständig von dem von Metallwerkstoffen.
Wenn PCB-Materialien mechanisch gebohrt werden, ist die Verarbeitungseffizienz hoch, die Lochpositionierung ist genau und die Qualität der Löcher ist ebenfalls hoch. Beim Bohren eines Mikrolochs ist der Durchmesser des Bohrers jedoch zu klein und es ist leicht zu brechen. Während des Bohrvorgangs können auch Defekte wie Materialablösung, Lochwandschäden, Grate und Flecken auftreten.
I.Bohrkraft
Verschiedene Probleme, die beim mechanischen Bohren auftreten, hängen direkt oder indirekt mit der Axialkraft und dem Schnittmoment zusammen. Die Hauptfaktoren, die die Axialkraft und das Axialmoment beeinflussen, sind die Vorschubgeschwindigkeit, die Schnittgeschwindigkeit, die Faserbündelform und das Vorhandensein oder Fehlen von vorgeformten Löchern, die sich auch auf die Axialkräfte und das Axialmoment auswirken. Die Axialkraft und das Drehmoment nehmen mit zunehmender Vorschubgeschwindigkeit und Schnittgeschwindigkeit zu. Mit zunehmender Vorschubgeschwindigkeit nimmt die Dicke der Schneidschicht zu, und mit zunehmender Schneidgeschwindigkeit nimmt die Anzahl der geschnittenen Fasern pro Zeiteinheit zu und der Werkzeugverschleiß nimmt rasch zu, so dass die Axialkraft und das Drehmoment zunehmen.
Die Axialkraft kann in eine statische Kraftkomponente FS und eine dynamische Kraftkomponente FD unterteilt werden. Die Kraftkomponente der Axialkraft wirkt sich unterschiedlich auf die Schneide aus, und die statische Kraftkomponente FS der Axialkraft beeinflusst das Schneiden der Meißelkante. Die dynamische Komponentenkraft FD wirkt sich hauptsächlich auf das Schneiden der Hauptschneide aus, und die dynamische Komponentenkraft FD hat einen größeren Einfluss auf die Oberflächenrauheit als die statische Komponentenkraft FS. Die Axialkraft nimmt mit der Vorschubgeschwindigkeit zu und der Einfluss der Schnittgeschwindigkeit auf die Axialkraft ist nicht ersichtlich. Außerdem nimmt bei vorgefertigten Löchern, wenn die Öffnung kleiner als 0,4 mm ist, die statische Komponentenkraft FS mit zunehmender Öffnung stark ab, während die dynamische Komponente FD mit abflachender Tendenz abnimmt.
Aufgrund der unterschiedlichen Verarbeitungseigenschaften der Verbundmatrix und der Verstärkungsfasern wirken sich das Matrixharz und die Fasern beim mechanischen Bohren unterschiedlich auf die Axialkraft aus. Khashaba untersuchte die Auswirkungen von Matrix- und Fasertypen auf Axialkräfte und Drehmomente:
Es wurde festgestellt, dass die Form des Faserbündels einen signifikanten Einfluss auf die Axialkraft hatte und die Art des Matrixharzes einen geringen Einfluss auf die Axialkraft hatte.
II. Verschleiß und Bruch des Bohrers
Der Verschleiß von PCB-Verbund-Mikrobohrern umfasst chemischen Verschleiß und Reibungsverschleiß. Der chemische Verschleiß wird durch den chemischen Angriff des Pyrolyseprodukts verursacht, das vom PCB-Material auf das Co-Bindemittel im mikrobohrten WC-Co-Hartmetall freigesetzt wird. Bei ca. 300 ° C ist diese Erosionsreaktion deutlicher geworden. Bei einer Bohrgeschwindigkeit von weniger als 150 mm / min ist chemischer Verschleiß nicht mehr die Hauptverschleißform, und Reibung und Verschleiß werden zur Hauptverschleißform. Der Verschleiß des PCB-Mikrobohrers hängt auch mit dem Verhältnis von Schnittgeschwindigkeit, Vorschubgeschwindigkeit und Meißelradius zur Faserbündelbreite zusammen. Untersuchungen von Inoue et al. Zeigen, dass: Das Verhältnis des Radius des Bohrers zur Breite des Faserbündels (Glasfaser) hat einen großen Einfluss auf die Standzeit: Je größer das Verhältnis, desto größer die Faserbündelbreite des Fräsers und desto größer der Werkzeugverschleiß.
In der Praxis bohrt der neue Bohrer bis zu 2.500 Löcher zum Schleifen.
Den Bohrer zum ersten Mal schleifen, bis zu 2000 Löcher bohren und erneut schleifen.
Das zweite Schleifen des Bohrers, das bis zu 1500 Löcher bohrt, muss erneut geschliffen werden.
Beim dritten Bohren des Bohrers wurden bis zu 1000 Löcher gebohrt und der Bohrer wurde verschrottet.
Während der Mikroporenbearbeitung der Leiterplatte nehmen die Axialkraft und das Drehmoment mit zunehmender Vorschubgeschwindigkeit und Bohrtiefe zu, und der Hauptgrund hängt mit dem Zustand der Spanabfuhr zusammen. Mit zunehmender Bohrtiefe ist die Spanabfuhr schwierig: In diesem Fall steigt die Schneidetemperatur, das Harzmaterial schmilzt und bindet die Glasfasern und die Kupferfolienstücke fest, um einen zähen Schneidkörper zu bilden. Dieser Schneidkörper hat eine Affinität zum PCB-Matrixmaterial. Sobald ein solcher Schneidkörper hergestellt ist, wird die Abgabe der Späne gestoppt und die Axialkraft und das Drehmoment werden stark erhöht, wodurch der mikroporöse Bohrer bricht. Die Bruchform des PCB-Mikrolochbohrers weist Knicken, Torsionsbrechen und Knicken und Torsionsbrechen auf und im Allgemeinen existieren beide nebeneinander. Die Bruchbedingung ist hauptsächlich das Verstopfen der Späne, was ein Schlüsselfaktor für die Erhöhung des Bohrmoments ist. Die Reduzierung der Axialkraft und des Schnittmoments ist der Schlüssel zur Reduzierung des Bruchs des Mikrolochbohrers.
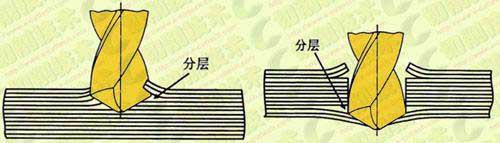
III. Bohren Schaden in Form von
1, Schichtung
Beim mechanischen Bohren von GFK-Laminaten (glasfaserverstärkt) können verschiedene Beschädigungen auftreten. Die schwerwiegendste davon ist die Delaminierung zwischen den Schichten, die zu einem starken Abfall der Materialeigenschaften um die Porenwände führt, und die von der Bohrerspitze ausgeübte Axialkraft ist die Hauptursache für die Delaminierung. Die Schichtung kann in Bohrablösung und Bohrablösung unterteilt werden. Die Bohrablösung tritt auf, wenn die Schneidkante des Bohrers in Kontakt mit der Laminierplatte ist und die in Umfangsrichtung in Umfangsrichtung wirkende Schneidkraft durch die Schneidnut des Bohrers von der Schicht getrennt ist, um einen geschichteten Bereich auf der Oberfläche der Laminierplatte zu bilden. Das Bohren der Delamination erfolgt, wenn sich der Bohrer dem Boden des Laminats nähert. Da die Dicke des ungeschnittenen Materials immer dünner wird, wird die Fähigkeit, einer Verformung zu widerstehen, weiter verringert, und eine Schichtbildung tritt auf, wenn die Last die Haftung zwischen den Laminaten übersteigt. Dies geschah, bevor das Laminat durchgebohrt wurde. Axialkräfte sind die Hauptursache für Delamination, und die Schnittgeschwindigkeit, der Substrat- und Faserbündeltyp wirken sich auch auf die Delamination aus. Das Bohren und Delaminieren von Epoxid-Verbundwerkstoffen nimmt mit zunehmender Bohrgeschwindigkeit ab, und der Grad der Delaminierung ist höher als der des Bohrens. Die wichtigsten Maßnahmen zur Reduzierung der Schichtung sind: Variable Vorschubtechnologie, voreingestellte Führungslöcher und Polsterung werden verwendet. Beim nicht unterstützten Bohren wird ein viskoser Dämpfer oder dergleichen verwendet.
2, Lochwandschaden
Die Mikroporen werden auf die Verbundleiterplatte gebohrt, und verschiedene Formen der Beschädigung, die um die Löcher herum auftreten, führen zu einer Verringerung der Isolation zwischen den Löchern und einem Bruch in der Kupferschicht der Löcher nach der Metallisierung der Löcher. Der relative Winkel zwischen der Schneidrichtung und der Faserrichtung, die Dicke des Glasfaserbündels an der Lochwand, die Position der Bohrspitze auf dem Glasgewebe usw. haben alle unterschiedliche Auswirkungen auf die Beschädigung der Lochwand. Das Glasfaser / Epoxy-Verbundmaterial wurde mit einem Bohrer mit 1,0 mm Durchmesser bei einer Geschwindigkeit von 5000 U / min gebohrt (8 Schichten von 90 ° versetzt, 0,2 mm pro Schicht). Tests zeigen, dass der Grad der Beschädigung um jedes Loch unterschiedlich ist und die erste, dritte, fünfte, siebte und achte Schicht von Faserfalten groß ist, mit einem maximalen Vorsprung von 30 μm; 2,4,6 Falten Projizieren Faser während der Schicht klein ist, bei weniger als der Mindest 5 um. Im Überlappungsbereich des Schussfadens und des Kettfadens ist die Faserbündeldicke bei einem Faserwinkel von 45 ° am größten und die Lochwandschadensbreite am größten; Im mittleren Bereich tritt die maximale Schadensbreite in einem Winkel von ca. 90 ° zum Winkel der Faser auf.
2, Lochwandschaden
Die Mikroporen werden auf die Verbundleiterplatte gebohrt, und verschiedene Formen der Beschädigung, die um die Löcher herum auftreten, führen zu einer Verringerung der Isolation zwischen den Löchern und einem Bruch in der Kupferschicht der Löcher nach der Metallisierung der Löcher. Der relative Winkel zwischen der Schneidrichtung und der Faserrichtung, die Dicke des Glasfaserbündels an der Lochwand, die Position der Bohrspitze auf dem Glasgewebe usw. haben alle unterschiedliche Auswirkungen auf die Beschädigung der Lochwand. Das Glasfaser / Epoxy-Verbundmaterial wurde mit einem Bohrer mit 1,0 mm Durchmesser bei einer Geschwindigkeit von 5000 U / min gebohrt (8 Schichten von 90 ° versetzt, 0,2 mm pro Schicht). Tests zeigen, dass der Grad der Beschädigung um jedes Loch unterschiedlich ist und die erste, dritte, fünfte, siebte und achte Schicht von Faserfalten groß ist, mit einem maximalen Vorsprung von 30 μm; 2,4,6 Falten Projizieren Faser während der Schicht klein ist, bei weniger als der Mindest 5 um. Im Überlappungsbereich des Schussfadens und des Kettfadens ist die Faserbündeldicke bei einem Faserwinkel von 45 ° am größten und die Lochwandschadensbreite am größten; Im mittleren Bereich tritt die maximale Schadensbreite in einem Winkel von ca. 90 ° zum Winkel der Faser auf.
2, Lochwandschaden
Bohren Sie Mikroporen auf eine Verbundplatine. Verschiedene Formen der Beschädigung, die um die Löcher herum auftreten, führen zu einer Abnahme der Isolation zwischen den Löchern und einem Bruch in der Kupferschicht der Löcher nach der Metallisierung der Löcher. Der relative Winkel zwischen der Schneidrichtung und der Faserrichtung, die Dicke des Glasfaserbündels an der Lochwand, die Position der Bohrspitze auf dem Glasgewebe usw. haben alle unterschiedliche Auswirkungen auf die Wandbeschädigung.
Das Glasfaser / Epoxy-Verbundmaterial wurde mit einem Bohrer mit 1,0 mm Durchmesser bei einer Geschwindigkeit von 5000 U / min gebohrt (8 Schichten von 90 ° versetzt, 0,2 mm pro Schicht). Test zeigte, dass: das Ausmaß der Beschädigung der einzelnen Schichten ist nicht gleich um das Bohrloch, wobei die ersten vorspringenden großen Falten 1,3,5,7,8 Faserschichten, bis zur maximalen Projektion von 30 m; Die 2, 4 und 6 Lagen von Faserfalten sind weniger ausgeprägt und das Minimum beträgt weniger als 5 & mgr; m. Im Überlappungsbereich des Schussfadens und des Kettfadens ist die Faserbündeldicke bei einem Faserwinkel von 45 ° am größten und die Lochwandschadensbreite am größten; Im mittleren Bereich tritt die maximale Schadensbreite in einem Winkel von ca. 90 ° zum Winkel der Faser auf.
Der Einfluss der Hauptdeklination des Werkzeugs auf die Oberflächenrauheit der bearbeiteten Lochwand: Bei einer Hauptdeklination von 30 ° ist die Oberflächenrauheit der Porenwand mit bis zu 50 μm am größten.
3, Flecken
Beim mechanischen Bohren eines Verbundwerkstoffes entsteht die Reibung zwischen der Meißelkante und dem Verbundwerkstoff, dem Gegenkegel und der Wandung des Loches. Eine große Menge an Schneidwärme, die durch das feine Schneiden zwischen der Kante des Bohrers und der Wand des Lochs erzeugt wird und durch den Bohrer gedreht wird, bewirkt, dass das Harz schmilzt. Und kleben Sie die Kupferfolie und die Lochwand an der Zwischenschicht oder dem Loch des Verbundstoffs, um einen Fleck zu bilden. Durch richtiges Schneiden und Schleifen des Mikrobohrers kann die Entstehung von Flecken und der Fleckenindex verringert werden.
4, Grate