Bearbeitungstechnologie von Praezisionsduesen Teilen aus Edelstahl
Die Dreh-Fräs-Verbundbearbeitung vieler kleiner Präzisionsteile aus Verbundwerkstoffen mit hoher Präzision, mehreren Chargen und komplexer Form stellt die mechanische Fertigungsindustrie vor große Herausforderungen. Mit der rasanten Entwicklung der Luft- und Raumfahrt, Hydraulik, Kommunikation, Mikroelektronik, Medizintechnik und anderen Branchen. Traditionelle CNC-Bearbeitungsverfahren und Bearbeitungsverfahren waren nicht in der Lage, die Bedürfnisse der verschiedenen, individuellen und Profilbearbeitung gerecht zu werden. Das verarbeitende Gewerbe entwickelt sich rasant in Richtung hoher Effizienz, Präzision und Compoundierung.
In Anbetracht der Eigenschaften solcher Teile wenden die meisten inländischen Unternehmen Methoden zur Verbesserung der Anlagenleistung und zur Entwicklung neuer Verarbeitungstechniken an, um die Verarbeitungsanforderungen zu erfüllen und die Produktionseffizienz zu verbessern. In diesem Papier wird ein typisches Verbunddüsenteil als Beispiel verwendet, und es werden die Eigenschaften und Vorteile des Präzisions-Drehautomaten B0326-II verwendet. Unter den Gesichtspunkten der Werkzeugauswahl, der Entwicklung von Bearbeitungsprozessen, des Entwurfs der wichtigsten Bearbeitungsrouten und der Problemanalyse der Probebearbeitung wurde eine eingehende Untersuchung der Bearbeitungstechnologie durchgeführt. Das Problem der großen Losgröße, der geringen Effizienz und der schwierigen Verarbeitung solcher Teile wird gelöst.
1. Analyse der Teile der Verarbeitung Technologie
Technische Anforderungen an die Teile
Abbildung 1 zeigt die Düsenteile in einer medizinischen Vorrichtung. Die monatliche Produktion beträgt 20.000 Stück, das Material ist Edelstahl 1Cr18Ni9Ti, was ein schwieriges Material ist; Die bearbeitungselemente dieses teils sind mehr, einschließlich drehen außenkreis und gewinde, fräsen ebene fläche; Bohren von Mittelloch und Bodenloch, Bohrloch, Gewindebohrung usw. Außerdem müssen die Maßhaltigkeit und Oberflächenrauheit der Teile hoch sein, und die Koaxialität der Löcher an beiden Enden beträgt 0,02 mm.
Auf der Grundlage der obigen Analyse ergeben sich folgende Verarbeitungsschwierigkeiten für das Teil:
Gewährleisten Sie die Maßhaltigkeit der Außen- und Innenbohrungen, die Koaxialitätsanforderungen der beiden Innenbohrungen und die Massenproduktion.
Düsenteil Verarbeitung
Der Präzisions-Drehautomat B0326-II wird hauptsächlich zum Drehen eingesetzt. Es hat auch bohren, gravieren, fräsen nut, fräsen zähne, gewindeschneiden, reiben und so weiter. Die kombinierte Mehrprozess-Bearbeitungspräzisionswerkzeugmaschine verfügt über Indexierungsfunktionen für die C-Achse und die Y-Achse, die das Fräsen, Bohren, Gewindebohren und andere Prozesse in der Radialebene ausführen können. Das Doppelspindelsteuersystem kann die automatische Positionierung und Zuführung der Hinterachse nach der spindelseitigen Verarbeitung realisieren und wirkungsvoll das Problem der geringen Effizienz und Genauigkeit durch das Drehen des Werkstückes verursacht lösen.
Wie in Abbildung 2 gezeigt, ist gemäß den Merkmalen der Werkzeugmaschine die Gestaltung der Außenkontur-Bearbeitungsroute des Teils: Spindelseite → Stirnfläche drehen → Außenkreis auf 39 mm drehen → Außenkreis auf 65,1 mm zum heckachseitigen Wagenende drehen.
Gemäß der obigen Analyse ist das Verarbeitungsdesign von Düsenteilen in Tabelle 1 gezeigt.
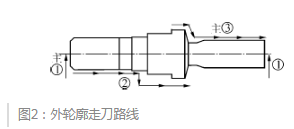
Außenkontur Fräsbahnen Zeichnung
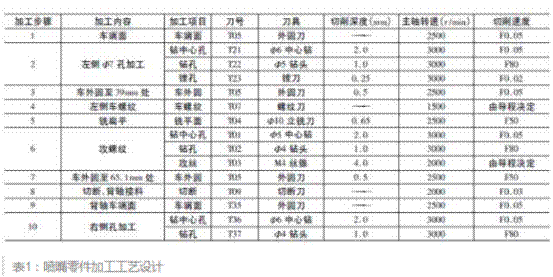
2. Der Schlüsselschritt des Designprozesses
Bearbeitung des linken Lochs
Das Loch auf der linken Seite wird am 5-Loch-Werkzeughalter T31-T35 auf der Spindelseite bearbeitet. Der 5-Loch-Werkzeughalter verfügt über ein kompaktes Layout, das die Zeit bis zum Durchlaufen des Messers verkürzt und eine hohe Bearbeitungseffizienz aufweist.
Bohrung Φ7 erfordert eine höhere Präzision und übernimmt den Bohrprozess. Die Lochtiefe von 38mm gehört zur Tieflochbearbeitung. Die Schwierigkeit liegt in der Abkühlung des Schneidbereichs des Bohrers beim Bohren des Lochs und dem Problem der Spanabfuhr. Hochdruckölkühlung und G83-Hackbohrer können effektiv Bruch und Verwicklungen von Spänen verhindern.
Spezifische Schritte:
Bohren Sie zuerst das Mittelloch von ca. 2 mm mit einem 6er-Zentrierbohrer. Die Tiefe sollte nicht zu gering sein, da sonst die Lochfase Grate aufweist. Bohren Sie dann mit einem Bohrer Φ5,8 und lassen Sie eine Bearbeitungszugabe von ca. 0,5 mm auf einer Seite. Aufgrund der hohen Härte des Teilematerials sollte der größte Teil der verbleibenden Menge im Prozess entfernt und die Hochdruckölkühlung eingeschaltet werden. Schließlich wird die Lochgröße durch Bohren sichergestellt, und der Schneidemodus ist Hochgeschwindigkeits- und Niedrigvorschubmodus. Bohrstange S25.0G-SVNR12SN ist ausgewählt, Messertyp VNBR0620-01, Spindeldrehzahl 3000 U / min, Schnitttiefe ap = 0,25 mm, Vorschubgeschwindigkeit f = 0,02 mm / r.
Drehen Sie den äußeren Kreis auf 39 mm
Wenn die erste rechteckige Bearbeitungsroute ausgeführt wird, wird sie zu Punkt A verarbeitet, wobei die Schnitttiefe jedes Mal 0,5 mm beträgt, die Vorschubgeschwindigkeit 0,05 mm / r beträgt und die Bearbeitung von drei Messern vervollständigt wird. Wenn die zweite rechteckige Bearbeitungsroute ausgeführt wird, wird sie zu Punkt B verarbeitet, jedes Mal, wenn die Schnitttiefe 0,3 mm beträgt, die Vorschubgeschwindigkeit 0,03 mm / r beträgt und das Vierermesser fertiggestellt ist; Die Endbearbeitungstiefe beträgt 0,1 mm und der Vorschub 0,01 mm / r. Dieser Schritt verwendet Kyocera SCLCR1616H-12 Außenrundmesser, Klinge Typ CCGT09T304M, die Oberflächenqualität der Teile ist besser.
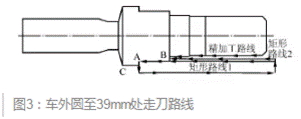
Abbildung 3. Drehen nimmt die Fräsbahnen
Linksdrehender Faden
Da das M10-Gewinde mit anderen Teilen des medizinischen Geräts abgeglichen werden muss, muss der Gewindedurchmesser kontrolliert werden, und der Rauheitswert erreicht Ra0,8.
Drehen Sie das Gewinde in drei Schritten, um die Anforderungen zu erfüllen:
Erster Schritt: Das äußere Kreismesser dreht den großen Durchmesser um 0,2 mm.
Der zweite Schritt, Nachdem das Gewindedrehen zum ersten Mal abgeschlossen ist, wird das äußere Kreismesser erneut aufgerufen, sich entlang der Gewindefläche zu drehen, um den oberen Grat zu entfernen, aber der Grat wird in Richtung der Unterseite des Zahns gedrückt.
dritter Schritt, Drehen Sie die letzten beiden Messer mit einem Gewindeschneider entlang des Gewindes und drehen Sie sie dann erneut, um im zweiten Schritt die Grate in Richtung Zahnunterseite zu entfernen.
Flach fräsen
Das Planfräsen nutzt hauptsächlich die Spindel-C-Achsen-Indexierungsfunktion des Präzisions-Drehautomaten B0326-II, um das sekundäre Spannproblem effektiv zu lösen. Die Gesamtdicke der Frässchicht in diesem Schritt beträgt 2,3 mm, und ein Schaftfräser mit großem Durchmesser kann ausgewählt werden, um die Verarbeitungseffizienz zu verbessern.
Entsprechend der Analyse wird der Durchmesser Φ10 Schaftfräser gewählt. Nach dem Abbremsen der Spindel wird diese in drei Fräsmaschinen aufgeteilt.
Die Frästiefe betrug erstmals 0,65 mm.
Beim zweiten Mal beträgt die Frästiefe 0,65 mm.
Zum dritten Mal beträgt die Frästiefe 0,35 mm.
Bei jedem Fräsvorschub von 50 mm / min wird die C-Achse um 180 ° gedreht und die andere Seite bearbeitet. Nachdem das Hobelfräsen beendet ist, werden am äußeren Ende des Hobels Grate sichtbar. Zu diesem Zeitpunkt ist es besser, ein externes Kreismesser zum Entgraten entlang des äußeren Kreises von Φ13 zu verwenden, und der Effekt ist besser.
Drehen Sie den äußeren Kreis auf 65,1 mm
Die Schwierigkeit beim Außendrehen besteht darin, dass der C-Bereich rillenförmig ist, was den Werkzeugwinkel begrenzt und das Schneiden des Messers erschwert. Herkömmliche kreisförmige Schneidwerkzeuge können leicht eingreifen und kollabieren, und die Oberflächenqualität der Rillen ist schlecht.
Daher wird das Drehen dreimal ausgeführt, und der Weg des Schneidens ist in 4 gezeigt. Zum ersten Mal wird der Rillenschneider mit einer Breite von 3 mm so ausgewählt, dass er mit einer Bearbeitungszugabe von 0,1 mm bis zum Rillengrund schneidet, und das Werkzeug wird entlang der Route 1 vorgeschoben, um den Schneidraum für die nächste Drehung bereitzustellen.
Zum zweiten Mal wird das herkömmliche externe 90 ° -Drehwerkzeug ausgewählt, und das Werkzeug wird entlang der Route 2 zugeführt und gemäß der rechteckigen G90-Route bearbeitet, und der Gesamtbetrag von 6,4 mm wird entfernt;
Beim dritten Mal verwenden Sie das hintere Kehrwerkzeug und folgen der Route 3 zum Schlichten. Aufgrund des kleinen Raums in der Nut kann die äußere 90 ° -Kreisschneiderschneide leicht gestört werden. Die Verwendung des hinteren Kehrmessers kann das Problem effektiv lösen und den Rauheitswert am Grund der Nut sicherstellen.
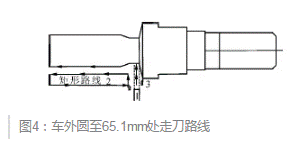
Abbildung 4. Drehen Sie den äußeren Kreis auf 65,1 mm und nehmen Sie die Schneidepfade
Das hintere Wellenaufnahmeloch bohren
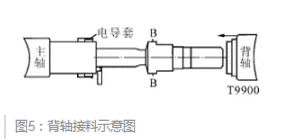
Abbildung 5. Skizze der Hinterachse Verbindung
3. Testverarbeitung Problemanalyse
Nachdem die Verarbeitungstechnologie entworfen wurde, wird die Programmierung ausgeführt. Nach wiederholter Verifizierung der Simulation zeigte die erste Probeverarbeitung des Teils einen Gratanstieg am Boden des Φ7-Lochs. Φ4 Blende ohne 60 ° Fase. Φ7 Lochtiefenabweichung und andere Probleme.
Die Genauigkeit der Lochgröße Φ7 und die Oberflächenqualität dieses Teils sind hoch. Wenn der Bohrer Φ5 bis zum Bohrlochgrund gebohrt wird, wird der Span aufgrund der Extrusion nicht rechtzeitig abgegeben, wodurch der Grat am Bohrlochgrund aufgedreht wird, was sich auf die Qualität des Teils auswirkt. Nehmen Sie nach wiederholten Versuchen die folgenden Anpassungen vor: Wenn der Bohrer bis zum Grund des Lochs gebohrt wird, tritt der Bohrer nicht direkt aus, hebt 0,1 mm entlang des Lochs an, verzögert 0,2 s (dh G04U0,2) und verlässt dann den Grund des Lochs, um den Aufwärtsgrat zu entfernen .
Wie in Abbildung 6 dargestellt. Die Fase mit 4 Löchern wird mit dem Zentrierbohrer mit 6 Löchern bearbeitet. Das Nicht-Anfasen der Öffnung wird beurteilt, wenn das Mittelloch zu tief gebohrt wird. und die Kegeloberfläche hat am Boden des zentralen Bohrlochs 60 ° überschritten, und die Verschleißkompensation +0,5 auf der Rückseite T36 kann das Problem lösen.
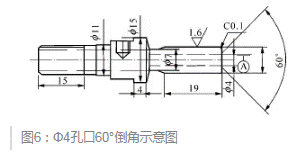
Abbildung 6. Φ4 Loch 60 ° Anfasen Diagramm
4. Zusammenfassung
Nach der Inbetriebnahme der Düsenteile ist die Werkzeugmaschine mit einer automatischen Zuführung ausgestattet. Das Zuführen, Verarbeiten, Empfangen und Entladen erfolgt vollautomatisch und der Verarbeitungsbedarf von 20.000 Stück pro Monat wird realisiert. Es löst die Probleme der Miniaturisierung, der Vielzahl, des hohen Volumens und der hohen Präzision, die in modernen Fertigungsprozessen auftreten.
Durch die Forschung von B0326-II Präzision Drehmaschine kleine Composite-Wellenteile Bearbeitungstechnologie. Es bietet die technische Grundlage für die Förderung einer neuen Art der kombinierten Bearbeitungstechnologie für Drehen und Fräsen sowie Referenz und Referenz für die Bearbeitung ähnlicher Teile.
In Anbetracht der Eigenschaften solcher Teile wenden die meisten inländischen Unternehmen Methoden zur Verbesserung der Anlagenleistung und zur Entwicklung neuer Verarbeitungstechniken an, um die Verarbeitungsanforderungen zu erfüllen und die Produktionseffizienz zu verbessern. In diesem Papier wird ein typisches Verbunddüsenteil als Beispiel verwendet, und es werden die Eigenschaften und Vorteile des Präzisions-Drehautomaten B0326-II verwendet. Unter den Gesichtspunkten der Werkzeugauswahl, der Entwicklung von Bearbeitungsprozessen, des Entwurfs der wichtigsten Bearbeitungsrouten und der Problemanalyse der Probebearbeitung wurde eine eingehende Untersuchung der Bearbeitungstechnologie durchgeführt. Das Problem der großen Losgröße, der geringen Effizienz und der schwierigen Verarbeitung solcher Teile wird gelöst.
1. Analyse der Teile der Verarbeitung Technologie
Technische Anforderungen an die Teile
Abbildung 1 zeigt die Düsenteile in einer medizinischen Vorrichtung. Die monatliche Produktion beträgt 20.000 Stück, das Material ist Edelstahl 1Cr18Ni9Ti, was ein schwieriges Material ist; Die bearbeitungselemente dieses teils sind mehr, einschließlich drehen außenkreis und gewinde, fräsen ebene fläche; Bohren von Mittelloch und Bodenloch, Bohrloch, Gewindebohrung usw. Außerdem müssen die Maßhaltigkeit und Oberflächenrauheit der Teile hoch sein, und die Koaxialität der Löcher an beiden Enden beträgt 0,02 mm.
Auf der Grundlage der obigen Analyse ergeben sich folgende Verarbeitungsschwierigkeiten für das Teil:
Gewährleisten Sie die Maßhaltigkeit der Außen- und Innenbohrungen, die Koaxialitätsanforderungen der beiden Innenbohrungen und die Massenproduktion.
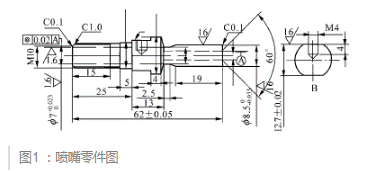
Düsenteil Verarbeitung
Der Präzisions-Drehautomat B0326-II wird hauptsächlich zum Drehen eingesetzt. Es hat auch bohren, gravieren, fräsen nut, fräsen zähne, gewindeschneiden, reiben und so weiter. Die kombinierte Mehrprozess-Bearbeitungspräzisionswerkzeugmaschine verfügt über Indexierungsfunktionen für die C-Achse und die Y-Achse, die das Fräsen, Bohren, Gewindebohren und andere Prozesse in der Radialebene ausführen können. Das Doppelspindelsteuersystem kann die automatische Positionierung und Zuführung der Hinterachse nach der spindelseitigen Verarbeitung realisieren und wirkungsvoll das Problem der geringen Effizienz und Genauigkeit durch das Drehen des Werkstückes verursacht lösen.
Wie in Abbildung 2 gezeigt, ist gemäß den Merkmalen der Werkzeugmaschine die Gestaltung der Außenkontur-Bearbeitungsroute des Teils: Spindelseite → Stirnfläche drehen → Außenkreis auf 39 mm drehen → Außenkreis auf 65,1 mm zum heckachseitigen Wagenende drehen.
Gemäß der obigen Analyse ist das Verarbeitungsdesign von Düsenteilen in Tabelle 1 gezeigt.
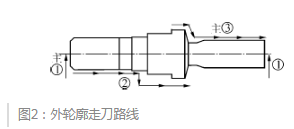
Außenkontur Fräsbahnen Zeichnung
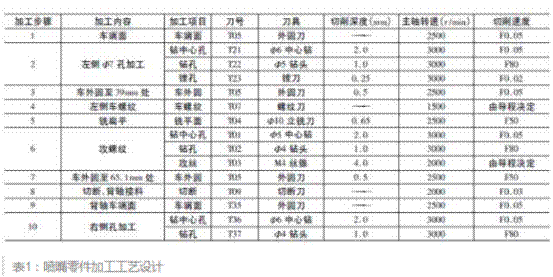
Düsenteil Verarbeitung Design Prozesstabelle
2. Der Schlüsselschritt des Designprozesses
Bearbeitung des linken Lochs
Das Loch auf der linken Seite wird am 5-Loch-Werkzeughalter T31-T35 auf der Spindelseite bearbeitet. Der 5-Loch-Werkzeughalter verfügt über ein kompaktes Layout, das die Zeit bis zum Durchlaufen des Messers verkürzt und eine hohe Bearbeitungseffizienz aufweist.
Bohrung Φ7 erfordert eine höhere Präzision und übernimmt den Bohrprozess. Die Lochtiefe von 38mm gehört zur Tieflochbearbeitung. Die Schwierigkeit liegt in der Abkühlung des Schneidbereichs des Bohrers beim Bohren des Lochs und dem Problem der Spanabfuhr. Hochdruckölkühlung und G83-Hackbohrer können effektiv Bruch und Verwicklungen von Spänen verhindern.
Spezifische Schritte:
Bohren Sie zuerst das Mittelloch von ca. 2 mm mit einem 6er-Zentrierbohrer. Die Tiefe sollte nicht zu gering sein, da sonst die Lochfase Grate aufweist. Bohren Sie dann mit einem Bohrer Φ5,8 und lassen Sie eine Bearbeitungszugabe von ca. 0,5 mm auf einer Seite. Aufgrund der hohen Härte des Teilematerials sollte der größte Teil der verbleibenden Menge im Prozess entfernt und die Hochdruckölkühlung eingeschaltet werden. Schließlich wird die Lochgröße durch Bohren sichergestellt, und der Schneidemodus ist Hochgeschwindigkeits- und Niedrigvorschubmodus. Bohrstange S25.0G-SVNR12SN ist ausgewählt, Messertyp VNBR0620-01, Spindeldrehzahl 3000 U / min, Schnitttiefe ap = 0,25 mm, Vorschubgeschwindigkeit f = 0,02 mm / r.
Drehen Sie den äußeren Kreis auf 39 mm
Bei diesem Schritt handelt es sich um die Außenkonturbearbeitung, bei der es darum geht, die Bearbeitungseffizienz zu verbessern und die Oberflächenqualität sicherzustellen. Berücksichtigen Sie die strukturellen Eigenschaften des Teils und die Materialeigenschaften. Das Routendesign des Fräsers ist in Abbildung 3 dargestellt. Dieser Schritt (LL) (JP2) wird in drei Schritten ausgeführt. Die ersten beiden verwenden den rechteckigen Pfad G90, um den größten Teil der Zulage und den dritten Abschluss zu entfernen. In den ersten beiden Fällen wurde der G90-Rechteckschneider verwendet, um den größten Teil der Zulage zu entfernen. Das Finishing ist zum dritten Mal abgeschlossen.
Wenn die erste rechteckige Bearbeitungsroute ausgeführt wird, wird sie zu Punkt A verarbeitet, wobei die Schnitttiefe jedes Mal 0,5 mm beträgt, die Vorschubgeschwindigkeit 0,05 mm / r beträgt und die Bearbeitung von drei Messern vervollständigt wird. Wenn die zweite rechteckige Bearbeitungsroute ausgeführt wird, wird sie zu Punkt B verarbeitet, jedes Mal, wenn die Schnitttiefe 0,3 mm beträgt, die Vorschubgeschwindigkeit 0,03 mm / r beträgt und das Vierermesser fertiggestellt ist; Die Endbearbeitungstiefe beträgt 0,1 mm und der Vorschub 0,01 mm / r. Dieser Schritt verwendet Kyocera SCLCR1616H-12 Außenrundmesser, Klinge Typ CCGT09T304M, die Oberflächenqualität der Teile ist besser.
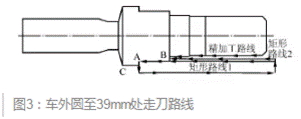
Abbildung 3. Drehen nimmt die Fräsbahnen
Linksdrehender Faden
Da das M10-Gewinde mit anderen Teilen des medizinischen Geräts abgeglichen werden muss, muss der Gewindedurchmesser kontrolliert werden, und der Rauheitswert erreicht Ra0,8.
Drehen Sie das Gewinde in drei Schritten, um die Anforderungen zu erfüllen:
Erster Schritt: Das äußere Kreismesser dreht den großen Durchmesser um 0,2 mm.
dritter Schritt, Drehen Sie die letzten beiden Messer mit einem Gewindeschneider entlang des Gewindes und drehen Sie sie dann erneut, um im zweiten Schritt die Grate in Richtung Zahnunterseite zu entfernen.
Flach fräsen
Das Planfräsen nutzt hauptsächlich die Spindel-C-Achsen-Indexierungsfunktion des Präzisions-Drehautomaten B0326-II, um das sekundäre Spannproblem effektiv zu lösen. Die Gesamtdicke der Frässchicht in diesem Schritt beträgt 2,3 mm, und ein Schaftfräser mit großem Durchmesser kann ausgewählt werden, um die Verarbeitungseffizienz zu verbessern.
Entsprechend der Analyse wird der Durchmesser Φ10 Schaftfräser gewählt. Nach dem Abbremsen der Spindel wird diese in drei Fräsmaschinen aufgeteilt.
Die Frästiefe betrug erstmals 0,65 mm.
Beim zweiten Mal beträgt die Frästiefe 0,65 mm.
Zum dritten Mal beträgt die Frästiefe 0,35 mm.
Bei jedem Fräsvorschub von 50 mm / min wird die C-Achse um 180 ° gedreht und die andere Seite bearbeitet. Nachdem das Hobelfräsen beendet ist, werden am äußeren Ende des Hobels Grate sichtbar. Zu diesem Zeitpunkt ist es besser, ein externes Kreismesser zum Entgraten entlang des äußeren Kreises von Φ13 zu verwenden, und der Effekt ist besser.
Drehen Sie den äußeren Kreis auf 65,1 mm
Die Schwierigkeit beim Außendrehen besteht darin, dass der C-Bereich rillenförmig ist, was den Werkzeugwinkel begrenzt und das Schneiden des Messers erschwert. Herkömmliche kreisförmige Schneidwerkzeuge können leicht eingreifen und kollabieren, und die Oberflächenqualität der Rillen ist schlecht.
Daher wird das Drehen dreimal ausgeführt, und der Weg des Schneidens ist in 4 gezeigt. Zum ersten Mal wird der Rillenschneider mit einer Breite von 3 mm so ausgewählt, dass er mit einer Bearbeitungszugabe von 0,1 mm bis zum Rillengrund schneidet, und das Werkzeug wird entlang der Route 1 vorgeschoben, um den Schneidraum für die nächste Drehung bereitzustellen.
Zum zweiten Mal wird das herkömmliche externe 90 ° -Drehwerkzeug ausgewählt, und das Werkzeug wird entlang der Route 2 zugeführt und gemäß der rechteckigen G90-Route bearbeitet, und der Gesamtbetrag von 6,4 mm wird entfernt;
Beim dritten Mal verwenden Sie das hintere Kehrwerkzeug und folgen der Route 3 zum Schlichten. Aufgrund des kleinen Raums in der Nut kann die äußere 90 ° -Kreisschneiderschneide leicht gestört werden. Die Verwendung des hinteren Kehrmessers kann das Problem effektiv lösen und den Rauheitswert am Grund der Nut sicherstellen.
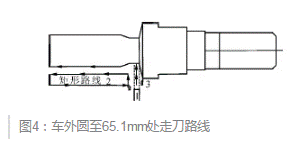
Abbildung 4. Drehen Sie den äußeren Kreis auf 65,1 mm und nehmen Sie die Schneidepfade
Das hintere Wellenaufnahmeloch bohren
Wie in Abbildung 5 gezeigt. Nachdem die gesamte Bearbeitung auf der Seite der Hauptwelle abgeschlossen ist, wird das Schneidmesser in die Schneidposition gebracht, die hintere Welle wird mit der Hauptwelle zentriert, die hintere Welle T9900 wird entlang der Richtung B-B der Hauptwelle gespannt. und die Hauptrückenwelle wird gleichzeitig gedreht, was die Steifigkeit stark erhöht. Schneiden Sie die hintere Welle ab, um das Material aufzunehmen, und verwenden Sie das Werkzeug T35, T36, T37 auf der Rückseite, um die Endfläche und das Bohrloch auszuführen. Die hintere Achse wird automatisch so positioniert, dass sie mit der konzentrischen Position der Spindel gespannt wird, wodurch der durch das erneute Spannen verursachte Koaxialitätsfehler vermieden wird, die Koaxialitätsanforderungen der Löcher holes7 und Φ4 sichergestellt und das Problem der Koaxialitätsbearbeitung des Teils gelöst werden.
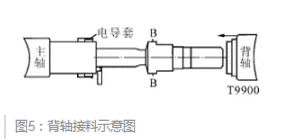
Abbildung 5. Skizze der Hinterachse Verbindung
3. Testverarbeitung Problemanalyse
Nachdem die Verarbeitungstechnologie entworfen wurde, wird die Programmierung ausgeführt. Nach wiederholter Verifizierung der Simulation zeigte die erste Probeverarbeitung des Teils einen Gratanstieg am Boden des Φ7-Lochs. Φ4 Blende ohne 60 ° Fase. Φ7 Lochtiefenabweichung und andere Probleme.
Die Genauigkeit der Lochgröße Φ7 und die Oberflächenqualität dieses Teils sind hoch. Wenn der Bohrer Φ5 bis zum Bohrlochgrund gebohrt wird, wird der Span aufgrund der Extrusion nicht rechtzeitig abgegeben, wodurch der Grat am Bohrlochgrund aufgedreht wird, was sich auf die Qualität des Teils auswirkt. Nehmen Sie nach wiederholten Versuchen die folgenden Anpassungen vor: Wenn der Bohrer bis zum Grund des Lochs gebohrt wird, tritt der Bohrer nicht direkt aus, hebt 0,1 mm entlang des Lochs an, verzögert 0,2 s (dh G04U0,2) und verlässt dann den Grund des Lochs, um den Aufwärtsgrat zu entfernen .
Wie in Abbildung 6 dargestellt. Die Fase mit 4 Löchern wird mit dem Zentrierbohrer mit 6 Löchern bearbeitet. Das Nicht-Anfasen der Öffnung wird beurteilt, wenn das Mittelloch zu tief gebohrt wird. und die Kegeloberfläche hat am Boden des zentralen Bohrlochs 60 ° überschritten, und die Verschleißkompensation +0,5 auf der Rückseite T36 kann das Problem lösen.
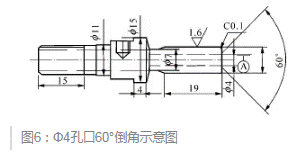
Abbildung 6. Φ4 Loch 60 ° Anfasen Diagramm
Als das erste Produkt getestet wurde, wurde festgestellt, dass die Tiefe des Lochs Φ7 37,8 mm betrug, was 0,2 mm kleiner als die tatsächliche Größe war. Der Grund für die Analyse ist hauptsächlich das spindelseitige Bohrwerkzeug T23, und es gibt eine Abweichung in der Werkzeugeinstellung. Auf der Spindelseite richtet das T23-Bohrwerkzeug das Werkzeug genau aus, und der T23-Verschleißkompensationseingang +0,2. Nach mehrmaligem Debuggen erfüllen die Düsenteile die Abnahmeanforderungen und die Bearbeitungsdüsen sind in Abbildung 7 dargestellt.
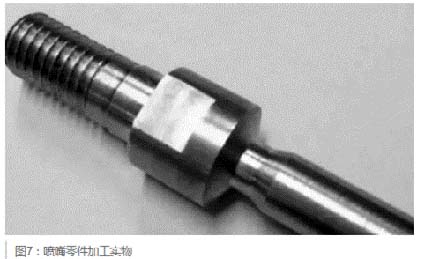
Abbildung 7. Physikalische Bearbeitung der Düsenteile aus rostfreiem Stahl
4. Zusammenfassung
Nach der Inbetriebnahme der Düsenteile ist die Werkzeugmaschine mit einer automatischen Zuführung ausgestattet. Das Zuführen, Verarbeiten, Empfangen und Entladen erfolgt vollautomatisch und der Verarbeitungsbedarf von 20.000 Stück pro Monat wird realisiert. Es löst die Probleme der Miniaturisierung, der Vielzahl, des hohen Volumens und der hohen Präzision, die in modernen Fertigungsprozessen auftreten.
Durch die Forschung von B0326-II Präzision Drehmaschine kleine Composite-Wellenteile Bearbeitungstechnologie. Es bietet die technische Grundlage für die Förderung einer neuen Art der kombinierten Bearbeitungstechnologie für Drehen und Fräsen sowie Referenz und Referenz für die Bearbeitung ähnlicher Teile.