Verfahren zum Fraesen von kleinen quadratischen Sackloechern in bearbeiteten Teilen
Bei der Entwicklung der Spindel des magnetoelektrischen Geschwindigkeitsmessers vom Typ SD-95 trat ein spezielles Problem bei der Verarbeitung kleiner quadratischer Blindlöcher auf. Die Teile sind in Abbildung 1 dargestellt. Wenn der Geschwindigkeitsmesser arbeitet, sind der Zähler und der Sensor durch eine flexible Welle verbunden. Zur Drehmomentübertragung wird in die Spindel ein Vierkant-Sackloch mit einer Seitenlänge von nur 2,75 mm und einer Arbeitslänge von 8 mm eingearbeitet. Darüber hinaus muss ein tiefes kreisförmiges Loch an der Rückseite des quadratischen Lochs größer sein als der Durchmesser des umschriebenen Kreises des quadratischen Lochs, um die axialen Turbulenzen und radialen Schwingungen des weichen Wellenkopfs aufzunehmen und das Schmieröl zu speichern. Aufgrund der großen Losgröße der Welle ist es unmöglich, spezielle Verarbeitungsmethoden anzuwenden, so dass dies zu einem produktionsbedingten Faktor des Produkts geworden ist und die wirtschaftlichen Vorteile beeinträchtigt.
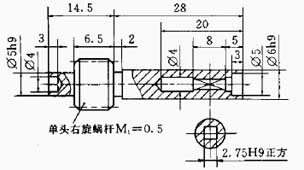
Abbildung 1 Zeichnung der Teile des quadratischen Lochs der Geschwindigkeits-Entfernungsmesserspindel
Da das Loch ein Sackloch und der Durchmesser klein ist, kann der Hinterschnitt nicht vorgefertigt werden und die Spanabfuhr ist schwierig, so dass herkömmliche Spanbearbeitungsverfahren wie Schneiden und Stanzen nicht verwendet werden können. Daher sollten Sie zuerst das Bodenloch verwenden und dann einen radialen Druck auf die Welle ausüben. Es wird plastisch verformt, so dass es durch einen runden und quadratischen spanlosen Formprozess geformt wird. Basierend auf den oben genannten Ideen haben wir eine Vielzahl von Druckformungsverfahren konzipiert und praktiziert. Das Folgende sind verschiedene Verfahren zum Formen von quadratischen Löchern.
I. Metall-Stanzverfahren
Die Prozessschritte sind:
Das Schruppen des f6mm-Abschnitts des Rohwagens beträgt f7,2mm, und das innere Loch des Bohrers ist f4mm tief und 20mm. Entfernen Sie das Werkstück und setzen Sie einen 2,75-mm-Vierkantdorn in das Loch ein. Nachdem Sie die richtige Ausrichtung gefunden haben, befindet sich die V-förmige Form mit der oberen und unteren Form auf der Stanzmaschine in einem Winkel von 90 Grad. Die Innen- und Außenseiten werden quadriert, die Länge beträgt 8 mm, und dann wird die Kernstange herausgenommen (Abb. 2).

Abbildung 2 Sackloch Press Formverfahren
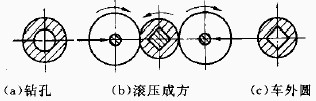
Abbildung 3 Verfahren zum Vierkant Walzen
Das Verfahren hat den Vorteil, dass das Werkstück nicht entladen wird und alle Arbeitsschritte auf der Drehmaschine erledigt sind, so dass das Vierkantloch nach dem Formen eine hohe Koaxialität zum Außenkreis aufrechterhalten kann und die Qualität einfach zu gewährleisten ist. Und die Ausrüstungsanforderungen sind gering, nur gewöhnliche Drehmaschinen, besonders geeignet für kleine Unternehmen. Der Nachteil ist, dass die Radialkraft beim Walzen groß ist, wodurch das Werkstück Wärme erzeugt und Vibrationen verursacht. Außerdem sind die technischen Anforderungen an die Arbeiter hoch. In der Praxis wird, um das Problem der großen Radialkraft zu überwinden, ein Verfahren zum gleichzeitigen Zuführen der vorderen und hinteren Doppelwalze angewendet und eine hydraulische Übertragung verwendet. Die Radialkräfte heben sich im wesentlichen auf, und die Rollgeschwindigkeit wird ebenfalls beschleunigt, und der Effekt ist gut. Dieses Verfahren macht jedoch den Vorschubmechanismus des Werkzeughalters komplizierter und wird oft verwendet, wenn die Chargengröße groß ist. Der Schlüssel zum Erfolg dieses Prozesses liegt in der Beherrschung der Walzgeschwindigkeit und des Vorschubs. Es sollte nicht nur eingerollt werden, die quadratische Lochform ist voll und es sollte nicht übermäßig sein, um den Rand des äußeren Kreisabschlusses nicht zu verlieren. Spezifische Parameter wie der Außendurchmesser des Rohlings vor dem Walzen, die Walzgeschwindigkeit, die Walzvorschubmenge usw. können durch einen Prozesstest erhalten werden.
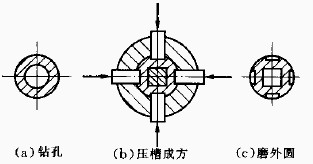
Abbildung 4 Schimmel Formverfahren
Der Arbeitszustand der Form ist wie folgt:
Das Werkstück 9 wird durch den Außenumfang des fertigen Fahrzeugs in den konkaven Formkörper 6 eingelegt. Wenn die Stanzmaschine die obere Matrizenplatte 8 nach unten fährt, wird das Werkstück zuerst durch den oberen Wagenheber 12 auf die Positionierfläche gedrückt. Der Keil 17 drückt den Schieber 18 entlang der horizontalen Schiene 19 nach links, und der bewegliche Nocken 15 wird durch den Stift 16 angetrieben, um sich nach links zu bewegen. Die Nockenrampe wirkt mit der Rolle 2 zusammen, um den Vierkantkern 3 zu zwingen, sich nach oben in die Innenbohrung des Werkstücks zu bewegen und das Loch durch das Loch f5 mm zu zentrieren. Die obere Schablone bewegt sich weiter nach unten. Zu diesem Zeitpunkt befindet sich die Keilsäule in einem Leerhub und der obere Auswerferstift wird unter der Wirkung der Feder 10 in einem festen Zustand gehalten, so dass das Werkstück zuverlässig positioniert wird. Danach beginnt der Ringkeil 14, in den Arbeitshub einzutreten, und die vier Formstempel 4 werden gezwungen, sich zusammen in einer zentripetalen Richtung zu bewegen, und die Nut wird auf das Werkstück herausgedrückt, um eine konvexe Form in dem Loch zu bilden. Das quadratische Loch wird durch die gemeinsame Wirkung des quadratischen Kerns geformt. Beim Rückhub wird die obere Matrizenplatte vorgeschoben und der Ringkeil 14 löst zunächst den Formstempel, so dass dieser unter Einwirkung der Rückholfeder 5 in die Ausgangsstellung zurückkehrt. Der Keil 17 drückt dann den Schieber 18 nach rechts und bewegt den Nocken entsprechend nach rechts, und der quadratische Kern verlässt das innere Loch durch die Rampe und die Rolle. Schließlich gibt der obere Auswerfer 12 das Werkstück frei und das Werkstück kann herausgenommen werden, wodurch ein Arbeitszyklus abgeschlossen wird.
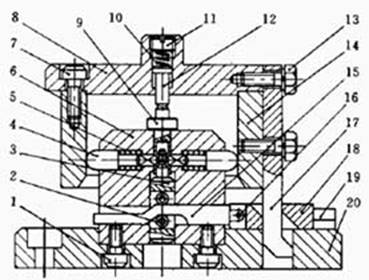
Figur 5 quadratisches Loch Umformwerkzeug
er Vorteil des Verfahrens besteht darin, dass die Positioniergenauigkeit in der Form hoch ist, nachdem der äußere Kreis des Werkstücks durch den Endbearbeitungswagen hindurchgegangen ist, und die tatsächliche Wandstärke verringert ist, so dass die Verformung einfach ist und somit eine hohe Qualität erhalten werden kann. Da das Ausmaß der Prägung gering ist (einseitig 0,6 mm) und in einem bestimmten Bereich ausgeführt wird, ist die auf das Werkstück wirkende Andruckkraft relativ gering. Daher ist auch die Werkstückverformung nach dem Stanzen gering und kann direkt in den nächsten Schleifvorgang eintreten, so dass die Produktivität stark verbessert wird. Darüber hinaus ist das Verfahren sehr bequem und arbeitssparend und bei Arbeitnehmern beliebt. Der Nachteil ist, dass nach dem Formen vier Längsnuten mit einer Breite von 2 mm und einer Tiefe von 0,6 mm auf der Außenfläche des Werkstücks verbleiben und nach dem Schleifen nicht mehr entfernt werden können. Offensichtlich entspricht dies nicht den Zeichnungsanforderungen. In dieser Hinsicht denken wir so: Da die Nut für den nächsten Schleifvorgang theoretisch nachteilig ist, ist in der Praxis, da die Nut lokalisiert ist, die Auswirkung nicht groß und die Auswirkung auf die Verwendung geringer. Die Praxis hat bewiesen, dass es beim Schmieren hilft, da der Tank nur zum Speichern einer bestimmten Menge Schmieröl verwendet wird. Daher haben wir die Zeichnungen entsprechend modifiziert, damit diese Rillen vorhanden sind. Wenn wir diese Rillen, um auszuschließen, müssen in vollem Umfang die Anforderungen der Zeichnungen zu entsprechen, kann es verwendet werden, um das Rohling Außendurchmesser zu erhöhen, in dem Verfahren zur Bildung von nach gehen drehen, aber wir dies noch nicht so gut empfehlen.
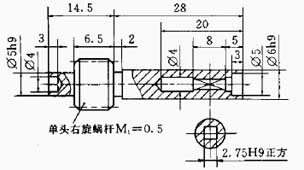
Abbildung 1 Zeichnung der Teile des quadratischen Lochs der Geschwindigkeits-Entfernungsmesserspindel
Da das Loch ein Sackloch und der Durchmesser klein ist, kann der Hinterschnitt nicht vorgefertigt werden und die Spanabfuhr ist schwierig, so dass herkömmliche Spanbearbeitungsverfahren wie Schneiden und Stanzen nicht verwendet werden können. Daher sollten Sie zuerst das Bodenloch verwenden und dann einen radialen Druck auf die Welle ausüben. Es wird plastisch verformt, so dass es durch einen runden und quadratischen spanlosen Formprozess geformt wird. Basierend auf den oben genannten Ideen haben wir eine Vielzahl von Druckformungsverfahren konzipiert und praktiziert. Das Folgende sind verschiedene Verfahren zum Formen von quadratischen Löchern.
I. Metall-Stanzverfahren
Die Prozessschritte sind:
Das Schruppen des f6mm-Abschnitts des Rohwagens beträgt f7,2mm, und das innere Loch des Bohrers ist f4mm tief und 20mm. Entfernen Sie das Werkstück und setzen Sie einen 2,75-mm-Vierkantdorn in das Loch ein. Nachdem Sie die richtige Ausrichtung gefunden haben, befindet sich die V-förmige Form mit der oberen und unteren Form auf der Stanzmaschine in einem Winkel von 90 Grad. Die Innen- und Außenseiten werden quadriert, die Länge beträgt 8 mm, und dann wird die Kernstange herausgenommen (Abb. 2).

Abbildung 2 Sackloch Press Formverfahren
Das Verfahren hat die Vorteile einfacher Prozessschritte, eines bequemen Formenbaus und eines kurzen Produktionszyklus. Der Nachteil besteht darin, dass die axiale Richtung des Werkstücks während des Stanzens ungehindert frei ist, so dass die Spindel unter der Wirkung der Presskraft zu Biegeverformungen neigt. Es ist schwierig, die Koaxialität zwischen dem quadratischen Loch und dem äußeren Kreis sicherzustellen. Gleichzeitig bricht der Dorn leicht, und es ist schwierig, ihn herauszunehmen, und die Arbeitsintensität des Arbeiters ist groß. Außerdem ist es für den äußeren Kreis der fertigen Maschine unangenehm, nachdem der äußere Teil des Werkstücks deformiert worden ist. Der praktische Vierkantstab besteht aus weißem Stahlmessermaterial und wird direkt durch Drahtschneiden hergestellt, so dass er eine gute Festigkeit aufweist. Zur Erleichterung der Kernzugstange ist in Längsrichtung eine Steigung von 1: 100 angebracht. Gleichzeitig muss beim Stanzen jederzeit auf die Schmierung geachtet werden, und der Kernstab muss mit einem Spezialwerkzeug herausgezogen werden. Das Verfahren hat eine echte Rate von weniger als 85% und ist nur für die Kleinserienfertigung geeignet.
II. Teile Walzverfahren bilden
II. Teile Walzverfahren bilden
Prozessschritte: Raues Auto f6mm Segment Außenkreis bis f7,2mm, Das innere Loch des Bohrers ist 4 mm tief und 20 mm. Das Loch ist 5 mm tief und 3 mm. Ohne das Werkstück zu entladen, wird ein 2,75-mm-Vierkantdorn auf der speziellen stromführenden Oberseite des Reitstocks der Drehmaschine eingespannt und in das Loch eingeführt und mit dem 5-mm-Loch positioniert. Dann wird die Drehmaschine gestartet, und das quadratische Kernsegment wird durch eine Walze gedrückt, um das Schrumpfloch zu verformen und unter der Bedingung des quadratischen Kerns ein quadratisches Loch zu bilden. Halten Sie nach dem Einrollen an und nehmen Sie den Dorn heraus (Abbildung 3).
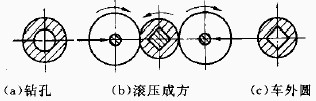
Abbildung 3 Verfahren zum Vierkant Walzen
Das Verfahren hat den Vorteil, dass das Werkstück nicht entladen wird und alle Arbeitsschritte auf der Drehmaschine erledigt sind, so dass das Vierkantloch nach dem Formen eine hohe Koaxialität zum Außenkreis aufrechterhalten kann und die Qualität einfach zu gewährleisten ist. Und die Ausrüstungsanforderungen sind gering, nur gewöhnliche Drehmaschinen, besonders geeignet für kleine Unternehmen. Der Nachteil ist, dass die Radialkraft beim Walzen groß ist, wodurch das Werkstück Wärme erzeugt und Vibrationen verursacht. Außerdem sind die technischen Anforderungen an die Arbeiter hoch. In der Praxis wird, um das Problem der großen Radialkraft zu überwinden, ein Verfahren zum gleichzeitigen Zuführen der vorderen und hinteren Doppelwalze angewendet und eine hydraulische Übertragung verwendet. Die Radialkräfte heben sich im wesentlichen auf, und die Rollgeschwindigkeit wird ebenfalls beschleunigt, und der Effekt ist gut. Dieses Verfahren macht jedoch den Vorschubmechanismus des Werkzeughalters komplizierter und wird oft verwendet, wenn die Chargengröße groß ist. Der Schlüssel zum Erfolg dieses Prozesses liegt in der Beherrschung der Walzgeschwindigkeit und des Vorschubs. Es sollte nicht nur eingerollt werden, die quadratische Lochform ist voll und es sollte nicht übermäßig sein, um den Rand des äußeren Kreisabschlusses nicht zu verlieren. Spezifische Parameter wie der Außendurchmesser des Rohlings vor dem Walzen, die Walzgeschwindigkeit, die Walzvorschubmenge usw. können durch einen Prozesstest erhalten werden.
III. Schimmel Formverfahren
Um den Anforderungen der Massenproduktion gerecht zu werden, haben wir spezielle Formen entwickelt, um die Produktivität erheblich zu steigern.
Die Prozessschritte sind:
Nach grobem Drehen der Drehmaschine wird der äußere Kreis des f6mm-Abschnitts verfeinert und die Schleifzugabe bleibt erhalten. Das innere Loch des Bohrers ist f4 mm tief und 20 mm, und das Loch ist f5 mm tief und 3 mm tief, was als Positionierungsreferenz verwendet wird. Verwenden Sie dann eine spezielle Form für den Stempel. In der Bohrung mit quadratischem Querschnitt mit dem Durchmesser der extrudierten vier Nuten entsprechen, und den Materialtransfer in den Poren. Ein viereckiges Loch wird unter der Verbindungswirkung des Dorns gebildet, und der spezifische Formungsvorgang ist wie in Fig. 4 gezeigt. Das spezielle Formwerkzeug ist in Abbildung 5 dargestellt.
Um den Anforderungen der Massenproduktion gerecht zu werden, haben wir spezielle Formen entwickelt, um die Produktivität erheblich zu steigern.
Die Prozessschritte sind:
Nach grobem Drehen der Drehmaschine wird der äußere Kreis des f6mm-Abschnitts verfeinert und die Schleifzugabe bleibt erhalten. Das innere Loch des Bohrers ist f4 mm tief und 20 mm, und das Loch ist f5 mm tief und 3 mm tief, was als Positionierungsreferenz verwendet wird. Verwenden Sie dann eine spezielle Form für den Stempel. In der Bohrung mit quadratischem Querschnitt mit dem Durchmesser der extrudierten vier Nuten entsprechen, und den Materialtransfer in den Poren. Ein viereckiges Loch wird unter der Verbindungswirkung des Dorns gebildet, und der spezifische Formungsvorgang ist wie in Fig. 4 gezeigt. Das spezielle Formwerkzeug ist in Abbildung 5 dargestellt.
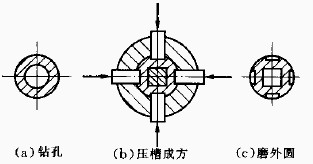
Abbildung 4 Schimmel Formverfahren
Der Arbeitszustand der Form ist wie folgt:
Das Werkstück 9 wird durch den Außenumfang des fertigen Fahrzeugs in den konkaven Formkörper 6 eingelegt. Wenn die Stanzmaschine die obere Matrizenplatte 8 nach unten fährt, wird das Werkstück zuerst durch den oberen Wagenheber 12 auf die Positionierfläche gedrückt. Der Keil 17 drückt den Schieber 18 entlang der horizontalen Schiene 19 nach links, und der bewegliche Nocken 15 wird durch den Stift 16 angetrieben, um sich nach links zu bewegen. Die Nockenrampe wirkt mit der Rolle 2 zusammen, um den Vierkantkern 3 zu zwingen, sich nach oben in die Innenbohrung des Werkstücks zu bewegen und das Loch durch das Loch f5 mm zu zentrieren. Die obere Schablone bewegt sich weiter nach unten. Zu diesem Zeitpunkt befindet sich die Keilsäule in einem Leerhub und der obere Auswerferstift wird unter der Wirkung der Feder 10 in einem festen Zustand gehalten, so dass das Werkstück zuverlässig positioniert wird. Danach beginnt der Ringkeil 14, in den Arbeitshub einzutreten, und die vier Formstempel 4 werden gezwungen, sich zusammen in einer zentripetalen Richtung zu bewegen, und die Nut wird auf das Werkstück herausgedrückt, um eine konvexe Form in dem Loch zu bilden. Das quadratische Loch wird durch die gemeinsame Wirkung des quadratischen Kerns geformt. Beim Rückhub wird die obere Matrizenplatte vorgeschoben und der Ringkeil 14 löst zunächst den Formstempel, so dass dieser unter Einwirkung der Rückholfeder 5 in die Ausgangsstellung zurückkehrt. Der Keil 17 drückt dann den Schieber 18 nach rechts und bewegt den Nocken entsprechend nach rechts, und der quadratische Kern verlässt das innere Loch durch die Rampe und die Rolle. Schließlich gibt der obere Auswerfer 12 das Werkstück frei und das Werkstück kann herausgenommen werden, wodurch ein Arbeitszyklus abgeschlossen wird.
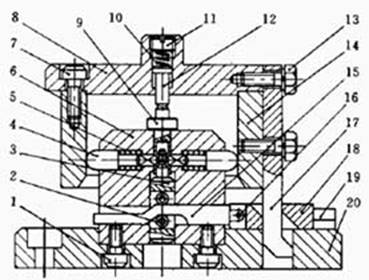
Figur 5 quadratisches Loch Umformwerkzeug
1, 7, 13. Verbindungsschrauben
2. Rad
3. Quadratischer Kern
4. Formstempel 5,
10. Feder zurücksetzen
6. Konkaver Körper
8. Obere Vorlage
9. Werkstück
11. Die Justierschraube
12. Oberer Auswerfer
14. Ringkeil
15 bewegliche Nocke
16. Pin
17. Wedge
18. Schieberegler
19. Führungsschiene
20. Formbasis
2. Rad
3. Quadratischer Kern
4. Formstempel 5,
10. Feder zurücksetzen
6. Konkaver Körper
8. Obere Vorlage
9. Werkstück
11. Die Justierschraube
12. Oberer Auswerfer
14. Ringkeil
15 bewegliche Nocke
16. Pin
17. Wedge
18. Schieberegler
19. Führungsschiene
20. Formbasis