Aluminiumlegierungs-Shell-Versilberung Prozess
Zusammenfassung: Es wurde der Glanzversilberungsprozess untersucht, der durch die Kombination von sekundärer Zinkierung und Cyanidierungsverzinkung vorbehandelt wurde. Der Prozessablauf und die zugehörigen Parameter wurden eingeführt. Die Auswirkungen der Herstellung der Zinkisierungslösung, Temperatur und Zeit auf die Beschichtungsleistung wurden diskutiert. Die Beschichtung, die durch dieses Verfahren erhalten wird, ist fein, mit guter Leichtigkeit und starker Bindungskraft.
Schlüsselwörter: Aluminiumlegierung; Sekundärzinklaugung; Cyanid verzinkt; Helle Versilberung
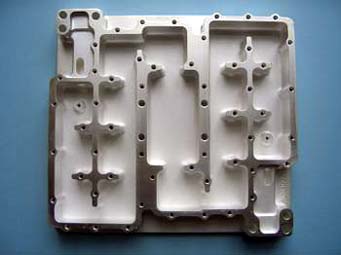
1. Einleitung
Aluminiumlegierungsversilberung ist in der Elektronik, in der Kommunikation, in den Elektrogeräten und in anderen Industrien am meisten benutzt. Da Aluminium jedoch ein sehr aktives Metall ist, hat es eine starke Affinität für Sauerstoff und bildet einen Oxidfilm auf der Oberfläche. Gleichzeitig ist der Wärmeausdehnungskoeffizient von Aluminium und seinen Legierungen sehr verschieden von dem von Silber, was es schwierig macht, Silber auf Aluminiumteilen zu plattieren.
[1]. Je größer die Teilegröße und je komplexer die Form ist, desto schwieriger ist das Plattieren. Viele Teile eines Militärfilters sind versilberte Aluminiumlegierung (Marke 7R04-Hll2) Teile, in denen die Hauptkomponente U, V-Typ Hohlraumversilberung am schwierigsten ist. Die Größe des Hohlraums beträgt 316 mm × 190 mm × 93 mm, die Oberfläche beträgt 40,6 dm² und die innere Hohlraumgröße beträgt 180 mm × 56 mm × 90 mm (tief). Die Form des Hohlraums ist in Abb. 1 dargestellt. Versilberung ist erforderlich (23 ± 2) μm und elektrolytische Passivierung.
Das Teil hat ein großes Volumen und einen tiefen Hohlraum. Um eine versilberte Schicht mit guter Haftung zu erhalten, ist eine Vorbehandlung vor dem Beschichten der Schlüssel. Viele Untersuchungen zur Vorbehandlung von Aluminium und seinen Legierungen wurden im In- und Ausland durchgeführt. Der Autor führte eine große Anzahl von Experimenten auf der Grundlage der Zusammenfassung dieser Methoden durch.
Herauskommen:
Das Vorbehandlungsverfahren, kombiniert mit sekundärer Zinklaugung und Kaliumchloridgalvanisierung, wurde mit Silber neu plattiert, und die meisten Hohlräume hatten Abschälung, Blasenbildung und Vergießen.
In dem Vorbehandlungsprozess, der die sekundäre Zinkauslaugung und die Cyanidierungsverzinkung kombiniert, führt die Cyanidbeschichtung von Kupfer und Silber zu feinen Kristallen, guter Leichtigkeit und starker Bindungskraft, die die Qualitätsanforderungen von Militärprodukten besser erfüllen können.
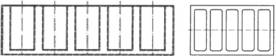
Abbildung 1 Shell-Struktur
Schlüsselwörter: Aluminiumlegierung; Sekundärzinklaugung; Cyanid verzinkt; Helle Versilberung
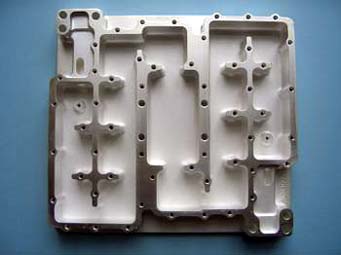
1. Einleitung
Aluminiumlegierungsversilberung ist in der Elektronik, in der Kommunikation, in den Elektrogeräten und in anderen Industrien am meisten benutzt. Da Aluminium jedoch ein sehr aktives Metall ist, hat es eine starke Affinität für Sauerstoff und bildet einen Oxidfilm auf der Oberfläche. Gleichzeitig ist der Wärmeausdehnungskoeffizient von Aluminium und seinen Legierungen sehr verschieden von dem von Silber, was es schwierig macht, Silber auf Aluminiumteilen zu plattieren.
[1]. Je größer die Teilegröße und je komplexer die Form ist, desto schwieriger ist das Plattieren. Viele Teile eines Militärfilters sind versilberte Aluminiumlegierung (Marke 7R04-Hll2) Teile, in denen die Hauptkomponente U, V-Typ Hohlraumversilberung am schwierigsten ist. Die Größe des Hohlraums beträgt 316 mm × 190 mm × 93 mm, die Oberfläche beträgt 40,6 dm² und die innere Hohlraumgröße beträgt 180 mm × 56 mm × 90 mm (tief). Die Form des Hohlraums ist in Abb. 1 dargestellt. Versilberung ist erforderlich (23 ± 2) μm und elektrolytische Passivierung.
Das Teil hat ein großes Volumen und einen tiefen Hohlraum. Um eine versilberte Schicht mit guter Haftung zu erhalten, ist eine Vorbehandlung vor dem Beschichten der Schlüssel. Viele Untersuchungen zur Vorbehandlung von Aluminium und seinen Legierungen wurden im In- und Ausland durchgeführt. Der Autor führte eine große Anzahl von Experimenten auf der Grundlage der Zusammenfassung dieser Methoden durch.
Herauskommen:
Das Vorbehandlungsverfahren, kombiniert mit sekundärer Zinklaugung und Kaliumchloridgalvanisierung, wurde mit Silber neu plattiert, und die meisten Hohlräume hatten Abschälung, Blasenbildung und Vergießen.
In dem Vorbehandlungsprozess, der die sekundäre Zinkauslaugung und die Cyanidierungsverzinkung kombiniert, führt die Cyanidbeschichtung von Kupfer und Silber zu feinen Kristallen, guter Leichtigkeit und starker Bindungskraft, die die Qualitätsanforderungen von Militärprodukten besser erfüllen können.
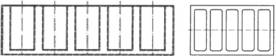
Abbildung 1 Shell-Struktur
2 Prozessspezifikationen
2.1 Prozessablauf
Organische Entfettung - chemische Entfettung - Alkali-Korrosion - Säureätzung - Zinklaugung - Essigsäuresalz - Schwerzinkat - Cyanidverzinkung - Verkupferung - Vorbeschichtetes Silber - Breitsilber - Eine elektrolytische Passivierung wird trockengeblasen und getrocknet.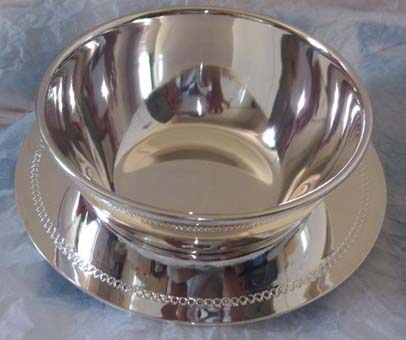
2.2 Lösungsformeln und Prozessbedingungen für jeden wichtigen Prozess
2.2.1 Organische Entfettung
Bei Raumtemperatur mit l80 # Flugbenzin.
2.2.2 Chemische Entfettung
2.2.3 Alkalikonorrosion
Der Zweck des Alkaliätzens besteht darin, den Oxidfilm auf der Oberfläche des Aluminiumteils zu entfernen, um eine ideale Mikrorauhigkeit zu erhalten und das Öl weiter zu entfernen, um so die Bindungskraft der Beschichtung zu erhöhen. Die Antwort ist schneller und die Zeit sollte streng kontrolliert werden.
2.2.4 Ätzen
Nach dem Alkaliätzen lösen sich Kupfer, Silizium, Mangan usw. in Aluminium und seinen Legierungen nicht in alkalischen Substanzen auf und verbleiben auf der Oberfläche des Werkstücks und der Korrosionsrückstand bildet einen "hängenden Asche" -Adsorptionsfilm.
Der Zweck des Ätzens besteht darin, diese Befestigungen aufzulösen, wobei das Werkstück einer hellen Oberfläche und einem guten Aktivierungszustand ausgesetzt bleibt.
(1) Geeignet für allgemeine Aluminiumlegierungsteile
2.2.5 Erstes Mal Zinkauslaugen
2.2.6 Zweite Zinkierung
Der sekundäre Verzinkungsprozess hat offensichtliche Auswirkungen auf die Verbesserung der Qualität der Zink-imprägnierten Schicht und die Verbesserung der Bindungskraft. Dies ist darauf zurückzuführen, dass Al2O3 zum ersten Mal vor dem Ersetzen von Al durch Eintauchen in Zink aufgelöst werden muss. Die resultierende Zinkschicht weist einen rauhen und lockeren Kristall, eine ungleiche Verteilung der Kristallkörner, einen großen Größenunterschied und eine schlechte Haftung der Zink-imprägnierten Schicht auf. Das sekundäre Zinkeintauchverfahren kann die Haftung, Gleichmäßigkeit und Korrosionsbeständigkeit nachfolgender Beschichtungen verbessern. Wenn die Zinkkristallkörner mit einer schlechten Bindung zwischen der Oberfläche von Aluminium und seinen Legierungen in Salpetersäure gelöst werden, wird die große Korngröße der Zinkkörner kleiner und eine gleichmäßige und detaillierte Oberfläche wird gebildet. Die freiliegenden Körner werden die Keimbildungszentren für das sekundäre Zinkeintauchen, so dass die resultierende Zinkschicht fein ist und die Bindung mit dem Substrat verbessert wird.
Die Prozessbedingungen sind:
2.2.7 Cyanidverzinkung
Für die komplexe Form des Schalenbauteils ist zwar das sekundäre Zinkeintauchen, die in dem Tiegel und der tiefen Vertiefung abgeschiedene Zinkschicht relativ dünn, und die nachfolgende Kupferplattierung neigt aufgrund der starken Alkalität und der höheren Temperatur zur Auflösung. Auf diese Weise geht die Schutzwirkung der Zinkschicht auf der Aluminiumoberflächenschicht verloren, und die Haftung der Plattierungsschicht wird stark verringert. Daher ist es notwendig, vor der Verkupferung zu galvanisieren, um die Dicke der Zinkschicht zu erhöhen.
2.1 Prozessablauf
Organische Entfettung - chemische Entfettung - Alkali-Korrosion - Säureätzung - Zinklaugung - Essigsäuresalz - Schwerzinkat - Cyanidverzinkung - Verkupferung - Vorbeschichtetes Silber - Breitsilber - Eine elektrolytische Passivierung wird trockengeblasen und getrocknet.
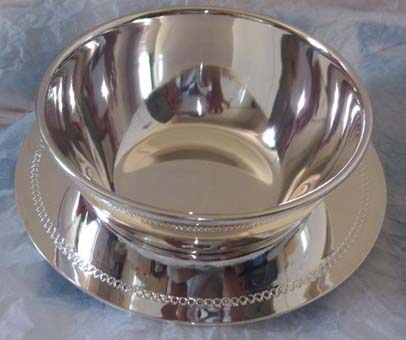
2.2 Lösungsformeln und Prozessbedingungen für jeden wichtigen Prozess
2.2.1 Organische Entfettung
Bei Raumtemperatur mit l80 # Flugbenzin.
2.2.2 Chemische Entfettung
Typ B 898 Entfettung Ling | 50g/L |
θ | <50℃ |
t | 2~10min |
2.2.3 Alkalikonorrosion
Der Zweck des Alkaliätzens besteht darin, den Oxidfilm auf der Oberfläche des Aluminiumteils zu entfernen, um eine ideale Mikrorauhigkeit zu erhalten und das Öl weiter zu entfernen, um so die Bindungskraft der Beschichtung zu erhöhen. Die Antwort ist schneller und die Zeit sollte streng kontrolliert werden.
NaOH | 80—100g/L |
θ | 60~700 |
Ct | 0.5~1 min |
Nach dem Alkaliätzen lösen sich Kupfer, Silizium, Mangan usw. in Aluminium und seinen Legierungen nicht in alkalischen Substanzen auf und verbleiben auf der Oberfläche des Werkstücks und der Korrosionsrückstand bildet einen "hängenden Asche" -Adsorptionsfilm.
Der Zweck des Ätzens besteht darin, diese Befestigungen aufzulösen, wobei das Werkstück einer hellen Oberfläche und einem guten Aktivierungszustand ausgesetzt bleibt.
(1) Geeignet für allgemeine Aluminiumlegierungsteile
HN03(p=1.639/mL) | 500 mL/L |
t | Zimmertemperatur |
f | 5~10S |
(2) Geeignet für Silizium-Aluminium-Legierung Stücke
HN03(p=1.63g/mL) | 500 mL/L |
HF(W≈40%) | 60 mL/L |
θ | Zimmertemperatur |
t | 5~10S |
Zn0 | 100g/L |
NaOH | 500g/L |
NaKC4H406·2H20 |
10g/L |
FeCl3·6H20 | 1g/L |
HF(w≈40%) | 3 mL/L |
θ | 25~30℃ |
t |
45—60S |
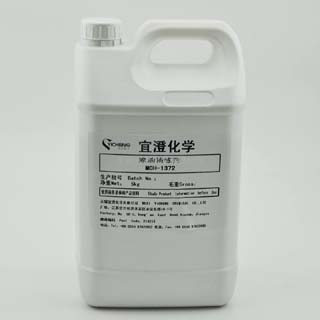
Der sekundäre Verzinkungsprozess hat offensichtliche Auswirkungen auf die Verbesserung der Qualität der Zink-imprägnierten Schicht und die Verbesserung der Bindungskraft. Dies ist darauf zurückzuführen, dass Al2O3 zum ersten Mal vor dem Ersetzen von Al durch Eintauchen in Zink aufgelöst werden muss. Die resultierende Zinkschicht weist einen rauhen und lockeren Kristall, eine ungleiche Verteilung der Kristallkörner, einen großen Größenunterschied und eine schlechte Haftung der Zink-imprägnierten Schicht auf. Das sekundäre Zinkeintauchverfahren kann die Haftung, Gleichmäßigkeit und Korrosionsbeständigkeit nachfolgender Beschichtungen verbessern. Wenn die Zinkkristallkörner mit einer schlechten Bindung zwischen der Oberfläche von Aluminium und seinen Legierungen in Salpetersäure gelöst werden, wird die große Korngröße der Zinkkörner kleiner und eine gleichmäßige und detaillierte Oberfläche wird gebildet. Die freiliegenden Körner werden die Keimbildungszentren für das sekundäre Zinkeintauchen, so dass die resultierende Zinkschicht fein ist und die Bindung mit dem Substrat verbessert wird.
Die Prozessbedingungen sind:
Zn(NO)2 | 30g/L |
NaOH | 200g/L |
C6H807 | 40g/L |
FeCl3·6H20 | 1g/L |
θ | 15~30℃ |
Ct | 30~60S |
2.2.7 Cyanidverzinkung
Für die komplexe Form des Schalenbauteils ist zwar das sekundäre Zinkeintauchen, die in dem Tiegel und der tiefen Vertiefung abgeschiedene Zinkschicht relativ dünn, und die nachfolgende Kupferplattierung neigt aufgrund der starken Alkalität und der höheren Temperatur zur Auflösung. Auf diese Weise geht die Schutzwirkung der Zinkschicht auf der Aluminiumoberflächenschicht verloren, und die Haftung der Plattierungsschicht wird stark verringert. Daher ist es notwendig, vor der Verkupferung zu galvanisieren, um die Dicke der Zinkschicht zu erhöhen.
Zn0 | 35~459/L |
NaCN | 70~90g/L |
NaOH | 60~70g/L |
95 Cyanid Galvanisierungs- und Öffnungsmittel | 5 mL/L |
95 Cyanid-Zink-Glanz-Aufheller | 3~5 mL/L |
θ | 5~30℃, |
J | O.5~3 A/dm2 |
t | 2~5 min |
2.2.8 Verkupferung
2.2.9 Vorbeschichtetes Silber
CuCN | 55~85g/L |
NaCN(free) | 10~15g/L |
991Brightener | l0~12mL/L |
θ | 55~65℃, |
J | 1~3 A/dm2 |
t | 10~15 min |
Stirring method | Kathode bewegen |
Ag(以KAg(CN)2加入) | 1~2g/L |
KCN | l00g/L |
anode | Edelstahlplatte |
J | 1~2 A/dm2 |
θ | 10~30℃ |
Ct | 5~10S |
2.2.10 Versilberung
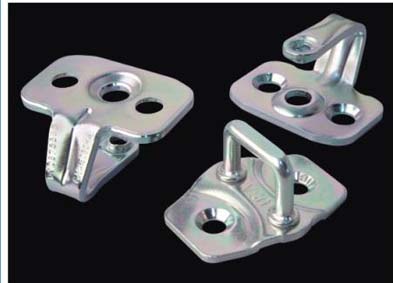
Ag(以KAg(CN)2 Join) | 20~40g/L |
KCN(free) | 90~150g/L |
KOH | 5~10g/L |
Silber Aufheller A | 30mL/L |
Silber Aufheller B | 15 mL/L |
θ | 10~30℃ |
J | 0.5~1.5 |
Rührmethode | Kathode bewegen |
2.2.11 Elektrolysepassivierung
3. Plattierungsleistungstest
3.1 Aussehenstest
Das visuelle Beobachtungsverfahren beobachtet die Glätte des Überzugs, die Gleichmäßigkeit der Farbe und ob es Unreinheiten wie Abblättern, Blasenbildung, Abblättern, Grübchenbildung, Flecken und Verbrennungen gibt.
3.2 Bindungskrafttest
3.2.1 Querschnittsmethode
Verwenden Sie auf der Probe ein Stahlmesser, um mehrere Quadrate mit einer Seitenlänge von 1 mm × 1 mm zu zeichnen. Beobachten Sie, ob die Beschichtung in diesem Bereich Blasen wirft oder abfällt.
3.2.2 heiße und kalte Zyklusmethode
Legen Sie die Probe in einen elektrischen Ofen bei 200 ° C und inkubieren Sie für 1 h. Unmittelbar nach dem Entfernen wird es in ein Wasser von 18 ° C bis 25 ° C zum Abkühlen gegeben, und es wird geprüft, ob die Beschichtung Blasen bildet oder abfällt.
4. Faktoren, die die Plattierungsleistung beeinflussen
4.1 Alkali-Säure-Ätzung
Das Experiment fand heraus, dass die Temperatur des Alkaliätzens zu hoch ist und die Zeit zu lang ist und die Manteloberfläche leicht überätzt wird; Wenn die Temperatur zu niedrig ist und die Zeit zu kurz ist, wird der ungleichmäßige Oxidfilm auf der Manteloberfläche nicht vollständig entfernt, was zu einer Abnahme der Plattierungshaftung führt. Um das Gemisch aus Tri-Aluminiumoxid, Siliciumlegierungselementen und deren Oxiden, die nach dem Alkaliätzen der Shell-Oberfläche gebildet werden, zu entfernen, befindet sich das Werkstück in einem guten aktivierten Zustand. Verschiedene Aluminiumlegierungskomponenten verwenden üblicherweise unterschiedliche Säureätzlösungen. welche die Bindungskraft der Beschichtung stärker beeinflussen.
4.2 Vorbehandlung
Tabelle 1 zeigt die Auswirkung verschiedener Vorbehandlungsverfahren auf die Beschichtungsqualität. Aus der Tabelle ist ersichtlich, dass nur der Vorbehandlungsprozess der Kombination von sekundärem Zinkeintauchen und Galvanisieren einen Kristall mit feinem Korn, starker Bindungskraft, guter Leichtigkeit und guter Beschichtungsqualität bereitstellt. Shell hat einen sehr geringen Teil der Blasenbildung aufgrund von schlechtem Wasser während des Betriebs verursacht.
Tabelle 1 Auswirkung des Vorbehandlungsprozesses auf die Beschichtungsqualität
4.3 Die Temperatur der Zink-Tauchlösung
Die Temperatur der Zink-Tauchlösung hat einen großen Einfluss auf die Qualität der Beschichtung. Bei dem Zinkabscheidungsprozess für das gleiche Aluminiumsubstrat ist die Abscheidungsrate ebenfalls unterschiedlich, wenn die Temperatur unterschiedlich ist, und die Temperatur des Zinks kristallisiert schneller, wenn die Temperatur erhöht wird. Wenn die Temperatur zu hoch ist, ist die Reaktion zu schnell, die Zinkschicht ist dick, die Kristalle sind rauh, die Lösungslebensdauer ist kurz, die Bindungsstärke der Beschichtung ist schlecht und die Chargen-Durchlaufrate ist niedrig; Wenn die Temperatur zu niedrig ist, ist die Reaktion langsam, die Zinkschicht ist dünn, kann während des Vorplattierens leicht aufgebrochen werden und die Bindungsstärke ist schlecht. Aus dem Experiment ist bekannt, dass das Eintauchen in Zink bei 25-30 ° C durchgeführt werden sollte. Die resultierende Beschichtung ist gleichförmig, dicht, mit einer guten Bindungskraft und einer hohen Batch-Durchlaufrate.
4.4 Herstellung der Zink-Tauchlösung
Lashmore schlug vor, dass die Zugabe von dreiwertigen Eisenionen einen großen Einfluss auf die Zinkauslaugungsreaktion hat. Um die Zinkimmersionsschicht zu kristallisieren, muss daher FeCl 3 zu der Lösung hinzugefügt werden. Die experimentellen Ergebnisse zeigen, dass die Additionsordnung von Eisen (III) -Ionen auch die Leistung der Beschichtung stark beeinflusst. Die Zugabe von FeCl 3 und NaKC 4 H 406 hat einen signifikanten Einfluss auf die Reaktion. Wenn Eisenchlorid direkt zu der Natriumhydroxidlösung zugegeben wird, schäumt die resultierende Beschichtung und fällt ab. Dies liegt daran, dass Eisenionen unter alkalischen Bedingungen dazu neigen, Präzipitate zu bilden, was die effektive Konzentration von Eisen in der Lösung reduziert. Eisen (III) chlorid sollte zuerst in Kalium-Natriumtartrat-Lösung gelöst werden, Zinkoxid in Natronlauge gelöst und dann gemischt werden, was zu einer guten Bindung der Beschichtung führt, die Batch-Durchlaufrate ist hoch.
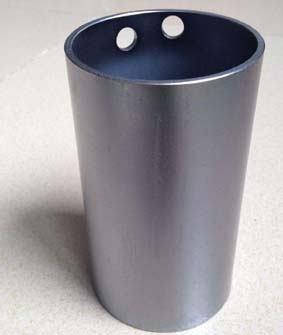
4.5 Zink-Tauchzeit
Wenn die Zeit des Zinkimmersionierens mehr als 60 ° beträgt, ist die Zinkschicht dick, der Kristall ist rauh, die Bindungskraft ist gering und die Chargen-Durchlaufrate ist niedrig. Wenn die erste Zinkeintauchzeit weniger als 45 Sekunden beträgt und die zweite Zinkeintauchzeit weniger als 30 Sekunden beträgt, ist die resultierende Zinkschicht dünn, während des Vorplattierens leicht aufzuspalten, und die Beschichtungshaftung ist schlecht. Daher sollte die erste Zinkimmersion bei 45-60 S und die zweite Zinkimmersionszeit bei 30-60 s kontrolliert werden. Die erhaltene Beschichtung ist gleichförmig, dicht, mit hoher Bindungskraft und hohem Chargendurchlauf
4,6 Kathodenstromdichte in der Cyanid-Kupferplattierung
Die Stromdichte der Cyanid-Verkupferung hat einen wesentlichen Einfluss auf die Qualität der Beschichtung. Bei unterschiedlichen Kathodenstromdichten variiert die Bindungskraft der Beschichtung stark. Experimente zeigen, dass die Stromdichte innerhalb einer kurzen Zeitspanne nach dem Beginn der Erregung auf den zulässigen Wert begrenzt werden sollte und dann bis nahe an die untere Grenze für das Elektroplattieren reduziert werden sollte. Auf diese Weise können alle Teile des Werkstücks mit Kupfer abgeschieden werden, um die Haftung der nachfolgenden Silberplattierungsschicht zu verbessern; Andernfalls wird das Werkstück nicht auf dem Tiegel oder in der tiefen Vertiefung abgelagert, und die Silberplattierungsschicht hat eine schlechte Haftung. Außerdem sollten bei der Cyanid-Kupferplattierung Teile unter die Nut geladen werden, um einen Austausch der Kupferschicht zu verhindern.
4.7 Hilfskathoden für helle Versilberung
In dem Experiment wurde gefunden, dass, wenn eine Schutzkathode während der Elektroplattierung von Silber verwendet wird, die Beschichtung auf der Oberfläche von Shell mit Feinheit und Gleichförmigkeit kristallisiert wird; Ansonsten ist die Beschichtung an der äußeren Ecke der Schale versengt. Wenn die Hilfsanode zum Galvanisieren von Silber verwendet wird, ist die Dicke der Außenhaut innerhalb der Außenhaut gleichmäßig, ansonsten ist die Außenhaut innerhalb der Außenhaut an den scharfen Ecken dünner, was sich auf die Qualität der Außenbeschichtung auswirkt. Daher wird bei der Glanzversilberung einerseits eine Schutzkathode verwendet und andererseits eine Hilfsanode innerhalb der Schale aufgehängt. Hilfsanoden bestehen aus Silberstreifen und in jeder Kavität sollten genügend Anoden vorhanden sein. Die Silberanode ist teilweise mit Isolierband verklebt, um einen Kurzschluss der Silberanode mit der Schale zu vermeiden.
5. Schlussfolgerung
Ein kombinierter Zink-Galvanisierungs- und Verzinkung-Vorbehandlungsprozess wird verwendet, um eine glänzende Silberbeschichtung auf der Oberfläche von Aluminium und seinen Legierungen zu erhalten, die durch feine Kristalle, gute Helligkeit und starke Bindungskraft gekennzeichnet ist.
KECr204 | 8~10g/L |
K2C03 | 6~8g/L |
pH | 9~10 |
θ | 10~35℃ |
J | 0.5~1 A/dm2 |
t | 2~5 min |
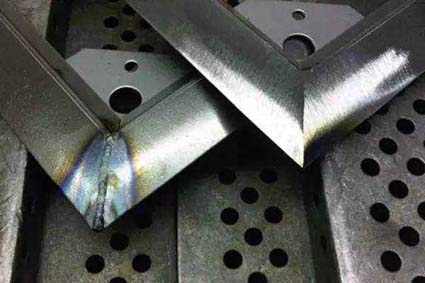
3.1 Aussehenstest
Das visuelle Beobachtungsverfahren beobachtet die Glätte des Überzugs, die Gleichmäßigkeit der Farbe und ob es Unreinheiten wie Abblättern, Blasenbildung, Abblättern, Grübchenbildung, Flecken und Verbrennungen gibt.
3.2 Bindungskrafttest
3.2.1 Querschnittsmethode
Verwenden Sie auf der Probe ein Stahlmesser, um mehrere Quadrate mit einer Seitenlänge von 1 mm × 1 mm zu zeichnen. Beobachten Sie, ob die Beschichtung in diesem Bereich Blasen wirft oder abfällt.
3.2.2 heiße und kalte Zyklusmethode
Legen Sie die Probe in einen elektrischen Ofen bei 200 ° C und inkubieren Sie für 1 h. Unmittelbar nach dem Entfernen wird es in ein Wasser von 18 ° C bis 25 ° C zum Abkühlen gegeben, und es wird geprüft, ob die Beschichtung Blasen bildet oder abfällt.
4. Faktoren, die die Plattierungsleistung beeinflussen
4.1 Alkali-Säure-Ätzung
Das Experiment fand heraus, dass die Temperatur des Alkaliätzens zu hoch ist und die Zeit zu lang ist und die Manteloberfläche leicht überätzt wird; Wenn die Temperatur zu niedrig ist und die Zeit zu kurz ist, wird der ungleichmäßige Oxidfilm auf der Manteloberfläche nicht vollständig entfernt, was zu einer Abnahme der Plattierungshaftung führt. Um das Gemisch aus Tri-Aluminiumoxid, Siliciumlegierungselementen und deren Oxiden, die nach dem Alkaliätzen der Shell-Oberfläche gebildet werden, zu entfernen, befindet sich das Werkstück in einem guten aktivierten Zustand. Verschiedene Aluminiumlegierungskomponenten verwenden üblicherweise unterschiedliche Säureätzlösungen. welche die Bindungskraft der Beschichtung stärker beeinflussen.
4.2 Vorbehandlung
Tabelle 1 zeigt die Auswirkung verschiedener Vorbehandlungsverfahren auf die Beschichtungsqualität. Aus der Tabelle ist ersichtlich, dass nur der Vorbehandlungsprozess der Kombination von sekundärem Zinkeintauchen und Galvanisieren einen Kristall mit feinem Korn, starker Bindungskraft, guter Leichtigkeit und guter Beschichtungsqualität bereitstellt. Shell hat einen sehr geringen Teil der Blasenbildung aufgrund von schlechtem Wasser während des Betriebs verursacht.
Tabelle 1 Auswirkung des Vorbehandlungsprozesses auf die Beschichtungsqualität
Vorbehandlungsprozess | Beschichtungsqualität |
einmal Zinklaugung | Grobe Kristalle, schlechtes Licht, meist Shell von der Haut, Blasenbildung, Verlust |
Zweimal Zinkauslaugung | Die äußere Oberfläche ist kristallklar mit guter Leichtigkeit, und die innere Oberfläche der Schale hat Abschälung und Blasenbildung. |
Kombinierte sekundäre Zinkimmersion und Verzinkung | Kristallisiert, gutes Licht, sehr wenige Muscheln haben Blasen |
Zink-Nickel-Legierung eintauchen | Die äußere Oberfläche der Oberfläche ist versengt, und die innere Oberfläche der Schale ist abgeschält, Blasen und abgeschält. |
Vorverzinkt | Schlechte Helligkeit, Abschälen der Oberfläche der Schale, Blasenbildung, Vergießen |
4.3 Die Temperatur der Zink-Tauchlösung
Die Temperatur der Zink-Tauchlösung hat einen großen Einfluss auf die Qualität der Beschichtung. Bei dem Zinkabscheidungsprozess für das gleiche Aluminiumsubstrat ist die Abscheidungsrate ebenfalls unterschiedlich, wenn die Temperatur unterschiedlich ist, und die Temperatur des Zinks kristallisiert schneller, wenn die Temperatur erhöht wird. Wenn die Temperatur zu hoch ist, ist die Reaktion zu schnell, die Zinkschicht ist dick, die Kristalle sind rauh, die Lösungslebensdauer ist kurz, die Bindungsstärke der Beschichtung ist schlecht und die Chargen-Durchlaufrate ist niedrig; Wenn die Temperatur zu niedrig ist, ist die Reaktion langsam, die Zinkschicht ist dünn, kann während des Vorplattierens leicht aufgebrochen werden und die Bindungsstärke ist schlecht. Aus dem Experiment ist bekannt, dass das Eintauchen in Zink bei 25-30 ° C durchgeführt werden sollte. Die resultierende Beschichtung ist gleichförmig, dicht, mit einer guten Bindungskraft und einer hohen Batch-Durchlaufrate.
4.4 Herstellung der Zink-Tauchlösung
Lashmore schlug vor, dass die Zugabe von dreiwertigen Eisenionen einen großen Einfluss auf die Zinkauslaugungsreaktion hat. Um die Zinkimmersionsschicht zu kristallisieren, muss daher FeCl 3 zu der Lösung hinzugefügt werden. Die experimentellen Ergebnisse zeigen, dass die Additionsordnung von Eisen (III) -Ionen auch die Leistung der Beschichtung stark beeinflusst. Die Zugabe von FeCl 3 und NaKC 4 H 406 hat einen signifikanten Einfluss auf die Reaktion. Wenn Eisenchlorid direkt zu der Natriumhydroxidlösung zugegeben wird, schäumt die resultierende Beschichtung und fällt ab. Dies liegt daran, dass Eisenionen unter alkalischen Bedingungen dazu neigen, Präzipitate zu bilden, was die effektive Konzentration von Eisen in der Lösung reduziert. Eisen (III) chlorid sollte zuerst in Kalium-Natriumtartrat-Lösung gelöst werden, Zinkoxid in Natronlauge gelöst und dann gemischt werden, was zu einer guten Bindung der Beschichtung führt, die Batch-Durchlaufrate ist hoch.
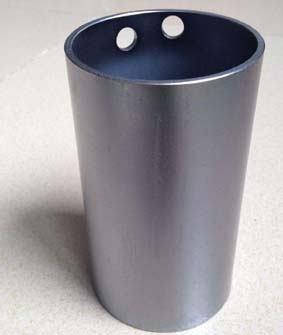
4.5 Zink-Tauchzeit
Wenn die Zeit des Zinkimmersionierens mehr als 60 ° beträgt, ist die Zinkschicht dick, der Kristall ist rauh, die Bindungskraft ist gering und die Chargen-Durchlaufrate ist niedrig. Wenn die erste Zinkeintauchzeit weniger als 45 Sekunden beträgt und die zweite Zinkeintauchzeit weniger als 30 Sekunden beträgt, ist die resultierende Zinkschicht dünn, während des Vorplattierens leicht aufzuspalten, und die Beschichtungshaftung ist schlecht. Daher sollte die erste Zinkimmersion bei 45-60 S und die zweite Zinkimmersionszeit bei 30-60 s kontrolliert werden. Die erhaltene Beschichtung ist gleichförmig, dicht, mit hoher Bindungskraft und hohem Chargendurchlauf
4,6 Kathodenstromdichte in der Cyanid-Kupferplattierung
Die Stromdichte der Cyanid-Verkupferung hat einen wesentlichen Einfluss auf die Qualität der Beschichtung. Bei unterschiedlichen Kathodenstromdichten variiert die Bindungskraft der Beschichtung stark. Experimente zeigen, dass die Stromdichte innerhalb einer kurzen Zeitspanne nach dem Beginn der Erregung auf den zulässigen Wert begrenzt werden sollte und dann bis nahe an die untere Grenze für das Elektroplattieren reduziert werden sollte. Auf diese Weise können alle Teile des Werkstücks mit Kupfer abgeschieden werden, um die Haftung der nachfolgenden Silberplattierungsschicht zu verbessern; Andernfalls wird das Werkstück nicht auf dem Tiegel oder in der tiefen Vertiefung abgelagert, und die Silberplattierungsschicht hat eine schlechte Haftung. Außerdem sollten bei der Cyanid-Kupferplattierung Teile unter die Nut geladen werden, um einen Austausch der Kupferschicht zu verhindern.
4.7 Hilfskathoden für helle Versilberung
In dem Experiment wurde gefunden, dass, wenn eine Schutzkathode während der Elektroplattierung von Silber verwendet wird, die Beschichtung auf der Oberfläche von Shell mit Feinheit und Gleichförmigkeit kristallisiert wird; Ansonsten ist die Beschichtung an der äußeren Ecke der Schale versengt. Wenn die Hilfsanode zum Galvanisieren von Silber verwendet wird, ist die Dicke der Außenhaut innerhalb der Außenhaut gleichmäßig, ansonsten ist die Außenhaut innerhalb der Außenhaut an den scharfen Ecken dünner, was sich auf die Qualität der Außenbeschichtung auswirkt. Daher wird bei der Glanzversilberung einerseits eine Schutzkathode verwendet und andererseits eine Hilfsanode innerhalb der Schale aufgehängt. Hilfsanoden bestehen aus Silberstreifen und in jeder Kavität sollten genügend Anoden vorhanden sein. Die Silberanode ist teilweise mit Isolierband verklebt, um einen Kurzschluss der Silberanode mit der Schale zu vermeiden.
5. Schlussfolgerung
Ein kombinierter Zink-Galvanisierungs- und Verzinkung-Vorbehandlungsprozess wird verwendet, um eine glänzende Silberbeschichtung auf der Oberfläche von Aluminium und seinen Legierungen zu erhalten, die durch feine Kristalle, gute Helligkeit und starke Bindungskraft gekennzeichnet ist.